《一種製革廢液分步循環再利用工藝》是張壯斗於2010年4月22日申請的專利,該專利公布號為CN101921881A,公布日為2010年12月22日,發明人是張壯斗。
《一種製革廢液分步循環再利用工藝》其特徵在於在預浸水、主浸水、浸灰、脫灰軟化、浸酸鉻鞣工序中分步進行廢液循環再利用。上述所有工序的廢液均實現全封閉循環利用。該發明實現了從原皮到藍濕皮的廢水循環再利用,同時能保證藍濕皮質量,大量節約治污及化料成本,極大的減少污水排放。
2018年8月,《一種製革廢液分步循環再利用工藝》獲得第一屆河南省專利獎三等獎。
(概述圖為《一種製革廢液分步循環再利用工藝》的摘要附圖)
基本介紹
- 中文名: 一種製革廢液分步循環再利用工藝
- 公布號:CN101921881A
- 公布日:2010年12月22日
- 申請號:2010101650901
- 申請日:2010年4月22日
- 申請人:張壯斗
- 地址:河南省商丘市開發區星林路與長江路交叉口
- 發明人:張壯斗
- 分類號:C14C3/02(2006.01)I、C14C1/00(2006.01)I、C14C1/08(2006.01)I、C14C1/06(2006.01)I、C14C1/04(2006.01)I
- 類別:發明專利
專利背景,發明內容,專利目的,技術方案,改善效果,附圖說明,權利要求,實施方式,榮譽表彰,
專利背景
一種製革廢液分步循環利用工藝沒有實現預浸水廢液及復灰廢液循環利用,由此廢水排放較大,2010年之前已實現預浸水和復灰廢液循環使用,進一步減少了用水量及廢水排放,且在其它工序的廢水循環使用中改進了參數。如增加了醋酸的使用,使脫灰廢液更利於循環。另外,在浸酸鉻鞣工序中免去了陽離子加脂劑的使用,並調整了pH值。而且進一步降低了部分化學材料的使用,如提鹼劑、鉻粉、軟化酶、加脂劑等。
從原皮到藍皮的生產工序是整個製革生產中的重污染階段,其排污量占整個製革過程中總排污量的75%以上,其水質特點是含有大量成分複雜且有毒、有害物質。其中含有大量的石灰、蛋白質、鹽類、油脂、氨氮化合物、硫化物、鉻鹽、毛類、皮渣、泥沙等,且COD、BOD非常高。其污染物種類繁多,成份複雜,水質水量變化係數大且有惡臭現象,是較難治理的工業廢水。
隨著環保技術設備的發展,2010年4月之前,製革廢水已經形成比較成熟的處理工藝(見下表)。但其運行過程往往花費高、效率低、效果差無法達到真正的治污目的。
工藝名稱技術優勢技術缺陷傳統活性污泥法該法對BOD5去除率在90%對需處理污水水質要求高,不適以上,COD在60%~80%間,色度在50%~90%間,S在85%~98%間。應衝擊負荷,需要高的動力和基建費用;占地面積也大,一般的企業難以承受;同時對廢水中的氨氮處理效果不佳。生物接觸氧化法對有機物去除率BOD5在95%左右,COD在92%左右,S在98%左右。容易產生堵塞,維護也比較困難。一旦出現問題,系統就得停止運行才能進行維護。氧化溝對BOD5去除率在95%以上,S在99%~100%,SS在75%左右處理效果不穩定,比較適宜於溫度較高的南方,對於北方,冬季運行可能有問題。雙層生物濾池對SS去除率在95%,BOD5在98%,COD在90%,Cr(III)在96%以上,S在96%。需要確定合適的回流比、選擇合適的濾料,運行費用比較大。
SBR法SBR工藝對COD、S、SS、Cr的去除率分別為93.3%、99.0%、90.3%、99.4%。運行費用比較大,規模較小效率較低,維護也比較困難。
在我們之前也有人對製革廢水進行了循環再利用,但只是簡單地對某一工序的廢水進行了循環利用,這樣對污水排放量的減少、化料的節約、生產成本的降低等都非常有限。若想實現從原皮到藍皮所有工段的廢水一次性全部回收利用,卻是一個極其複雜難解決的問題,並經常伴隨以下問題的出現:灰皮增重率、藍皮得革率均下降1.5%-3.5%,收縮溫度下降1.5℃-3.5℃,還會使藍皮粒面受損,粒面變粗,顏色變深,甚至產生“毛面”現象。
發明內容
專利目的
《一種製革廢液分步循環再利用工藝》的目的:實現從原皮到藍皮所有工序的廢水循環利用,特別是浸灰和鉻鞣工段,廢液可以無限次循環使用,除去自然狀態下的正常揮發和不可避免的撒漏外,廢液的回收率可達到100%,並且保證藍皮質量,使藍皮得革率增大1%-3.5%,收縮溫度提高3℃-12℃(與常規工藝相比),獲得了優質藍皮。由此生產的成品革各項性能指標均達要求,並有效降低了成革松面率,提高了成革的緊實度。並可實現節約化料15%-55%,如節約鉻粉40%-50%,部分化料可實現節約90%以上,個別化料如食鹽可實現節約100%,減少該階段污水排放75%-90%。
技術方案
《一種製革廢液分步循環再利用工藝》其特徵在於在預浸水、主浸水、浸灰、脫灰軟化、浸酸鉻鞣工序中分步進行廢液循環再利用,上述工序全部實現全封閉循環。包括如下步驟:
(1)預浸水工序的廢液循環再利用:在預浸水轉鼓旁設定預浸水廢液儲液池,來自預浸水工序的廢液濾去廢液中固形物後排入預浸水廢液儲液池,攪拌均勻,以備用於下批皮的預浸水;利用預浸水廢液進行預浸水的工藝是:以原皮重量計,加入100%-250%的預浸水廢液,加0.2%-0.4%殺菌劑,轉鼓轉動5-20分鐘,然後加入0.1%-0.8%浸水助劑、0.1%-1.0%脫脂劑、0.05%-0.5%純鹼,轉鼓轉動10-60分鐘,停20-60分鐘,轉停結合進行2-8次,預浸水結束後的廢水排入儲液池。應定期檢測廢液中的微生物數量,一般每循環二至三次檢測一次。
(2)主浸水工序的廢液循環再利用:在主浸水轉鼓旁設定主浸水廢液儲液池,來自主浸水工序的廢液濾去廢液中固形物後排入主浸水廢液儲液池,攪拌均勻,以備用於下批皮的主浸水;利用主浸水廢液進行主浸水的工藝是:以原皮重量計,加入70%-250%的主浸水廢液,加入0.1%-1.0%浸水助劑、0.1%-0.8%脫脂劑、0.1%-1.0%純鹼、0.05%-0.3%硫化鹼,轉鼓轉動30-80分鐘,停10-50分鐘,轉停結合進行1-4次,加0.1%-0.4%殺菌劑,轉鼓轉動5-20分鐘,過夜;次日連續轉10-50分鐘,主浸水結束廢水排入儲液池。應定期檢測廢液中的微生物數量,一般每循環二至三次檢測一次。
(3)浸灰工序的廢液循環再利用:在浸灰轉鼓旁設定浸灰廢液儲液池,來自浸灰工序的浸灰廢液濾去廢液中固形物後排入浸灰廢液儲液池,攪拌均勻,以備用於下批皮的浸灰;利用浸灰廢液進行浸灰的工藝是:以原皮重量計,加20%-90%浸灰廢液、0.15%-0.3%脫脂劑、0.1%-0.5%硫氫化鈉,轉鼓轉動10-40分鐘,停5-15分鐘,轉停結合進行3-6次;再加30%-90%浸灰廢液、0.2%-1.0%石灰、0.2%-0.6%硫化鈉、0.2%-0.5%硫氫化鈉、0.3%-1.5%浸灰劑,轉鼓轉動10-50分鐘,停5-30分鐘,轉停結合進行2-4次;再加20-60%浸灰廢液、0.2%-1.0%硫化鈉、0.05%-0.4%氫氧化鈉、0.1%-0.8%浸灰劑,轉鼓轉動30-90分鐘,停10-40分鐘,轉停結合進行2-4次;補加10%-20%清水、0.5%-2.0%石灰,轉停各10-40分鐘,然後每轉5-10分鐘停20-40分鐘,進行2-4次,然後每轉動5-10分鐘停30-120分鐘,過夜;每次使用前均需化驗廢灰液中硫化鹼、Ca等含量。在浸灰過程中,視毛根脫落程度及時利用濾毛機濾毛;
(4)復灰工序的廢液循環再利用:在復灰轉鼓旁設定復灰廢液儲液池,來自復灰工序的廢液濾去廢液中固形物後排入復灰廢液儲液池,攪拌均勻,以備用於下批皮的復灰;利用復灰廢液進行復灰的工藝是:以灰皮重量計,加入70%-220%的廢液,0.2%-1.5%石灰,0.05%-1.0%Na2S(或NaHS),0.1%-0.7%浸灰劑,0.05%-0.3%燒鹼,轉30分鐘左右,停30-60分鐘,轉5-20分鐘停30-60分鐘(共反覆3-8次),過夜或直接出鼓;復灰結束後廢水排入儲液池;
(5)脫灰軟化工序的廢液循環再利用:在脫灰軟化轉鼓旁設定脫灰軟化廢液儲液池,來自脫灰軟化工序的廢液濾去廢液中固形物後排入脫灰軟化廢液儲液池,攪拌均勻,以備用於下批皮的脫灰軟化;利用脫灰軟化廢液進行脫灰軟化的工藝是:以灰皮重量計,加入30%-220%的廢液,加0.05%-0.45%脫脂劑、0.2%-1.5%脫灰劑、0.2%-1.5%硫酸銨、0.05%-0.5%鹽酸,0.1%-0.5%醋酸,轉鼓轉動15-60分鐘,加0%-0.3%軟化酶,轉動15-40分鐘。脫灰軟化結束後廢水排入儲液池。每循環一次都應檢測廢液中的蛋白酶及微生物數量,蛋白酶檢測最好使用液質聯用儀,亦可使用光電比色法,根據檢測結果確定應加入的軟化酶數量以及是否需要加入防腐劑;
(6)浸酸鉻鞣工序的廢液循環再利用:在浸酸鉻鞣轉鼓旁設定鉻鞣廢液儲液池,該池最好深至地下2-8米以利控溫,且最好有備用池。來自鉻鞣工序的廢液濾去廢液中固形物後排入鉻鞣廢液儲液池,經過降溫後,用酸調節鉻鞣廢液的pH值到0.2-1.2,攪拌均勻,以備用於下批皮的浸酸鉻鞣。利用鉻鞣廢液進行浸酸鉻鞣的工藝是:以灰皮重量計,加20%-100%鉻鞣廢液、0.1%-0.4%防霉劑,0%-5%鹽,或其它有抑制酸腫作用的物質,轉鼓轉動5-30分鐘,0.3%-0.6%甲酸,轉動10-40分鐘,0.2%-0.7%硫酸,平分二至四次加入,每次間隔5-30分鐘,轉鼓轉動70-100分鐘,加0%-0.5%加脂劑,轉動15-50分鐘,停1-2小時;加入0.5%-3.0%鉻粉,轉鼓轉動20-60分鐘,再加入0.5%-3.0%鉻粉,轉動0.5-2.0小時,加入0.1%-0.7%甲酸鈉,轉15-55分鐘,加入0.15%-0.45%提鹼劑,轉動2.0-5.5小時,補加20%-80%鉻鞣廢液,後升溫至28℃-38℃,轉動2-5小時。應定期化驗廢鉻液中鉻含量及pH值。應定期檢測廢液中的微生物數量,一般循環三至五次檢測一次,主要檢測黴菌數量,根據檢測結果確定防霉劑的用量。
上述工藝中,每個儲液池都裝有攪拌裝置(個別池亦可人工攪拌)。經預浸水、主浸水和浸灰後的灰皮進行去肉或片皮,去肉或片皮過程中產生的廢液分別收集入預浸水、主浸水及浸灰廢液儲液池以備循環再利用。經浸水、浸灰、脫灰軟化工序和浸酸鉻鞣工序處理後的皮可以免去常規水洗步驟,亦可進行水洗,並將水洗液收集排入水洗廢液池以備循環使用。
該發明所使用的初始廢液分別來自於傳統的主浸水、浸灰、脫灰軟化、浸酸鉻鞣工序,各種廢液的構成情況是本領域技術人員已知的。一般來說,主浸水廢液中含有浸水劑、NaCl、Na2CO3、脫脂劑、油脂及其分解產物、毛、角蛋白質、粘蛋白、肉、血等,其中,一般情況下,廢液中殘留的脫脂劑含量通常為初始用量的15%-30%,廢液中殘留的浸水劑含量通常為初始用量的15%-25%,廢液中殘留的Na2CO3含量通常為初始用量的30%-50%;浸灰廢液中含有油脂及其分解產物、鹽類、石灰、浸灰劑、S、OH、Na、Ca、蛋白質及其分解產物、酶類及胺類物質等,其中,一般情況下,廢液中殘留的石灰通常為初始用量的37%-55%,廢液中殘留的Na2S含量通常為2.4g/1-3.2g/l;脫灰軟化廢液中含有蛋白質及其分解產物、脫灰劑、脫脂劑、油脂及其分解產物、酶類及銨鹽、胺類物質等,其中廢液中殘留的酶含量通常為初始用量的30%-50%,廢液中殘留的銨鹽含量通常為初始用量的30%-40%;鉻鞣廢液中含有Cr、Cl、SO4、蛋白質及其分解產物、油脂及其分解產物等,其中廢液中殘留的Cr通常為2.8g/l-3.2g/l,Cl通常為7g/l-15g/l,廢液中殘留的酸根含量通常為初始用量的30%-45%。
優選地,主浸水工序和浸灰工序可以採用同一個轉鼓,在轉鼓旁分別設定預浸水、主浸水廢液儲液池和浸灰廢液儲液池,以閥門的方式控制轉鼓向各儲液池的廢液排放。具體來說,當預浸水、主浸水和浸灰同用一個轉鼓時,在轉鼓上設定閥門1,用於將預浸水廢液排放到預浸水廢液儲液池,同時,在轉鼓上設定閥門2,用於將主浸水廢液排放到主浸水廢液儲液池,同時,在轉鼓上設定閥門3,用於將浸灰廢液排放到浸灰廢液儲液池。排放預浸水廢液時,閥門1打開,閥門2、3關閉,廢液經分流管道排放到預浸水廢液儲液池;排放主浸水廢液時,閥門2打開,閥門1、3關閉,廢液經分流管道排放到主浸水廢液儲液池;排放浸灰廢液時,閥門1、2關閉,閥門3打開,廢液經分流管道排放到浸灰廢液儲液池。
類似地,脫灰軟化工序和鉻鞣工序也可以採用同一個轉鼓,在轉鼓旁分別設定脫灰軟化廢液儲液池和鉻鞣廢液儲液池,以閥門的方式控制轉鼓向各儲液池的廢液排放。具體來說,當脫灰軟化和鉻鞣同用一個轉鼓時,在轉鼓上設定閥門4,用於將脫灰軟化廢液排放到脫灰軟化廢液儲液池,同時,在轉鼓上設定閥門5,用於將鉻鞣廢液排放到鉻鞣廢液儲液池。排放脫灰軟化廢液時,閥門4打開,閥門5關閉,廢液經分流管道排放到脫灰軟化廢液儲液池;排放鉻鞣廢液時,閥門4關閉,閥門5打開,廢液經分流管道排放到鉻鞣廢液儲液池。
在該發明的廢液循環再利用過程中,對於浸水、浸灰、脫灰軟化、浸酸鉻鞣這些全封閉廢液循環的工序而言,可以根據各廢液儲液池中廢液的粘稠程度定期對廢液進行清潔化處理,除去其中的固體物,並定期消毒,定期檢測廢液中的微生物、蛋白酶、pH值、鉻離子、鈣離子、硫化物及其它相關成份,液體繼續循環再利用。例如,用壓濾的方式對廢液進行清潔化處理,經壓濾分離出的固體物用於填坑或制磚或其它用途,分離出的廢水收集入各廢液儲液池以備循環再利用。
對廢液進行清潔化處理周期可以根據具體生產狀況進行調整,當廢液的粘稠程度過大,例如,使廢液的抽送效率降低、限制了皮化材料的溶解分散等,以致於不利於皮革生產時,可進行清潔化處理。對於具體的廢液清潔化處理周期,本領域技術人員可以根據經驗適當調整。一般情況下,對於採用傳統工藝的中型製革廠來說,浸灰廢液儲液池可以每隔15-40天清理一次,脫灰軟化廢液儲液池可以每隔20-50天清理一次,鉻鞣廢液儲液池可以每隔15-40天清理一次。
改善效果
《一種製革廢液分步循環再利用工藝》實現了製革中從原皮到藍濕皮各工段的廢水循環再利用,而且可以無限次循環,幾乎不排放污水,特別是利用廢鉻液,後期的補水升溫比常規工藝少3℃-15℃,節省了能源,且獲得了優質藍皮。相對於傳統工藝而言,能夠節約以下化料:脫脂劑15%-30%,浸水劑15%-25%,純鹼30%-50%,Na2S35%-50%,NaHS30%-45%,石灰37%-55%,浸灰酶20%-40%,浸灰劑10%-30%,硫酸銨30%-50%,脫灰劑15%-30%,軟化酶30%-100%,甲酸30%-45%,硫酸30%-50%,鹽100%,鉻粉35%-55%。當然具體工藝不同,節約化料的量也略有不同,但一般來說,可實現節約化料15%-55%,減少污水排放70%-85%,藍濕皮得革率增大1%-3.5%;收縮溫度提高3℃-12℃,獲得了優質藍濕皮。由此生產的成品革各項性能指標均達要求,並有效降低了成革松面率,提高了成革的緊實度。
附圖說明
圖1是根據《一種製革廢液分步循環再利用工藝》的新型製革廢液分步循環再利用工藝的流程示意圖。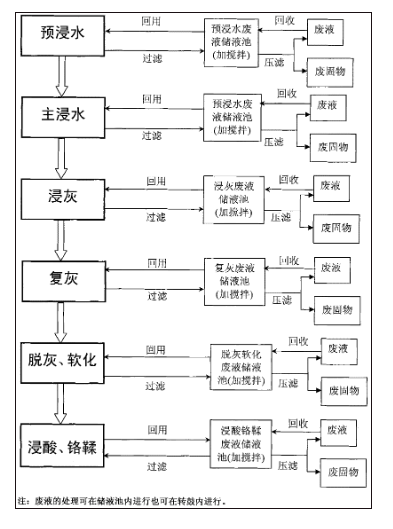
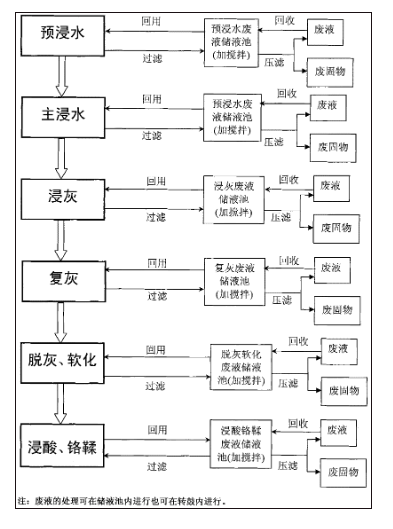
權利要求
1.《一種製革廢液分步循環再利用工藝》其特徵在於在預浸水、主浸水、浸灰、脫灰軟化、浸酸鉻鞣工序中分步進行廢液循環再利用,上述工序全部實現全封閉循環。包括如下步驟:
(1)預浸水工序的廢液循環再利用:在預浸水轉鼓旁設定預浸水廢液儲液池,來自預浸水工序的廢液濾去廢液中固形物後排入預浸水廢液儲液池,攪拌均勻,以備用於下批皮的預浸水;利用預浸水廢液進行預浸水的工藝是:以原皮重量計,加入100%-250%的預浸水廢液,加0.2%-0.4%殺菌劑,轉鼓轉動5-20分鐘,然後加入0.1%-0.8%浸水助劑、0.1%-1.0%脫脂劑、0.05%-0.5%純鹼,轉鼓轉動10-60分鐘,停20-60分鐘,轉停結合進行2-8次,預浸水結束後的廢水排入儲液池。應定期檢測廢液中的微生物數量,一般每循環二至三次檢測一次。
(2)主浸水工序的廢液循環再利用:在主浸水轉鼓旁設定主浸水廢液儲液池,來自主浸水工序的廢液濾去廢液中固形物後排入主浸水廢液儲液池,攪拌均勻,以備用於下批皮的主浸水;利用主浸水廢液進行主浸水的工藝是:以原皮重量計,加入70%-250%的主浸水廢液,加入0.1%-1.0%浸水助劑、0.1%-0.8%脫脂劑、0.1%-1.0%純鹼、0.05%-0.3%硫化鹼,轉鼓轉動30-80分鐘,停10-50分鐘,轉停結合進行1-4次,加0.1%-0.4%殺菌劑,轉鼓轉動5-20分鐘,過夜;次日連續轉10-50分鐘,主浸水結束廢水排入儲液池。應定期檢測廢液中的微生物數量,一般每循環二至三次檢測一次。
(3)浸灰工序的廢液循環再利用:在浸灰轉鼓旁設定浸灰廢液儲液池,來自浸灰工序的浸灰廢液濾去廢液中固形物後排入浸灰廢液儲液池,攪拌均勻,以備用於下批皮的浸灰;利用浸灰廢液進行浸灰的工藝是:以原皮重量計,加20%-90%浸灰廢液、0.15%-0.3%脫脂劑、0.1%-0.5%硫氫化鈉,轉鼓轉動10-40分鐘,停5-15分鐘,轉停結合進行3-6次;再加30%-90%浸灰廢液、0.2%-1.0%石灰、0.2%-0.6%硫化鈉、0.2%-0.5%硫氫化鈉、0.3%-1.5%浸灰劑,轉鼓轉動10-50分鐘,停5-30分鐘,轉停結合進行2-4次;再加20-60%浸灰廢液、0.2%-1.0%硫化鈉、0.05%-0.4%氫氧化鈉、0.1%-0.8%浸灰劑,轉鼓轉動30-90分鐘,停10-40分鐘,轉停結合進行2-4次;補加10%-20%清水、0.5%-2.0%石灰,轉停各10-40分鐘,然後每轉5-10分鐘停20-40分鐘,進行2-4次,然後每轉動5-10分鐘停30-120分鐘,過夜;每次使用前均需化驗廢灰液中硫化鹼、Ca等含量。在浸灰過程中,視毛根脫落程度及時利用濾毛機濾毛;
(4)復灰工序的廢液循環再利用:在復灰轉鼓旁設定復灰廢液儲液池,來自復灰工序的廢液濾去廢液中固形物後排入復灰廢液儲液池,攪拌均勻,以備用於下批皮的復灰;利用復灰廢液進行復灰的工藝是:以灰皮重量計,加入70%-220%的廢液,0.2%-1.5%石灰,0.05%-1.0%Na2S(或NaHS),0.1%-0.7%浸灰劑,0.05%-0.3%燒鹼,轉30分鐘左右,停30-60分鐘,轉5-20分鐘停30-60分鐘(共反覆3-8次),過夜或直接出鼓;復灰結束後廢水排入儲液池;
(5)脫灰軟化工序的廢液循環再利用:在脫灰軟化轉鼓旁設定脫灰軟化廢液儲液池,來自脫灰軟化工序的廢液濾去廢液中固形物後排入脫灰軟化廢液儲液池,攪拌均勻,以備用於下批皮的脫灰軟化;利用脫灰軟化廢液進行脫灰軟化的工藝是:以灰皮重量計,加入30%-220%的廢液,加0.05%-0.45%脫脂劑、0.2%-1.5%脫灰劑、0.2%-1.5%硫酸銨、0.05%-0.5%鹽酸,0.1%-0.5%醋酸,轉鼓轉動15-60分鐘,加0%-0.3%軟化酶,轉動15-40分鐘。脫灰軟化結束後廢水排入儲液池。每循環一次都應檢測廢液中的蛋白酶及微生物數量,蛋白酶檢測最好使用液質聯用儀,亦可使用光電比色法,根據檢測結果確定應加入的軟化酶數量以及是否需要加入防腐劑;
(6)浸酸鉻鞣工序的廢液循環再利用:在浸酸鉻鞣轉鼓旁設定鉻鞣廢液儲液池,該池最好深至地下2-8米以利控溫,且最好有備用池。來自鉻鞣工序的廢液濾去廢液中固形物後排入鉻鞣廢液儲液池,經過降溫後,用酸調節鉻鞣廢液的pH值到0.2-1.2,攪拌均勻,以備用於下批皮的浸酸鉻鞣。利用鉻鞣廢液進行浸酸鉻鞣的工藝是:以灰皮重量計,加20%-100%鉻鞣廢液、0.1%-0.4%防霉劑,0%-5%鹽,或其它有抑制酸腫作用的物質,轉鼓轉動5-30分鐘,0.3%-0.6%甲酸,轉動10-40分鐘,0.2%-0.7%硫酸,平分二至四次加入,每次間隔5-30分鐘,轉鼓轉動70-100分鐘,加0%-0.5%加脂劑,轉動15-50分鐘,停1-2小時;加入0.5%-3.0%鉻粉,轉鼓轉動20-60分鐘,再加入0.5%-3.0%鉻粉,轉動0.5-2.0小時,加入0.1%-0.7%甲酸鈉,轉15-55分鐘,加入0.15%-0.45%提鹼劑,轉動2.0-5.5小時,補加20%-80%鉻鞣廢液,後升溫至28℃-38℃,轉動2-5小時。應定期化驗廢鉻液中鉻含量及pH值。應定期檢測廢液中的微生物數量,一般循環三至五次檢測一次,主要檢測黴菌數量,根據檢測結果確定防霉劑的用量。
2.如權利要求1所述的新型製革廢液分步循環再利用工藝,其特徵在於每個儲液池都安裝有攪拌裝置,亦可進行人工攪拌。
3.如權利要求1所述的新型製革廢液分步循環再利用工藝,其特徵在於經浸水及浸灰後的皮進行去肉及片皮,去肉和片皮過程中產生的廢液收集入浸水和浸灰廢液儲液池以備循環再利用。
4.如權利要求1所述的新型製革廢液分步循環再利用工藝,其特徵在於預浸水、主浸水和浸灰工序可採用同一個轉鼓,在轉鼓旁分別設定預浸水、主浸水廢液儲液池和浸灰廢液儲液池,以閥門的方式或其它分流方式控制轉鼓向各儲液池的廢液排放。
5.如權利要求1所述的新型製革廢液分步循環再利用工藝,其特徵在於脫灰軟化工序和鉻鞣工序採用同一個轉鼓,在轉鼓旁分別設定脫灰軟化廢液儲液池和鉻鞣廢液儲液池,以閥門的方式控制轉鼓向各儲液池的廢液排放。
6.如權利要求1所述的新型製革廢液分步循環再利用工藝,其特徵在於根據各廢液儲液池中廢液的粘稠程度定期對廢液進行清潔化處理,除去其中的固體物,液體繼續循環再利用。
7.如權利要求6所述的新型製革廢液分步循環再利用工藝,其特徵在於用壓濾的方式對廢液進行清潔化處理,經壓濾分離出的固體物用於填坑或制磚或其它用途,分離出的廢水收集入各廢液儲液池以備循環再利用。
8.如權利要求1所述的新型製革廢液分步循環再利用工藝,其特徵在於經浸灰、脫灰軟化及鉻鞣工序處理後的皮免去常規水洗步驟。亦可進行水洗,並將水洗廢液進行循環再利用。當循環利用灰皮的水洗廢液時應加入酸類物質將其pH值調至6-10之間。
9.如權利要求1所述的新型製革廢液分步循環再利用工藝,其特徵在於在鉻鞣廢液儲液池旁再設定備用池。其它工序如浸灰和脫灰軟化工序等亦可設定備用池。
10.如權利要求1所述的新型製革廢液分步循環再利用工藝,其特徵在於各種化學材料的用量、升降溫幅度、操作時間及操作步驟均可做出大幅度調整。
11.如權利要求1所述的新型製革廢液分步循環再利用工藝,其特徵在於其中任何一道工序的廢液循環再利用工藝,包括預浸水、主浸水、浸灰、復灰、脫灰軟化、浸酸鞣製等均可單獨或與其它工序結合使用。
12.如權利要求1所述的新型製革廢液分步循環再利用工藝,其特徵在於在浸灰過程中,視毛根脫落程度及時利用濾毛機濾毛。如所做原皮為山羊皮、綿羊皮和豬皮時,大部分毛的去除在鼓外進行,所剩部分毛亦可在浸灰過程中使用濾毛機濾出。
13.如權利要求1所述的新型製革廢液分步循環再利用工藝,其特徵在於浸酸鉻鞣過程中,鹽的加入量為0,亦可加入少量的鹽類或其它有抑制酸腫作用的物質。
14.如權利要求1所述的新型製革廢液分步循環再利用工藝,其特徵在於鉻粉的總用量為2.5%-5.5%。
實施方式
如圖所示,在預浸水工序中,原皮進行預浸水後,廢液濾去固形物後排放到預浸水廢液儲液池,用攪拌器攪拌均勻,然後由耐鹼泵抽出排入到預浸水轉鼓,利用預浸水廢液進行預浸水的工藝是:以原皮重量計,加入200%的預浸水廢液,加0.25%殺菌劑,轉鼓轉動15分鐘,然後加入0.35%浸水助劑、0.2%脫脂劑,轉鼓轉動20分鐘,停40分鐘,轉停結合進行4次,預浸水結束後的廢水排入儲液池。在主浸水工序中,主浸水廢液濾去固形物後排入主浸水廢液儲液池,攪拌均勻,然後由耐鹼泵抽出排入到主浸水轉鼓,利用主浸水廢液進行主浸水的工藝是:以原皮重量計,加入200%的主浸水廢液,加入0.7%浸水助劑、0.3%脫脂劑、0.5%純鹼、0.1%硫化鹼,轉鼓轉動40分鐘,停40分鐘,轉停結合進行3次,加0.3%殺菌劑,轉鼓轉動20分鐘,過夜;次日連續轉40分鐘,主浸水結束廢水排入儲液池。
在浸灰工序中,浸灰廢液濾去固形物後排入浸灰廢液儲液池,攪拌均勻,然後由耐鹼泵抽出排入到浸灰轉鼓,利用浸灰廢液進行浸灰工藝是:以原皮重量計,加70%浸灰廢液、0.2%脫脂劑、0.1%硫氫化鈉,轉鼓轉動30分鐘,停5分鐘,轉停結合進行4次;再加70%浸灰廢液、0.7%石灰、0.3%硫化鈉、0.2%硫氫化鈉、1.0%浸灰劑,轉鼓轉動40分鐘,停20分鐘,轉停結合進行2次;再加50%浸灰廢液、0.3%硫化鈉、0.3%氫氧化鈉、0.15%浸灰酶、0.6%浸灰劑,轉鼓轉動60分鐘,停30分鐘,轉停結合進行2次;補加20%清水、1.5%石灰,轉停各30分鐘,然後每轉5分鐘停25分鐘,進行2次,然後每轉動5分鐘停90分鐘,過夜;將灰皮進行去肉片皮,然後進行復灰。在復灰工序中,復灰廢液濾去固形物後排入復灰廢液儲液池,攪拌均勻,然後由耐鹼泵抽出排入到浸灰轉鼓,利用復灰廢液進行復灰的工藝是:以灰皮重量計,加入100%的廢液,0.8%石灰,0.2%Na2S(或NaHS),0.4%浸灰劑,0.10%燒鹼,轉30分鐘,停40分鐘,轉5分鐘停55分鐘(共反覆6次),過夜或直接出鼓;復灰結束後廢水排入儲液池。在脫灰軟化工序中,脫灰軟化廢液濾去固形物後排入脫灰軟化廢液儲液池,然後由耐鹼泵抽出排入到脫灰軟化轉鼓,利用廢液進行脫灰軟化的工藝是:加入100%的脫灰軟化廢液,加0.2%脫脂劑、0.6%脫灰劑、1.2%硫酸銨、0.2%鹽酸、0.3%醋酸,轉鼓轉動40分鐘,加0.25%軟化酶,轉動30分鐘。在浸酸鉻鞣工序中,廢鉻液濾去固形物後排入到儲液池,用硫酸調其pH值為0.6,攪拌均勻,然後由耐酸泵抽出流入到鉻鞣轉鼓,利用鉻鞣廢液進行浸酸鉻鞣的工藝是:70%廢鉻液、0.25%防霉劑,轉鼓轉動10分鐘,0.6%甲酸(用廢鉻液稀釋其濃度至5%左右),轉動20分鐘,0.6%硫酸(用廢鉻液稀釋其濃度至5%左右),平分三次加入,每間隔10分鐘添加一次,轉動90分鐘,轉動30分鐘,停1.5小時;2.0%鉻粉,轉動30分鐘,2%鉻粉,轉動1小時,0.5%甲酸鈉,轉30分鐘,0.25%提鹼劑,轉動4小時,後升溫至35℃,補加50%廢鉻液,轉動3小時。
測得藍濕皮的收縮溫度為105℃,藍濕皮顏色為湖藍色,粒面細緻。
上述預浸水、主浸水、浸灰、脫灰軟化、浸酸鉻鞣工序的循環廢液視情況定期進行壓濾處理,壓濾得到的廢液回收入相應的廢液池繼續循環再利用,壓濾得到的廢固物用於填坑或其他。
榮譽表彰
(概述圖為《一種製革廢液分步循環再利用工藝》的摘要附圖)