專利背景
普通高速高壓壓射成型工藝需要680℃左右的高溫鋁液快速充型,成型過程中易卷氣形成內部縮孔和氣孔缺陷,鑄件加工組裝後易產生氣密不良;壓鑄成型後的冷卻過程產品熱變形大,壓鑄毛坯變形量可達到2毫米左右,清理時需要人工校形保證後續加工需要的平面度,給加工定位造成困難,也對產品的質量和精確度造成不利影響。
截至2014年9月,普通壓鑄工藝產品內部質量不穩定,組裝產品氣密不良比例在10%左右;壓鑄件的清理工序人工勞動強度大,外觀質量不易保證,是壓鑄生產的瓶頸工序,制約了壓鑄行業的快速發展。
發明內容
專利目的
《一種用於半固態金屬壓鑄成型的壓鑄方法》需要解決的技術問題就在於提供一種用於半固態金屬壓鑄成型的壓鑄方法,該方法採用半固態漿料的壓鑄方式,使壓鑄件產品內部緻密、不會產生氣孔,毛坯壓鑄件的形變數極小,不需要對壓鑄件進行複雜的表面處理,能夠保證產品最佳的質量和性能。
技術方案
《一種用於半固態金屬壓鑄成型的壓鑄方法》採用技術方案為:
一種用於半固態金屬壓鑄成型的壓鑄方法,所述壓鑄方法使用半固態壓鑄機作為加工設備,採用製漿機作為製備半固態漿料和送料的設備;所述壓鑄方法的設備布局為:半固態壓鑄機的左側為製漿機,半固態壓鑄機的右側是用於向模具噴塗脫模劑的噴塗機,半固態壓鑄機的前側是用於將模具內壓鑄件取出的取件機,取件機的右側與傳送帶配合,傳送帶的右端為操作台,操作台上設有用於衝去壓鑄件上水口的油壓機;
所述壓鑄方法的步驟為:
(1)將模具安裝在半固態壓鑄機上,採用噴塗機將脫模劑噴塗到模具表面,然後合模;
(2)採用加熱爐將金屬原料熔化,將液態金屬原料放入保溫爐內保存;金屬原料為鋁合金金屬原料;
(3)製漿機將保溫爐內的液態金屬原料製備出半固態漿料;製漿機將熔化的金屬原料放入料勺內,然後將固態的金屬變質劑放入料勺的液態金屬原料內,使液態金屬原料降溫並產生大量的晶核,製備出半固態漿料;
(4)製漿機將半固態漿料輸送至半固態壓鑄機的模具內;由於半固態漿料的溫度較熔融狀態的金屬漿料溫度更低,更容易快速壓鑄成型,所以,半固態漿料在壓鑄成型後,其溫度較低,所以其壓鑄件出模後,具有一定的機械強度,不會因為溫度過高而在出模後發生變形,造成壓鑄件的形狀發生改變,確保了壓鑄件產品較佳的表面平整和精確規格,不需要後續加工中進行人工打磨使產品形狀矯形。
(5)半固態壓鑄機進行壓鑄動作,然後開模,取件機將模具內的壓鑄件取出放入傳送帶輸出;
(6)傳動帶將壓鑄件輸送至操作台,由油壓機衝掉壓鑄件上的水口,得到最終的壓鑄產品。
優選的,步驟(5)中的半固態壓鑄機為1000T的臥式冷室壓鑄機,壓鑄溫度為586℃~594℃,壓鑄速度為4.2米/秒,系統壓力為15.5兆帕,增壓壓力為29兆帕。壓鑄溫度的控制能夠使鋁合金在模具內快速冷卻定型,取出壓鑄件後,壓鑄件已經溫度較低,具有一定的機械強度,不會因為高溫而發生形變,確保了壓鑄件的形狀精確性。
優選的,步驟(3)中的液態金屬原料中各個組分的質量百分比為:矽6~7.5%,銅0.3~1.7%,鋅0.2~2.5%,鎳0.4~2.2%,鎂0.2~0.7%,鐵0.2~1.3%,其餘為鋁。該液態金屬原料可作為散熱殼體的壓鑄原料或者一般設備殼體的壓鑄原料,其具有極佳的機械強度和散熱效果,具體性能見表1中所示。
優選的,步驟(3)中製漿機製備半固態漿料的方法為:保溫爐內液態金屬原料的溫度為其液相線以上12℃~23℃;製漿機將保溫爐內熔化的金屬原料放入料勺內,然後將固態的金屬變質劑放入料勺內,金屬變質劑在料勺內吸收液態金屬原料的熱量後熔化,使液態金屬原料降溫並產生大量的晶核,製備出半固態漿料;在加入金屬變質劑的同時向料勺內的金屬原料中吹入氬氣以加速混合與冷卻,氬氣的吹入速度為13升/分鐘;金屬變質劑的加入量為料勺內金屬原料質量的1.5%~3.8%。這樣製備的半固態漿料,能夠在壓鑄機內完整填充模具空腔,不會產生氣泡,並且凝固後的壓鑄件具有極佳的機械強度和表面平整性。
優選的,金屬變質劑的組分與液態金屬原料的組分相同。相同組分的金屬變質劑能夠與液態金屬原料有效混合。
可選的,金屬變質劑的組分及各組分的質量比為:矽(6.55~6.90)、銅(0.22~0.85)、錳(0.003~0.008)、鎂(0.15~0.75)、鋅(0.03~0.075)、鈦(0.06~0.1)、鉛(0.03~0.05)、鋁(91.7~92.8)。經過大量的試驗驗證和選擇,該組分的金屬變質劑能夠使半固態漿料產生較佳的機械性能。
進一步優選的,金屬變質劑的組分及各組分的質量比為:矽(6.70)、銅(0.57)、錳(0.007)、鎂(0.38)、鋅(0.047)、鈦(0.08)、鉛(0.04)、鋁(92.5)。
改善效果
《一種用於半固態金屬壓鑄成型的壓鑄方法》用於半固態金屬壓鑄成型的壓鑄方法,採用半固態漿料的壓鑄方式,在壓鑄過程中壓鑄件產品內部緻密、不會產生氣孔,確保了壓鑄件產品最佳的內部結構和機械性能,確保了產品的質量;
《一種用於半固態金屬壓鑄成型的壓鑄方法》用於半固態金屬壓鑄成型的壓鑄方法,採用半固態漿料壓鑄,相比於傳統的高速高壓壓射成型工藝,其出模時的壓鑄件溫度較低,毛坯壓鑄件在出模時具有一定的機械強度,而傳統的液態壓鑄出模壓鑄件,其溫度較高,出模時容易發生形變;《一種用於半固態金屬壓鑄成型的壓鑄方法》的毛坯壓鑄件的形變數極小,不需要對壓鑄件進行複雜的表面處理,能夠保證產品最佳的形狀和表面平整性;
《一種用於半固態金屬壓鑄成型的壓鑄方法》用於半固態金屬壓鑄成型的壓鑄方法,採用半固態壓鑄工藝,使得壓鑄件產品中具有較多的球狀晶體,使壓鑄件具有更高的機械性能。
附圖說明
圖1為《一種用於半固態金屬壓鑄成型的壓鑄方法》用於半固態金屬壓鑄成型的壓鑄方法的設備布局示意圖。
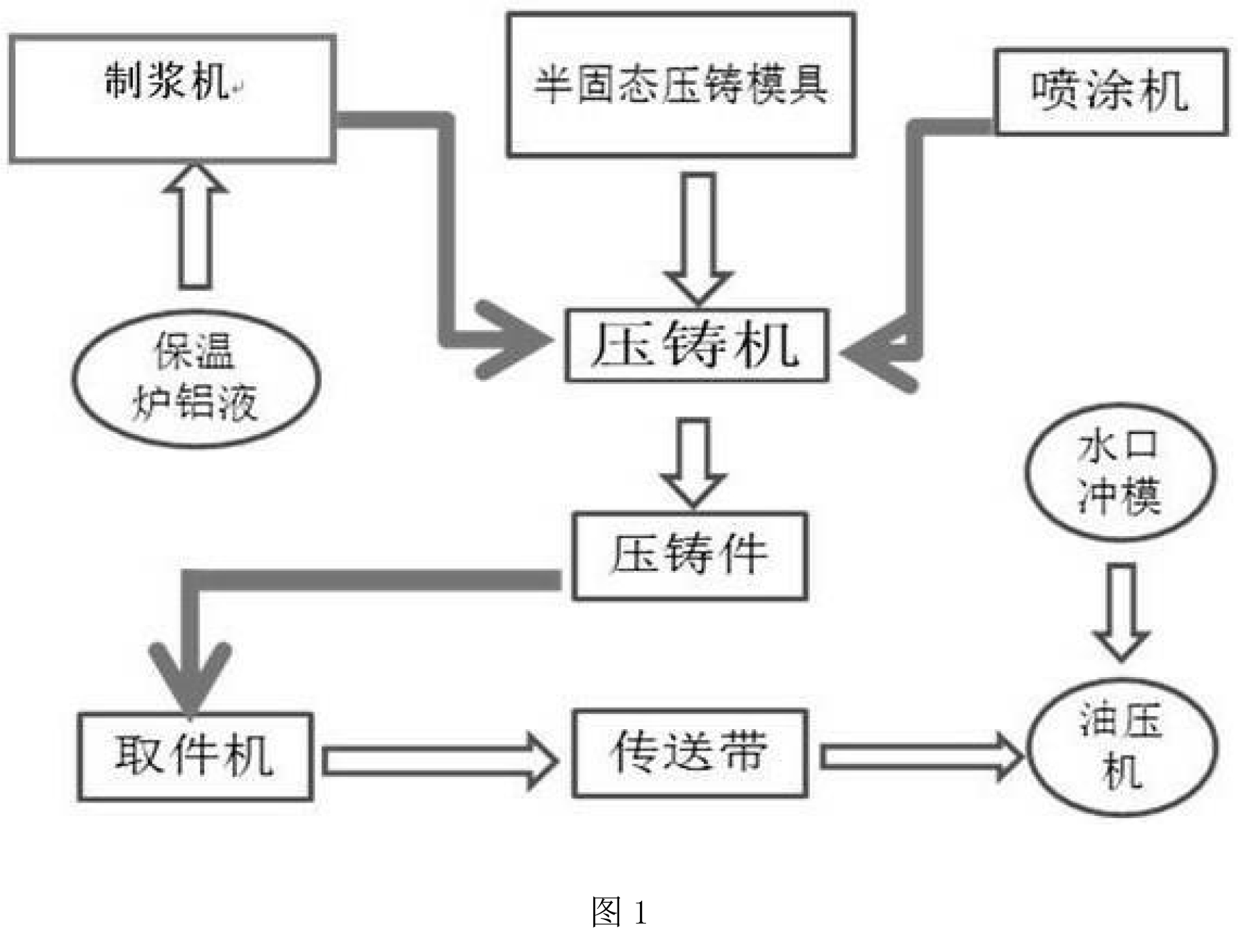
圖2為《一種用於半固態金屬壓鑄成型的壓鑄方法》壓鑄方法的流程圖。
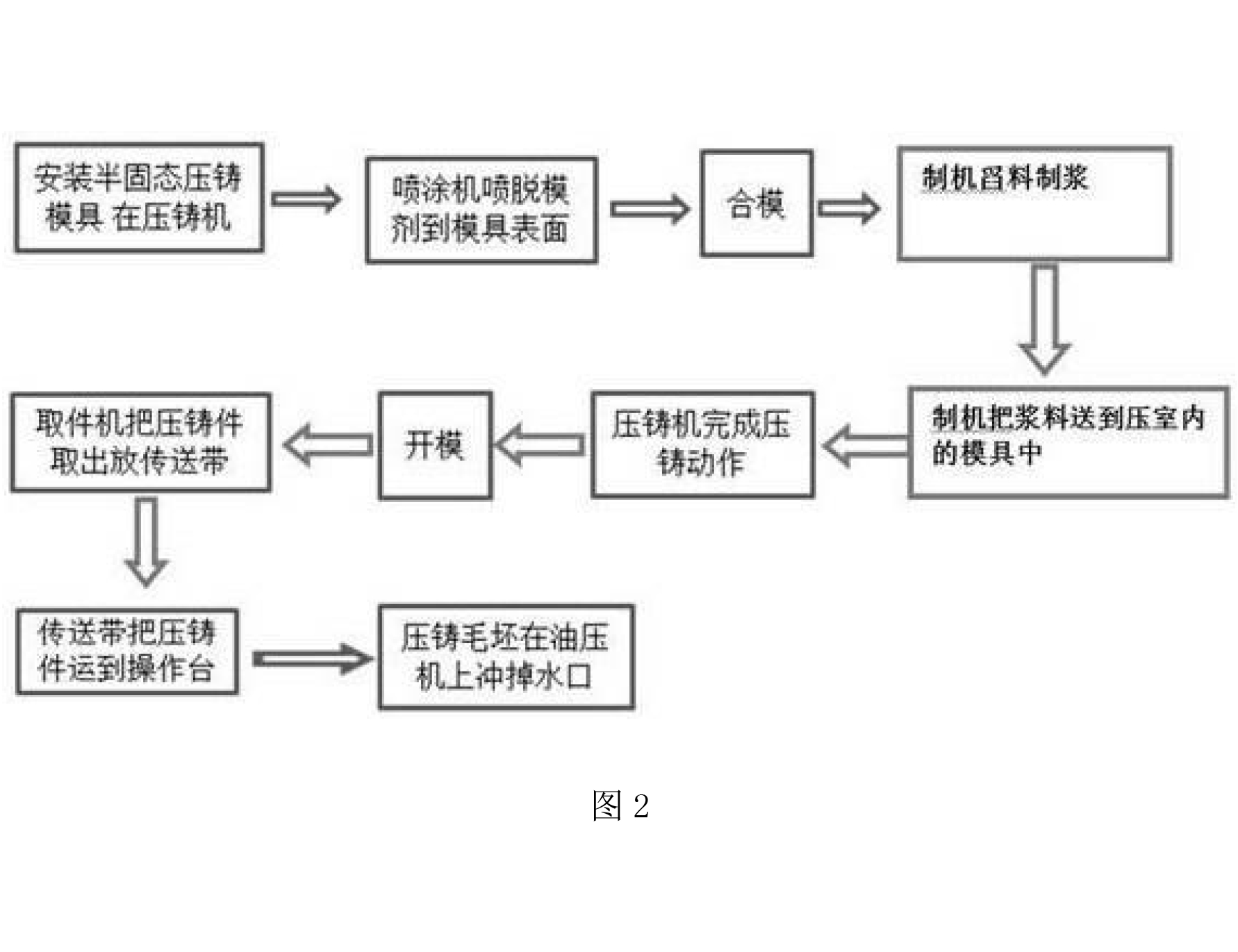
技術領域
《一種用於半固態金屬壓鑄成型的壓鑄方法》涉及一種金屬壓鑄方法,具體涉及一種用於半固態金屬壓鑄成型的壓鑄方法。
權利要求
1.一種用於半固態金屬壓鑄成型的壓鑄方法,其特徵在於,所述壓鑄方法使用半固態壓鑄機作為加工設備,採用製漿機作為製備半固態漿料和送料的設備;所述壓鑄方法的設備布局為:半固態壓鑄機的左側為製漿機,半固態壓鑄機的右側是用於向模具噴塗脫模劑的噴塗機,半固態壓鑄機的前側是用於將模具內壓鑄件取出的取件機,取件機的右側與傳送帶配合,傳送帶的右端為操作台,操作台上設有用於衝去壓鑄件上水口的油壓機;
所述壓鑄方法的步驟為:
(1)將模具安裝在半固態壓鑄機上,採用噴塗機將脫模劑噴塗到模具表面,然後合模;
(2)採用加熱爐將金屬原料熔化,將液態金屬原料放入保溫爐內保存;金屬原料為鋁合金金屬原料;
(3)製漿機將保溫爐內的液態金屬原料製備出半固態漿料;
(4)製漿機將半固態漿料輸送至半固態壓鑄機的模具內;
(5)半固態壓鑄機進行壓鑄動作,然後開模,取件機將模具內的壓鑄件取出放入傳送帶輸出;
(6)傳送帶將壓鑄件輸送至操作台,由油壓機衝掉壓鑄件上的水口,得到最終的壓鑄產品;其中,步驟(5)中的半固態壓鑄機為1000T的臥式冷室壓鑄機,壓鑄溫度為586℃~594℃,壓鑄速度為4.2米/秒,系統壓力為15.5兆帕,增壓壓力為29兆帕;步驟(3)中的液態金屬原料中各個組分的質量百分比為:矽6~7.5%,銅0.3~1.7%,鋅0.2~2.5%,鎳0.4~2.2%,鎂0.2~0.7%,鐵0.2~1.3%,其餘為鋁。
2.如權利要求1所述的壓鑄方法,其特徵在於,步驟(3)中製漿機製備半固態漿料的方法為:保溫爐內液態金屬原料的溫度為其液相線以上12℃~23℃;製漿機將保溫爐內熔化的金屬原料放入料勺內,然後將固態的金屬變質劑放入料勺內,金屬變質劑在料勺內吸收液態金屬原料的熱量後熔化,使液態金屬原料降溫並產生大量的晶核,製備出半固態漿料;在加入金屬變質劑的同時向料勺內的金屬原料中吹入氬氣以加速混合與冷卻,氬氣的吹入速度為13升/分鐘;金屬變質劑的加入量為料勺內金屬原料質量的1.5%~3.8%。
3.如權利要求2所述的壓鑄方法,其特徵在於,金屬變質劑的組分與液態金屬原料的組分相同。
實施方式
《一種用於半固態金屬壓鑄成型的壓鑄方法》採用技術方案為一種用於半固態金屬壓鑄成型的壓鑄方法,所述壓鑄方法使用半固態壓鑄機作為加工設備,採用製漿機作為製備半固態漿料和送料的設備;所述壓鑄方法的設備布局為:半固態壓鑄機的左側為製漿機,半固態壓鑄機的右側是用於向模具噴塗脫模劑的噴塗機,半固態壓鑄機的前側是用於將模具內壓鑄件取出的取件機,取件機的右側與傳送帶配合,傳送帶的右端為操作台,操作台上設有用於衝去壓鑄件上水口的油壓機;
所述壓鑄方法的步驟為:
(1)將模具安裝在半固態壓鑄機上,採用噴塗機將脫模劑噴塗到模具表面,然後合模;
(2)採用加熱爐將金屬原料熔化,將液態金屬原料放入保溫爐內保存;金屬原料為鋁合金金屬原料;
(3)製漿機將保溫爐內的液態金屬原料製備出半固態漿料;製漿機將熔化的金屬原料放入料勺內,然後將固態的金屬變質劑放入料勺的液態金屬原料內,使液態金屬原料降溫並產生大量的晶核,製備出半固態漿料;液態金屬原料中各個組分的質量百分比為:矽6~7.5%,銅0.3~1.7%,鋅0.2~2.5%,鎳0.4~2.2%,鎂0.2~0.7%,鐵0.2~1.3%,其餘為鋁。
製漿機製備半固態漿料的方法為:保溫爐內液態金屬原料的溫度為其液相線以上12℃~23℃;製漿機將保溫爐內熔化的金屬原料放入料勺內,然後將固態的金屬變質劑放入料勺內,金屬變質劑在料勺內吸收液態金屬原料的熱量後熔化,使液態金屬原料降溫並產生大量的晶核,製備出半固態漿料;在加入金屬變質劑的同時向料勺內的金屬原料中吹入氬氣以加速混合與冷卻,氬氣的吹入速度為13升/分鐘;金屬變質劑的加入量為料勺內金屬原料質量的1.8%。
金屬變質劑的組分及各組分的質量比為:矽(6.70)、銅(0.57)、錳(0.007)、鎂(0.38)、鋅(0.047)、鈦(0.08)、鉛(0.04)、鋁(92.5)。
(4)製漿機將半固態漿料輸送至半固態壓鑄機的模具內;由於半固態漿料的溫度較熔融狀態的金屬漿料溫度更低,更容易快速壓鑄成型,所以,半固態漿料在壓鑄成型後,其溫度較低,所以其壓鑄件出模後,具有一定的機械強度,不會因為溫度過高而在出模後發生變形,造成壓鑄件的形狀發生改變,確保了壓鑄件產品較佳的表面平整和精確規格,不需要後續加工中進行人工打磨使產品形狀矯形。
(5)半固態壓鑄機進行壓鑄動作,然後開模,取件機將模具內的壓鑄件取出放入傳送帶輸出;半固態壓鑄機為1000T的臥式冷室壓鑄機,壓鑄溫度為586℃~594℃,壓鑄速度為4.2米/秒,系統壓力為15.5兆帕,增壓壓力為29兆帕。
(6)傳動帶將壓鑄件輸送至操作台,由油壓機衝掉壓鑄件上的水口,得到最終的壓鑄產品。
針對實施例1製備得到的鋁合金壓鑄件產品中隨機抽取三個壓鑄件產品,對其進行的性能測試,具體測試結果見表1,具體測試方法為:
(1)力學性能:採用室溫拉伸實驗法(GB/T228.1),設備為拉伸試驗機,在室溫下對直徑為10毫米的標準試樣進行測試。測試結果見表1。
(2)導熱性能:採用閃光導熱分析儀LFA447 Nano flash儀器測試熱擴散係數。遵照的標準為ASTME1461;採用功率補償型差示掃描量熱DSC8000測試比熱容。
導熱係數=熱擴散係數*比熱容*密度;測試結果見表1。
(3)平面度:採用三坐標測試儀測試平面上的14個點的Z向坐標,可得平面度數據。測試結果見表1。
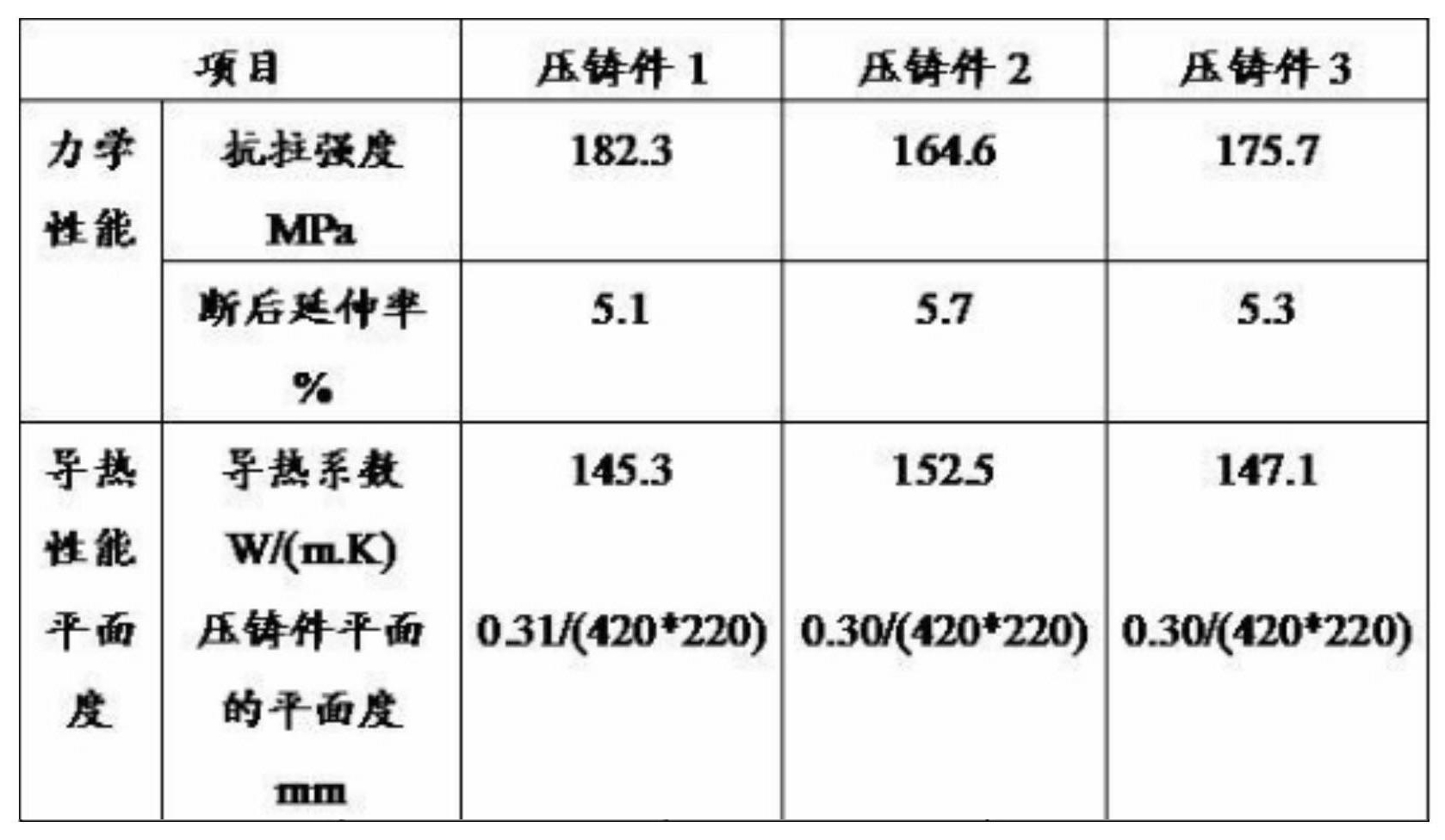
表1
由表1中的測試數據可以看出,《一種用於半固態金屬壓鑄成型的壓鑄方法》的實施例1所取得的產品,具有較佳的力學性能、導熱性能和平面度,產品的機械強度極佳,具有非常好的平面度,在同類的壓鑄產品中具有領先的產品性能。
榮譽表彰
2018年12月20日,《一種用於半固態金屬壓鑄成型的壓鑄方法》獲得第二十屆中國專利優秀獎。