專利背景
隨著原油日益變重及其加工深度的提高,作為重油加工的主要工藝之一,延遲焦化發揮了重要的作用。延遲焦化過程得到的焦化汽油由於不飽和烴及膠質含量高,且硫、氮等雜質含量也較高,因此具有腐蝕性且安定性差,使其套用受到限制。焦化汽油必須經過加氫精制,才能用作汽油調和組分、催化重整原料或裂解制乙烯的原料。
隨著煉油工業的發展,尤其是催化裂化技術的不斷提高,煉廠氣的深加工越來越受到人們的重視。煉廠氣的利用有多種路徑,其中液化石油氣加氫就是人們普遍關注的課題之一。液化石油氣加氫後會有許多用途,比如,用作乙烯原料、合成順酐的原料、車用液化石油氣,其中液化石油氣加氫用作乙烯原料因為其用量較大、經濟效益好,所以備受關注。
世界乙烯原料的構成基本穩定,並且一直以石腦油和輕烴為主,但是近幾年來,由於各國資源的不同,原料市場的變化,乙烯原料出現了向多樣化發展的趨勢。以丁烷作為乙烯原料的方法就是乙烯原料多樣化的發展趨勢之一。截至2010年7月,在
美國以丁烷作為乙烯原料已占到3%~5%,用此作為乙烯原料的調劑與補充。
截至2010年7月,中國國內石化企業新建、擴建了多套大型乙烯生裝置,造成了
乙烯原料的短缺,現實狀況迫使企業尋找新的乙烯原料來填補這個缺口,液化石油氣加氫作乙烯原料就是解決這一問題的有效方法之一。
中國煉化企業眾多,液化石油氣資源豐富,液化石油氣加氫作乙烯原料這一項研究工作既能使煉廠氣得以綜合利用,又能對乙烯原料的短缺做一補充和調劑,因此開展以C4餾份為原料加氫製備乙烯裂解料的研究工作具有現實意義。
工業C4餾份加氫製備乙烯裂解料的方法就是將工業C4餾份中的烯烴、二烯烴加氫,使之成為烷烴。
CN1160701A介紹了一種C3餾分的加氫的方法,但該方法目的在於使C3餾分中的炔烴選擇加氫,並非對整個餾分(包括單烯烴)的加氫。CN1145891A介紹了一種加氫方法,但此法只適用於C5餾分加氫制戊烷。使用非貴金屬加氫催化劑時,單烯烴的轉化率較低,加氫產物達不到用於乙烯原料的要求。USP4482767介紹了一種C3(來源於FCC)餾分水合聯產液化石油氣的方法,但該方法僅適合於C3餾分。CN01114163.8介紹了一種液化石油氣加氫製備車用液化石油氣的方法,但此法有兩個缺點,之一是該催化劑是貴金屬類型(Pd/α-AL2O3),不耐硫;之二是該方法不適合於生產乙烯裂解料,因為車用液化石油氣的指標為烯烴<5.0%,而乙烯裂解料要求加氫後液化石油氣中烯烴含量<1.0%。
一般情況下,催化裂化等工藝過程得到的工業C4餾分含烯烴在40v%左右,在進行加氫反應時有如下特點:(1)放熱量大。比如,含烯烴在43v%的C4餾分,在將其全部烯烴加氫時的反應熱為50.47千焦/摩爾,絕熱反應溫升可達170℃。(2)反應速度快,放熱量集中。由該項反應的動力學研究結果可知,在通過催化劑床層反應時,反應停留時間在整個停留時間的1/4~1/3時,反應的轉化率可達總轉化率的75%~80%,即反應物料在通過催化劑床層1/4~1/3過程,其放熱量就已達到整個反應熱的75%~80%。(3)受熱力學平衡影響。在工業C4餾分中反-2-丁烯的含量最高,以此為例,其反應溫度與平衡常數關係列於表1中。
由表1中數據可知,隨著反應溫度的升高,平衡常數隨之降低。當反應溫度在高分別於250℃、300℃、340℃之後,反應平衡常數出現了迅速減小的現象。
從理論上來說,烯烴加氫反應是一個強放熱反應,控制步驟為反應控制,如果反應溫度較低,儘管反應平衡常數較大,但是反應速度較慢;反之,如果反應溫度較高,儘管反應速度較大,但是反應平衡常數較小。對於該項而言,反應熱的擴散如果不能很好地控制(或者說反應溫升不能有效控制),就會將反應控制轉為熱力學控制,使反應的轉化率降低。
在實驗中發現,當反應溫度超過340℃之後,因受化學平衡的影響,其反應產物中烯烴含量下降較為緩慢。所以,對於工業C4餾分加氫製備乙烯裂解料項目來說,在工業生產中其反應熱的移出(有效擴散)是一個必須解決的關鍵問題。
此外,2010年7月前在工業C4餾分加氫生產中還存在如下問題:(1)反應溫度高,反應結果受熱力學平衡影響較大。比如撫順石油化工研究院研製生產的FH-40C加氫精制催化劑是一個加氫性能非常好的催化劑,但它對於該項反應而言,起始反應溫度是在210℃,活性較佳的發揮段是在240~300℃,這樣即使反應的入口溫度定在210℃,其出口溫度達到了380℃(出口溫度=入口溫度+絕熱溫升=210+170=380℃),超過了340℃。工業C4餾分加氫後作乙烯裂解料,其指標要求是烯烴含量<1.0v%;而對於該項反應而言,在反應溫度超過340℃後因受化學平衡的影響,其反應產物中烯烴含量很難達到指標。(2)反應床層入口處易結焦,反應床層阻力增加較快,造成生產裝置經常停工除焦,以此降低反應床層阻力維持正常生產。
發明內容
專利目的
《一種液化石油氣-焦化汽油加氫組合工藝方法》提供了一種將工業C4餾分和焦化汽油加氫處理的組合工藝,該發明方法一方面解決了C4餾分加氫過程的穩定性,同時解決了普通焦化汽油加氫裝置得到的加氫焦化汽油中稀烴含量高,不易達到催化重整和蒸汽裂解原料質量的要求。
技術方案
《一種液化石油氣-焦化汽油加氫組合工藝方法》液化石油氣一焦化汽油加氫組合工藝方法包括如下內容:
A、焦化汽油在焦化汽油加氫反應段進行加氫反應;
B、焦化汽油加氫反應段流出物與液化石油氣原料混合進入液化石油氣加氫反應段;
C、液化石油氣加氫反應段的反應流出物經過分離,得到加氫液化石油氣和加氫焦化汽油。
《一種液化石油氣-焦化汽油加氫組合工藝方法》方法中,焦化汽油加氫反應段採用加氫精制催化劑,操作條件一般為:反應壓力2.0兆帕~15.0兆帕,最好為4.0兆帕~8.0兆帕;反應溫度為220℃~390℃,最好為300℃~360℃;液時體積空速為0.5小時~3.0小時,最好為1.0小時~2.0小時;氫油體積比為300~1500,最好為300~800。經過上述條件加氫反應後的焦化汽油中的烯烴含量一般為5%(體積)左右,如果作為催化重整原料或蒸汽裂解制乙稀的原料,則需要進一步加氫精制。
《一種液化石油氣-焦化汽油加氫組合工藝方法》方法中,液化石油氣加氫反應段採用普通加氫精制催化劑,操作條件為:焦化汽油/液化石油氣體積比為0.5:1~10:1(均為液態時的體積比),反應溫度為220~380℃,反應壓力2.0兆帕~15.0兆帕,最好為4.0兆帕~8.0兆帕,反應壓力最好與焦化汽油加氫反應段相同(不考慮反應過程的壓力損失),液化石油氣進料體積空速為0.5~4.0小時,氫油體積比為100~1500(標準狀態下體積比,氫為氫氣,油為液態液化石油氣體積);優選的反應條件是:焦化汽油/液化石油氣為2:1~4:1;反應溫度為270~340℃;液化石油氣進料體積空速為0.5~2.0小時,氫油體積比為300~500(v)。經過上述加氫精制過程,得到的加氫液化石油氣和加氫焦化汽油中的稀烴含量均可以低於1.0%。
《一種液化石油氣-焦化汽油加氫組合工藝方法》方法中,使用的加氫精制催化劑可以是該領域常規的加氫精制催化劑,一般以氧化鋁為載體,以鎢、
鉬、鎳、
鈷中的一種或幾種為活性組分,以氧化物計的活性組分重量含量為15%~60%,催化劑中可以含有適宜的助劑,可以採用商品加氫精制催化劑,也可以按該領域2010年7月前方法製備。
改善效果
《一種液化石油氣-焦化汽油加氫組合工藝方法》的特點是提供了液化石油氣-焦化汽油加氫組合工藝,採用該發明提供的工藝方法,利於反應熱的擴散,利於取出反應熱;降低了反應溫度,減小了溫度對反應平衡的影響,提高了轉化率;減少了催化劑積炭,延長了催化劑單程使用壽命。採用該發明方法可以同時獲得高質量的加氫焦化汽油和加氫液化石油氣。
附圖說明
圖1為《一種液化石油氣-焦化汽油加氫組合工藝方法》所提供的液化石油氣-焦化汽油加氫組合工藝流程示意圖。
1-焦化汽油原料管線,2-氫氣管線,3-焦化汽油加氫反應器,4-液化石油氣原料管線,5-焦化汽油加氫反應器流出物管線,6-液化石油氣加氫反應器,7-液化石油氣加氫反應器流出物管線。
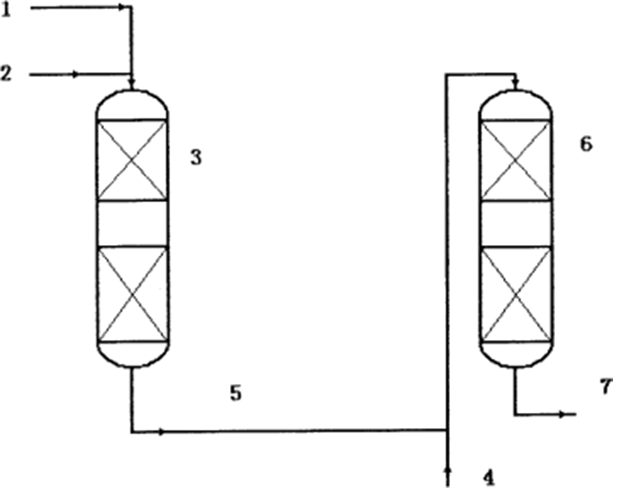
圖1
技術領域
《一種液化石油氣-焦化汽油加氫組合工藝方法》涉及一種加氫處理工藝,更具體地說,是一種將液化石油氣加氫處理和焦化汽油加氫處理兩種工藝方法有機結合的組合工藝方法。
權利要求
1.《一種液化石油氣-焦化汽油加氫組合工藝方法》包括如下內容:
A、焦化汽油在焦化汽油加氫反應段進行加氫反應;
B、焦化汽油加氫反應段流出物與液化石油氣原料混合進入液化石油氣加氫反應段;
C、液化石油氣加氫反應段的反應流出物經過分離,得到加氫液化石油氣和加氫焦化汽油。
2.按照權利要求1所述的方法,其特徵在於:焦化汽油加氫反應段採用加氫精制催化劑,操作條件為:反應壓力2.0兆帕~15.0兆帕,反應溫度為220℃~390℃,液時體積空速為0.5小時~3.0小時,氫油體積比為300~1500。
3.按照權利要求1所述的方法,其特徵在於:液化石油氣加氫反應段採用加氫精制催化劑,操作條件為:焦化汽油/液化石油氣體積比為0.5:1~10:1,反應溫度為220~380℃,反應壓力2.0兆帕~15.0兆帕,液化石油氣進料體積空速為0.5~4.0小時,氫油體積比為100~1500。
4.按照權利要求1所述的方法,其特徵在於:液化石油氣加氫反應段操作條件為:焦化汽油/液化石油氣為2:1~4:1,反應溫度為270~340℃,反應壓力4.0兆帕~8.0兆帕,液化石油氣進料體積空速為0.5~2.0小時,氫油體積比為300~500。
5.按照權利要求2或3所述的方法,其特徵在於:加氫精制催化劑以氧化鋁為載體,以鎢、鉬、鎳、鈷中的一種或幾種為活性組分,以氧化物計的活性組分重量含量為15%~60%。
實施方式
《一種液化石油氣-焦化汽油加氫組合工藝方法》中焦化汽油加氫反應段出來的焦化汽油(一般有5%以上的烯烴未被加氫)再與液化石油氣混合後一同進入到液化石油氣加氫反應段,在氫氣和催化劑存在下進行加氫反應,在此反應步驟中,焦化汽油有兩個作用,其一,自身的部分烯烴完成加氫;其二,兼顧取出液化石油氣加氫的反應熱,焦化汽油加氫反應段流出物為氣相,與液化石油氣原料混合後部分焦化汽油液化,在後續的液化石油氣加氫段中,隨著反應放熱,液化的焦化汽油再次氣化,同時吸收了反應放熱,有效控制了反應溫升,有利於烯烴的加氫飽和反應。
下面通過實施例進一步說明《一種液化石油氣-焦化汽油加氫組合工藝方法》的方案和效果。實施例中,兩個反應段使用的催化劑均為撫順石油化工研究院研製生產的FH-40C加氫精制催化劑,主要理化性質如表2。
焦化汽油原料和氫氣先進入到焦化汽油加氫反應器中,從此出來的焦化汽油及其反應過量的氫氣與液化石油氣原料混合後進入到液化石油氣加氫反應器中,反應流出物進入分離系統得到加氫後的焦化汽油和液化石油氣。
加氫後的焦化汽油,可以用作汽油調和組份、催化重整原料或裂解制乙烯的原料。加氫後的液化石油氣可以用作乙烯原料、合成順酐的原料、車用液化石油氣等。
比較例
取100毫升的FH-40C催化劑,裝入內徑25毫米,長1200毫米的不鏽鋼反應器中。反應原料:氫氣為電解淨化氫,純度>99%;碳四餾份取自撫順石油二廠,組成見表3;此次實驗為單一液化石油氣進料,反應為上進料,反應物料從反應器底部流出,經冷卻後進入分離器中,尾氣從分離器頂部排出,底部液相定時取樣,用氣相色譜分析組成。
在反應壓力11.5兆帕,液化石油氣進料體積空速2.0小時(液體的液化石油氣進料量:200毫升/小時),氫與液化石油氣(液體)體積比300條件下進行了反應溫度影響的考察實驗,實驗結果見表4,運轉後卸下的催化劑積炭分析數據列於表5。
註:液化石油氣進料體積空速=液化石油氣進料的液體體積/催化劑體積=2.0小時
由表4中數據可知,反應溫度在310℃~334℃區間,隨著反應溫度的提高,反應產物中的烯烴含量隨之降低。當反應溫度達到348℃後,反應產物中的烯烴含量隨之升高,反應溫度再降回333℃之後,反應產物中的烯烴含量又降低了。
在實驗中出現了上述現象,其原因是化學反應平衡所致。根據所計算出來的反-丁烯的平衡常數值(見表1)及表4中的實驗數據可以做如下解釋:(1)反應溫度在310℃~334℃區間,隨著反應溫度的提高,反應產物中的烯烴含量隨之降低。原因是在此溫度範圍內,隨著反應溫度的提高,對於該項反應而言會有兩種影響:其一是反應速度隨之加快,其二是反應平衡常數隨之降低,但在此時的反應條件下,反應溫度對該項反應的影響是處在主導地位,而化學平衡的影響是處在次要的地位。(2)當反應溫度達到348℃後,反應產物中的烯烴含量隨之升高。原因是在此時的反應條件下,反應溫度的影響已變為次要地位,而此時的化學平衡的影響已變為主導的地位。即反應溫度升高,反應平衡常數變小,反應產物中烯烴含量升高。
另外,由表5中數據還可知,在2010年前的反應條件下運轉,催化劑積炭速度較快。這是因為此次運轉反應溫度較高所致。此次運轉總計運轉時間為550小時,且多數時間反應床層的熱點溫度在340~365℃。由催化劑的積炭數據也可以推知,正常情況下,該項反應溫度的熱點不應超過340℃。
由表4可知,當入口溫度提到266℃時,反應結果達到了所預期的指標(產物中烯烴含量<1.0%。但是該項技術在實際工業套用會有如下情況:隨著運轉時間的增加會導致催化劑活性逐步降低,這樣就需要不斷提高反應器入口溫度用以補償。而在2010年前的反應條件下,在反應初期入口溫度266℃時,反應床層熱點溫度就已達到344℃,顯然採用2010年前的反應條件,反應入口溫度已不具有提溫的空間,即2010年前的反應條件在工業生產中不具有可行性。
實施例1~8
取100毫升的FH-40C催化劑,裝入內徑25毫米,長1200毫米的不鏽鋼反應器中。反應原料:氫氣為電解淨化氫,純度>99%;碳四餾份取自撫順石油二廠,組成見表3;加氫焦化汽油取自中國石化鎮海煉化分公司,組成見表6。反應為上進料,反應物料從反應器底部流出,經冷卻後進入分離器中,尾氣從分離器頂部排出,底部液相定時取樣,用氣相色譜分析組成,具體反應條件及結果列於表7。
由表7中的數據可知,採用液化石油氣與焦化汽油混合進料的方法,不但可以使兩種物料同時得到加氫,還可以大幅度地降低液化石油氣加氫反應的反應溫升,並且反應結果也能達到所要求的產品指標,說明採用混合進料的方法是解決液化石油氣加氫的反應熱的取出和控制溫升的有效手段。
實施例9
《一種液化石油氣-焦化汽油加氫組合工藝方法》方案的穩定性實驗,具體反應條件及結果列於表8。
由表8中數據可知,在催化劑活性穩定性實驗結束時,已運轉達800小時,催化劑仍具有很好的活性,說明《一種液化石油氣-焦化汽油加氫組合工藝方法》工藝具有較好的活性和穩定性。
榮譽表彰
2016年12月7日,《一種液化石油氣-焦化汽油加氫組合工藝方法》獲得第十八屆中國專利優秀獎。