專利背景
導輥是軋鋼用滾動導衛裝置的重要部件,用來輸送型材和線材使其順利的進入軋機。工作環境十分惡劣。900℃以上紅熱鋼材連續從導衛上通過,同時又要噴水冷卻,溫差變化大而急劇,所以導輥磨損快,壽命低,需頻繁更換,消耗量大,產生
龜裂和斷裂,影響軋鋼生產效率。另外,導輥使用中,易產生粘鋼現象,影響軋制鋼材的質量。而粘鋼的根本原因是導衛的高溫、急冷、急熱的工作條件下,與快速穿過的紅鋼發生焊合作用,這就要求導輥材料必須具備高的熱強性和抗氧化性,良好的耐磨性,熱穩定性及導熱性,較小熱膨脹係數,低摩擦係數。因此,解決導輥的材質問題是提高軋鋼作業效率和鋼材質量,降低消耗,減輕工人勞動強度,減少事故的有效措施。
發明內容
專利目的
《一種導輥及其製備工藝》目的就是為了彌補已有技術的缺陷,提供一種導輥及其製備工藝。採用該發明技術製備導輥成本低,使用壽命長,具有良好的抗高溫氧化性能,高溫強度,抗衝擊高溫韌性和抗高溫摩擦磨損。
技術方案
一種導輥,其特徵在於:其各原料組分的重量百分比為:C 3.1-3.45%;Si 0.1-0.9%;Mn 0.1-0.4%;P 0.01-0.03%;S 0.01-0.03%;Cr 24-25%;Mo 0.4-0.6%;V 0.9-1%;W 2-3%;稀土0.05-0.1%;餘量為Fe。
所述的一種導輥的製備工藝,其特徵在於:依次按以下步驟進行:
a.精密鑄造:取各原料並按照規定配比配得混合料,待用;再製備導輥:
首先,用低溫蠟基模料做出導輥模型,用矽溶膠-水玻璃複合型殼制殼工藝製得導輥模型型殼,在矽溶膠-水玻璃複合模型型殼過程中,在導輥模型上先塗抹2-5層矽溶膠,3-4層水玻璃蒸汽脫蠟後,得到導輥模型型殼;
其次,焙燒導輥模型型殼,焙燒溫度為950-1020℃,保溫時間為40分鐘,焙燒結束後,將配製的混合料倒入導輥模型型殼內進行澆注,此時,混合料呈鋼水,鋼水出爐溫度為1600-1620℃,澆注溫度為1520-1540℃,導輥模型型殼溫度為450-600℃,澆注後,將製成的導輥自然冷卻至室溫,去除澆注系統後得到導輥;
b.
退火:將步驟a加工成的導輥由室溫升至1000℃,保溫7小時,再冷卻至室溫;
c.粗加工:採用常規刀具對步驟c得到的導輥進行車削加工;
d.
淬火:將車削加工後的導輥由室溫呈階梯式上升至1030℃,並分別在220℃、420℃以及600℃,各保溫2小時,在1030℃保溫3小時,出爐後,風冷至室溫;
e.回火:將經過淬火處理的導輥由室溫升至270℃-290℃,保溫5小時,然後隨爐冷卻至室溫;
f.精加工:將經回火處理後的導輥用硬質合金刀具精加工成成品導輥。
所述的一種導輥的製備工藝,其特徵在於:步驟b中,退火過程中由室溫升至1000℃是按每小時100-120℃的速度進行升溫。
所述的一種導輥的製備工藝,其特徵在於:步驟d中,淬火過程中由室溫升至1030℃是按每小時升溫100-120℃速度進行升溫。
所述的一種導輥的製備工藝,其特徵在於:步驟e中,回火過程中由室溫升至270℃-290℃是按每小時80-100℃速度進行升溫。
所述的一種導輥的製備工藝,其特徵在於:步驟e處理後的導輥硬度HRC為62-65。
所述導輥採用了DF-2材質。DF-2材質由碳化物和金屬基體組成,碳化物主要是(Cr,Fe)7C3,。它在抗磨損中起到“牙齒”作用,由於它的硬度高達HV1300-1800,所以能抗磨損。但是“牙齒”要發揮作用,還要有賴於“牙床”強有力的支撐,在金屬基體中以馬氏體為最強、最硬。通過合金化和熱處理,使得到金屬基體基本是馬氏體組成。
在DF-2材質中,含碳量和含鉻量已達到共晶平衡,在共晶體中,碳化物M7C3是從一個結構中心增長,在橫截面上顯示出不連續地分布在奧氏體基體上。DF-2材質不僅有棒狀或桿狀的M7C3型碳化物(而不是板狀)故,DF-2材質的導輥具有高的強度、韌性及硬度耐蝕性好的特點。
導輥的基體由化學成分和冷卻速度、壁厚三個因素決定的。《一種導輥及其製備工藝》的化學成分是這樣確定的。
提高碳含量,可以增加顯微組織碳化物的數量從而提高DF-2材質的耐磨性,但超過共晶碳含量時,會形成粗大的過共晶碳化物,導致韌性顯著降低,含碳量達到3%耐磨性最好。
2.鉻
鉻是強烈形成碳化物的元素,部分與碳結合形成高硬度碳化物,尚有部分溶入奧氏體中。在相等的含碳量,含鉻量低時,形成連續網狀分布Cr3C型碳化物。只有鉻含量同碳含量比例大於6∶1才能完全生成Cr7C3碳化物,起到沉澱強化作用。
3.矽
矽在鋼中只能形成固體溶體,只有少量矽存在,才能起固溶強化作用,過量矽會降低金屬基體的塑性,使導輥在激冷,激熱條件下易產生裂紋,故矽含量控制1.0%以下。
4.錳
錳是穩定奧氏體,可提高基體淬透性,可增加板條殘餘奧氏體的數量,增加鋼的韌性,減少淬火應力,但含量過多,會大大增大導輥熱敏感性,增加回火脆性,從而導致導輥耐磨性降低,因此,錳含量應控制0.6%以下。
5.鉬、釩、鎢
鉬既可溶於
奧氏體,又可形成碳化物,溶於固溶體,能顯著提高鋼的高溫強度。當含量大於1%時,形成的碳化物會彌散析出,而產生沉澱強化。Mo
2C硬度HV為1500,所以提高導輥硬度,單一鉬元素應控制在1.59%以下。
釩能顯著提高導輥的紅硬性,硬度及耐磨性,釩形成碳化物V4C3在加熱時部分溶於奧氏體中,回火時以V4C3 的細小晶粒彌散析出造成二次硬化性。
鎢是提高導輥紅硬性主要元素,在鋼中形成碳化物,在回火時,一部分鎢以碳化物的形式彌散析出,造成二次硬化,加熱時,未溶碳化物則起阻止奧氏體晶粒長大的作用。
釩的彌散硬化作用比鎢強烈,而鎢提高馬氏本的回火穩定性比釩強烈,兩者不能互相代替,釩含量增加,耐磨性,紅硬性提高,但被磨削性降低,故鉬、釩、鎢複合加入效果明顯,因此,Mo含量控制在1%以下,V含量控制0.7-1.0%之間,W含量控制在2.0-3.0%之間。
6.S、P
磷、硫都是對導輥有害雜質,應嚴格控制共含量。
7. 稀土
稀土能淨化鋼液,改善鋼中夾雜物形態分布,從而改善鑄態組織及改善鋼的性能。
稀土元素能與鋼中低熔點雜質元素如鉛、銻、砷、形成高熔點物質,以消除這些元素沿晶界所造成脆性。稀土元素進一步脫硫、固氫、固氮。稀土元素將鋼中夾雜改變為稀土硫化物,稀土氧化物及稀土硫氧化物,它們的熔點比原來夾雜高,在鋼液中易聚集成球狀而浮出。( 用鋁脫氧,形成細小針狀A12O3,不能有效浮出。)稀土元素在鋼中還能起到細化晶粒作用。
導輥的耐磨性與冶金的質量也有很大關係。
鑄件中的偏析、縮孔、縮松、氣孔、夾渣、夾雜,都能加速導輥磨損進程,導輥中夾雜物嚴重影響導輥的疲勞強度而鑄造不能完全改變這些存在的缺陷,只能改善。
導輥的冶煉依據是這樣確定的:
<一> 用鹼性爐襯熔煉
因為DF-2材質含鉻、釩高,用鹼性爐襯熔煉,可大大減少鋼水夾雜。
<二> 去氣、變質、淨化
將稀土矽鈣破碎至粒度3-S毫米小塊,預先放置鹼性鋼包中,用包內沖水法對鋼水進行複合變質,鎮定3-5分鐘,使鋼水充分靜置,當溫度降到1490-1510℃左右時,用耐火石棉擋渣,用茶壺嘴包進行澆注。這樣大大減少了鋼水夾雜,降低偏析,細化晶粒。導輥耐磨性在很大程度上由金屬基體決定的。
導輥的熱處理依據是這樣確定的:
發揮DF-2材質導輥耐磨性,應使機體為馬氏體。取決於淬火溫度和冷卻速度。淬火溫度對相變後的顯微組織和硬度都有明顯影響。隨著淬火溫度的提高,奧氏體固溶的碳含量增加,
淬火轉變來的馬氏體硬度有所提高。如果奧氏體化溫度過高,在淬火後,可能有大量殘餘奧氏體產生而形成
馬氏體和
奧氏體的混合組織,硬度有所下降,殘餘奧氏體越多。殘餘奧氏體在隨後回火過程中有去穩定化作用,並產生馬氏體相變,產生二次硬化,析出二次碳化物量最合適的就是最佳淬火溫度,故DF-2材質的最佳淬火溫度為960-1050℃。在回火冷卻過程中相變為馬氏體,出現二次硬化,二次硬化後硬度高於淬火的硬度。出現二次硬化的回火溫度取決於殘餘奧氏體的穩定性,即取決於淬火溫度,回火溫度為270℃-290℃。加熱速度。鑄件在鑄造過程中已有很大應力,加熱不恰當時,形成很大的溫差應力,兩個應力疊加,容易造成開裂,DF-2材質的升溫速度可達110℃/小時。
冷卻速度。奧氏體化以後冷卻往往是產生開裂的主要原因,因此,淬透性一定要調節到能在空氣中淬出馬氏體組織來。
改善效果
1.《一種導輥及其製備工藝》材料設計以主導合金元素與輔助元素相結合的原則,立足於國內政策,成功研製了一種鉻基馬氏體耐熱耐磨鋼,即研製出《一種導輥及其製備工藝》導輥。《一種導輥及其製備工藝》以較低的成本,獲得具有優良性能導輥材料,可以代替進口導輥,具有較好的社會效益。
2.《一種導輥及其製備工藝》製備的導輥的各項指標完全能滿足導輥耐高溫,耐磨,抗熱衝擊,熱疲勞等各項性能要求(見附表一)其使用壽命比原來導輥使用壽命提高4倍以上,具有較大經濟效益。
3.《一種導輥及其製備工藝》產品導輥在高溫下具有良好的抗氧化性能,即在900-950℃下抗氧化,輥面不脫皮,具有足夠的高溫強度,有較高的抗蠕變強度和持久疲勞強度,950-200℃溫度循環下,不產生熱疲勞裂紋,在高溫狀態下,有足夠的硬度,從而具有良好的抗高溫摩擦磨損(見附表二、三),具有良好的抗衝擊高溫韌性(詳見表一)
試樣編號 | 衝擊值(Akn)焦 | 衝擊韌性(akn)焦/平方米 |
---|
1 | | |
---|
2 | | |
---|
3 | | |
---|
表二《一種導輥及其製備工藝》產品導輥抗氧化性能試驗報告
(試驗溫度為950℃,試驗時間為150小時)
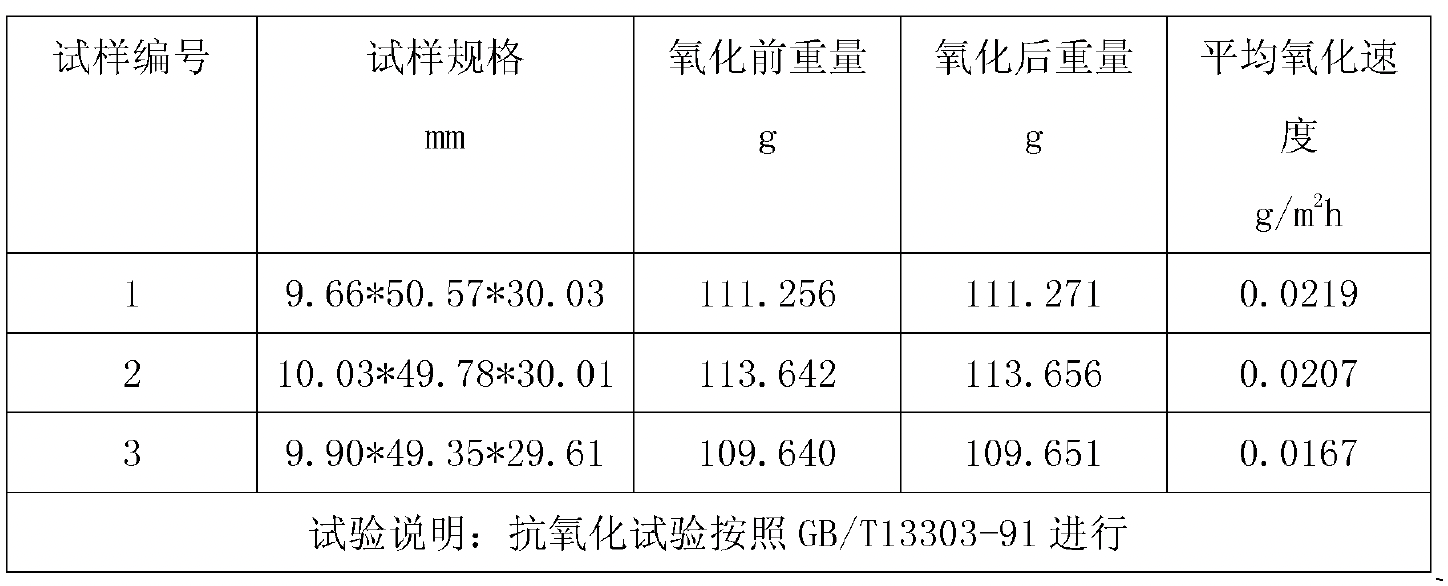
本發明產品導輥抗氧化性能試驗報告
表三《一種導輥及其製備工藝》導輥的機械性能試驗報告

本發明導輥的機械性能試驗報告
表一,表三中的檢測數據是由中科院固體研究所作出機械性能試驗報告。
技術領域
《一種導輥及其製備工藝》主要涉及一種合金材料及其處理方法,尤其涉及一種導輥及其製備工藝。
權利要求
1.一種導輥的製備工藝,其特徵在於:其各原料組分的重量百分比為:C 3.1-3.45%;Si 0.1-0.9%;Mn 0.1-0.4%;P 0.01-0.03%;S 0.01-0.03%;Cr 24-25%;Mo 0.4-0.6%;V 0.9-1%;W 2-3%;稀土0.05-0.1%;餘量為Fe;依次按以下步驟進行:
a.精密鑄造:取各原料並按照規定配比配得混合料,待用;再製備導輥:首先,用低溫蠟基模料做出導輥模型,用矽溶膠-水玻璃複合型殼制殼工藝製得導輥模型型殼,在矽溶膠-水玻璃複合模型型殼過程中,在導輥模型上先塗抹2-5層
矽溶膠,3-4層水玻璃蒸汽脫蠟後,得到導輥模型型殼;其次,焙燒導輥模型型殼,焙燒溫度為950-1020℃,保溫時間為40分鐘,焙燒結束後,將配製的混合料倒入導輥模型型殼內進行澆注,此時,混合料呈鋼水,鋼水出爐溫度為1600-1620℃,澆注溫度為1520-1540℃,導輥模型型殼溫度為450-600℃,澆注後,將製成的導輥自然冷卻至室溫,去除澆注系統後得到導輥;
b.退火:將步驟a加工成的導輥由室溫升至1000℃,保溫7小時,再冷卻至室溫;
c.粗加工:採用常規刀具對步驟b得到的導輥進行車削加工;
d.淬火:將車削加工後的導輥由室溫呈階梯式上升至1030℃,並分別在220℃、420℃以及600℃,各保溫2小時,在1030℃保溫3小時,出爐後,風冷至室溫;
e.回火:將經過淬火處理的導輥由室溫升至270℃-290℃,保溫5小時,然後隨爐冷卻至室溫;
f.精加工:將經回火處理後的導輥用硬質合金刀具精加工成成品導輥。
2.根據權利要求1所述的一種導輥的製備工藝,其特徵在於:步驟b中,退火過程中由室溫升至1000℃是按每小時100-120℃的速度進行升溫。
3.根據權利要求1所述的一種導輥的製備工藝,其特徵在於:步驟d中,淬火過程中由室溫升至1030℃是按每小時升溫100-120℃速度進行升溫。
4.根據權利要求1所述的一種導輥的製備工藝,其特徵在於:步驟e中,回火過程中由室溫升至270℃-290℃是按每小時80-100℃速度進行升溫。
5.根據權利要求1所述的一種導輥的製備工藝,其特徵在於:步驟e處理後的導輥硬度HRC為62-65。
實施方式
一種導輥,其各原料組分的重量配比為:C 3.14 ;Si 0.81 ;Mn 0.45 ;Cr 24.27 ;V 0.85 ;Mo 0.56 ;W 2.03 ;S 0.04 ;P 0.03 ;稀土 0.01 ;餘量為 Fe。
這種導輥的製備工藝,依次包括有以下步驟:
a. 精密鑄造:取各原料並按照規定配比配得混合料,待用;再製備導輥:
首先,用低溫蠟基模料做出導輥模型,用矽溶膠- 水玻璃複合型殼制殼工藝製得導輥模型型殼,在矽溶膠- 水玻璃複合模型型殼過程中,在導輥模型上先塗抹2-5層矽溶膠,3-4層水玻璃蒸汽脫蠟後,得到導輥模型型殼;其次,焙燒導輥模型型殼,焙燒溫度為950-1020℃,保溫時間為40分鐘,焙燒結束後,將配製的混合料倒入導輥模型型殼內進行澆注,此時,混合料呈鋼水,鋼水出爐溫度為1600-1620℃,澆注溫度為1520-1540℃,導輥模型型殼溫度為400-600℃,澆注後,將製成的導輥自然冷卻至室溫,去除澆注系統後得到導輥;
b. 退火:將步驟a 加工成的導輥由室溫升至1000℃保溫7小時,然後隨爐冷卻至室溫;
c. 粗加工:採用常規刀具對退火處理後的導輥進行車削加工;
d. 淬火:將車削加工後的導輥由室溫升至( 階梯式)1030℃,分別在250℃,450℃,650℃,各保溫2小時,在1030℃保溫小時,然後出爐風冷至室溫;
e. 回火:將經過淬火處理的導輥由室溫升至270℃ -290℃保溫5小時,然後隨爐冷卻至室溫;
f. 精加工:將經回火處理後的導輥用硬質合金刀具精加工成成品導輥。
一種導輥,其各原料組分的重量配比為:C 3.17 ;Si 0.75 ;Mn 0.42 ;Cr 24.54 ;V 0.89 ;Mo 0.93 ;W 2.46 ;S 0.04 ;P 0.04 ;稀土 0.01 ;餘量為Fe。
這種導輥的製備工藝,依次包括有以下步驟:
a. 精密鑄造:取各原料並按照規定配比配得混合料,待用;再製備導輥:
首先,用低溫蠟基模料做出導輥模型,用矽溶膠- 水玻璃複合型殼制殼工藝製得導輥模型型殼,在矽溶膠- 水玻璃複合模型型殼過程中,在導輥模型上先塗抹3 層矽溶膠,3-4層水玻璃,蒸汽脫蠟後,得到導輥模型型殼;
其次,焙燒導輥模型型殼,焙燒溫度為950-1020℃,保溫時間為40分鐘,焙燒結束後,將配製的混合料倒入導輥模型型殼內進行澆注,此時,混合料呈鋼水,鋼水出爐溫度為1600-1620℃,澆注溫度為1480-1500℃,導輥模型型殼溫度為400-600℃,澆注後,將製成的導輥自然冷卻至室溫,去除澆注系統後得到導輥;
b. 退火:將步驟a 加工成的導輥由室溫升至1000℃保溫7 小時,然後隨爐冷卻至室溫;
c. 粗加工:採用常規刀具對退火處理後的導輥進行車削加工;
d. 淬火:將車削加工後的導輥由室溫升至( 階梯式)1030℃,分別在250℃,450℃,650℃,各保溫2小時,在1030℃保溫2小時,然後出爐風冷至室溫;
e. 回火:將經過淬火處理的導輥由室溫升至270℃-290℃保溫5小時,然後隨爐冷卻至室溫;
f. 精加工:將經回火處理後的導輥用硬質合金刀具精加工成成品導輥。
一種導輥,其各原料組分的重量配比為:C 3.19 ;Si 0.50 ;Mn 0.40 ;Cr 24.17 ;V 0.95 ;Mo 0.80 ;W 2.40 ;S 0.04 ;P 0.03 ;稀土0.01 ;餘量為Fe。
這種導輥的製備工藝,依次包括有以下步驟:
a. 精密鑄造:取各原料並按照規定配比配得混合料,待用;再製備導輥:
首先,用低溫蠟基模料做出導輥模型,用矽溶膠- 水玻璃複合型殼制殼工藝製得導輥模型型殼,在矽溶膠水玻璃複合模型型殼過程中,在導輥模型上先塗抹2-5 層矽溶膠,3-4 層水玻璃蒸汽脫蠟後,得到導輥模型型殼;
其次,焙燒導輥模型型殼,焙燒溫度為950-1020℃,保溫時間為40分鐘,焙燒結束後,將配製的混合料倒入導輥模型型殼內進行澆注,此時,混合料呈鋼水,鋼水出爐溫度為1600-1620℃,澆注溫度為1480-1500℃,導輥模型型殼溫度為400-600℃,澆注後,將製成的導輥自然冷卻至室溫,去除澆注系統後得到導輥;
b. 退火:將步驟a 加工成的導輥由室溫升至1000℃保溫7小時,然後隨爐冷卻至室溫;
c. 粗加工:採用常規刀具對退火處理後的導輥進行車削加工;
d. 淬火:將車削加工後的導輥由室溫升至( 階梯式)1030℃,分別在250℃,450℃,650℃,各保溫2小時,在1030℃保溫2 小時,然後出爐風冷至室溫;
e. 回火:將經過淬火處理的導輥由室溫升至270℃-290℃保溫5小時,然後隨爐冷卻至室溫;
f. 精加工:將經回火處理後的導輥用硬質合金刀具精加工成成品導輥。
榮譽表彰
2021年8月16日,《一種導輥及其製備工藝》獲得安徽省第八屆專利獎銀獎。