專利背景
2-萘酚是一種精細化學品中間體,傳統生產方法是以精萘為原料經
磺化、水解、中和、
鹼熔、
酸化、精製等工序製得,生產每噸2-萘酚約產生10噸廢水。該廢水含鹽量高、毒性大、色澤深,主要含有萘磺酸鈉、甲基萘磺酸鈉及雜茚類的磺酸鈉、亞硫酸鈉、硫酸鈉等物質,其中含萘磺酸鈉16000~25000毫克/升,亞硫酸鈉34~38克/升,硫酸鈉55~60克/升,COD濃度達25000~40000毫克/升。不加治理會造成嚴重的環境污染,而且浪費大量資源。
2012年4月前2-萘酚廢水處理工藝主要有樹脂吸附法、萃取法、碳化和焚燒法、膜分離法、化學氧化法、生化法等。“樹脂吸附法”工藝操作條件及要求高,樹脂飽和時間短,反洗頻繁,且樹脂價格高,裝置投資大;膜分離法主要缺點是各種膜的性能不穩定,膜孔易堵塞;直接化學氧化法成本較高;生化法處理COD較高的廢水有一定的難度,且萘系染料中間體廢水極難降解,所需微生物須經特殊馴化培養。萃取法、樹脂吸附法或蒸發濃縮等方法,可以把2-萘酚廢水中的化學物質濃縮,這些物質主要是2-萘磺酸鈉、1-萘磺酸鈉、甲基萘磺酸鈉、氧雜茹萘磺酸鈉、氮雜茚萘磺酸鈉、硫雜茚磺酸鈉、萘二磺酸鈉等,組分複雜,不能被簡單地直接利用,採取集中焚燒的辦法處理,缺點是投資、能耗費用高,對資源沒有回收利用。
發明內容
專利目的
《2-萘酚生產廢水綜合治理與資源化利用工藝》所要解決的技術問題是針對2012年4月前已有技術的不足,提供一種工藝更為合理、2-萘酚生產廢水綜合治理與資源化利用工藝。
《2-萘酚生產廢水綜合治理與資源化利用工藝》中所述的2-萘酚生產廢水,主要是2-萘酚生產過程“中和工序”排放的過濾母液和洗滌廢水。
技術方案
《2-萘酚生產廢水綜合治理與資源化利用工藝》是一種2-萘酚生產廢水綜合治理與資源化利用工藝,其特點是,其步驟如下:
(1)酸化脫硫:2-萘酚生產廢水用無機酸直接酸化至pH值2~3,放出的SO2氣體用無機鹼液噴淋吸收,生成的亞硫酸鹽溶液回用於2-萘酚生產系統;
(2)一級萃取、反萃取:脫硫後的廢水過濾除去不溶物後,常溫常壓下與萃取劑按油水相比1~5:1充分混合,分層後的萃余相即萃後水送二級萃取;萃取相即負載萃取劑常壓下與無機鹼液加熱至60℃~90℃後充分混合,反萃取加鹼量以將pH終點值控制在8.5~9.5為準,分層後的反萃液冷卻後過濾,得到的萘磺酸鹽固體回用於2-萘酚水解吹萘工序;濾液轉入蒸發系統,再生後的萃取劑循環使用於一級萃取;
(3)二級萃取、反萃取:一級萃取的萃後水用無機酸調節pH值至2~3,常溫常壓下再與萃取劑按油水相比1~5:1充分混合進行二級萃取,分層後的萃後水送氧化絮凝處理;負載萃取劑常壓下與無機鹼液加熱至60℃~90℃後充分混合,反萃取加鹼量以將pH終點值控制在8.5~9.5為準,分層後反萃液轉入蒸發系統,再生後的萃取劑循環使用於二級萃取;
(4)蒸發濃縮:將一級反萃取的過濾液和二級萃取的反萃液進入蒸發系統,濃縮至總含固量40%~70%質量濃度的廢水濃縮液,蒸發冷凝水送氧化絮凝達標排放;
(5)減水劑合成:將廢水濃縮液和甲醛在硫酸催化下進行縮合反應,加鹼中和並冷卻,過濾出固體結晶,即得液體減水劑;
(6)水解吹萘:將步驟(2)得到的萘磺酸鹽固體加入水解吹萘釜,加水後,在140℃~150℃下通水蒸汽40~60分鐘,吹出的萘用冷水回收;加入亞硫酸鈉,使部分2-萘磺酸轉變為鈉鹽利用;
(7)氧化絮凝:將上述二級萃後水和蒸發冷凝水加入次氯酸鈉氧化,再加入聚合氯化鋁和聚丙烯醯胺絮凝反應沉澱處理後,出水達標排放。
以上所述的《2-萘酚生產廢水綜合治理與資源化利用工藝》2-萘酚生產廢水綜合治理與資源化利用工藝技術方案中,進一步優選的技術方案或技術特徵如下:
1、在步驟(1)和(3)中,所述的無機酸可以使用2012年4月前已有技術中常用的無機酸,優選硫酸、鹽酸、硝酸或者磷酸,進一步優選硫酸或鹽酸,最優選質量濃度為10%~98%的硫酸或10%~31%的鹽酸。
2、在步驟(1)中,所述的無機鹼液可以使用2012年4月前已有技術中常用的無機鹼液,優選燒鹼、氨水、純鹼、氧氧化鉀或者碳酸氫鈉溶液,進一步優選燒鹼或純鹼,其質量濃度按需要選定,沒有特別要求。
3、在步驟(2)和(3)中,所述的無機鹼液可以使用2012年4月前已有技術中常用的無機鹼液,優選燒鹼、氨水、純鹼、氧氧化鉀或者碳酸氫鈉溶液,且其質量濃度為10%-50%,最優選質量濃度為5%~30%的燒鹼溶液。
4、在步驟(2)和步驟(3)中,所述的萃取劑可以使用2012年4月前已有技術中常用的絡合萃取劑,該絡合萃取劑由絡合劑和稀釋劑組成,絡合劑選自磷酸酯類、烷基氧磷類、烷基胺類中的一種或幾種組成的混合物,稀釋劑選自脂肪烴類、芳烴類中的一種或幾種組合的混合物。所述的脂肪烴類稀釋劑優選正己烷或煤油,所述的芳烴類稀釋劑優選苯、甲苯或二甲苯。《2-萘酚生產廢水綜合治理與資源化利用工藝》優選的絡合萃取劑具有以下優點①萃取效率高,具有高選擇性。②化學穩定性強,二次污染小,萃取得到的污染物可以充分利用。③萃取劑易於再生,反萃率高,反萃取沒有乳化現象;萃取與反萃取過程界面清晰,無溶劑夾帶現象。④萃取與反萃取操作易於進行,安全係數高,成本低。
5、在步驟(4)中,所述一級反萃取的過濾液和二級萃取的反萃液直接蒸發濃縮至總含固量40%~70%質量濃度;或蒸發濃縮至一定濃度再加入萘磺酸或加入甲基萘磺酸或加入萘磺酸和甲基萘磺酸的混合物,調整至總含固量為40%~70%質量濃度的廢水濃縮液。
6、在步驟(6)中,所述萘磺酸鹽固體回水解吹萘工序單獨處理利用,或者與工業萘磺化的中和料混合套用處理。所述步驟(1),酸化脫硫的主要目的是為了回收2-萘酚廢水中的SO3,並為廢水後續處理提供條件。
7、在步驟(4)中,將一級反萃液的濾液及二級萃取的反萃液(黑液)轉入蒸發系統進行蒸發濃縮,採用的蒸發器可以為單效也可以為多效,壓力可以採用常壓或減壓。
8、在步驟(5)中,利用“黑液”濃縮後的“廢水濃縮液”合成減水劑,可以採用專利公開號CN1594133A,名稱為“將萘磺酸中和洗滌廢液中分離出的污染物質再利用的方法”中所記載的方法。也可以使用2012年4月前已有技術中公開的其它可適用的方法。
該發明工藝可以根據不同需要採用間歇操作或連續操作的方式處理。2-萘酚生產廢水經過上述方法處理後,各段水質情況見下表:
改善效果
與2012年4月前已有技術相比,《2-萘酚生產廢水綜合治理與資源化利用工藝》工藝更為合理,可以有效地實現2-萘酚生產廢水綜合治理與資源化利用,2-萘酚生產廢水經該發明方法處理後,出水指標達到污水處理排放標準(GB18918-2002)的二級標準。回收的萘磺酸鹽滿足2-萘酚生產質量要求。合成液體減水劑產品各項指標達到或超過GB8076-2008混凝土外加劑高效減水劑指標要求。
附圖說明
圖1為《2-萘酚生產廢水綜合治理與資源化利用工藝》的一種工藝流程簡圖。
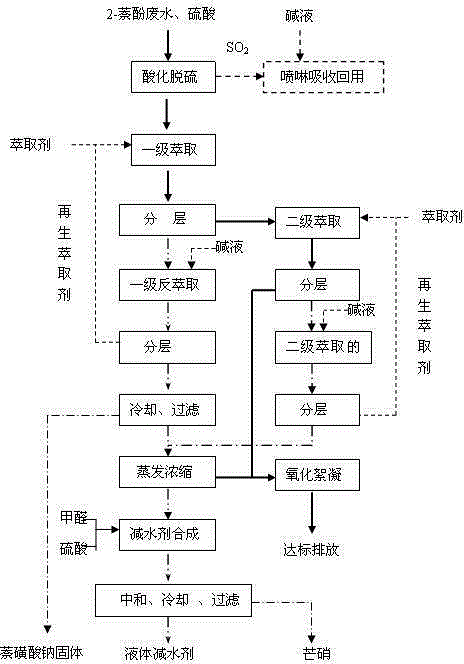
技術領域
《2-萘酚生產廢水綜合治理與資源化利用工藝》涉及一種萘系化工產品生產廢水處理工藝,具體地說是將2-萘酚生產廢水中萘磺酸鈉和亞硫酸鈉等有用物質進行資源化利用,並對廢水進行綜合治理的工藝。
權利要求
1.《2-萘酚生產廢水綜合治理與資源化利用工藝》特徵在於,其步驟如下:
(1)酸化脫硫:2一荼酚生產廢水用無機酸直接酸化至pH值2~3,放出的SO2氣體用無機鹼液噴淋吸收,生成的亞硫酸鹽溶液回用於2一荼酚生產系統;
(2)一級萃取、反萃取:脫硫後的廢水過濾除去不溶物後,常溫常壓下與萃取劑按油水相比1~5:1充分混合,分層後的萃余相即萃後水送二級萃取;萃取相即負載萃取劑常壓下與無機鹼液加熱至60°C~90°C後充分混合,反萃取加鹼量以將pH終點值控制在8.5~9.5為準,分層後的反萃液冷卻後過濾,得到的荼磺酸鹽固體回用於2一荼酚水解吹荼工序;濾液轉入蒸發系統,再生後的萃取劑循環使用於一級萃取;
(3)二級萃取、反萃取:一級萃取的萃後水用無機酸調節pH值至2~3,常溫常壓下再與萃取劑按油水相比1~5:1充分混合進行二級萃取,分層後的萃後水送氧化絮凝處理;負載萃取劑常壓下與無機鹼液加熱至60°C~90°C後充分混合,反萃取加鹼量以將pH終點值控制在8.5~9.5為準,分層後反萃液轉入蒸發系統,再生後的萃取劑循環使用於二級萃取;
(4)蒸發濃縮:將一級反萃取的濾液和二級萃取的反萃液進入蒸發系統,濃縮至總含固量40%~70%質量濃度的廢水濃縮液,蒸發冷凝水送氧化絮凝達標排放;
(5)減水劑合成:將廢水濃縮液和甲醛在硫酸催化下進行縮合反應,加鹼中和並冷卻,過濾出固體結晶,即得液體減水劑;
(6)水解吹荼:將步驟(2)得到的荼磺酸鹽固體加入水解吹荼釜,加水後,在140°C~150°CT通水蒸汽40~60分鐘,吹出的荼用冷水回收;加入
亞硫酸鈉,使部分2-荼磺酸轉變為鈉鹽利用;
(7)氧化絮凝:將二級萃後水和蒸發冷凝水加入次氯酸鈉氧化,再加入聚合氯化鋁和聚丙烯醯胺絮凝反應沉澱處理後,出水達標排放。
2.根據權利要求1所述的工藝,其特徵在於:在步驟(1)和(3)中,所述的無機酸選自硫酸、鹽酸、硝酸或者磷酸。
3.根據權利要求1所述的工藝,其特徵在於:在步驟(1)和(3)中,所述的無機酸為質量濃度為10%~98%的硫酸或10%~31%的鹽酸。
4.根據權利要求1所述的工藝,其特徵在於:在步驟(1)中,所述的無機鹼液選自燒鹼、氨水、純鹼、氧氧化鉀或者碳酸氫鈉溶液。
5.根據權利要求1所述的工藝,其特徵在於:在步驟(2)和(3)中,所述的無機鹼液選自燒鹼、氨水、純鹼、氧氧化鉀或者碳酸氫鈉溶液,且其質量濃度為10%-50%。
6.根據權利要求1所述的工藝,其特徵在於:在步驟(2)和(3)中,所述的無機鹼液為質量濃度為5%~30%的燒鹼溶液。
7.根據權利要求1所述的工藝,其特徵在於:在步驟(2)和步驟(3)中,所述的萃取劑為絡合萃取劑,它由絡合劑和稀釋劑組成,絡合劑選自磷酸酯類、烷基氧磷類、烷基胺類中的一種或幾種組成的混合物,稀釋劑選自脂肪炷類、芳炷類中的一種或幾種組合的混合物。
8.根據權利要求7所述的工藝,其特徵在於:所述的脂肪炷類稀釋劑選自正己烷或煤油,所述的芳炷類稀釋劑選自苯、甲苯或二甲苯。
9.根據權利要求1所述的工藝,其特徵在於:在步驟(4)中,所述一級反萃取的過濾液和二級萃取的反萃液直接蒸發濃縮至總含固量40%~70%質量濃度;或蒸發濃縮至一定濃度再加入荼磺酸或加入甲基荼磺酸或加入荼磺酸和甲基荼磺酸的混合物,調整至總含固量為40%~70%質量濃度的廢水濃縮液。
實施方式
實施例1,參照圖1,2-萘酚生產廢水綜合治理與資源化利用工藝,其步驟如下:
(1)酸化脫硫:2-萘酚生產廢水用無機酸直接酸化至pH值2,放出的SO2氣體用無機鹼液噴淋吸收,生成的亞硫酸鹽溶液回用於2-萘酚生產系統;
(2)一級萃取、反萃取:脫硫後的廢水過濾除去不溶物後,常溫常壓下與萃取劑按油水相比1∶1充分混合,分層後的萃余相即萃後水送二級萃取;萃取相即負載萃取劑常壓下與無機鹼液加熱至60℃後充分混合,反萃取加鹼量以將pH終點值控制在8.5為準,分層後的反萃液冷卻後過濾,得到的萘磺酸鹽固體回用於2-萘酚水解吹萘工序;濾液轉入蒸發系統,再生後的萃取劑循環使用於一級萃取;
(3)二級萃取、反萃取:一級萃取的萃後水用無機酸調節pH值至2,常溫常壓下再與萃取劑按油水相比1∶1充分混合進行二級萃取,分層後的萃後水送氧化絮凝處理;負載萃取劑常壓下與無機鹼液加熱至60℃後充分混合,反萃取加鹼量以將pH終點值控制在8.5為準,分層後反萃液轉入蒸發系統,再生後的萃取劑循環使用於二級萃取;
(4)蒸發濃縮:將一級反萃取的過濾液和二級萃取的反萃液進入蒸發系統,濃縮至總含固量40%質量濃度的廢水濃縮液,蒸發冷凝水送氧化絮凝達標排放;
(5)減水劑合成:將廢水濃縮液和甲醛在硫酸催化下進行縮合反應,加鹼中和並冷卻,過濾出固體結晶,即得液體減水劑;
(6)水解吹萘:將步驟(2)得到的萘磺酸鹽固體加入水解吹萘釜,加水後,在140℃下通水蒸汽40分鐘,吹出的萘用冷水回收;加入亞硫酸鈉,使部分2-萘磺酸轉變為鈉鹽利用;
(7)氧化絮凝:將上述二級萃後水和蒸發冷凝水加入次氯酸鈉氧化,再加入聚合氯化鋁和聚丙烯醯胺絮凝反應沉澱處理後,出水達標排放。
實施例2,參照圖1,2-萘酚生產廢水綜合治理與資源化利用工藝,其步驟如下:
(1)酸化脫硫:2-萘酚生產廢水用無機酸直接酸化至pH值3,放出的SO2氣體用無機鹼液噴淋吸收,生成的亞硫酸鹽溶液回用於2-萘酚生產系統;
(2)一級萃取、反萃取:脫硫後的廢水過濾除去不溶物後,常溫常壓下與萃取劑按油水相比5∶1充分混合,分層後的萃余相即萃後水送二級萃取;萃取相即負載萃取劑常壓下與無機鹼液加熱至90℃後充分混合,反萃取加鹼量以將pH終點值控制在9.5為準,分層後的反萃液冷卻後過濾,得到的萘磺酸鹽固體回用於2-萘酚水解吹萘工序;濾液轉入蒸發系統,再生後的萃取劑循環使用於一級萃取;
(3)二級萃取、反萃取:一級萃取的萃後水用無機酸調節pH值至3,常溫常壓下再與萃取劑按油水相比5∶1充分混合進行二級萃取,分層後的萃後水送氧化絮凝處理;負載萃取劑常壓下與無機鹼液加熱至90℃後充分混合,反萃取加鹼量以將pH終點值控制在9.5為準,分層後反萃液轉入蒸發系統,再生後的萃取劑循環使用於二級萃取;
(4)蒸發濃縮:將一級反萃取的過濾液和二級萃取的反萃液進入蒸發系統,濃縮至總含固量70%質量濃度的廢水濃縮液,蒸發冷凝水送氧化絮凝達標排放;
(5)減水劑合成:將廢水濃縮液和甲醛在硫酸催化下進行縮合反應,加鹼中和並冷卻,過濾出固體結晶,即得液體減水劑;
(6)水解吹萘:將步驟(2)得到的萘磺酸鹽固體加入水解吹萘釜,加水後,在150℃下通水蒸汽60分鐘,吹出的萘用冷水回收;加入亞硫酸鈉,使部分2-萘磺酸轉變為鈉鹽利用;
(7)氧化絮凝:將上述二級萃後水和蒸發冷凝水加入次氯酸鈉氧化,再加入聚合氯化鋁和聚丙烯醯胺絮凝反應沉澱處理後,出水達標排放。
實施例3,參照圖1,2-萘酚生產廢水綜合治理與資源化利用工藝,其步驟如下:
(1)酸化脫硫:2-萘酚生產廢水用無機酸直接酸化至pH值2.5,放出的SO2氣體用無機鹼液噴淋吸收,生成的亞硫酸鹽溶液回用於2-萘酚生產系統;
(2)一級萃取、反萃取:脫硫後的廢水過濾除去不溶物後,常溫常壓下與萃取劑按油水相比3∶1充分混合,分層後的萃余相即萃後水送二級萃取;萃取相即負載萃取劑常壓下與無機鹼液加熱至75℃後充分混合,反萃取加鹼量以將pH終點值控制在9.0為準,分層後的反萃液冷卻後過濾,得到的萘磺酸鹽固體回用於2-萘酚水解吹萘工序;濾液轉入蒸發系統,再生後的萃取劑循環使用於一級萃取;
(3)二級萃取、反萃取:一級萃取的萃後水用無機酸調節pH值至2.5,常溫常壓下再與萃取劑按油水相比3∶1充分混合進行二級萃取,分層後的萃後水送氧化絮凝處理;負載萃取劑常壓下與無機鹼液加熱至75℃後充分混合,反萃取加鹼量以將pH終點值控制在9.0為準,分層後反萃液轉入蒸發系統,再生後的萃取劑循環使用於二級萃取;
(4)蒸發濃縮:將一級反萃取的過濾液和二級萃取的反萃液進入蒸發系統,濃縮至總含固量55%質量濃度的廢水濃縮液,蒸發冷凝水送氧化絮凝達標排放;
(5)減水劑合成:將廢水濃縮液和甲醛在硫酸催化下進行縮合反應,加鹼中和並冷卻,過濾出固體結晶,即得液體減水劑;
(6)水解吹萘:將步驟(2)得到的萘磺酸鹽固體加入水解吹萘釜,加水後,在145℃下通水蒸汽50分鐘,吹出的萘用冷水回收;加入亞硫酸鈉,使部分2-萘磺酸轉變為鈉鹽利用;
(7)氧化絮凝:將上述二級萃後水和蒸發冷凝水加入次氯酸鈉氧化,再加入聚合氯化鋁和聚丙烯醯胺絮凝反應沉澱處理後,出水達標排放。
實施例4,在實施例1-3任何一項所述的工藝的步驟(1)和(3)中,所述的無機酸選自硫酸、鹽酸、硝酸或者磷酸。
實施例5,在實施例1-3任何一項所述的工藝的在步驟(1)和(3)中,所述的無機酸為質量濃度為10%~98%的硫酸或10%~31%的鹽酸。
實施例6,在實施例1-5任何一項所述的工藝的步驟(1)中,所述的無機鹼液選自燒鹼、氨水、純鹼、氧氧化鉀或者碳酸氫鈉溶液。
實施例7,在實施例1-6任何一項所述的工藝的步驟(2)和(3)中,所述的無機鹼液選自燒鹼、氨水、純鹼、氧氧化鉀或者碳酸氫鈉溶液,且其質量濃度為10%-50%。
實施例8,在實施例1-6任何一項所述的工藝的步驟(2)和(3)中,所述的無機鹼液為質量濃度為5%~30%的燒鹼溶液。
實施例9,在實施例1-8任何一項所述的工藝的步驟(2)和步驟(3)中,所述的萃取劑為絡合萃取劑,它由絡合劑和稀釋劑組成,絡合劑選自磷酸酯類、烷基氧磷類、烷基胺類中的一種或幾種組成的混合物,稀釋劑選自脂肪烴類、芳烴類中的一種或幾種組合的混合物。
實施例10,在實施例1-8任何一項所述的工藝中,所述的脂肪烴類稀釋劑選自正己烷或煤油,所述的芳烴類稀釋劑選自苯、甲苯或二甲苯。
實施例11,在實施例1-10任何一項所述的工藝的步驟(4)中,所述一級反萃取的過濾液和二級萃取的反萃液直接蒸發濃縮至總含固量40%~70%質量濃度;或蒸發濃縮至一定濃度再加入萘磺酸或加入甲基萘磺酸或加入萘磺酸和甲基萘磺酸的混合物,調整至總含固量為40%~70%質量濃度的廢水濃縮液。
實施例12,在實施例1-11任何一項所述的工藝的步驟(6)中,所述萘磺酸鹽固體回水解吹萘工序單獨處理利用,或者與工業萘磺化的中和料混合套用處理。
實施例13,參照圖1,2-萘酚生產廢水綜合治理與資源化利用工藝實驗一:
河北某化工廠2-萘酚生產廢水,COD達36000毫克/升,其中含萘磺酸鈉24000毫克/升,亞硫酸鈉34克/升,硫酸鈉58克/升。
(1)酸化脫硫:取2-萘酚生產廢水加入四口燒瓶,常溫下,邊攪拌邊滴加質量濃度96%硫酸,酸化至pH值2~3,並鼓入空氣,吹出的SO2氣體用鹼液(質量濃度30%NaOH)噴淋吸收,生成的亞硫酸鈉溶液回用於2-萘酚生產系統。
(2)一級萃取、反萃取:上述脫硫後的廢水經過濾除去不溶物後,常溫下與萃取劑按油水相比5∶1加入分液漏斗,充分搖勻混契約10分鐘,再靜置20分鐘,分層後下層的萃余相(萃後水)COD約2000毫克/升,送二級萃取進一步處理;上層萃取相(負載萃取劑)加入到燒杯中,加熱至60℃~90℃,在攪拌下加入鹼液(質量濃度15%NaOH)充分混合,反萃取加鹼量以pH值為準,終點pH值控制在8.5~9.5,鹼液加完後繼續攪拌10分鐘,倒入分液漏斗靜置20分鐘分層,分出下層的反萃液冷卻至常溫,過濾析出的固體結晶,得到的萘磺酸鈉回用於2-萘酚水解吹萘工序,過濾液送蒸發濃縮;再生後的萃取劑循環使用於下次萃取。
(3)二級萃取、反萃取:經過一級萃取的萃余相(萃後水)加入到燒杯中,滴加質量濃度96%硫酸調節pH值至2~3,常溫下與萃取劑按油水相比5∶1再加入分液漏斗,充分搖勻混契約10分鐘,再靜置20分鐘,下層的萃余相(萃後水)COD低於300毫克/升,經氧化絮凝可達標;上層萃取相(負載萃取劑)加入到燒杯中,加熱至60℃~90℃,在攪拌下加入鹼液(質量濃度15%NaOH)充分混合,反萃取加鹼量以pH值為準,終點pH值控制在8.5~9.5,鹼液加完後繼續攪拌10分鐘,置於分液漏斗,再靜置20分鐘分層,分出下層的二級萃取的反萃液轉入蒸發濃縮,再生後的萃取劑循環使用於下次萃取。
(4)蒸發濃縮:將上面的一級反萃液冷卻過濾後的濾液和二級萃取的反萃液倒入旋轉蒸發器,加熱並抽真空,進行減壓蒸發,蒸發至總含固量30%左右,再加入萘磺酸調整至50%質量濃度的“廢水濃縮液”,蒸發冷凝水進行氧化絮凝。
(5)減水劑合成:取一定量“廢水濃縮液”加入四口圓底燒瓶,開啟攪拌,緩慢滴加質量濃度98%濃硫酸,酸加完後,取樣測總酸度,調節總酸度在28%左右。加熱升溫至80℃,開始滴加甲醛,保持80~85℃,在2小時內滴加完,在20分鐘內升溫到102~110℃,恆溫縮合反應4小時。反應結束後,向燒瓶內中緩緩加入質量濃度30%液鹼,在攪拌下進行中和反應,調節pH為7~8,用冷凍鹽水冷卻降溫至10℃以下,過濾去除十水硫酸鈉,所得濾液即為高效液體減水劑。測試該減水劑水泥靜漿流動度225毫米,產品各項指標達到或超過GB8076-2008混凝土外加劑高效減水劑指標要求。
(6)水解吹萘:將上面一級反萃液冷卻過濾得到的萘磺酸鈉固體加入四口圓底燒瓶,加入經計量的水,在140℃~150℃下通水蒸汽40分鐘,吹出的萘用冷水噴啉回收;吹萘後,邊攪拌邊加入亞硫酸鈉溶液,使2-萘磺酸轉變為鈉鹽利用。
(7)氧化絮凝:將上述二級萃後水和蒸發冷凝水加入帶攪拌的四口燒瓶,開啟攪拌,滴加次氯酸鈉溶液(有效氯≥7%),氧化反應結束,邊攪拌邊加入聚合氯化鋁(PAC)和聚丙烯醯胺(PAM)溶液,絮凝反應沉澱處理後,出水CODcr≤100毫克/升,SS≤30毫克/升,達到了污水處理排放標準(GB18918-2002)二級標準。
實施例14,參照圖1,2-萘酚生產廢水綜合治理與資源化利用工藝實驗二:
蘇州某染料化工廠2-萘酚生產廢水,該廢水呈深褐色,COD達30000~35000毫克/升,其中含萘磺酸鈉20000~25000毫克/升,亞硫酸鈉30~35克/升,硫酸鈉55~60克/升。
(1)酸化脫硫:常溫下把2-萘酚生產廢水用泵打入酸化釜,開啟攪拌,滴加質量濃度95%硫酸,至pH值2~3,用鼓風機鼓入空氣,吹出的SO2氣體通過降膜吸收塔,用質量濃度30%NaOH溶液噴淋吸收,生成的亞硫酸鈉溶液回用於2-萘酚生產系統。
(2)一級萃取、反萃取:上述脫硫後的2-萘酚廢水經過濾除去懸浮物等雜質後,常溫下和高效萃取劑用泵輸送,經轉子流量計調節流量,按油水相比1∶1連續送至萃取釜,並充分攪拌混合後,連續流入分層塔,停留時間1小時,經分層後,下層的萃余相(萃後水)COD約1800毫克/升,連續送二級萃取進一步處理;上層油層為萃取相(負載萃取劑),連續輸送至負載萃取劑貯罐。負載萃取劑和質量濃度10%NaOH溶液用泵輸送,經轉子流量計調節流量,加鹼量以pH值為準,終點pH值控制在8.5~9.5,經過預熱器預熱,連續流入帶加熱裝置的反萃釜,保持溫度在60℃~90℃,並充分攪拌混合後,連續流入帶保溫裝置的分層塔,停留時間1小時,下層反萃液連續送至冷卻釜,通冷卻水降至常溫,用離心機過濾析出的結晶固體,得到的萘磺酸鈉回用於2-萘酚水解吹萘工序,濾液轉入蒸發濃縮;上層油層為反萃後再生的萃取劑,連續輸送至萃取劑貯罐,循環使用於下次萃取。
(3)二級萃取、反萃取:經過一級萃取的萃余相(萃後水)常溫下和高效萃取劑用泵輸送,經轉子流量計調節流量,按油水相比1∶1連續送至萃取釜,滴加質量濃度31%鹽酸調節pH值至2~3,並充分攪拌混合後,連續流入分層塔,停留時間1小時,靜置分層後,下層的萃余相(萃後水)COD低於300毫克/升,連續流出至氧化絮凝;上層萃取相(負載萃取劑),連續輸送至負載萃取劑貯罐。負載萃取劑和質量濃度15%NaOH溶液分別用泵輸送,經轉子流量計調節流量後,經過預熱器預熱,連續流入帶加熱裝置的反萃釜,保持溫度在60℃~90℃,充分攪拌混合後,連續流入分層塔,停留時間1小時,靜置分層後,下層的二級萃取的反萃液連續送蒸發濃縮,上層油層為反萃後再生的萃取劑,連續輸送至萃取劑貯罐,循環使用於下次萃取。。
(4)蒸發濃縮:將上面的一級反萃液冷卻過濾後的濾液和二級萃取的反萃液經熱交換器加熱,用泵送入三效逆流蒸發系統,進行減壓蒸發,濃縮至總含固量60%左右重量濃度的“廢水濃縮液”,蒸發冷凝水經冷卻塔降溫至35℃下,用泵送入氧化絮凝。
(5)減水劑合成:將一定量“廢水濃縮液”加入縮合釜,開啟攪拌,緩慢滴加質量濃度98%濃硫酸,酸加完後,取樣測總酸度,並調節總酸度至30%左右。開蒸汽加熱升溫至80℃,開始滴加甲醛,保持溫度80~85℃,在2小時內滴加完,加完後20分鐘內升溫到102~110℃,保溫反應4小時。反應結束後,冷卻至80℃,向縮合釜內緩緩加入質量濃度30%液鹼,在攪拌下進行中和反應,調節pH為7~8,用冷凍鹽水冷卻降溫至10℃以下,過濾去除芒硝,所得濾液即為高效液體減水劑。測試該減水劑的水泥靜漿流動度220毫米,產品各項指標達到或超過GB8076-2008混凝土外加劑高效減水劑指標要求。
(6)水解吹萘:將上面一級反萃液冷卻過濾得到的萘磺酸鈉固體與2-萘酚合成磺化工序得到的2-萘磺酸鈉混合加入水解吹萘釜,經計量罐加入計量的水,在140℃~150℃下通水蒸汽40~60分鐘,所含1-萘磺酸水解成萘隨蒸汽蒸出,吹出的萘用冷水噴啉回收;吹萘後,在攪拌下保持溫度不低於90℃,將80~95℃的15%亞硫酸鈉加入釜內,使2-萘磺酸轉變為鈉鹽利用。
(7)氧化絮凝:上述二級萃後水和蒸發冷凝水連續輸送至氧化池,開啟攪拌,連續滴加次氯酸鈉溶液(有效氯≥7%),氧化反應結束,連續輸送至絮凝反應池,邊攪拌邊加入聚合氯化鋁(PAC)和聚丙烯醯胺(PAM)溶液,混合液連續流入沉降池,靜置沉降,沉降時間約1小時,出水CODcr≤100毫克/升,SS≤30毫克/升,達到了污水處理排放標準(GB18918-2002)二級標準。
榮譽表彰
2015年12月1日,《2-萘酚生產廢水綜合治理與資源化利用工藝》獲得第九屆江蘇省專利項目優秀獎。