靜液壓制(冷等靜壓成型)是藉助高壓泵的作用把液體介質壓入耐高壓的鋼體密閉容器內,高壓流體的靜壓力直接作用在彈性模套內的粉末上,使粉末體在同一時間內各個方向均衡受壓而獲得密度分布均勻和強度較高的壓坯。
基本介紹
- 中文名:靜液壓制
- 外文名:hydrostatic pressing
- 含義:一種粉體壓製成型方法
- 套用:陶瓷製造、粉體材料加工
簡介,靜液壓制設備,缸體,高壓泵,管道閥門,缸口密封蓋結構,模具結構,靜液壓制原理,
簡介
在金屬模成形中,複雜形狀或圓柱狀等簡單形狀物體的成形,其加壓方向的厚度比加壓斷面積大時,成形密度不均勻,在燒結時會產生變形問題。這是因為用金屬模威形時,模壁與粉體之闖發生摩擦,壓力傳導不能均勻地達到全系統所致。而用靜水壓成形時,由於通過橡膠等彈性體而在應該成形的粉末上施以靜水壓,從而將金屬模成形中存在的粉體流動與阻止其流動的模壁摩擦阻力的問題通過使用與粉體發生相似收縮的橡膠等彈性體而解決了。
靜水壓制雖在70年前就已提出,但由於超高壓技術長期沒有發展而未得到工業性實用。近20年來隨著超高壓技術的進步,已成為工業化的成形方法。從點火栓火花塞、球磨機用磨球等小型製品,到連續鑄造用浸漬噴嘴等均已在工業上得到套用。正在向以成形大型製品及同時成形大量製品為目的的大型化生產發展。在大型設備中,高壓容器內部尺寸為宜徑1.5m、高3.5m的超大型機器也已出現。
靜液壓制方法是可以獲得密度均勻的壓件的粉末成形方法之一。這種方法的實質在於:把粉末裝在彈性模具中,經受各個方向的液體靜壓力。過程是在密封室中進行的,密封室裝有用來工作的液體-油、水、甘油等。液體靜壓力通常是202~404MPa或更高一些。
靜液壓制彈性模一般是用橡皮、塑膠等製成的。將粉末裝人模中時,裝粉的均勻性對製品的密度和形狀有一定影響,所以,通常用振動的方法使粉末在模具中均勻填充。在密封好的彈性模外邊還要緊套上一個帶孔的套筒,然後進行壓制。
液靜壓制的特點是在這種情況下,沒有外摩擦的影響。粉末顆粒在液體靜力作用下,向壓件中心移動。用液靜壓制各種形狀的壓件(圓柱體、球體、矩形坯條)時,發現只有球形和圓柱形壓件,其外緣到中心的密度有很小的降低(1%~2%)。這種現象可能是由於拱橋效應所引起的。矩形坯條各處的密度和硬度都相同。
液靜壓壓制是在液靜壓機中進行的。液靜壓機的主體部分分高壓工作室和高壓泵兩部分。
靜液壓制設備
靜液壓制設備主要由3部分組成,即由缸體(高壓容器)、高壓泵、管道閥門組成。
缸體
冷等靜壓缸體也叫高壓容器。其形狀一般為厚壁圓筒形。按照材料力學關於厚壁圓筒的強度計算可知,如果將單層壁圓筒在壁厚不變的情況下改為雙層壁預應力圓筒,則高壓容器的耐壓強度可以提高很多。若改成多層預應力圓筒,則其耐壓強度更加提高。冷等靜壓缸體按筒壁的層數可分為下列3種
- 單層厚壁圓筒
- 雙層厚壁圓筒
- 纏繞式圓筒,由高強度(σb>3000MPa)的小鋼帶多層纏繞製成。
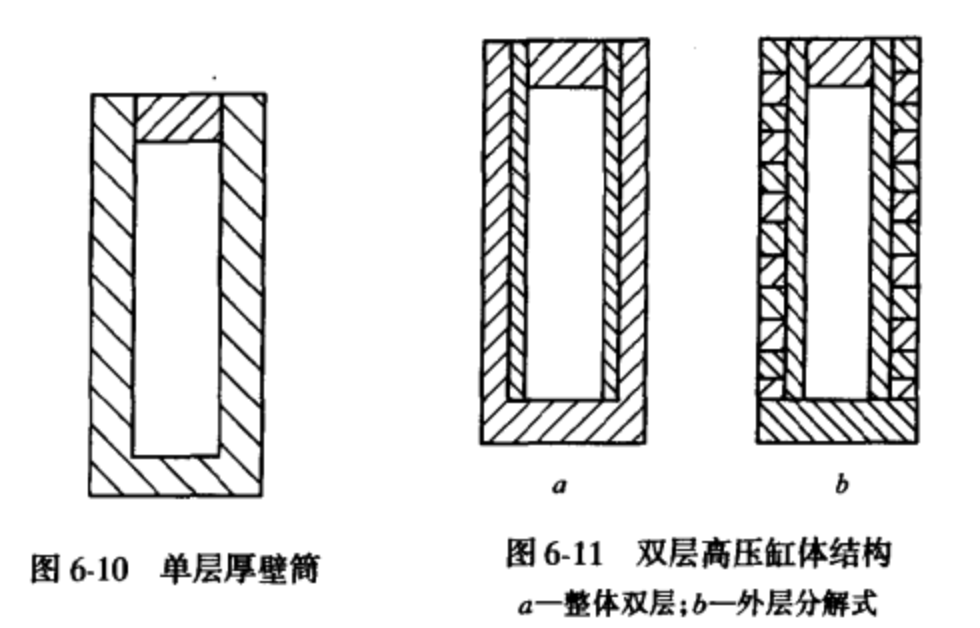
高壓泵
高壓柱塞泵和(液、氣)泵,油泵可供給300 MPa壓力油,氣泵可供100 MPa壓縮氣。薄膜泵,一般用來供高壓氣(Ar,N2),壓力小於100 MPa。
增壓器,是增壓氣泵和增壓油泵的總稱。增壓氣泵可將0~2 MPa常壓氣體增壓到5~50MPa;增壓油泵可將32MPa油液增壓到300MPa。
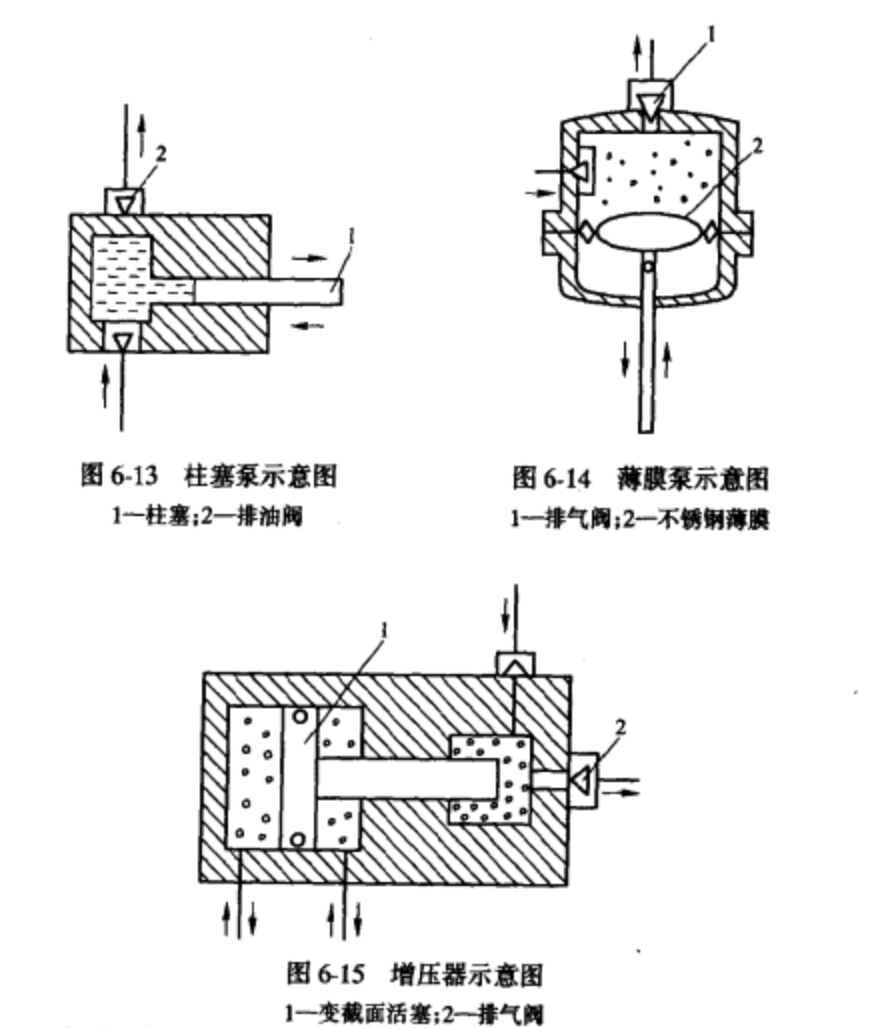
管道閥門
管道一般用厚壁無縫鋼管,最好是厚壁無縫不鏽鋼管。
閥門:低壓可用電液閥,高壓一般為手動針形閥。
缸口密封蓋結構
螺旋式,使用麻煩,逐漸淘汰。
活塞式,缸口由活塞與“O”形橡膠密封環(圈)或楔形橡膠聚四氟複合密封環(圈)密封。
模具結構
濕袋結構,濕袋是用橡皮、聚乙烯等軟袋,做成裝粉末的軟袋。在使用時,軟袋直接放入油液中直接與液體接觸。壓制完成後,將粉末壓坯和橡膠袋一同取出,將橡膠袋錶面的油擦乾再將壓坯從橡膠袋中取出即可。此法稱濕袋法。是因為常與油膩的橡膠袋接觸,壓坯脫模時油膩粘污雙手,不易操作。
乾袋結構。乾袋結構是採用雙層橡皮袋、加壓橡皮袋固定並密封在高壓缸體口上,高壓油只局限在鋼模和加壓橡皮袋之間很小的空間內。裝粉末的橡皮袋(也可不用)放在加壓成形橡皮袋內,粉末受加壓橡皮袋擠壓而成形。這種結構裝粉和取壓件都很方便。特別是生產時不與油液接觸,工件乾淨,勞動條件較好,因此生產效率很高(可達10~15件/min)。大製品(可達300件/h)。
乾袋法在高強度陶瓷硬質合金棒材、磁性材料等在生產中得到了廣泛套用,特別是近年來英國希馬克公司生產的Monostatic系列乾袋式等靜壓機生產效率很高壓坯表面光潔。尺寸精度高可生產形狀複雜的陶瓷壓坯。
靜液壓制原理
靜液壓制工藝的物理本質就足利用巴斯葛原理,流體基本上是不可壓縮的,給流體施加壓力,壓強通過流體連續的傳遞,在液體中各處的壓強相等。不過要注意,在高壓狀態下液體也會發生收縮,一般認為在壓力超過50MPa時,體積會發生明顯收縮,可高達
。


上圖是等靜壓機的原理圖(以濕式為例)。用大型高強度鋼鍛件做的高壓缸是等靜壓機的主體零件,或者用鋼件做缸體內襯,外面用鋼帶,鋼絲纏繞,提高壓缸的抗壓強度,保證壓缸工作時的安全性。高壓缸內裝液體油,或者含有5%油的乳化液,也可裝純淨水,用這些液體做傳遞壓力的介質。操作時用高壓泵向壓缸內加添少許液體,可把缸內的液體壓力提高到約200MPa,需要壓制的粉末裝在一個柔性的塑膠套(袋)內,排盡膠套內的空氣,並把膠袋密封,防止壓制過程中油進入套內。膠套置於高壓缸內的液體介質裡面,在高壓液體的作用下,膠套內的粉末被壓成壓坯。通常在柔性塑膠套的外面套一個等尺寸同形狀的鋼外套,以便保證壓坯的形狀和尺寸的準確性。柔性套用天然橡膠或人造塑膠製造,通常人造塑膠的成分(質量分數)是:聚氯乙烯樹脂100份,苯二甲酸二辛酯100份(或者苯二甲酸二丁酯),三元基硫酸鉛2~3份,再加硬脂酸0.3份,攪拌混合均勻,抽真空排氣後,用混合調好的膠體製造軟套的過程為:只把符合設計尺寸要求的芯棒放在混合好的液態膠內,使芯棒表面沾帶有一定厚度的膠體,再把帶有膠體的芯棒放在適當的高溫烘箱內烘烤一定時間,套子定形後水冷脫模,並仔細檢查保證膠套沒有滲漏,否則,在等靜壓機的高壓缸內加壓時,液體滲入套內粉末變成稀的金屬泥料而不能成形。
裝有粉末的柔性套放人高壓缸的液體內,軟模套和粉末同時受壓變形。與鋼模壓制不同,等靜壓時軟模套和被壓粉末同時變形,消除了壓模和粉末之間的摩擦壓力損失,粉末之間相對運動距離很小,特別是縱向比橫向要小得多。高壓缸內的液體各處的水靜壓力認為都是相等的。這樣一來,等靜壓壓制的粉末壓坯各處的密度近似是相等的。
但是,經過仔細的分析研究後發現,等靜壓壓出的毛坯各點的密度還是有一點差別,特別對大直徑坯料,但總體差別不大。對於直徑80mm的鉬生坯的密度進行了解剖分析,壓制壓力接近200MPa,用車床把鉬壓坯的外徑每次車掉10mm,分六次把壓坯的直徑車小到20mm。實際上每次車掉一個同心圓套,計算出圓套的體積和重量,就可算出每個同心圓套筒的密度,可以得出壓坯直徑方向的密度分布。壓坯的平均密度和相對密度自外向里逐漸變小,車下的套環的密度自大直逕到小直徑密度是逐漸下降,即整個壓坯的密度由里向外逐漸向上升。最外面一層環的密度比心部的密度高約5%。而等靜壓壓制的平板坯的內外密度差比圓柱體的小約50%。板坯的內外密度差比圓柱體的小,板坯的密度均勻。
這種密度差的根源在於粉末之間存在有內摩擦,引起由外向內的壓力損失。粉末壓坯的壓制密度與壓力有直接關係,這種關係可能符合巴爾申關係或者雙對數方程的關係。等靜壓壓制的壓坯密度與壓制壓力之間關係的研究表明,粉末粒度和壓坯形狀(長徑比)之問有關係,壓坯的徑向收縮和軸向收縮是不一樣的,存在有收縮的各向異性。細粉的收縮率比粗粉的高,粗粉收縮的各向異性比細粉的嚴重一點(粉末的粒度5.0μm、3.5μm和2.3μm)。