概述
全世界電工鋼的總產量約700萬噸。當前,特別這幾年隨著中國電力、電器工業的迅猛發展,中國的
矽鋼片需求量快速增加,2004年的消費量幾乎已占全世界矽鋼片產量的一半,導致中國的
矽鋼產量進入了一個快速發展時期,但仍然無法滿足國內需求,2004年進口矽鋼片164萬噸。

電工鋼已有上百年的歷史,電工鋼包括Si<0.5%電工鋼和Si含量 0.5~6.5%的矽鋼兩類,主要用作各種電機、變壓器和
鎮流器鐵芯,是電力、電子和軍事工業中不可缺少的重要
軟磁合金。電工鋼在磁性材料中用量最大,也是一種節能的重要金屬功能材料。電工鋼,特別是
取向矽鋼的製造工藝和設備複雜,成分控制嚴格,製造工序長,而且影響性能的因素多,因此常把取向矽鋼產品質量看作是衡量一個國家特殊鋼製造技術水平的重要標誌,並獲得特殊鋼中“藝術產品”的美稱。
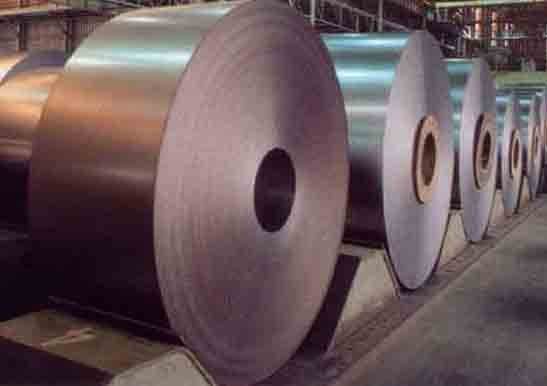
發展歷史
鐵的
磁導率比空氣的磁導率高几千到幾萬倍,
鐵芯磁化時
磁通密度高,可產生遠比外加磁場更強的磁場。普通熱軋
低碳鋼板是工業上最早套用的鐵芯軟磁材料。1886年美國Westinghouse電氣公司首先用雜質含量約為0.4%的熱軋低碳鋼板製成變壓器
疊片鐵芯。1890年已廣泛使用0.35mm厚熱軋低碳鋼薄板製造電機和
變壓器鐵芯。但由於低碳鋼
電阻率低,
鐵芯損耗大;碳和氮含量高,
磁時效嚴重。1882年英國哈德菲爾特開始研究矽鋼,1898年發表了4.4%Si-Fe合金的磁性結果。1903年美國取得哈德
菲爾特專利使用權。同一年美國和德國開始生產
熱軋矽鋼板。1905年美國已大規模生產。在很短時間內全部代替了普通熱軋
低碳鋼板製造電機和變壓器,其
鐵損比普通低碳鋼低一半以上。1906~1930年期間,是生產廠與用戶對熱軋矽鋼板成本、力學性能和電機、變壓器設計製造改革方面統一認識、改進產品質量和提高產量的階段。
冷軋電工鋼發展階段(1930~1967年)
此階段主要是冷軋普通取向矽鋼(GO)板的發展階段。1930年美國高斯採用冷軋和退火方法開始進行大量實驗,摸索晶粒易磁化方向<001>平行於軋制方向排列的取向矽鋼帶卷製造工藝。1933年高斯採用兩次冷軋和退火方法製成沿軋向磁性高的3%Si鋼,1934年申請專利並公開發表。1935年Armco鋼公司按高斯專利技術與Westinghouse電氣公司合作進行生產。之後,Armco鋼公司採用快速分析微量碳等技術和不斷改進制造工藝及設備,使產品質量逐步提高。直到1958年在掌握MnS抑制劑和板坯高溫加熱兩個前工序製造工藝後,製造取向矽鋼的專利技術已基本完善,產品磁性大幅度提高且穩定。1959年開始生產0.30mm厚產品,1963年生產0.27mm產品。40年代初,Armco鋼公司開始生產冷軋無取向矽鋼板。1963~1967年期間,英國、日本等國家陸續停止生產
熱軋矽鋼板。熱軋矽鋼板逐步被冷軋
無取向電工鋼和冷軋取向矽鋼板所代替。
1961年,新日鐵在引進Armco專利基礎上,首先試製AlN+MnS綜合抑制劑的高磁感取向矽鋼。1964年開始試生產並命名為Hi-B,但磁性不穩定。經過15年的持續改進,Hi-B鋼製造工藝已日臻完善,並於1968年正式生產Z8H牌號。從1979年開始,新日鐵和川崎公司採用提高矽含量、減薄產品鋼帶厚度和細化
磁疇技術,陸續生產了0.30、0.27、0.23及0.18mm高磁感取向矽鋼新牌號。
分類
| 類 別
| 矽含量,%
| | |
| | 1.0~2.5
| 0.50
| |
| 3.0~4.5
| 0.35和0.50
| | |
| | | ≤0.5
| 0.50和0.65
|
| >0.5~3.2
| 0.35和0.50
| | |
取向矽鋼 (冷軋變壓器鋼)
| 普通取向矽鋼
| 2.9~3.3
| 0.20,0.23,0.27 0.30和0.35
| |
| | 2.9~3.3
| | |
電工鋼除上表品種類別外,還有一些特殊用途的
電工鋼板,如0.15和0.20mm厚3%Si冷軋
無取向矽鋼薄帶和0.025、0.05及0.1mm厚3%Si冷軋取向矽鋼薄帶,用作中、
高頻電機和變壓器以及
脈衝變壓器等;繼電器和電力開關用的0.7mm厚3%Si高強度冷軋無取向矽鋼板;新型高轉速
電機轉子用的高強度冷軋電工鋼板;醫用
核磁共振斷層掃瞄器等
磁禁止和
高能加速器電磁鐵用的
低碳電工鋼熱軋厚板和
冷軋板;高頻電機和變壓器以及磁禁止用的4.5%~6.5%Si高矽鋼板等。
性能要求
一般要求電機、變壓器和其他電器部件效率高,耗電量少,體積小和重量輕。
電工鋼板通常是以
鐵芯損耗和磁感應強度作為產品磁性保證值[1]。對電工鋼板性能的要求如下:
鐵芯損耗(PT)低
鐵芯損耗是指
鐵芯在≥50Hz交變磁場下磁化時所消耗的無效電能,簡稱
鐵損,也稱交變損耗,其單位為W/kg。這種由於磁通變化受到各種阻礙而消耗的無效電能,通過鐵芯發熱既損失掉電能,又引起電機和變壓器的溫升。電工鋼的鐵損(PT)包括
磁滯損耗、
渦流損耗(Pe)和反常損耗(Pa)三部分。電工鋼板鐵損低,既可節省大量電能,又可延長電機和變壓器工作運轉時間,並簡化冷卻裝置。由於電工鋼板的鐵損所造成的電量損失占各國全年發電量的2.5%~4.5%,因此各國生產電工鋼板總是千方百計設法降低鐵損,並以鐵損作為考核產品磁性的最重要指標,按產品的鐵損值作為劃分產品牌號的依據。
磁感應強度是
鐵芯單位截面積上通過的磁力線數,也稱
磁通密度,它代表材料的磁化能力,單位為T。
電工鋼板的磁感應強度高,鐵芯的
激磁電流(也稱
空載電流)降低,
銅損和
鐵損都下降,可節省電能。當電機和變壓器功率不變時,磁感應強度高,設計Bm可提高,鐵芯截面積可縮小,這使鐵芯體積減小和重量減輕,並節省電工鋼板、導線、絕緣材料和結構材料用量,可降低電機和變壓器的總損耗和製造成本,並且有利於大變壓器和大電機的製造、安裝和運輸。
取向矽鋼設計Bm高達1.7~1.80T,接近B8值,因此以B8作為磁感保證值。電機設計Bm約為1.5T,接近冷軋
無取向電工鋼B50值,因此冷軋
無取向矽鋼以B50作為磁感保證值。熱軋
矽鋼的磁感更低,通常以B25作為保證值。
電機是在運轉狀態下工作,
鐵芯是用帶齒圓形沖片疊成的
定子和轉子組成,要求
電工鋼板為磁
各向同性,因此用無取向冷軋電工鋼或熱軋矽鋼製造。一般要求縱橫向
鐵損差值<8%,磁感差值<10%。
沖片性良好
用戶使用電工鋼板時沖剪工作量很大,因此要求電工鋼板應具有良好的沖片性,這對微、小型電機尤為重要。沖片性好可以提高沖模和剪刀壽命,保證沖剪片尺寸精確以及減小沖剪片毛刺。
影響沖片性的因素主要有:1)
沖模或
剪刀材料。如硬質合金沖模的沖片性比
工具鋼沖模提高一倍以上。2)沖頭與沖模的間距。合適的間距一般為鋼板厚度的5%~6%。3)沖片用潤滑油種類。4)沖片形狀。5)鋼板表面絕緣膜種類和質量。6)鋼板的硬度等。後兩個因素與
電工鋼板質量有關。
鋼板表面光滑、平整和厚度均勻
要求電工鋼板表面光滑、平整和厚度均勻,主要是為了提高鐵芯的
疊片係數。疊片係數高可使
鐵芯有效利用空間增大,
空氣隙減小,使激磁電流減小。電工鋼板的疊片係數每降低1%相當於
鐵損增高2%,磁感降低1%。
絕緣薄膜性能好
為防止鐵芯
疊片間發生短路而增大
渦流損耗,冷軋電工鋼板表面塗一薄層無機鹽或無機鹽+
有機鹽的半有機
絕緣膜。對絕緣膜有以下要求:1)
耐熱性好。在750~800℃
消除應力退火時不會破壞。2)絕緣膜薄且均勻。3)層間電阻高。4)附著性好。5)沖片性好。6)耐蝕性和防鏽性好。7)
焊接性好。用途不同,對絕緣膜的要求也有差異。
鐵磁材料的磁性隨使用時間而變化的現象稱為磁時效。這種現象主要是材料中碳和氮等雜質元素引起的。
電工鋼板中碳和氮含量小於0.0035%時,磁時效明顯減小。
生產工藝[2]
冶煉
矽鋼主要用氧氣轉爐冶煉(也可用
電弧爐冶煉),配合鋼水
真空處理和AOD技術(見
爐外精煉,採用模鑄或連鑄法。根據不同的用途,冶煉時改變矽(0.5~4.5%)和鋁(0.2~0.5%)含量以滿足不同磁性的要求。高牌號
矽鋼片的矽和鋁量相應提高。碳、硫和夾雜物儘量減少。
軋制
冷軋矽鋼片的磁性、表面質量、填充係數和沖片性比熱軋
矽鋼片好,並可成卷生產,所以從60年代開始有些國家已停止生產熱軋矽鋼片。中國採用約 900℃低溫一次快速熱軋和氫氣保護下成垛退火方法製造熱軋矽鋼片,成材率較高,成品表面質量和磁性都較好。
酸洗
通過除鱗機與鹽酸罐,除去熱軋鋼帶的氧化物,以防止冷軋成品表面的缺陷。
冷軋
為了確保不同用途的厚度與材質,將減速比例設在40%-90%,並為實現自動厚度控制、自動形狀控制等先進的控制設備。
退火
是軟化
冷衝壓工程中硬化了的鋼帶材質的工程。通過金屬加熱及急速冷卻,生產深加工用鋼及高張力鋼,並採用裝箱(罩退)退火與
連續退火法。
絕緣塗層
將矽鋼板加工成鐵芯時,為改善其加工性能並防止相當於鋼板厚度自乘的
渦電流損失,採用連續塗鍍設備,在鋼板上下面噴射絕緣塗液。
影響因素
化學成分的影響
電工鋼成分組成基本包括三大類元素。第一類為基本合金元素,如Si、Al、Mn等;第二類為雜質元素,如C、S、N、O、Ti、Zr 等;第三類為微量元素如Sb、Sn等。
第一類元素的影響
Si、Al、Mn是有益的合金元素,可使鐵的
磁各向異性常數K1和飽和
磁滯伸縮常數λs值降低,磁化更容易,所以Ph降低。另外這些元素還可提高
電阻率,使Pe降低。因此提高第一類元素的含量可以明顯降低
鐵損。但當這些元素含量太高時,材料變得既硬又脆而無法冷加工。
第二類元素的影響
C、S、N、O、Ti、Zr等為有害元素,這些元素的存在可在鋼中形成細小彌散的
碳化物、硫化物、氮化物及氧化物,阻礙
成品退火時
晶粒長大,對磁性能不利,因此要求鋼中這類元素的含量越低越好。
第三類元素的影響
在
無取向矽鋼中添加少量的Sb、Sn,可以改善
無取向電工鋼再結晶退火後的
織構,使(100)和(110)有利織構組分明顯增加,使(111)不利織構組分明顯減弱,從而降低鐵損,提高磁感。添加少量的此類元素,還可以抑制
內氧化層和氮化層的形成,改善磁性。
晶粒尺寸大,
晶界數量少,
疇壁移動的阻力小,
磁滯損耗降低。另一方面,晶粒尺寸大,
磁疇尺寸增大,
渦流損耗和反常損耗都增加。因此為了降低總
鐵損有一個合適的臨界晶粒尺寸。
無取向電工鋼中夾雜物和雜質元素應儘量降低,這是提高磁性的最重要措施。它們不僅阻礙疇壁移動使磁滯損耗和
矯頑力增高,同時為了降低其周圍靜
磁能而產生了閉合疇使磁化困難。它們對
晶粒長大和
織構組分也有很壞的影響。
電工鋼板中存在任何內應力都使矯頑力增高。
晶體織構
在
取向矽鋼中,提高B8使
磁滯損耗明顯降低。對無取向電工鋼來說,(100)面織構高,磁滯損耗和P15最低,(110)織構次之,(111)織構最差。
鋼板厚度
一般來說,鋼板厚度減薄,磁滯損耗增高。但厚度減薄,
渦流損耗明顯降低。因此對總
鐵損來說也有一個合適的臨界厚度。
鋼板表面平整光潔,表面自由
磁極減少,靜
磁能降低,
疇壁移動阻力減小,則磁滯損耗和
矯頑力降低。