《鐵路T型簡支梁現場預製循環流水生產線施工工法》是中鐵十二局集團有限公司、中國土木工程集團有限公司完成的建築類施工工法,完成人是王立軍、范軍、王勇、王雙卯、張金平。適用於生產總量在1000片以上的所有T梁預製場。
《鐵路T型簡支梁現場預製循環流水生產線施工工法》主要的工法特點是工廠化、流水化生產;施工方便;梁體在養護車間內恆溫養護。
2011年9月,《鐵路T型簡支梁現場預製循環流水生產線施工工法》被中華人民共和國住房和城鄉建設部評定為2009-2010年度國家二級工法。
基本介紹
- 中文名:鐵路T型簡支梁現場預製循環流水生產線施工工法
- 工法編號:GJEJGF253-2010
- 完成單位:中鐵十二局集團有限公司、中國土木工程集團有限公司
- 主要完成人:王立軍、范軍、王勇、王雙卯、張金平
- 套用實例:包西鐵路通道(陝西段)BXS-2標段內95座橋
- 主要榮譽:國家二級工法(2009-2010年度)
形成原因,工法特點,操作原理,適用範圍,工藝原理,施工工藝,材料設備,質量控制,安全措施,環保措施,效益分析,套用實例,榮譽表彰,
形成原因
鐵路T形簡支梁現場預製循環流水生產線可以實現T形簡支梁的工廠化、半自動化大規模批量生產。T形簡支梁預製在中國國內外已經發展多年,施工技術非常成熟,無論是工廠制梁還是現場制梁,截至2009年,一直採用傳統的固定制梁台座生產方式,受無砕軌道雙塊式軌枕環形流水生產線的啟發,借鑑相關行業工廠化、流水化、自動化生產經驗,中鐵十二局集團甘泉制梁場開始研究制梁循環流水生產線施工新方式,成功建設了世界上首條T梁預製循環流水生產線。
工法特點
《鐵路T型簡支梁現場預製循環流水生產線施工工法》的工法特點如下:
1、工廠化、流水化生產:通過動力系統牽引,所有工序集成在底模托架台車上按照制梁的順序流水作業完成,始端輸入原材料,循環中完善,終端輸出產品。
2、施工方便,提高了工效,流水化生產環環相扣,車間內工人在固定區域進行固定的工作內容,專業化程度得以提升,開發了新型的勞務管理模式。
3、梁體在養護車間內恆溫養護,在高緯度環境地區養護效果非常顯著。
操作原理
適用範圍
1、隨著鐵路建設的飛速發展,大標段成為必然,時速200千米/小時及以下的鐵路,建設大規模T梁預製場成為現場制梁的主要方式,《鐵路T型簡支梁現場預製循環流水生產線施工工法》適用於生產總量在1000片以上的所有T梁預製場。生產總量在1000片以下的T梁預製場,使用該工法時需調整生產線總長度、車間數及加強各個車間的功能共用性。
2、由於梁體生產的特殊性,使用《鐵路T型簡支梁現場預製循環流水生產線施工工法》生產T梁時需注意,大風天氣較多、溫差較大地區需加強恆溫養護後降溫過程控制。
工藝原理
《鐵路T型簡支梁現場預製循環流水生產線施工工法》的制梁生產區共設計4條循環流水生產線,每2條線形成閉合雙向循環,每條線分為9個生產車間13個台座,配置8套側模、12套底模及托架台車。通過動力系統卷揚機的牽引,由專用的移動式底模托架台車在生產線軌道系統上完成各個制梁工序的不斷往前推移,實現從原材料到半成品最後到成品梁的循環流水作業。
施工工藝
《鐵路T型簡支梁現場預製循環流水生產線施工工法》的施工工藝如下所述:
- 工藝流程
循環流水線制梁作業是將所有工序分解、排列、最佳化後再組合,所有工序全部集中在生產線的9個車間內進行作業,按工序作業順序由底模作業車間、底腹板鋼筋綁紮車間、模板安裝車間、頂板鋼筋綁紮車間、混凝土澆築車間、養護車間、拆模車間、初張拉車間及橫移車間組織作業生產。
工藝流程運轉如圖1所示。
底模作業車間是負責底模就位,利用移梁機將閉合循環對面的底模吊移到生產線滾輪上,進行底模清理、反拱調整、塗刷脫模劑、安裝支座板後,牽引底模拖架至底腹板鋼筋綁紮車間。
底腹板鋼筋綁紮車間完成梁體底腹板鋼筋的原位梆扎,鋼筋報檢通過後牽引至模板安裝車間。
模板安裝車間完成端模、側模及抽拔橡膠棒的安裝,利用10噸龍門吊安裝端模及錨墊板,人工穿入橡膠棒,10噸龍門吊安裝側模,安裝檢驗完畢後牽引至頂板鋼筋綁紮車間。
頂板鋼筋綁紮車間完成橋面頂板鋼筋的綁紮,調筋後報檢通過牽引至混凝土澆築車間。
混凝土澆築車間完成梁體混凝土的入模及預留孔洞、斷縫成型,同一生產線上的2片梁同時澆築,拔除橡膠棒,拆除斷縫板、橫隔板、梳筋板後牽引相鄰2片梁體至相臨的養護車間養護。
養護車間完成梁體混凝土達到拆模強度前的自然養護,同條線的兩個養護車間連線一個整體,用篷布、草簾、塑膠布密封嚴實,保證棚內35~40℃的恆溫養護效果,以快速增長混凝土強度,滿足拆模及初張要求,加快模板循環。
拆模車間完成端模、側模的拆除,達到強度後的梁體連同模板牽引到位後,在該車間進行模板拆卸作業,拆模採取“上頂下拉、同步平移”的方法,卸下整塊鋼模後,塗刷脫模劑,通過小龍門吊吊至對面相鄰生產線進行安裝,從而形成側模的循環。
初張拉車間完成梁體的初次張拉,滿足起吊移梁要求。
梁體橫移車間完成梁體橫移出生產線到存梁區及底模托架台車的調運,利用160噸提梁機提至縱移區,再由2台80噸龍門吊提吊到存梁區,待提梁機返回到生產線後,將整體底模托架提吊到對面生產線的滾輪上,該次的底模循環完成,進入另一次循環。
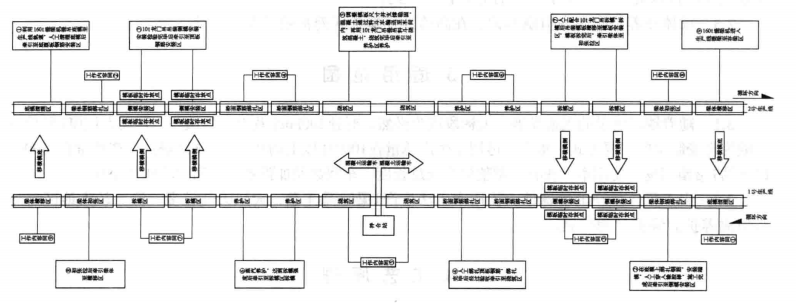
圖1 T梁循環生產線工藝流程運轉圖
每條生產線共用一個牽引車間,每次每個台位前移40米後,回送主鋼絲繩40米,再次牽引,依次將所有工序牽引前移,在橫移車間,梁體預製完成,在存梁區內進行終張拉、壓漿、封端、防水層、保護層等工序作業。
- 操作要點
1、循環流水生產線功能區高度集成
梁場流水生產線共設定4條,1號線與2號線、3號線與4號線分別組成環形流水作業,形成閉合循環。生產線與鋼筋加工區、鋼構件加工區、拌合站等配套車間平行設定,鋼筋加工區對應於生產線綁紮區、拌合站對應於生產線澆築區橫向就近緊密設定。設定固定式養護通道,相對於傳統分散式養護,解決了集中養護問題。
2、循環流水生產線軌道系統
流水線軌道系統分為重載區和輕載區,都採用輪軌式技術,由滾輪和基礎兩部分組成,重載區設計為整體條形基礎,輕載區為兩條條形基礎,並在基礎上均勻布置滾輪。生產線軌道系統斷面圖見圖2。
滾輪加工設計為輪軸式結構,軸與輪的表面要進行熱處理且硬度達到55HRC,輪與軸採用間隙配合、兩者的配合間隙為0.008~0.02毫米之間且表面光潔度要滿足要求;輪兩側各凸起一個3毫米高、13毫米寬的凸台起導向作用;軸與支架間採用過盈配合,防止軸與支架間相互磨損;支架兩側擋板軸孔要同心,偏差不超過0.1毫米,確保滾輪安裝完成後輪頂面與支架底面平行,擋板要高出輪頂面2厘米以防止側滑,牽引時由輪與軸之間滾動完成台車縱移。滾輪構造圖見圖3。
滾輪安裝採用栓接形式,內部填塞乾硬砂漿由螺栓將其擠密,四周焊接鋼板條進行加固,用電子測微水準儀(精度0.1毫米)進行縱向高程測量,框式水平儀進行橫向水平測量保證測量滾輪安裝精準度,要求不大於1毫米;為防止由於滾輪安裝誤差產生個別滾輪與鋼軌不接觸情況造成台車撓度過大出現偏向、變形等現象影響產品質量,滾輪布置設計為縱向間距1米。

圖2 循環流水生產線軌道系統斷面圖

圖3 滾輪構造圖
3、循環流水生產線底模台車
底模托架台車是循環流水生產線預製T梁必要的工裝載體,需要合格的剛度、強度及良好行走性能。台車共設計四道縱梁,縱梁間距為350毫米,所用材料為16b號工字鋼,縱梁與縱梁之間用小鋼板連線,並在底部兩側縱梁加設滑移鋼軌,保證了專用底模托架台車的良好的滑動性能。每隔1000毫米設定一道橫樑,橫樑所處位置對應底模橫擔,橫樑用1厘米厚30厘米寬的鋼板,台車的兩個端頭均設定U形環掛鈎,便於牽引時的連線。
底模托架台車經過計算,縱梁及橫樑的強度、剛度、抗傾覆性均滿足要求,在整體吊裝時,最大撓度在允許彈性變形範圍內,滿足要求。
底模托架台車結構斷面如圖4所示。
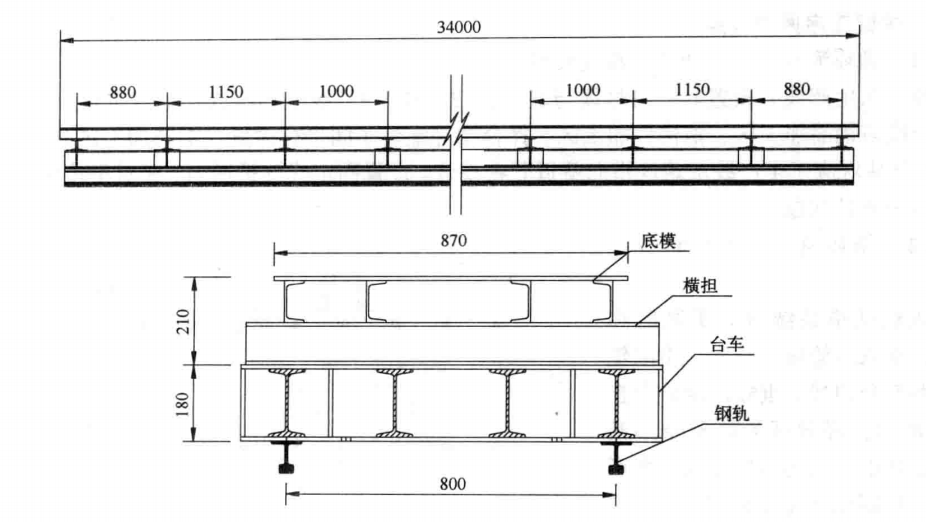
圖4 底模托架台車斷面圖(單位:毫米)
4、循環流水生產線牽引系統
生產線的動力系統由一台10噸卷揚機和一台2噸回送卷揚機組成,固定在生產線兩端,採用單線往復式牽引,結構簡單,操作方便,10噸卷揚機用於牽引梁體,2噸卷揚機用於回送鋼絲繩,兩台裝置聯動,使鋼絲繩作往復運動,鋼絲繩每40米設定一個牽引環,各個車間範圍內採用分段牽引。在卷揚機前設定了滑輪組,增大牽引力,控制牽引速度,保證了梁體牽引過程的穩定性。牽引原理如圖5所示。
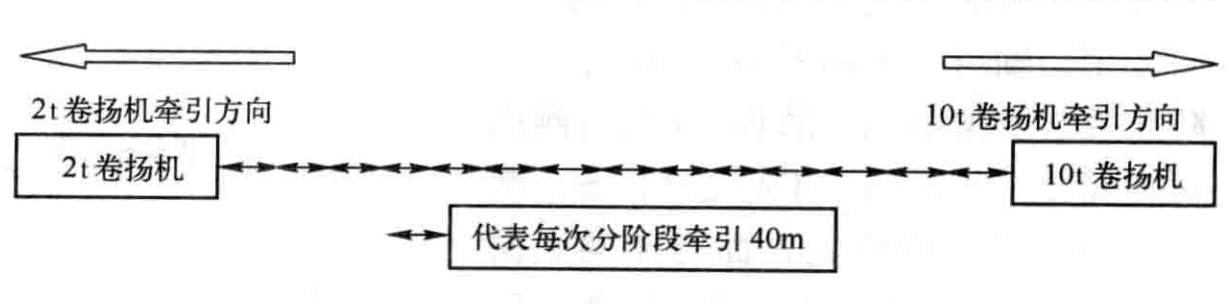
圖5 牽引原理圖
10噸卷揚機將梁體往前牽引40米到位後,鬆開牽引卡環,用另一端的2噸卷揚機回送主鋼絲繩40米,再次用10噸卷揚機牽引,依次將所有工序牽引前移。
- 生產線流水化生產組織要點
移動底模托架台車在各個車間之間平移,車間的功能有一定共用性,比如底模作業車間也可以綁紮梁體底腹板鋼筋,底腹板鋼筋綁紮車間也可以進行模板的安裝及頂板鋼筋的綁紮,在混凝土澆築車間,所有的生產線都調整成兩套底模托架台車同步移動,同條生產線上兩片梁同時澆築混凝土,同時進入養護車間養護,每16個小時每條生產線出梁2片。
同步推進、工序零接口:流水生產線按固定節拍進行循環。施工要特別防止某道工序對生產線造成擁堵,如果某一道工序未完成或者不合格,勢必影響整條生產線的運轉,所有的工序完成都必須準時化。工序組織者要合理安排工序銜接,工序完成後,及時牽引到下一車間進行後一道工序的施工,防止各工序之間停頓時間過長,牽引工作要有一定的提前量。同時組織下一道工序做好相關施工準備,保證流水線固定節拍的通暢運行生產,以防發生模板待立或鋼筋待綁現象。
物流的準確性:生產流水線的特點決定廠內生產流水線的物流作業必須服從和服務於制梁工藝流程的需要,所以生產流水線的物流具有很強的配合性、動態性、集散性和均衡性。如果生產流水線上物流存在問題,必然會影響整個生產流水線的效率。比如鋼筋的運輸,由於鋼筋運輸工人慣性思維的影響,認為“這次多送點,下次便可少送點”,卻未考慮生產流水線的節拍性和動態性,多送了鋼筋占用了模板存放位置,影響生產線的暢通,增加了生產線的負擔,少送了則導致鋼筋綁紮無法正常施工,必須要保證配送的準時化、準確。
鐵路T形簡支梁現場預製循環流水生產線施工工法作業崗位的固定化:工人固定區域作業,專業化程度要求高,每一車間工人均固定作業,為保證工序的準時化、準確率,要求車間工人具有較高的技能水平,如工人頻繁流動更換,勢必影響生產線運轉。
材料設備
- 材料
循環流水生產線預製T形梁所用的原材料與傳統制梁方式相同,均需滿足相關標準要求,《鐵路T型簡支梁現場預製循環流水生產線施工工法》的主要材料見下表。
序號 | 名稱 | 規格型號 | 主要技術指標 |
---|---|---|---|
1 | 混凝土 | C55、C50 | 抗凍F≥200 電通量≤1000庫侖 抗滲≥P20 膠凝材料耐腐蝕係數K≥1.0 |
2 | 鋼筋 | Q235、HRB335 | 《熱軋光圓鋼筋》GB1499.1-2007 《熱軋帶肋鋼筋》GB1499.2-2007 |
3 | 鋼絞線 | 1x7-15.2-1860 | 《預應力混凝土用鋼絞線》GB/T5224-2003 |
4 | 壓漿劑 | M50 | 《鐵路後張法預應力混凝土梁管道壓漿技術條件》TB/T3192-2008 |
5 | 防水卷材 | L1.5型 | 鐵道部科技基[2007]56號發布:《客運專線橋樑混凝土橋面防水層暫行技術條件(修訂稿)》 |
- 設備
《鐵路T型簡支梁現場預製循環流水生產線施工工法》的主要設備見下表。
序號 | 名稱 | 規格型號 | 數量 |
1 | 滾輪 | φ100毫米 自製 | 4500個 |
2 | 專用底模托架台車 | 34米長、自製 | 48台 |
3 | 提梁機 | QLM80/10+80-40A3 | 2台 |
4 | 牽引卷揚機 | 10噸 | 4台 |
5 | 回送卷揚機 | 2噸 | 4台 |
6 | 主牽引繩 | 400米、φ28毫米 | 4條 |
7 | 回送牽引繩 | 200米、φ12毫米 | 4條 |
8 | 液壓式張拉千斤頂 | YCW300B-150 | 10台 |
9 | 滑輪組 | 10噸 | 4套 |
10 | 靜載試驗架 | 32米 | 1套 |
參考資料:
質量控制
《鐵路T型簡支梁現場預製循環流水生產線施工工法》的質量控制要求有以下5點:
1、T梁預製各工序工藝嚴格按《預製後張法預應力混凝土鐵路橋T形簡支梁技術條件》TB/T3043-2005要求施工,並遵守相關鐵路混凝土施工質量驗收標準及耐久性規範。
2、軌道系統滾輪安裝時,要求同條生產線上所有滾輪頂面高程誤差小於1毫米。
3、生產前對原材料進行嚴格檢驗,採用經檢驗合格的原材料;模板採用整體定型鋼模,嚴格把好模板質量關,同時牽引前要檢查模板的緊固性。
4、按設計圖精確安放預埋件,同時設好保護層墊塊,保證位置和幾何尺寸準確無誤。
5、成品梁檢驗符合《預應力混凝土鐵路橋簡支梁靜載彎曲試驗方法及評定標準》TB/T2092-2003中相關的強度、剛度要求。
安全措施
根據《鐵路T型簡支梁現場預製循環流水生產線施工工法》,安全措施主要體現在大型設備使用、用電安全及防火等方面。該工法除嚴格遵循《建築機械使用安全技術規程》JGJ6-86、《施工現場臨時用電安全技術規範》JGJ6-88的規定要求執行外,還在安全管理、技術及現場應急處理等方面採取了如下措施:
1、針對模板、牽引、吊梁、移梁、預應力等重點工序,安排專職安全員旁站監督。
2、循環流水生產線採用大型車間化作業,對大型機械,特別是起重設備、拌合站等操作司機專人專機,持證上崗。
3、建立健全安全組織保證體系,落實安全責任考核制,把安全生產情況與每個人的經濟利益掛鈎,使安全生產處於良好狀態。
4、貫徹“安全第一,預防為主”的方針,堅持“安全為了生產,生產必須安全”的原則,做到思想保證、組織保證和技術保證,確保施工人身、設備的安全。
環保措施
《鐵路T型簡支梁現場預製循環流水生產線施工工法》的環保措施是:
1、採用循環流水生產線施工,生產區高度集成,節約了大量的土地。
2、及早施作防護工程、排水工程,防止水土流失;工程完工後,及時進行現場徹底清理,並按設計要求處理。
3、對有害物質(如燃料、廢料、垃圾等)要通過處理後運至指定地點,防止對人員造成損害。
4、臨時工程、配套車間等統一規劃,按施工環保的要求進行實施。嚴格在設計核准的用地界和經相關部門批准的臨時用地範圍內開展施工作業活動,用地使用完後必須恢復至原有的地形地貌或比原有更改善的狀況。
5、對於施工中廢棄的零碎配件,邊角料、水泥袋、包裝箱等設立清潔工班專門進行打掃,及時收集清理並搞好現場衛生,以保護自然環境與景觀不受破壞。
效益分析
經濟效益
《鐵路T型簡支梁現場預製循環流水生產線施工工法》的經濟效益是:初步測算,甘泉梁場共制梁4208片,按傳統的制梁模式需要支付工費7313萬元,循環流水生產線的制梁模式需支付工費用6450萬元,節約費用863萬元;循環流水生產線建場費用高,滾輪、底模托架台車等為固定資產周轉使用材料,該次梁場建場攤銷1390萬元,傳統模式建場費為1080萬元,相比多支出310萬元;在平移梁費用上,循環流水生產線模式相比傳統模式節約費用55.5萬元(已扣除機械攤銷增加費用);在養護費用上,循環流水生產線模式節約費用215萬元;綜合對比,採用工廠化循環流水線施工可累計節約資金823萬元,通過分析和比較可看出實行循環流水線預製T形簡支梁,經濟效益顯著。
節能效益
《鐵路T型簡支梁現場預製循環流水生產線施工工法》的節能效益是:循環流水生產線生產區及制梁工序高度集成,運輸距離短,倒置的輪軌式移動方式配合滑輪組牽引系統降低了牽引力,節約了動力,固定式恆溫養護車間,提高了養護棚的密封性,降低了熱能損失、水資源消耗,節能效益顯著。
註:施工費用以2009-2010年施工材料價格計算
套用實例
《鐵路T型簡支梁現場預製循環流水生產線施工工法》的套用實例如下:
工程概況
中鐵十二局集團甘泉制梁場承擔著包西鐵路通道(陝西段)BXS-2標段內95座橋,共4208片鐵路預應力混凝土T形簡支梁的預製任務,屬特大型現場制梁場,任務重、工期緊,為按期完成施工任務,為後續工程施工創造條件,根據其多年的制梁經驗,汲取高效率的生產流水化、工廠化理念,採用了循環流水生產線預製鐵路T形簡支梁的施工生產方案。
施工套用效果
2008年7月循環流水生產線建設完成並投入,預製的梁體內實外美,2008年10月22日順利通過鐵道部產品質量監督檢驗中心生產許可證實地核查認證,轉入批量生產階段,生產能力可達12片/日,截止2010年8月底,累計生產各類T梁4208片。在冬期施工、可以確保鋪架。
榮譽表彰
2010年,《鐵路T型簡支梁現場預製循環流水生產線施工工法》通過了山西省省級工法鑑定,被評為2009年度山西省省級工法,並被評為2009-2010年度鐵路建設工程部級工法與2009年度集團公司三級工法。
2011年9月,中華人民共和國住房和城鄉建設部發布《關於公布2009-2010年度國家級工法的通知》建質[2011]154號,《鐵路T型簡支梁現場預製循環流水生產線施工工法》被評定為2009-2010年度國家二級工法。