《鐵礦粉複合造塊工藝》是中南大學於2005年9月1日申請的專利,該專利的公布號為CN1924035,申請公布日為2007年3月7日,發明人是姜濤、李光輝、胡友明、張克誠、鄔捷鵬等。該發明屬於鋼鐵冶金領域。
《鐵礦粉複合造塊工藝》將細粒鐵精礦單獨分出製備成球團,再與粗粒的含鐵礦粉及其他原料混合後鋪到傳統燒結機上進行焙燒,製成由酸性球團礦嵌入高鹼度燒結礦而組成的複合煉鐵爐料。採用該發明,能充分、合理利用2005年9月之前的含鐵原料;克服了細粒精礦燒結過程中料層透氣性差、難以燒結的缺點;克服高爐在同時使用燒結礦和球團礦時所存在的爐料偏析的缺點;顯著降低燒結能耗、節約建廠投資。
2015年11月27日,《鐵礦粉複合造塊工藝》獲得第十七屆中國專利獎優秀獎。
基本介紹
- 中文名:鐵礦粉複合造塊工藝
- 申請人:中南大學
- 申請日:2005年9月1日
- 申請號:2005100320956
- 公布號:CN1924035
- 公布日:2007年3月7日
- 發明人:姜濤、李光輝、胡友明、張克誠、鄔捷鵬、黃柱成、范曉慧、朱德慶、張元波、許斌、郭宇峰、楊永斌、董海剛、劉牡丹、潘健、朱忠平、王海濤
- 地址:湖南省長沙市麓山南路1號
- 分類號:C22B1/16(2006.01)
- 代理機構:中南大學專利中心
- 代理人:龔燦凡
- 類別:發明專利
專利背景,發明內容,專利目的,技術方案,改善效果,附圖說明,權利要求,實施方式,榮譽表彰,
專利背景
截至2005年9月,隨著中國鋼鐵工業迅猛發展,對煉鐵原料數量和質量的要求也越來越高,高爐煉鐵使用人造塊礦(燒結礦和酸性球團礦)的比例已超過90%。2005年前煉鐵生產所用的燒結礦和球團礦是在不同的造塊設備上採用不同的工藝製備的,並分別送至高爐料倉,按比例配料後進入高爐冶煉。實踐表明:傳統的燒結法必須生產高鹼度燒結礦才能保證燒結礦強度以滿足高爐冶煉的要求,而且燒結法不適宜大規模處理細粒級鐵精礦;而酸性球團礦生產工藝對原料粒度及水分要求苛刻,將面臨資源緊缺的問題,同時需要建立獨立的球團廠,高溫設備投資大,並且新建球團廠還受到資源、廠地等條件的限制,因而使得從根本上解決高爐用酸性球團礦短缺的問題具有一定的困難。
此外,由於燒結礦、球團礦在高爐爐內的運動狀態不同,導致兩者在高爐內產生較大的偏析,影響高爐生產過程。
發明內容
專利目的
為合理、充分利用粉礦和細粒鐵精礦資源,解決中國高爐用酸性爐料供應不足以及高爐煉鐵使用燒結礦和球團礦存在的偏析問題,降低燒結能耗,節約建廠投資,實現高爐優質高產低能耗生產,特提出該發明。
技術方案
《鐵礦粉複合造塊工藝》將細粒鐵精礦單獨分出製備成球團,再與粗粒的含鐵礦粉及其他原料混合後鋪到傳統燒結機上進行焙燒,製成由酸性球團礦嵌入高鹼度燒結礦而組成的複合煉鐵爐料。
該發明首先將占所有含鐵原料百分比為30~60%的細粒鐵精礦加入粘結劑和燃料進行配料、混勻,粘結劑加入量占所有含鐵原料0~1.5%,燃料的加入量占所有含鐵原料0~1.5%,混合料在圓盤造球機上製成直徑為8~16毫米球團;將占所有含鐵原料百分比為70~40%的粉礦及其他含鐵原料與熔劑和燃料進行配料,熔劑加入量占所有含鐵原料5.5~4.0%,燃料加入量占所有含鐵原料5.0~3.5%,並按傳統燒結工藝進行一次、二次混合處理;然後將球 團與二次混合料混勻,於燒結機上進行布料、點火、燒結,經冷卻後整粒,得複合燒結塊礦。整粒後小於5毫米的粉礦作為返料。燒結料層高度為500~900毫米,點火負壓4~5千帕,點火時間0.75~1分鐘,燒結抽風負壓6~9千帕。
所述粘結劑為膨潤土或生石灰。所述燃料為焦粉或無煙煤粉。所述細粒鐵精礦是鐵礦經磨礦、分選所得產品,一般-200目含量大於40%,在該工藝中的用量占所有含鐵原料的30%~60%。所述鐵礦粉礦一般指粒度為0~8毫米未經磨礦、分選鐵礦原料,在該工藝中的用量占所有含鐵原料的70%~40%。2005年前中國國內外尚無鐵礦粉複合造塊的任何研究或生產的報導。
改善效果
《鐵礦粉複合造塊工藝》具有以下效果:
1)充分、合理利用2005年9月之前的含鐵原料
採用該發明,將原來燒結用的細粒精礦作為酸性球團生產原料,而將粉礦作為鹼性燒結礦基本原料,在一台燒結機上同時製備出由酸性球團礦和高鹼度燒結礦組成的複合人造塊礦,使不同類型鐵礦原料得到更加合理利用。
2)克服了細粒精礦燒結過程中料層透氣性差、難以燒結的缺點
採用該發明,將細粒鐵精礦配入適量粘結劑單獨造球,製備成生球後,再與其它由鐵粉礦、熔劑等構成的混和料充分混合,布料、點火、燒結,由生球和制粒粉料組成的燒結原料可大大改善燒結料層的透氣性,顯著提高垂直燒結速度和利用係數,克服了傳統燒結工藝中精礦制粒效果差導致燒結料層透氣性差的缺點。
3)克服高爐在同時使用燒結礦和球團礦時所存在的爐料偏析的缺點
採用該發明,使酸性球團礦“嵌入”高鹼度燒結礦基體中,形成一個整體,從根本上解決了由於兩者運動狀態不同時出現的偏析,最佳化了高爐操作。
4)顯著降低燒結能耗、節約建廠投資
採用該發明,使得採用超高料層燒結技術(800~900毫米)成為可能。由於料層透氣性的改善,有利於充分利用料層的自動蓄熱作用,降低燒結固體能耗。並且燒結生產率的大幅提高,也會相應降低燒結生產能耗。另外,該工藝在燒結機上同時製備高鹼度燒結礦和酸性球團礦,對無條件另建鏈篦機—迴轉窯氧化球團廠或豎爐球團廠的鋼鐵企業,可大大節省投資。
附圖說明
圖1:《鐵礦粉複合造塊工藝》的工藝流程示意圖。
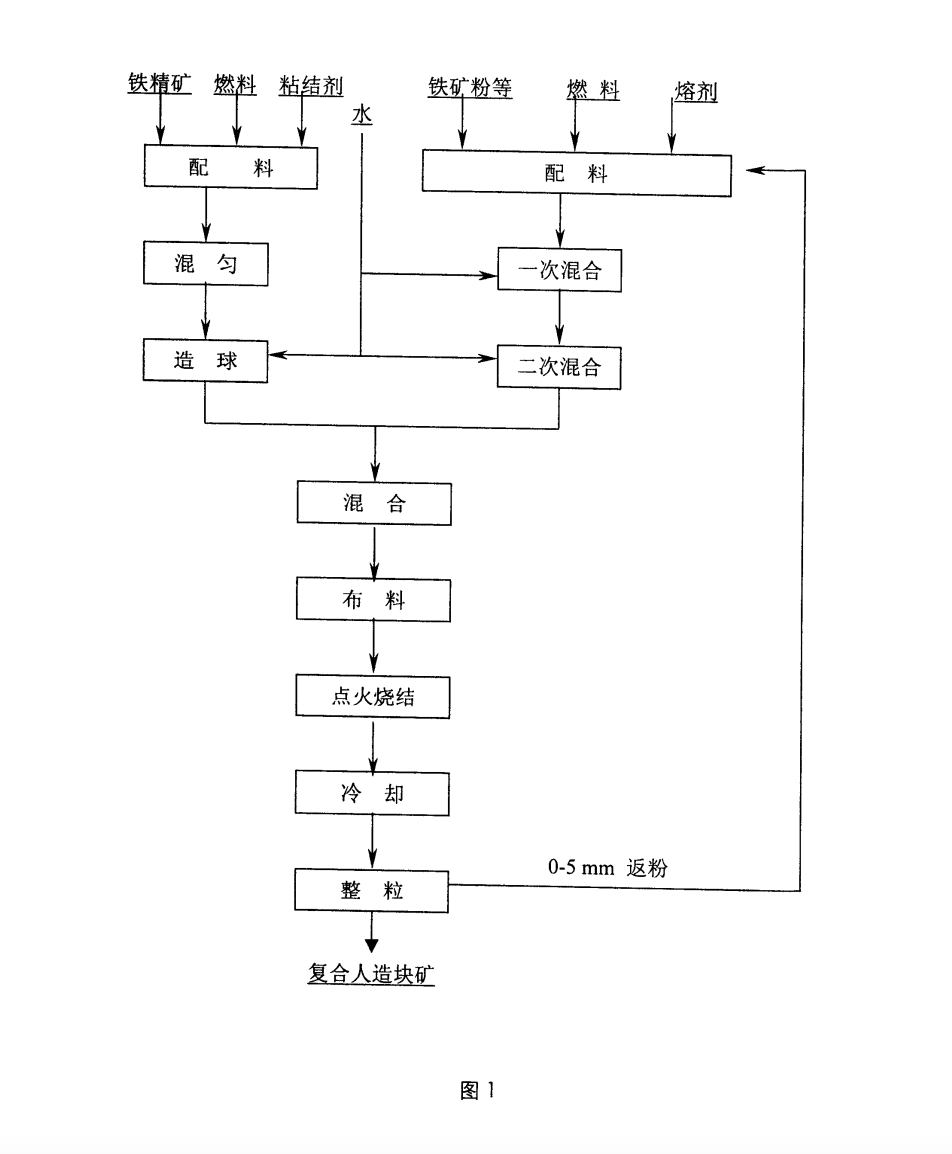
附圖說明
權利要求
1.《鐵礦粉複合造塊工藝》其特徵在於:將占所有含鐵原料百分比為30~60%的細粒鐵精礦加入粘結劑和燃料進行配料、混勻,混合料在圓盤造球機上製成直徑為8~16毫米球團;將占所有含鐵原料百分比為70~40%的粉礦及其他含鐵原料與熔劑和燃料進行配料,熔劑加入量占所有含鐵原料5.5~4.0%,燃料加入量占所有含鐵原料5.0~3.5%,並按傳統燒結工藝進行一次、二次混合處理;然後將球團與二次混合料混勻,於燒結機上進行布料、點火、燒結,經冷卻後整粒,得複合燒結塊礦,燒結料層高度為500~900毫米,點火負壓4~5千帕,點火時間0.75~1分鐘,燒結抽風負壓6~9千帕。
2.根據權利要求1所述的方法,其特徵在於:所述粘結劑為膨潤土或生石灰,其加入量占所有含鐵原料0~1.5%。
3.根據權利要求1所述的方法,其特徵在於:所述燃料為焦粉或無煙煤粉,其加入量占所有含鐵原料0~1.5%。
4.根據權利要求1所述的方法,其特徵在於:所述細粒鐵精礦一般指-0.074毫米含量大於40%的鐵礦原料;所述鐵礦粉礦一般指粒度為0~8毫米鐵礦原料。
實施方式
1.燒結混合料中細粒鐵精礦部分占35.5%,其中添加1.0%生石灰,不配加燃料,在圓盤造球機內進行單獨造球,鹼度保持0.6;混合料中粉礦部分占64.5%,其中配入5.0%焦粉和4.38%的生石灰,鹼度為3.2,進行一次和二次混合。控制混合料的總鹼度為2.25。將製備好的生球和二次混合料混勻,在燒結杯中布料,點火,燒結。燒結負壓為7千帕,料層高度700毫米。可獲得燒結礦的成品率為81.11%,轉鼓強度為63.52%,利用係數2.212t.m.h,垂直燒結速度22.57毫米/分鐘。
2.燒結混合料中細粒鐵精礦部分占30%,其中添加1.0%焦粉,不配加生石灰,鹼度為0.1,在圓盤造球機內進行單獨造球;混合料中粉礦部分占70%,其中配入4.0%焦粉和5.38%的生石灰,鹼度為3.4,進行一次和二次混合。控制物料的總鹼度為2.25。將製備好的生球和二次混合料混勻,在燒結杯中布料,點火,燒結。燒結負壓為8千帕,料層高度600毫米。可獲得燒結礦的成品率為80.16%,轉鼓強度為61.07%,利用係數2.083t.m.h,垂直燒結速度22.20毫米/分鐘。
3.燒結混合料中細粒鐵精礦部分占40%,添加1.0%膨潤土,鹼度為0.1,在圓盤造球機內進行單獨造球;混合料中粉礦部分占60%,其中配入5.0%焦粉和5.38%的生石灰,保持鹼度3.4,進行一次和二次混合。控制物料的總鹼度為2.25。將製備好的生球和二次混合料混勻,在燒結杯中布料,點火,燒結。燒結負壓為7千帕,料層高度750毫米。可獲得燒結礦的成品率為78.51%,轉鼓強度為62.21%,利用係數1.985t.m.h,垂直燒結速度21.79毫米/分鐘。
4.燒結混合料中細粒鐵精礦部分占50%,其中添加0.5%生石灰和0.5%膨潤土,不配加焦粉,鹼度為0.48,在圓盤造球機內進行單獨造球;混合料中粉礦部分占50%,其中配入4.7%焦粉和4.55%的生石灰,保持鹼度2.90,進行一次和二次混合。控制物料的總鹼度為2.0。將製備好的生球和二次混合料混勻,在燒結杯中布料,點火,燒結。燒結負壓為8千帕,料層高度850毫米。可獲得燒結礦的成品率為80.38%,轉鼓強度為62.67%,利用係數1.747t.m.h,垂直燒結速度18.35毫米/分鐘。
榮譽表彰
2015年11月27日,《鐵礦粉複合造塊工藝》獲得第十七屆中國專利獎優秀獎。