基本介紹
- 中文名:超薄太陽電池
- 外文名:ultra-thin solar cell
- 分類:太陽電池
- 材料:超薄單晶矽片
- 技術關鍵:矽片切割技術
- 優點:體積小,效率高,無輻射傷害
製造方法簡述
第一階段
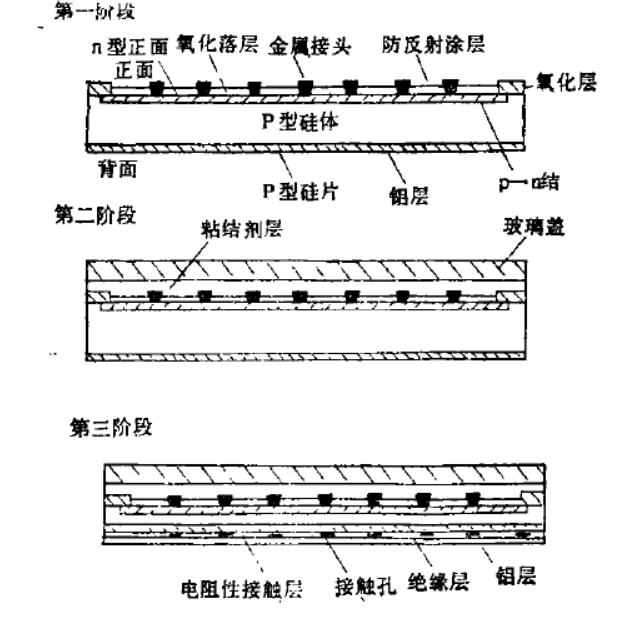
第二階段
第三階段
關鍵技術及工藝
矽片切割技術
自動化生產
電極製備
制絨及後清洗
第二,採用單面鹼制絨、酸制絨或乾法制絨等新工藝實現單面制絨。
超薄太陽電池是在超薄的單晶片上製造的太陽電池。由於這種太陽電池特別薄,在電池表面收集電荷時,電子和空穴幾乎沒有機會重新結合,因此,這種電池的效率比普通的太陽...
2008年1月3日專電 一種可“印”在鋁箔上的超薄太陽能電池日前在美國加利福尼亞州一家工廠的流水線上源源不斷地生產出來。這種可以大規模生產的太陽能電池被...
薄膜太陽能電池是緩解能源危機的新型光伏器件。薄膜太陽能電池可以使用在價格低廉的陶瓷、石墨、金屬片等不同材料當基板來製造,形成可產生電壓的薄膜厚度僅需數μm,...
太陽能電池又稱為“太陽能晶片”或“光電池”,是一種利用太陽光直接發電的光電半導體薄片。它只要被滿足一定照度條件的光照到,瞬間就可輸出電壓及在有迴路的情況下...
太陽薄膜電池有質量小、厚度極薄、可彎曲等優點。當前工業化製作太陽能薄膜電池的材料主要有:碲化鎘、銅銦鎵硒、非晶體矽、砷化鎵等。...
超薄太陽能板,是由奧地利大學研究員和東京大學研究員聯手進行,這種太陽能板是全球最薄、最輕的有機太陽能電池。其厚度僅有1.8-1.9微米(1微米為0.001毫米),僅...
CdTe與太陽光譜非常匹配,最適合於光電能量轉換,是一種良好的PV材料,具有很高的理論效率(28%),一直被光伏界看重,是技術上發展較快的一種薄膜電池。...
《薄膜太陽電池》是2018年科學出版社出版的圖書,作者是趙志強等。... 詳細討論了新型薄膜太陽電池的結構概念、工作原理、關鍵材料、基本工藝和前沿進展,並簡要地介紹...
柔性太陽能電池板是世界太陽能產業的新興技術產品,它是由樹脂包封的無定形矽作為主要光電元件層平鋪在柔性材料製成的底板上製成的太陽能電池板。特點是:可彎曲...
薄膜電池顧名思義就是將一層薄膜製備成太陽能電池,其用矽量極少,更容易降低成本,同時它既是一種高效能源產品,又是一種新型建築材料,更容易與建築完美結合。在...
《新型薄膜太陽能電池》是2018年12月化學工業出版社出版的圖書,作者是丁建寧。... 《新型薄膜太陽能電池》是2018年12月化學工業出版社出版的圖書,作者是丁建寧。
非晶矽太陽電池是指通過光電效應或者光化學效應把光能轉化成電能的裝置。1976年有出現的新型薄膜式太陽電池,基本組成成分是非晶矽化合物,又稱為a-Si太陽能電池和無...
紙制太陽能電池是以木材紙漿、銀質配線以及有機物組合而成,其製造成本僅為普通太陽能電池的10萬分之1,與玻璃制電池相比,具有可彎曲摺疊、更優越的加工性等特性,...
單晶矽太陽電池是當前開發得最快的一種太陽電池,它的構成和生產工藝已定型,產品已廣泛用於宇宙空間和地面設施。這種太陽電池以高純的單晶矽棒為原料,純度要求99.999...
柔性太陽能電池,是薄膜太陽能電池的一種,而且技術先進、性能優良、成本低廉、用途廣泛。可以套用 於太陽能背包、太陽能敞篷、太陽能手電筒、太陽能汽車、太陽能帆船...
太陽電池,指的是可以有效吸收太陽能,並將其轉化成電能的半導體部件。用半導體矽﹑硒等材料將太陽的光能變成電能的器件。具有可靠性高﹐壽命長﹐轉換效率高等優點﹐...
太陽能電池板(Solar panel)是通過吸收太陽光,將太陽輻射能通過光電效應或者光化學效應直接或間接轉換成電能的裝置,大部分太陽能電池板的主要材料為“矽”,但因製作...
標準太陽電池就是在其種類下,其光伏電池的各項參數符合國家規定的各項指標。標準太陽電池是專門標定過的太陽電池,它通過標準太陽光譜輻照度分布來測量輻照度或設定太陽...
碲化鎘薄膜太陽能電池簡稱CdTe電池,它是一種以p型CdTe和n型CdS的異質結為基礎的薄膜太陽能電池。...
太陽能電池片的生產工藝流程分為矽片檢測——表面制絨及酸洗——擴散制結——去磷矽玻璃——等離子刻蝕及酸洗——鍍減反射膜——絲網印刷——快速燒結等。具體介紹...
光電太陽能電池是通過光電效應或者光化學效應直接把光能轉化成電能的裝置。以光電效應工作的薄膜式太陽能電池為主流,而以光化學效應工作的實施太陽能電池則還處於萌芽...
《太陽電池材料》是2011年2月24日化學工業出版社出版的圖書,作者是楊德仁。... 《太陽電池材料》是2011年2月24日化學工業出版社出版的圖書,作者是楊德仁。
有機太陽能電池,顧名思義,就是由有機材料構成核心部分的太陽能電池。主要是以具有光敏性質的有機物作為半導體的材料,以光伏效應而產生電壓形成電流, 實現太陽能...
太陽電池的一種。 矽體太陽電池近年來得到了廣泛的套用 由於其製造工藝上的不同可分為單晶矽, 多晶矽兩種結構。多晶矽材料是由許多具有不同晶向的小顆粒單晶矽組成...
太陽能電池系列(也叫太陽能電池組件)是太陽能發電系統中的核心部分,也是太陽能發電系統中最重要的部分。其作用是將太陽能轉化為電能,或送往蓄電池中存儲起來,或...