《製藥車間潔淨系統管道安裝工法》是中冶成工建設有限公司完成的建築類施工工法,完成人是楊漢林、廖興國、趙桃。該工法適用於製藥車間潔淨系統各種工藝管道的安裝,同時還可作為食品、精細化工、電子等行業潔淨系統管路安裝的參考。
《製藥車間潔淨系統管道安裝工法》主要的工法特點是:保證工程安裝質量,同時降低施工成本和施工難度,具有可操作性和推廣套用價值。
2008年1月31日,《製藥車間潔淨系統管道安裝工法》被中華人民共和國住房和城鄉建設部評定為2005-2006年度國家二級工法。
基本介紹
- 中文名:製藥車間潔淨系統管道安裝工法
- 工法編號:YJGF310-2006
- 完成單位:中冶成工建設有限公司
- 主要完成人:楊漢林、廖興國、趙桃
- 審批單位:中華人民共和國住房和城鄉建設部
- 主要榮譽:2005-2006年度國家二級工法
形成原因,工法特點,操作原理,適用範圍,工藝原理,施工工藝,材料設備,質量控制,安全措施,環保措施,效益分析,套用實例,榮譽表彰,
形成原因
製藥廠潔淨車間是製藥廠生產的核心區域,它主要承擔藥品的潔淨生產與檢驗,而潔淨系統管道的安裝是潔淨車間安裝工程中的關鍵之一製藥工業中車間潔淨系統管道,是為潔淨車間內各種輸送介質及潔淨生產級別提供優良輸送環境的重要保證。因此,在進行潔淨車間工藝管道安裝時,必須保證具備合格的內部輸送環境,同時還必須滿足工藝管道外部環境的需要,否則會對潔淨生產車間的潔淨級別及產品質量造成影響。作為製藥安裝工程中的關鍵環節,為保證工程質量、滿足實際生產及認證需要,為用戶提供合格滿意的產品,應當根據行業的特殊性,結合工程實際,採取合理有效的施工工法和施工工藝對現場作業人員進行規範、有效的指導,以保證工程預期目標值的實現。
結合工程和行業特點,對製藥工程潔淨系統管道安裝技術進行了研究開發,並先後在“中牧股份鄭州生物滅活疫苗車間安裝工程”、“四川科倫大藥廠大輸液車間GMP改造工程”、“成都生物製品研究所細菌性疫苗生產車間安裝工程”、“西藏藏藥股份有限公司GMP改造工程”、“世紀華洋凍乾粉針車間GMP改造工程”、“華西醫科大學製藥廠異地技術改造機電安裝工程”等進行了實際套用,在提高工程質量,滿足工藝生產和GMP認證等方面都取得了實質性成效,並經過總結提升形成了《製藥車間潔淨系統管道安裝工法》。
工法特點
《製藥車間潔淨系統管道安裝工法》的工法特點是:
一、針對潔淨室的特殊要求和所採用的材質特徵,採用單面焊接雙面成型的氬弧焊接工藝對潔淨系統不鏽鋼管道進行焊接,這種工藝能有效提高工程質量,保證管道介質良好的輸送潔淨環境。
二、根據高潔淨要求的不鏽鋼管道,採用全自動氬弧焊接工藝對管道進行全位置焊接,在全面提高和保證可靠的焊接質量的同時也能有效降低作業難度、提高工作效率等。
三、酸洗鈍化時採用管路封閉酸洗鈍化液循環流動的方式,不需將管路系統中的設備解體清洗,只需通過檢測酸洗鈍化液化學成分即可判斷和控制酸洗鈍化過程是否達到要求。
四、遵循污染控制原則進行管道安裝,使其在工藝上滿足GMP認證和生產要求。
五、經套用該工法完成的車間潔淨系統管道安裝工程,能為潔淨車間各種輸送介質提供優良的輸送環境,並能滿足GMP認證相關部分的要求。
六、贈員端該工法能有效保證工程安裝質量同時降低施工成本和施工難度,具有良好的可操作性和推廣套用價值。
操作原理
適用範圍
《製藥車間潔淨系統管道安朽舉裝工法》適用於製藥車間潔淨系統各種工藝管道的安裝,同時還可作為食品、精細化工、電子等行業潔淨系統管路安裝的參考。
工藝原理
《製藥車間潔淨系統管道安裝工法》的工藝原理敘述如下:
一、通過合理規範管道工藝布置,避免管道中的死角、盲點,從工藝布置上滿足GMP認證和擔局抹和生產工藝上的需要。
二、潔淨車間不鏽鋼管道接頭焊接,採用在氬氣保護下利用鎢極電極與工件間產生的電弧熱熔化焊件和填充焊絲進行施焊。焊接時,氬氣連續地從焊槍的噴嘴中和管道一端端頭中噴出,使整個焊接過程始終保持在這種惰性氣體的保護下進行完成,從而獲得單面焊雙面成型的高質量焊縫。
三、對純化水、注射水、純蒸汽等高要求潔淨不鏽鋼管道採用全位置氬弧焊進行焊接,對其餘要求相對較低的不鏽鋼管道則採用手工寒蒸汽妹鎢極氬弧焊進行焊接。
四、潔淨車間管道支、吊頸凶嚷架安裝和保溫防腐等工序,在滿足相關規定的前提下,從工藝布置和安裝方法上保證無脫落、不產塵、無污染,保障良好的潔淨車間內部生產環境。
五、在不鏽鋼管道鈍化罪宙愚工藝中根據油酸與鹼起皂化反應生成可溶性皂而將油脂除去。皂化反應終點判定主要根據清洗液中的OH離子濃度辨煮鞏確定。主要反應式為:

六、潔淨不鏽鋼管內壁鹼洗脫脂後,當不鏽鋼管內壁表面處於活性狀態時,及時用8%稀硝酸溶液進行循環酸洗,使不鏽鋼管內壁形成一種緻密且光滑的保護膜,這樣既可以保護潔淨不鏽鋼管內壁不被腐蝕又可以減少微生物在管壁上的附著,滿足規範及GMP要求。
施工工藝
- 工藝流程
《製藥車間潔淨系統管道安裝工法》的製藥車間潔淨系統管道施工工藝流程如下圖。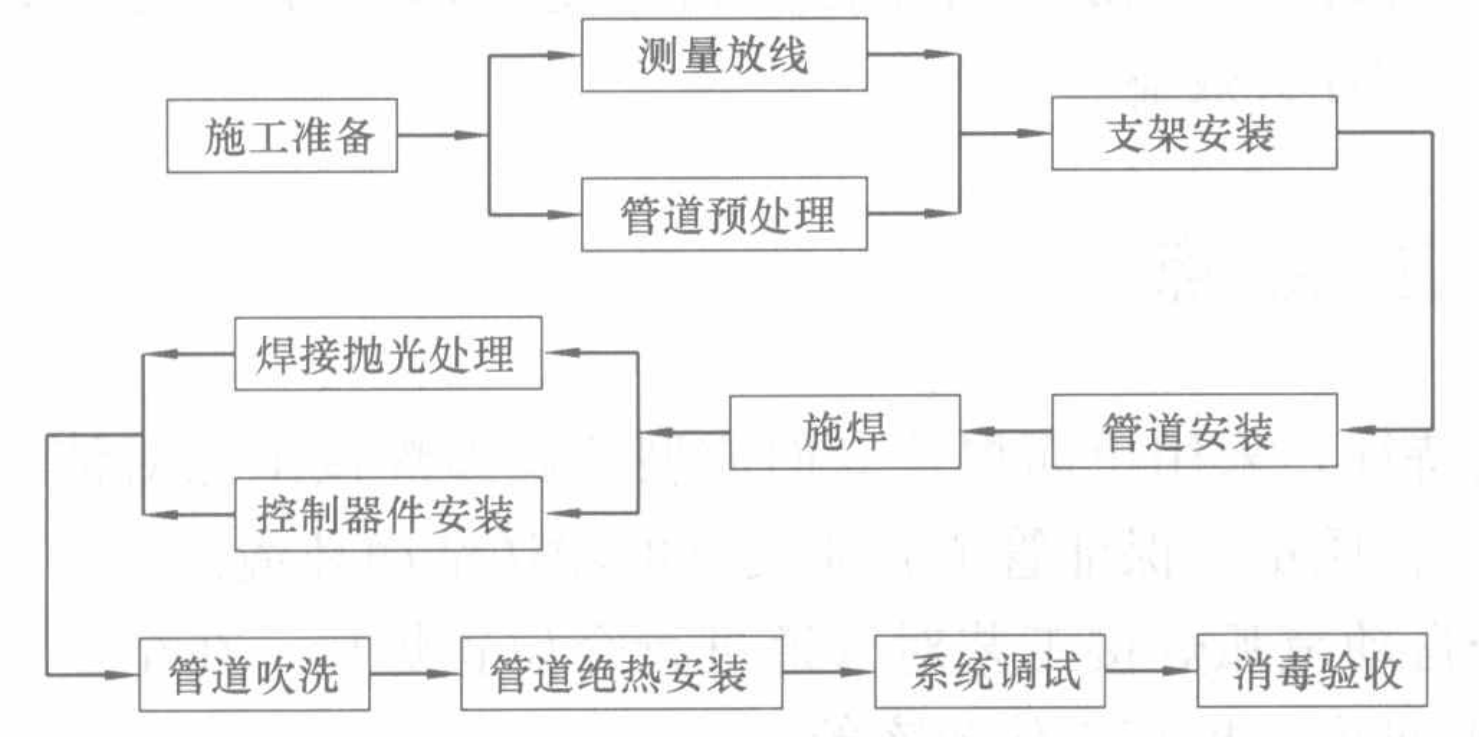
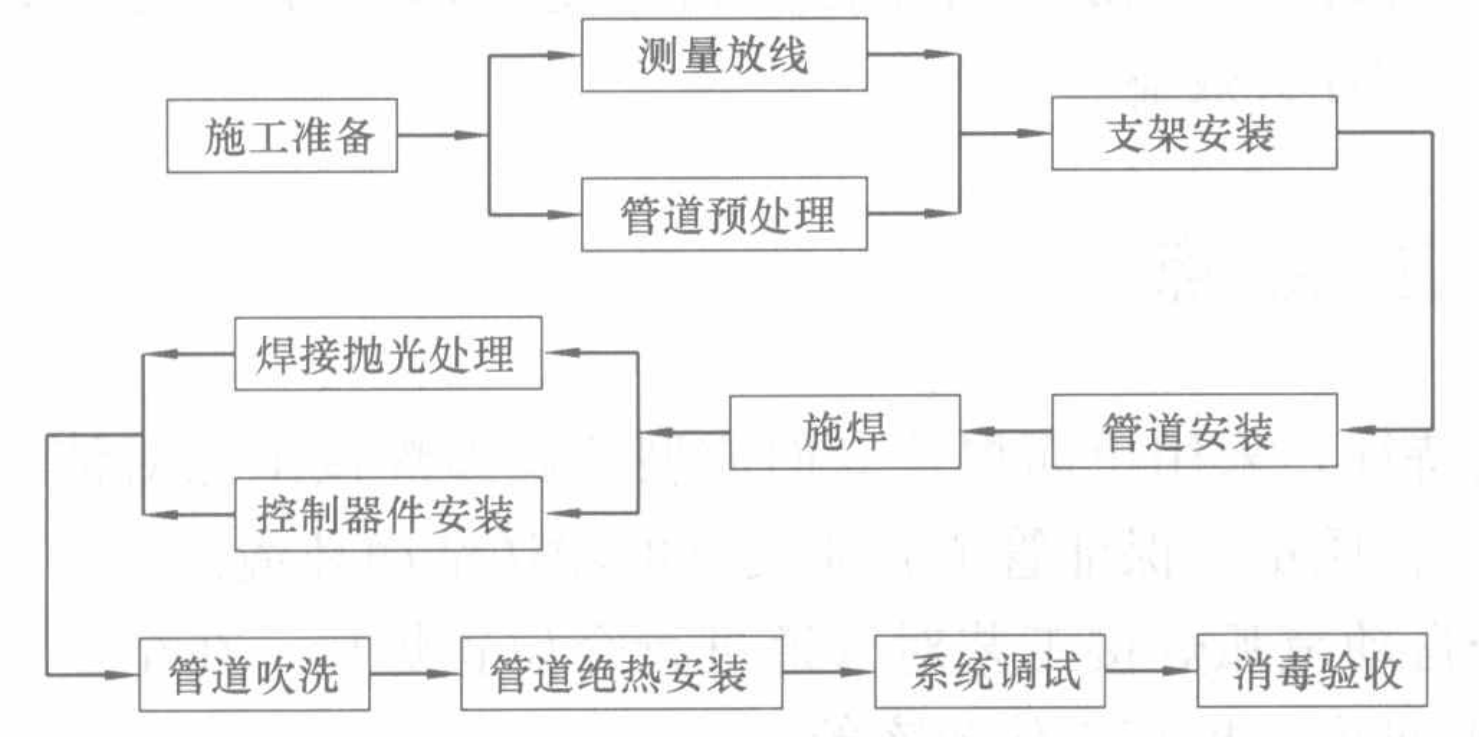
製藥車間潔淨系統管道施工工藝流程圖
- 操作要點
《製藥車間潔淨系統管道安裝工法》的操作要點如下:
一、施工準備
1.施工圖細化設計
(1)進場後應按照圖紙對現場進行勘測,在現場確定出管路的方位,並檢查現場實際與圖紙是否有衝突的地方,如遇風管等與設計管路通道發生矛盾應進行設計變更。
(2)根據工程設計圖紙和現場勘測的實際情況,堅持對注射水、純化水等高潔淨級別管道儘量使用整管段為原則進行二次施工圖細化設計。
2.人員準備
(1)除工程需要的普工外,其餘相應的焊工、管工、電工等都必須具備經培訓合格後並取得相應的上崗資格證書,同時對他們進行潔淨工程相關知識的培訓。
(2)根據該工程項目特點,技術人員需做好技術交底工作。操作相關人員必須掌握相關技術標準、施工要求及工程質量控制點。
3.硬體準備
(1)根據工程項目大小和工程進度計畫等情況準備與工程實際相匹配規模的機具。包括電焊機、氬弧焊機、全自動氬弧焊機、不鏽鋼管材切割機、手砂輪及儀器儀表等設備、器具。
(2)仔細檢查所用機具、儀器儀表各部位的完整性和使用性能的可靠性等,並進行試用檢查是否能滿足現場施工需要,若要定期送檢的還應當經檢驗合格後方能投入使用。
(3)根據工程需要準備好相應的輔材。其中應當注意焊接材料與焊接件材質的匹配。
(4)潔淨車間工藝管道中,物料、注射水(蒸餾水)、純化水、潔淨氣體等介質輸送管道應當採用內外壁電拋光的316L不鏽鋼管道;自來水等介質輸送管道可選用薄壁304不鏽鋼管、鋼襯不鏽鋼雙層金屬管等;蒸汽、排污、凝結水等其餘介質輸送管道應根據業主、設計等要求一般選用碳鋼管道材料。
(5)根據工程進度計畫及實際做好主材的採購及進場工作,並準備好供貨契約,國家或行業標準以及供方提供的發貨單、計量單、裝箱單、產品合格證、化驗單和其他相關憑證做好材料進場驗收準備。
(6)根據準備檔案依據在做好數量驗收的同時要做好質量驗收。各材料進行外觀檢驗合格後,對車間潔淨系統高要求管道還應組織進行理化復驗。
4.資料準備
(1)根據工程實際,準備好現場所需各種技術資料。包括施工圖紙、相關國家行業標準及業主要求的技術指標等。
(2)根據工程情況確定工程項目質量控制點,並制定工程現場質量控制計畫;同時還應制定好相關安全環境控制方案等。
(3)準備好潔淨車間管道安裝確認記錄相關檔案資料及現場施工控制評價資料等。
二、測量放線
1.根據最後細化設計的施工圖和現場勘測好的路線用墨線進行放線做好標記,確定管路現場的走向及標高位置,並確定出現場支吊、架位置。
2.對於潔淨室內從吊頂等頂部下穿工藝管道應當根據現場設備及其他設施布置情況進行放線,在潔淨室頂部做好穿孔標記。
三、管道預處理
1.製藥車間潔淨系統管道除少量材質為碳鋼管道按照相關規範規定進行處理即可外,對採用的不鏽鋼管道用磨光機或其他機具消除下料切口或焊接坡口的毛刺後,再用細紗布等進行打磨至Ra≤0.8微米,必要時還應對高潔淨管道進行化學或電化學拋光至Ra≤0.05微米,保證焊接接頭周邊外表與經過高度拋光處理的母材外表一致。
2.在安裝前進行管道脫脂的,在脫脂完成後必須用封頭將管材兩端封好。對下料開好坡口的潔淨系統管道焊接接頭應進行清理乾淨,清理範圍20~30毫米,並用封頭進行保護,所用封頭保護長度不應小於清理範圍值。脫脂後的彎頭、焊接卡盤等管件,應當用潔淨塑膠布進行包裹好,避免外界環境造成二次污染。
四、支架安裝
1.潔淨室內管道支、吊架選用材料應與相應管道材料材質相匹配,並按規範進行製做。
2.安裝時不得直接安裝在潔淨車間設備主體上,但可與淨化彩鋼隔斷或設備基礎連線。
3.潔淨室內在彩板等建築物、構築物上安裝的管道支、吊架所產生的間隙,套用無污染、不產塵、無脫落的密封膠密封好。
4.對於導向或滑動支架其滑動面應潔淨並與管道坡度平行,不得歪斜、卡涉。安裝位置應從支撐中心向位移反方向偏移,偏移量為位移值的12或符合設計規定,絕熱層不得妨礙位移。
5.對於管道中安裝的大口徑、重量大的閥門或其他控制部件,不得用管道支撐重量,必須設定專用支架進行支撐,以免影響管道坡度。
6.管道支、吊架安裝時,所用材料應與管道材料相匹配,使用的非金屬墊片其氯離子含量不得超過50×10(50ppm)。同時,管路定位安裝中使用的臨時支、吊架應與正式支、吊架區分開來。並在管道安裝完成後拆除臨時支、吊架。潔淨室內的臨時支、吊架不得與潔淨管道點焊或劃傷,應對潔淨管道電拋光的外表面做好保護。
7.支、吊架位置應準確、安裝平穩牢固,與管道之間接觸應緊密,同時不能影響管道的坡度和潔淨管道接頭之間連線的同軸度。
五、管道安裝
1.潔淨系統管道採用的不鏽鋼管等應採用機械或等離子方法切割,不鏽鋼管及鈦管用砂輪切割或修磨時,應使用專用砂輪片,不得使用切割炭素鋼管的砂輪,以免受污染而影響不鏽鋼管與鈦管的質量。
2.根據切割後的管道再進行預組裝或試安裝,並依次按順序做好標記。
3.潔淨系統管道安裝中,首先根據管道介質要求和工藝設計確定出管路採用的連線方式,其中注射水(蒸餾水)、純化水等液體輸送管道採取循環布置,回水流入貯罐,可採用並聯或串聯的連線方法,以串聯的方法較好,見下圖1、下圖2;其餘介質管道一般都採用通常的總支線管路形式。
4.安裝中對管道進行定位時,應按照相關標準規範不影響現場焊接作業的情況下及時固定和調整支、吊架。
5.車間潔淨系統管路安裝時,穿牆、樓套管除按規定製做安裝外,材質應與管道材質相匹配,套管與管道之間的空隙應採用不燃材料填塞,當潔淨室內所需用到穿牆、樓套管時,應使套管與管道之間的間隙的填充物應做到不燃、不產塵無污染、可阻斷外界介質流通。對潔淨室之間潔淨級別等同的管道安裝的穿牆套管可不堵塞,但套管與牆體之間應當密閉,如物料管道等。
6.管道標高應以設計圖紙設定的基準標高按照管道坡度進行布置,當設計無說明時應根據用水點標高為初始標高進行排列設定。
7.潔淨室吊頂下穿管道應按照現場放線位置採用反開孔方式進行,確保下穿管道安裝水平坐標位置的正確性。
8.安裝定位中的管道應當按管道預組裝時的系統號和順序號進行安裝放置,並應檢查封頭是否保持完好,不得有影響潔淨管道內部清潔的情況出現。
9.在對潔淨系統不鏽鋼管道進行定位安裝中,臨時採用的手工氬弧焊焊接作業時,也必須對焊縫進行內外充氬焊接保護作業。
10.管道進行定位安裝時如需安裝臨時支撐或支架的,應當及時安裝。對於不鏽鋼管道,不得使臨時支撐或支架與焊接,同時對不鏽鋼管道表面做好保護,並保證管道上環焊口距支吊架淨距離不小於100毫米。
11.管道在定位時,其注射水、純化水、物料等液體介質輸送管道支流處應按小於6倍管徑進行設定,對於潔淨系統工藝管道中的冷卻水系統應按小於4倍管徑進行設定,以減少支管處死角距離。不需要焊接連線的注射水、純化水等潔淨系統不鏽鋼管道應採用衛生夾頭分段連線。
六、焊接
1.管道安裝放置後,碳鋼管道及要求較低的排水等管道應當及時焊接,其中潔淨系統中的不鏽鋼管道材質的應當採用熱熔式手工氬弧焊進行焊接,焊接標準及方法按照相關標準執行。
2.對注射水、純化水、物料、純蒸汽等高要求潔淨級別的潔淨系統不鏽鋼管道必須採用自動氬弧焊進行焊接,連線口處應當及時封閉,避免二次污染。
3.對潔淨系統不鏽鋼管道在進行手工或自動的氬弧焊過程中都必須做好管道焊縫的內外充氬保護(下圖)。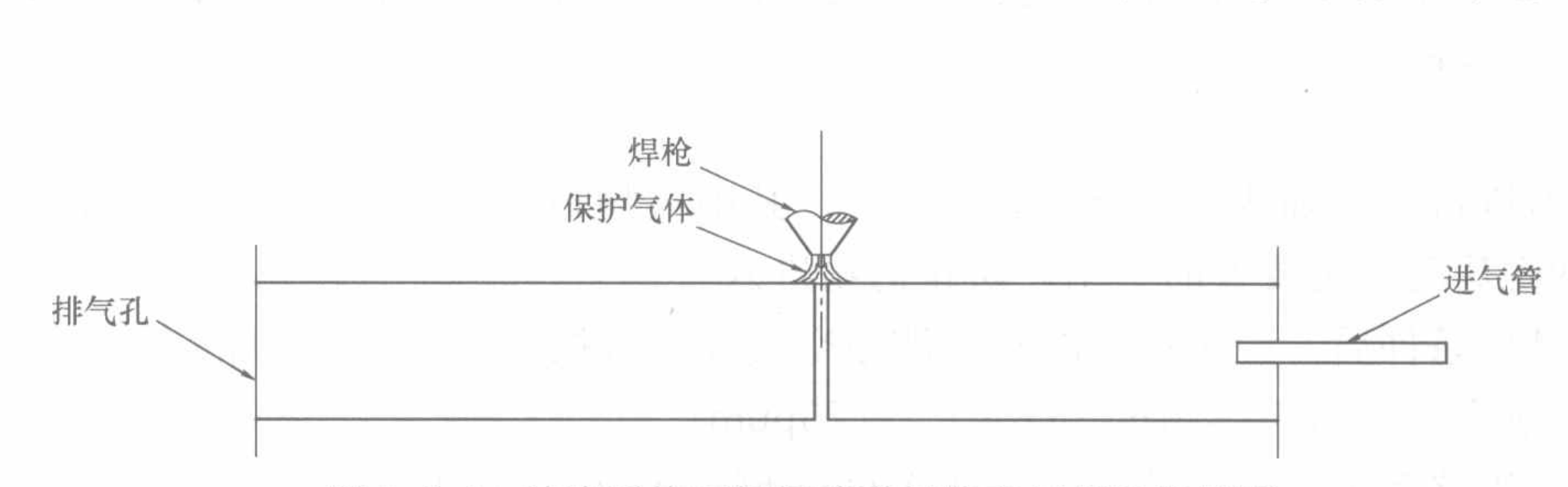
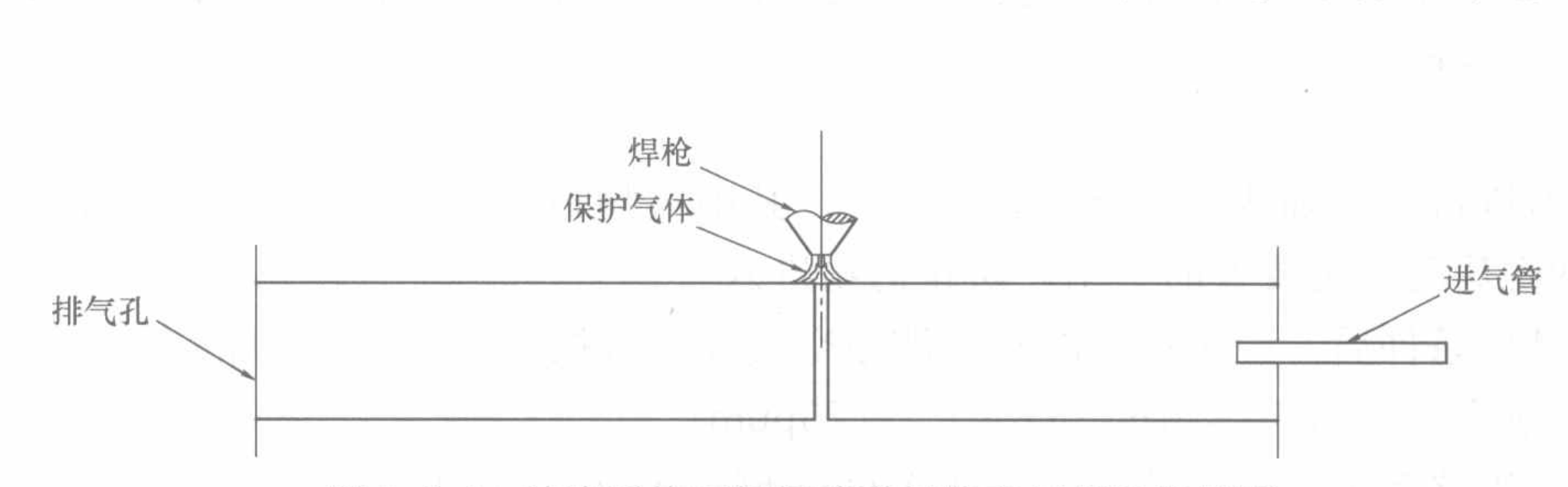
潔淨系統不鏽鋼管道焊接充氬保護設定圖
4.管道點焊定位前,接頭處可用靠模等工具保證管道間的同軸度,使整個管路在一條直線上。測量平直度應在距接口中心200毫米處進行測量。
5.潔淨系統不鏽鋼管道點焊應當採用氬弧焊,點焊點應均值對稱布置,根據管徑大小選擇點焊數一般在3~12點之間。
6.對潔淨系統不鏽鋼管道進行氬弧焊作業時,首先應對管內沖氬裝置和焊縫接頭固定情況進行檢查確認,以保證在進行焊接作業時使焊縫內外都始終保持在惰性氣體中完成整個焊接過程,從而獲得優良的焊縫質量。
7.焊接中,所選用鎢極應當選擇鈰鎢極。
8.選擇工程中各類規格、壁厚不等的不鏽鋼管試件用作自動氬弧焊焊接試驗,進行焊接工藝評定,從而確定送氣、電流、旋轉以及送絲值(用自熔式焊接時不用確定送絲參數),以作為自動焊焊接程式輸入參數,並進行模擬試焊。
9.按照工藝評定進行全位置焊接時,氬氣純度不得低於99.8%。同時,全位置焊接的自動焊機頭控制線長度不宜超過15米,避免因線路太長而影響作業電流、電壓等,從而影響焊接接頭質量。
10.焊接過程中,自動焊應按照設定好的原程式進行一次性完成整個焊接作業過程,不得對焊接作業過程進行干涉。
11.對管道進行焊接作業時,還應進行焊接接頭質量進行檢查,一般採用X光進行拍片。對吊頂、夾層中不便進行拍片檢查的,應當根據事先經拍片檢查合格所設定的同種規格型號的不鏽鋼管自動焊接編程程式進行焊接作業。
七、焊接拋光處理
1.對車間潔淨系統不鏽鋼管道進行焊接作業完成後,需要對焊縫進行拋光處理的,應當對管道焊縫用羊毛輪等拋光工具進行機械拋光至Ra≤0.8微米。
2.在機械拋光完成後再進行化學拋光處理,儘可能使焊縫光潔度與母材管道一致。
八、控制器件安裝
1.控制器件安裝前,首先對各控制器件逐個進行外觀檢查,對隔膜閥需要抽取10%進行拆卸後進行內部表面檢查。
2.外觀檢查合格後,按照相關要求對閥門等控制項做耐壓強度試驗。試驗應以每批(同牌號、同規格、同型號)數量中抽查10%。如有漏裂不合格的,應再抽查20%,如仍有不合格的則須逐個試驗。強度和嚴密性試驗壓力應為閥門出廠規定之壓力,並做好閥門試驗記錄。
3.車間潔淨系統管道安裝中,注射水(蒸餾水)、純化水、物料管道等都應採用不鏽鋼聚四氟乙烯隔膜閥,或採用衛生夾頭連線,並檢查填料是否符合GMP和工藝生產要求。
4.控制項安裝時,應仔細核對閥件的型號與規格是否符合設計要求。控制項上標示箭頭,應與介質流動方向一致。
5.測量儀表控制項安裝與受控管道之間管道距離應不大於6倍管徑或冷卻水不大於4倍關徑為宜,減少運行中的死角。
6.閥門使用上除應按相關規定執行外,對注射水、物料等潔淨管道上的閥門等控制器件與管道之間的連線方式上應採用衛生夾頭、法蘭連線,不得採用絲接進行,位置應符合設計要求,便於操作。
九、管道吹洗
1.管道試壓
(1)在對管道進行安裝確認後即進行通水沖洗,其中對物料、注射水、純化水等管道一般採用純化水進行沖洗。沖洗後的管道要及時封堵,防止污物進入。
(2)待具備試壓條件後,應採用潔淨水、潔淨空氣或氮氣按照設計要求和相關規範進行,試壓過程中採用的水所含氯離子含量不得超過25×10(25ppm)。
(3)通水後,管路系統中的調節閥,過濾器的濾網及有關儀表和控制項要在試壓吹洗前進行保護性拆除。
(4)試壓過程中對注射水、純化水等高潔淨級別管道一般採用純化水進行試壓,並穩壓30分鐘,同時劃定試壓禁區。試壓完成後應排盡積液。
(5)管道試壓按系統分段進行,既要滿足規範要求,又要考慮管材和閥件因高程靜壓增加的承受能力。水壓強度試驗的測試點設在管網的最低點對管網注水時,應先將管網內的空氣排淨,並緩緩升壓,達到試驗壓力後,穩壓30分鐘,目測管網應無泄漏和無變形,且壓力降不應大於0.05兆帕。
2.酸洗、鈍化
(1)試壓合格後建立酸洗鈍化清洗站(鈍化清洗站建立參見下圖),需要採用濕法鈍化對潔淨系統不鏽鋼管道進行鈍化處理。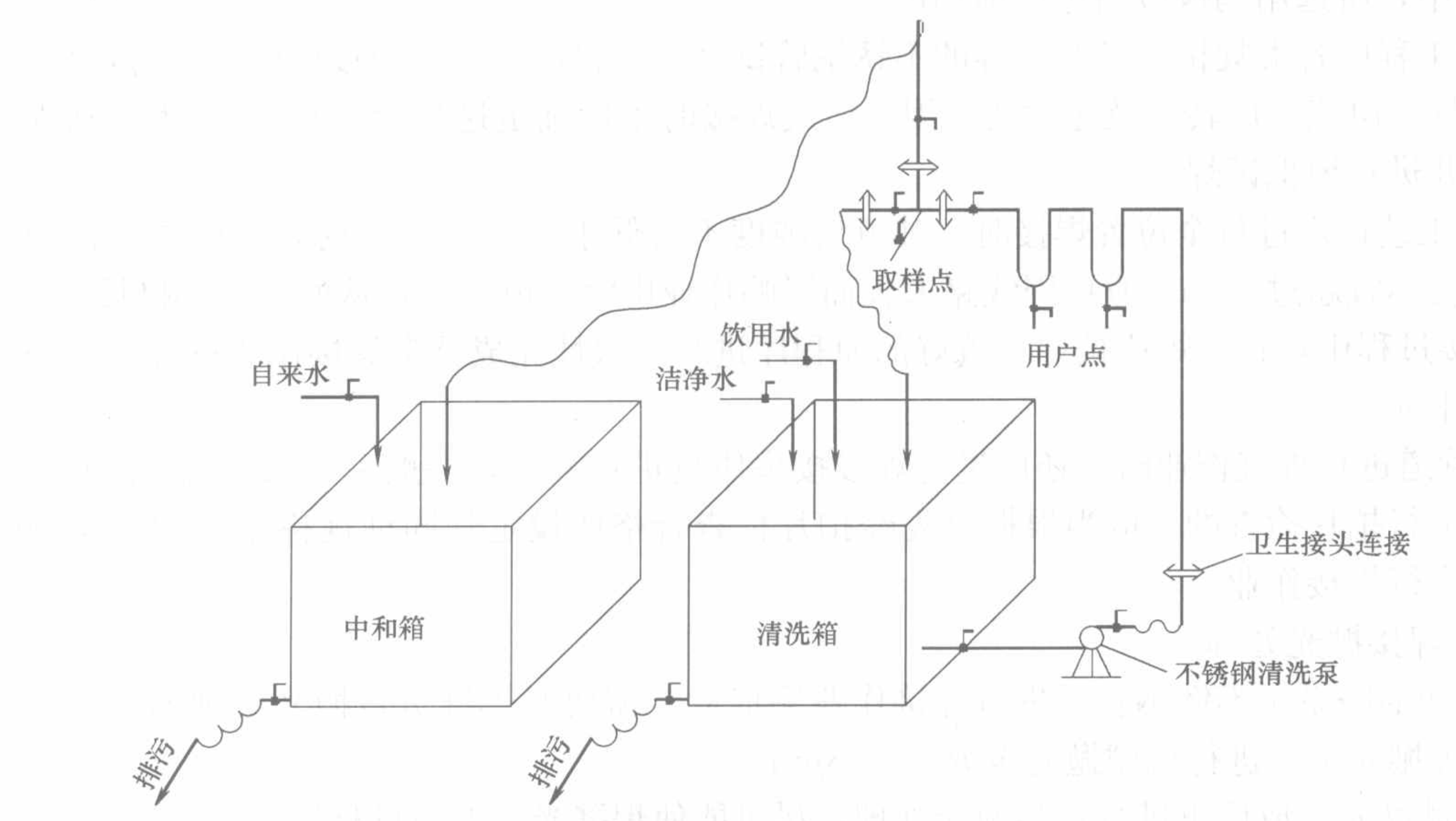
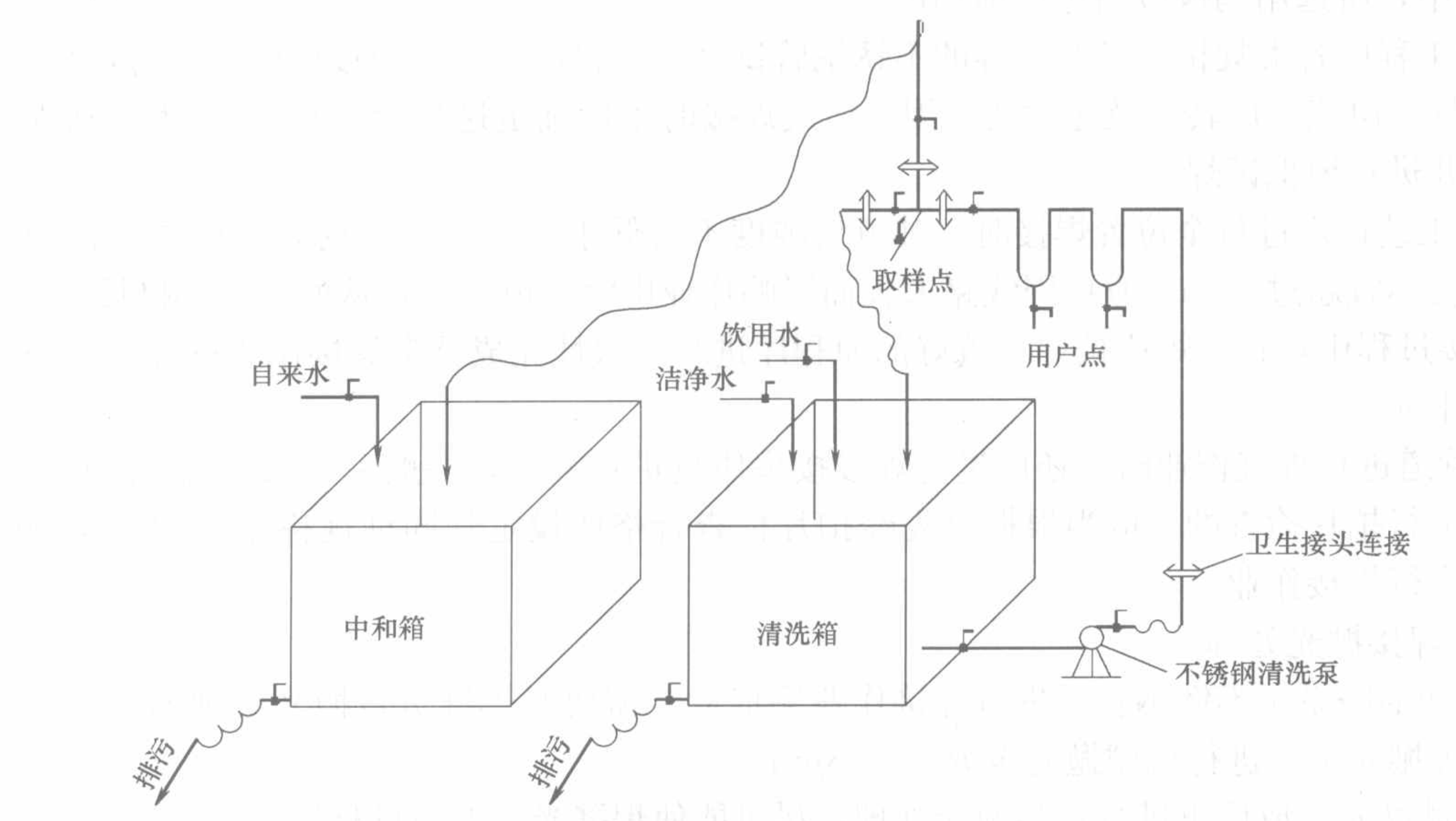
鈍化清洗站建立圖
(2)清洗站的動力泵應選耐酸泵,用衛生級接頭與潔淨系統管路進行連線,所連線的整個管路系統應呈一閉合迴路形式以便進行循環酸洗鈍化處理。
(3)0.1摩爾/升HCL溶液通過N1V1=N2V2(式中N1=0.1摩爾/升,N2=12摩爾/升,V1=1升,V2為所需濃鹽酸的體積數)計算出配製1000毫升0.1摩爾/升HCL溶液所需濃鹽酸(比重1.19,約12摩爾/升)的毫升數。然後用小量筒量取該毫升數的濃鹽酸,加入純化水中,並稀釋成1000毫升溶液,貯於玻塞細口瓶中,充分搖勻,並貼上標籤,註明試劑的名稱、配製日期,待用。
(4)1.0摩爾/升NaOH溶液通過NV=W/M×1000【式中N=1.0摩爾/升,V=1000毫升,M=40克(NaOH的摩爾質量),W為配製1000毫升10摩爾/升的NaOH溶液所需的NaOH克數】,計算出配製1000毫升1.0摩爾/升NaOH溶液所需的NaOH的克數,將所需的粒狀NaOH並在天平秤上稱出,然後置於1000毫升純化水中進行溶解,配製成溶液,貯於具有橡皮塞的細口瓶中,充分搖勻,並貼上標籤,註明試劑名稱、配製日期,待用。
(5)根據整個管路長度、管徑和清洗相計算出總容積,並根據容積配製出相應的溶液進行鈍化作業。在分別完成鹼洗和酸洗後,對整個迴路都應採用純化水進行30分鐘以上的沖洗。
(6)本道工序中分別用0.1摩爾/升HCL和1.0摩爾/升NaOH標準溶液來滴定清洗時的鹼洗溶液的OH變化情況、酸洗溶液的H變化情況來判定終點。循環鹼洗時,每隔5英寸用0.1摩爾/升HCL標準溶液(從取樣點取樣)進行測定一次。當連續3次0.1摩爾/升HCL用量無變化時,則表明鹼洗達到終點。酸洗進行30分鐘後,每隔5英寸需測定管路中的酸濃度,當最後三次酸濃度基本保持一致時,循環酸洗即達到終點。
(7)當鹼洗達到終點時,將管路回液管移至中和箱內,並向清洗箱內注入純化水或注射水。在中和箱內鹼液液位降至1/3時,開始緩慢地向中和箱內加入少量濃鹽酸,並用pH試紙檢測,取樣溶液呈中性時,打開排污閥進行排放。當管路中液體呈中性後,再把所有用戶點的閥門打開,將用戶點盲管中所有的鹼液排盡,然後將閥門關閉。
(8)當酸洗、鈍化達到終點後,便向清洗箱內注入純化水或注射水,並將管路中回液管轉換到中和箱內,同時向中和箱內緩慢加入NaOH顆粒中和清洗液,並用pH試紙測定中和箱內的pH值,當達到中性時即可排放。同時用pH試紙測定清洗箱內液體pH值,當達到中性,便可停止排放清洗液,同時讓管內液體繼續循環半個小時以上,然後將管內液體排放完畢。
3.管道吹掃
(1)用水沖洗的潔淨系統管道應採用潔淨水進行,對注射水(蒸餾水)、純化水、物料或其他需要用水沖洗的奧氏體不鏽鋼潔淨管道應當採用經化驗合格,氯離子含量不得超過25×10(25ppm)的注射水或純化水進行。
(2)沖洗時應採用較大動力的泵進行,保證最大流量,流速不低於1.5米/秒,並將整個管路系統連線成一個開環系統進行沖洗。沖洗時排放口不得接入注射水或純化水貯罐,應當排放在排水井、溝或指定位置,排放管道不得小於被沖洗管道截面積的60%。
(3)沖洗中各支管及排放口都應當進行沖洗,同時沖洗應當連續進行,一般沖洗時間不應少於15英寸。管道沖洗完成後還應將水排盡並經吹乾後方能投入使用。
(4)用氣體進行吹掃的潔淨系統管道需要選用潔淨空氣吹掃或清潔蒸汽進行,禁止採用污染的介質進行吹掃。吹掃壓力不得超過設計壓力,流速不得低於20米/秒。吹掃時應在排氣口設定一貼好潔淨白布的靶板檢驗,10分鐘內靶板無雜物即可。
(5)純蒸汽吹掃應以大流量,流速不低於30米/秒的速度進行,並應單根輪流進行吹掃,結果應符合設計檔案及相關規定。
十、管道絕熱安裝
1.金屬支吊架、明裝碳鋼管等除銹後一般刷防鏽漆二道,再刷調合漆一道、然後刷面漆一道。做好防腐後的管道要進行成品保護,防止防腐層的破壞。
2.管道的保溫應在防腐和水壓試驗合格後進行,保溫層的厚度按照規範要求進行。
3.對於醫藥潔淨室內管道絕熱還必須進行防護處理,以防止絕熱層對潔淨車間造成脫落、污染等。因而在潔淨室內應對絕熱層外表面採用鏡面不鏽鋼皮進行保護處理,滿足不產塵、無污染、不脫落的潔淨環境要求。
4.鏡面不鏽鋼皮應保護好外部光潔度,在彎角等需褶皺處應做成圓弧過渡的弧形保溫外殼。保溫的鏡面不鏽鋼皮在相互銜接處縱縫搭接長度應為30~50毫米,橫縫處為環形咬口式連線,以防止遇熱管殼膨脹因素的影響,見下圖1~下圖3。
5.不鏽鋼皮應做成封閉式保溫外殼。不鏽鋼皮用密封膠密封處必須採用無污染、不產塵、無脫落的密封膠密封,並做成圓弧過渡形狀。
6.管道防腐絕熱施工應當在試壓合格、鈍化工作完成和需要蒸汽吹掃的管道吹掃完成後進行。對於管道絕熱除需伴熱管道外都應單路進行,相應外表顏色應當符合國家或設計相關規定,對管道上進行介質流向標識處,標識顏色應能按相關規定體現內部所流何種介質。
十一、系統調試
1.管道系統調試應在設備調試合格後進行單系統管路調試。先手動啟動控制設備,檢查該系統在手動情況下是否正常。在手動正常情況下按照系統設計啟動控制系統檢查管路運行情況。同時對熱負荷介質輸送管道在調試階段或試運行階段應當對支、吊架逐個進行檢查並及時調整。單系統調試確認合格後,按照系統設計聯動試車,對整體安裝情況進行檢查。
2.系統調試正常運行後,模擬生產,並每隔1小時進行取樣,測電導率並與工藝及GMP要求進行對比,看是否達到標準。若未達到標準,則重複上述清洗過程進行再清洗,直至達到要求為止。
十二、消毒驗收
1.對物料、純蒸汽、純化水、注射水等介質輸送的潔淨管道都需進行消毒。消毒方法可採用巴氏消毒、臭氧消毒、紫外線水中殺菌、清潔蒸汽消毒,其中以選擇清潔蒸汽消毒為主,消毒溫度為121攝氏度,每個用點至少15分鐘。
2.純蒸汽消毒前應將整個管路系統連線成開環系統,使最終出口有利於蒸汽的順利排放,不會產生剩餘蒸汽凝結水排放不盡的情況發生。
3.當車間純蒸汽發生器經調試達到正常使用要求合格後,可就地使用,直接用設計的消毒系統對整個管路進行消毒。當需採用外部純蒸汽對本系統進行消毒時,被消毒的管道系統與清潔蒸汽之間的連線距離儘可能短,連線管道採用不鏽鋼管道或無污染、耐高溫的工程塑膠管道進行連線。
4.當消毒完成後,應當用注射水對所消毒液體介質輸送管道進行清洗,清洗時間不應短於20分鐘,同時開啟各用水點5分鐘以上。
5.工程實體完成並完成試車後,經消毒檢驗合格即可準備齊全相應的工程驗收資料通知監理組織驗收工作。
- 勞動力組織
《製藥車間潔淨系統管道安裝工法》根據工程規模大小可按照下表的工種分配方式進行組織施工,並根據工程量及進度動態調整。
序號 | 工種 | 參考人數 |
1 | 專業技術員 | 1 |
2 | 管工 | 2 |
3 | 電焊、氣割工 | 1 |
4 | 自動氬弧焊工 | 1 |
5 | 手工氬弧焊工 | 1 |
6 | 普工 | 4 |
7 | 電工(含維護電工1人) | 2 |
8 | 測量工 | 1 |
9 | 清洗操作工 | 3 |
10 | 化驗工 | 1 |
11 | 管工 | 1 |
12 | 氬弧焊工 | 1 |
13 | 探傷工 | 1 |
合計 | 20人 |
材料設備
《製藥車間潔淨系統管道安裝工法》材料無需特別說明的材料,機具規格型號應根據工程實際進行選用,一般使用的主要工機具如下表所示,數量以工程量大小而定。
序號 | 名稱 | 規格 | 備註 |
1 | 手工氬弧焊機 | TIG-200A | 潔淨不鏽鋼管道定位、焊接 |
2 | 電焊機 | BX-300 | 碳鋼管及支架等用 |
3 | 角向磨光機 | Φ100 | 去毛刺、打磨用 |
4 | 全自動氬弧焊機 | AUTOMATIG256 | 不鏽鋼全位置焊用 |
5 | 手拉葫蘆 | 2噸 | 起吊物品用 |
6 | 手鑽 | 0~25 | 支架安裝 |
7 | 台鑽 | 0~25 | 支架等鑽孔 |
8 | 不鏽鋼管材切割機 | Φ400 | 潔淨系統不鏽鋼下料 |
9 | 型材切割機 | Φ400 | 支架下料切割等 |
10 | 酸洗泵 | 2.2千瓦 | 鈍化作業 |
11 | 液化池 | 1000×500×600 | 鈍化、試壓蓄水用 |
12 | 中和箱 | 1300×800×600 | 中和鈍化工藝中液體用 |
13 | X射線探傷儀 | XXQ—2505 | 焊接工藝評定、焊縫檢查 |
質量控制
《製藥車間潔淨系統管道安裝工法》的質量控制要求如下:
一、工程質量控制標準
1、嚴格執行《潔淨室施工及驗收規範》JGJ 71—90、《藥品生產質量管理規範》(GMP)(1998年修訂)、《潔淨廠房設計規範》GB 50073-2001等潔淨室和製藥相關規範和設計規定。
2、參照《脫脂工程施工及驗收規範》HG 20202—2000、《工業金屬管道工程施工及驗收規範》GB 50235—97、《工業設備及管道絕熱工程質量檢驗評定標準》GB 50185—93、《現場設備、工業管道焊接工程施工及驗收規範》GB 50236—98等執行。
二、質量保證措施
1、建立有效的質量控制體系,根據質量控制項目按照隨作業、隨記錄、隨驗收要求做好質量過程控制。
2、加強材料採購驗收,所用材料必須保證合格證、材質證明書等資料齊全,對高潔淨級別使用316L、304材質等不鏽鋼還應當送檢復驗,保證潔淨系統管道材質、控制器部件(閥門、檢測儀器和儀表等)的質量。
3、對潔淨車間不鏽鋼管道焊接時確保施工環境必須符合現場焊接作業條件。檢查是否具備足夠的照明度;現場應具備避風條件,保證氬弧焊在無風環境下作業等條件。做好焊接接頭拍片檢查,對吊頂、夾層無法或不利於拍片場地時應採用先試焊拍片檢查,然後按拍片檢查合格焊縫所設定的參數對同等潔淨管道進行施焊,以保證焊接接頭質量。
4、在安裝過程中,做到隨安裝、隨檢查、隨記錄,以控制安裝過程中管道坡度、立管垂直度、支盲管段距離、控制器部件安裝質量。
5、做好工序交接工作,堅持上道工序合格再進行下道工序作業。
安全措施
採用《製藥車間潔淨系統管道安裝工法》施工時,除應執行國家、地方的各項安全施工的規定外,尚應遵守注意下列事項:
一、堅持認真貫徹落實“安全第一,預防為主,綜合治理”的方針,根據國家有關規定、條例,結合施工單位實際情況和工程特點。組成項目經理負責下的專職安全員和班組兼職安全員以及工地安全用電負責人的直線型安全文明施工監督實施控制體系,執行安全生產責任制,為現場安全文明施工提供操作性強的管理保障。
二、對現場人員做好日常性的安全教育,要做到“班前講安全、班後評安全;開展安全日、安全月活動;新工人和參加安裝的普工進行安全應知應會和安全操作規程的教育。
三、施工現場內危險的深坑、施工預留孔、洞等處,應有防護設施,或掛危險標誌。
四、材料、構件、設備、現場機具和作業環境等按照相關防火、防風、防雷、防觸電等安全規定及安全施工要求進行布置,拆除的控制閥門等部件的裝箱箱板和廢料等應及時清理,防止釘傷,隨時清理地面上的油污,以免使人滑倒跌傷。
五、正確使用防護用品和防護設施,對剛焊接完畢的管道接頭,應避免手或身體與直接接觸,以免燙傷。
六、在吊頂作業或檢查時,應打開弔頂照明燈,如遇施工期間不具備吊頂照明條件的,要用安全行燈或手電筒等進行照明。避免因光線不明而引發管道安裝質量、碰傷等事故的發生。
七、管道清洗、脫脂、鈍化作業的場地,要通風良好,有防護措施並制定安全應急預案,同時應將排放液體經處理達到排放要求後排放到指定地點。
八、潔淨車間內作業人員應做到隨走隨清理現場施工垃圾,用具堆放整齊,做到有序施工、文明施工。
九、在潔淨室環氧地坪施工完成後,安裝工程作業人員必須保護好現場地坪。在作業區域的地面上敷設軟性材料既不劃傷地坪,又不會對室內造成污染,還能避免作業工具等劃傷地坪的保護層,並方便現場作業垃圾的堆放和清理,使作業的施工用具或管材等有序堆放在上面。
十、現場施工作業用的氧、乙炔等易燃、易爆等物品放置位置應當符合規範要求,氧、乙炔等壓力容器安裝安全閥和壓力表,避免暴曬、碰撞,氧氣瓶要嚴防沾油脂,乙炔發生器應具有防回火的安全裝置。
十一、與電焊、氣焊、氬弧焊工在一起操作施工時,應注意防止電焊或氣焊弧光傷眼睛。
十二、在吊裝管材等物品時所採用吊裝的鋼絲繩、卸扣和捯鏈等,應符合起吊重量的要求,所吊物品不得有鬆動或脫、滑落現象,對現場作業所使用的起重工具應當6個月進行一次荷重試驗;各種起吊機械和工具在使用前,應試吊檢查。
十三、現場有危險作業區域的,應當設定警戒線和掛上警示牌,不許外人進入。
十四、管道系統調試期間,檢查各排放口或進行排放口試排水,特別是在系統循環鈍化期間各排放口所排出的液體應當排放到專用耐腐蝕桶中,避免給潔淨車間內部造成污染。
環保措施
《製藥車間潔淨系統管道安裝工法》的環保措施如下:
一、固體物污染控制
無污染建渣等固體廢棄物應堆放至業主指定位置進行;對於可回收利用的固體廢棄物應當進行集中回收再利用;對於有污染、有毒等固體廢棄物也必須集中統一回收,並按照相關規定在指定地點填埋、回收處理等。
二、氣體污染控制
1、施工中所用氣體介質應當隨時對包裝情況進行檢查並妥善保管,避免因包裝損壞發生氣體泄漏造成經濟損失、環境污染甚至發生安全事故。
2、對作業過程中所產生的氣體污染應當採取稀釋、禁止等措施以降低甚至消除對環境造成的污染。
三、液體污染控制
1、當酸洗完成後,應採用氫氧化鈉溶液中和廢酸液,直至酸液呈中性後才能排放到污水溝或污水井中。
2、當鹼洗完成後,廢鹼液不能直接排放,套用稀硝酸或稀鹽酸中和廢鹼液,直至溶液呈中性後才能排放。
3、工程施工作業過程中的廢四氯化碳溶液不能直接排放,套用密閉桶封裝,並在陰涼處保存回收處理。
4、施工作業中達到排放要求的廢水應當在規定渠道中進行排放。
四、噪聲污染控制
1、施工過程中對作業時會產生噪聲的施工環節應當在隔聲篷或房間等環境中進行施工,當現場無條件單獨設定隔聲加工房時應當採取增設臨時隔聲壁、板等措施進行控聲,以減少對周圍環境造成影響。
2、對需要在產生噪聲環節中進行施工的作業人員應當做好勞動保護。
五、對施工中產生的輻射性、強光刺激等,應當採取禁止措施將影響區域縮小在儘可能小的空間內,以減小或避免對周圍環境造成污染,同時操作人員應當按要求規範作業做好勞動保護。
效益分析
《製藥車間潔淨系統管道安裝工法》的效益分析如下:
一、社會效益分析
運用該工法對潔淨系統管道安裝作業,彌補了國家相關規範文本對製藥工程中的不足,最大限度地控制了按照規範進行管道安裝對製藥工藝生產所造成不必要的污染,要求達到優良的高級別潔淨管道焊接接頭難度也得到降低,從而提高整個工程安裝質量,滿足藥品生產和GMP認證的需要。工程施工中產生的焊接弧光、噪聲等公害也得到最大的降低,取得社會效益。
二、經濟效益分析
該工法由於採用合理的管道工藝設定、自動焊接技術和合理優異的酸洗鈍化技術,提高了工程質量,降低了施工難度,有效預防了不合格品的出現和解決了工藝生產中污染控制問題,能順利實現GMP認證和生產工藝要求,降低作業成本,形成經濟效益。在“成都生物製品研究所細菌性疫苗生產車間安裝工程”中,潔淨系統管道安裝部分工程造價為4148896元,通過施工工藝改進、科學組織管理,實際套用成本為3415329元,節約成本733567元。
註:施工費用以2005-2006年施工材料價格計算
套用實例
《製藥車間潔淨系統管道安裝工法》在“成都生物製品研究所細菌性疫苗生產車間安裝工程”中得到了成功套用,具體情況如下:
該工程是成都生物製品研究所投資12000多萬元(安裝單項工程契約額達3106萬元),按國際標準設計建成(2005年前)中國最先進、生產規模最大的細菌性疫苗生產車間,生產設施和設備自動化程度高,具標準化水平的製藥工程。工程實施要求嚴格參照國際相關標準執行,並要在很短的工期內完成11.68噸的車間潔淨系統不鏽鋼管道安裝任務。而通過該工法的實際套用,使該工程最後達到了生產工藝要求,順利通過驗收,並於2004年1月一次性通過GMP認證,經過一年的生產運行,業主給予了高度的認可和評價。在單項安裝契約額近600萬的“四川科倫大藥廠大輸液車間GMP改造工程”和單項安裝工程契約額達365萬的“華西醫科大學製藥廠異地技術改造機電安裝工程”以及“中牧股份鄭州生物滅活疫苗車間安裝工程”和“世紀華洋凍乾粉針車間GMP改造工程”等項目中,該工法也得到成功套用,使業主在進行GMP認證過程中一次性通過。證明了該工法具有實際套用價值和推廣性。
榮譽表彰
2008年1月31日,中華人民共和國住房和城鄉建設部以“建質[2008]22號”檔案發布《關於公布2005-2006年度國家級工法的通知》,《製藥車間潔淨系統管道安裝工法》被評定為2005-2006年度國家二級工法。
操作原理
適用範圍
《製藥車間潔淨系統管道安裝工法》適用於製藥車間潔淨系統各種工藝管道的安裝,同時還可作為食品、精細化工、電子等行業潔淨系統管路安裝的參考。
工藝原理
《製藥車間潔淨系統管道安裝工法》的工藝原理敘述如下:
一、通過合理規範管道工藝布置,避免管道中的死角、盲點,從工藝布置上滿足GMP認證和生產工藝上的需要。
二、潔淨車間不鏽鋼管道接頭焊接,採用在氬氣保護下利用鎢極電極與工件間產生的電弧熱熔化焊件和填充焊絲進行施焊。焊接時,氬氣連續地從焊槍的噴嘴中和管道一端端頭中噴出,使整個焊接過程始終保持在這種惰性氣體的保護下進行完成,從而獲得單面焊雙面成型的高質量焊縫。
三、對純化水、注射水、純蒸汽等高要求潔淨不鏽鋼管道採用全位置氬弧焊進行焊接,對其餘要求相對較低的不鏽鋼管道則採用手工鎢極氬弧焊進行焊接。
四、潔淨車間管道支、吊架安裝和保溫防腐等工序,在滿足相關規定的前提下,從工藝布置和安裝方法上保證無脫落、不產塵、無污染,保障良好的潔淨車間內部生產環境。
五、在不鏽鋼管道鈍化工藝中根據油酸與鹼起皂化反應生成可溶性皂而將油脂除去。皂化反應終點判定主要根據清洗液中的OH離子濃度確定。主要反應式為:

六、潔淨不鏽鋼管內壁鹼洗脫脂後,當不鏽鋼管內壁表面處於活性狀態時,及時用8%稀硝酸溶液進行循環酸洗,使不鏽鋼管內壁形成一種緻密且光滑的保護膜,這樣既可以保護潔淨不鏽鋼管內壁不被腐蝕又可以減少微生物在管壁上的附著,滿足規範及GMP要求。
施工工藝
- 工藝流程
《製藥車間潔淨系統管道安裝工法》的製藥車間潔淨系統管道施工工藝流程如下圖。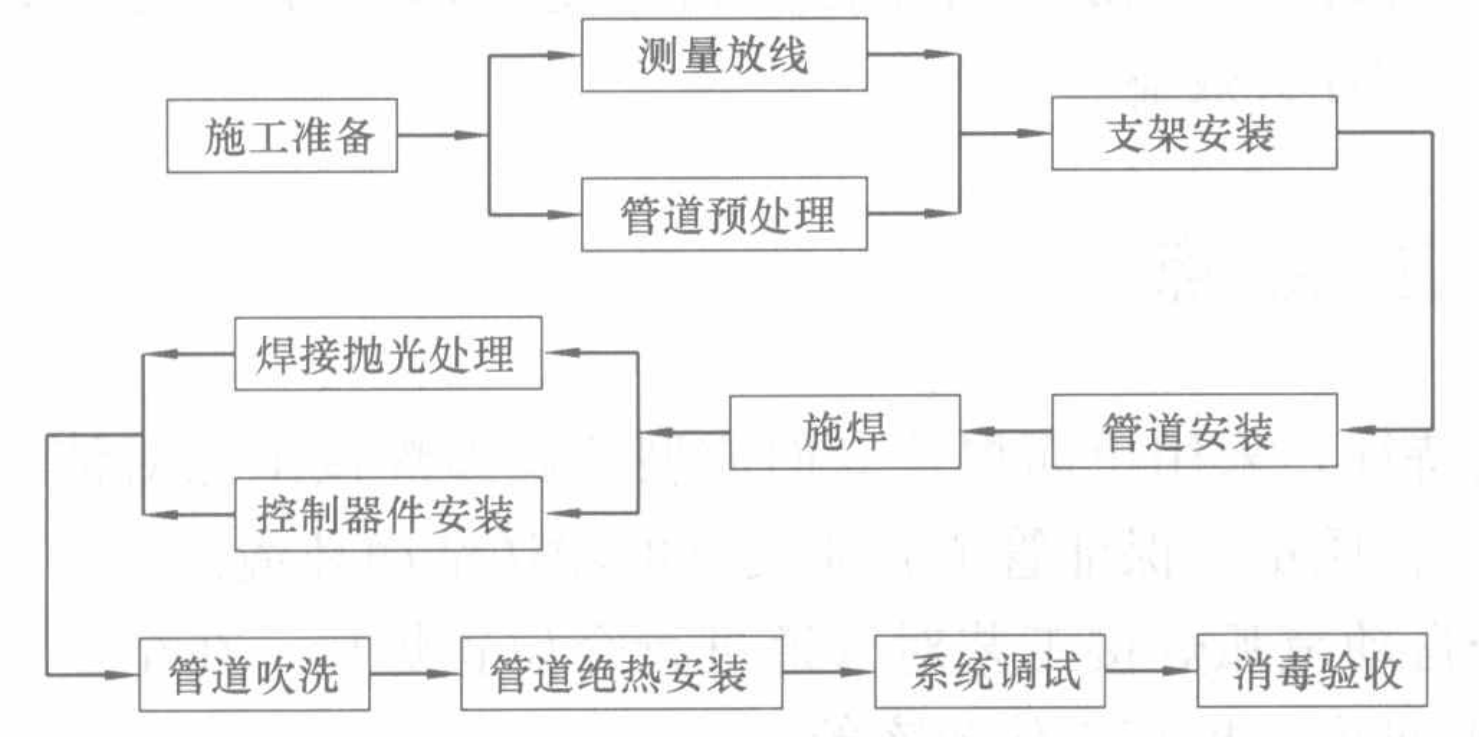
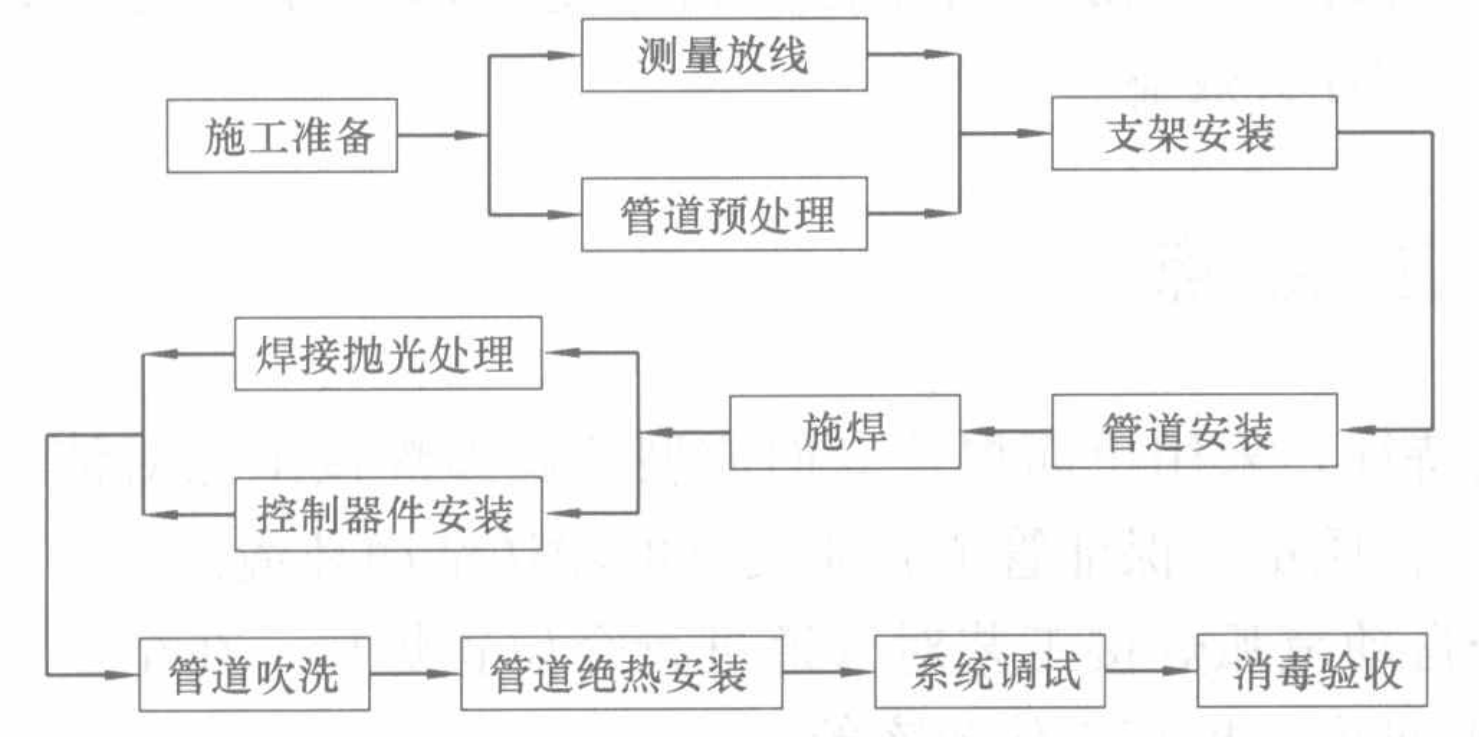
製藥車間潔淨系統管道施工工藝流程圖
- 操作要點
《製藥車間潔淨系統管道安裝工法》的操作要點如下:
一、施工準備
1.施工圖細化設計
(1)進場後應按照圖紙對現場進行勘測,在現場確定出管路的方位,並檢查現場實際與圖紙是否有衝突的地方,如遇風管等與設計管路通道發生矛盾應進行設計變更。
(2)根據工程設計圖紙和現場勘測的實際情況,堅持對注射水、純化水等高潔淨級別管道儘量使用整管段為原則進行二次施工圖細化設計。
2.人員準備
(1)除工程需要的普工外,其餘相應的焊工、管工、電工等都必須具備經培訓合格後並取得相應的上崗資格證書,同時對他們進行潔淨工程相關知識的培訓。
(2)根據該工程項目特點,技術人員需做好技術交底工作。操作相關人員必須掌握相關技術標準、施工要求及工程質量控制點。
3.硬體準備
(1)根據工程項目大小和工程進度計畫等情況準備與工程實際相匹配規模的機具。包括電焊機、氬弧焊機、全自動氬弧焊機、不鏽鋼管材切割機、手砂輪及儀器儀表等設備、器具。
(2)仔細檢查所用機具、儀器儀表各部位的完整性和使用性能的可靠性等,並進行試用檢查是否能滿足現場施工需要,若要定期送檢的還應當經檢驗合格後方能投入使用。
(3)根據工程需要準備好相應的輔材。其中應當注意焊接材料與焊接件材質的匹配。
(4)潔淨車間工藝管道中,物料、注射水(蒸餾水)、純化水、潔淨氣體等介質輸送管道應當採用內外壁電拋光的316L不鏽鋼管道;自來水等介質輸送管道可選用薄壁304不鏽鋼管、鋼襯不鏽鋼雙層金屬管等;蒸汽、排污、凝結水等其餘介質輸送管道應根據業主、設計等要求一般選用碳鋼管道材料。
(5)根據工程進度計畫及實際做好主材的採購及進場工作,並準備好供貨契約,國家或行業標準以及供方提供的發貨單、計量單、裝箱單、產品合格證、化驗單和其他相關憑證做好材料進場驗收準備。
(6)根據準備檔案依據在做好數量驗收的同時要做好質量驗收。各材料進行外觀檢驗合格後,對車間潔淨系統高要求管道還應組織進行理化復驗。
4.資料準備
(1)根據工程實際,準備好現場所需各種技術資料。包括施工圖紙、相關國家行業標準及業主要求的技術指標等。
(2)根據工程情況確定工程項目質量控制點,並制定工程現場質量控制計畫;同時還應制定好相關安全環境控制方案等。
(3)準備好潔淨車間管道安裝確認記錄相關檔案資料及現場施工控制評價資料等。
二、測量放線
1.根據最後細化設計的施工圖和現場勘測好的路線用墨線進行放線做好標記,確定管路現場的走向及標高位置,並確定出現場支吊、架位置。
2.對於潔淨室內從吊頂等頂部下穿工藝管道應當根據現場設備及其他設施布置情況進行放線,在潔淨室頂部做好穿孔標記。
三、管道預處理
1.製藥車間潔淨系統管道除少量材質為碳鋼管道按照相關規範規定進行處理即可外,對採用的不鏽鋼管道用磨光機或其他機具消除下料切口或焊接坡口的毛刺後,再用細紗布等進行打磨至Ra≤0.8微米,必要時還應對高潔淨管道進行化學或電化學拋光至Ra≤0.05微米,保證焊接接頭周邊外表與經過高度拋光處理的母材外表一致。
2.在安裝前進行管道脫脂的,在脫脂完成後必須用封頭將管材兩端封好。對下料開好坡口的潔淨系統管道焊接接頭應進行清理乾淨,清理範圍20~30毫米,並用封頭進行保護,所用封頭保護長度不應小於清理範圍值。脫脂後的彎頭、焊接卡盤等管件,應當用潔淨塑膠布進行包裹好,避免外界環境造成二次污染。
四、支架安裝
1.潔淨室內管道支、吊架選用材料應與相應管道材料材質相匹配,並按規範進行製做。
2.安裝時不得直接安裝在潔淨車間設備主體上,但可與淨化彩鋼隔斷或設備基礎連線。
3.潔淨室內在彩板等建築物、構築物上安裝的管道支、吊架所產生的間隙,套用無污染、不產塵、無脫落的密封膠密封好。
4.對於導向或滑動支架其滑動面應潔淨並與管道坡度平行,不得歪斜、卡涉。安裝位置應從支撐中心向位移反方向偏移,偏移量為位移值的12或符合設計規定,絕熱層不得妨礙位移。
5.對於管道中安裝的大口徑、重量大的閥門或其他控制部件,不得用管道支撐重量,必須設定專用支架進行支撐,以免影響管道坡度。
6.管道支、吊架安裝時,所用材料應與管道材料相匹配,使用的非金屬墊片其氯離子含量不得超過50×10(50ppm)。同時,管路定位安裝中使用的臨時支、吊架應與正式支、吊架區分開來。並在管道安裝完成後拆除臨時支、吊架。潔淨室內的臨時支、吊架不得與潔淨管道點焊或劃傷,應對潔淨管道電拋光的外表面做好保護。
7.支、吊架位置應準確、安裝平穩牢固,與管道之間接觸應緊密,同時不能影響管道的坡度和潔淨管道接頭之間連線的同軸度。
五、管道安裝
1.潔淨系統管道採用的不鏽鋼管等應採用機械或等離子方法切割,不鏽鋼管及鈦管用砂輪切割或修磨時,應使用專用砂輪片,不得使用切割炭素鋼管的砂輪,以免受污染而影響不鏽鋼管與鈦管的質量。
2.根據切割後的管道再進行預組裝或試安裝,並依次按順序做好標記。
3.潔淨系統管道安裝中,首先根據管道介質要求和工藝設計確定出管路採用的連線方式,其中注射水(蒸餾水)、純化水等液體輸送管道採取循環布置,回水流入貯罐,可採用並聯或串聯的連線方法,以串聯的方法較好,見下圖1、下圖2;其餘介質管道一般都採用通常的總支線管路形式。
4.安裝中對管道進行定位時,應按照相關標準規範不影響現場焊接作業的情況下及時固定和調整支、吊架。
5.車間潔淨系統管路安裝時,穿牆、樓套管除按規定製做安裝外,材質應與管道材質相匹配,套管與管道之間的空隙應採用不燃材料填塞,當潔淨室內所需用到穿牆、樓套管時,應使套管與管道之間的間隙的填充物應做到不燃、不產塵無污染、可阻斷外界介質流通。對潔淨室之間潔淨級別等同的管道安裝的穿牆套管可不堵塞,但套管與牆體之間應當密閉,如物料管道等。
6.管道標高應以設計圖紙設定的基準標高按照管道坡度進行布置,當設計無說明時應根據用水點標高為初始標高進行排列設定。
7.潔淨室吊頂下穿管道應按照現場放線位置採用反開孔方式進行,確保下穿管道安裝水平坐標位置的正確性。
8.安裝定位中的管道應當按管道預組裝時的系統號和順序號進行安裝放置,並應檢查封頭是否保持完好,不得有影響潔淨管道內部清潔的情況出現。
9.在對潔淨系統不鏽鋼管道進行定位安裝中,臨時採用的手工氬弧焊焊接作業時,也必須對焊縫進行內外充氬焊接保護作業。
10.管道進行定位安裝時如需安裝臨時支撐或支架的,應當及時安裝。對於不鏽鋼管道,不得使臨時支撐或支架與焊接,同時對不鏽鋼管道表面做好保護,並保證管道上環焊口距支吊架淨距離不小於100毫米。
11.管道在定位時,其注射水、純化水、物料等液體介質輸送管道支流處應按小於6倍管徑進行設定,對於潔淨系統工藝管道中的冷卻水系統應按小於4倍管徑進行設定,以減少支管處死角距離。不需要焊接連線的注射水、純化水等潔淨系統不鏽鋼管道應採用衛生夾頭分段連線。
六、焊接
1.管道安裝放置後,碳鋼管道及要求較低的排水等管道應當及時焊接,其中潔淨系統中的不鏽鋼管道材質的應當採用熱熔式手工氬弧焊進行焊接,焊接標準及方法按照相關標準執行。
2.對注射水、純化水、物料、純蒸汽等高要求潔淨級別的潔淨系統不鏽鋼管道必須採用自動氬弧焊進行焊接,連線口處應當及時封閉,避免二次污染。
3.對潔淨系統不鏽鋼管道在進行手工或自動的氬弧焊過程中都必須做好管道焊縫的內外充氬保護(下圖)。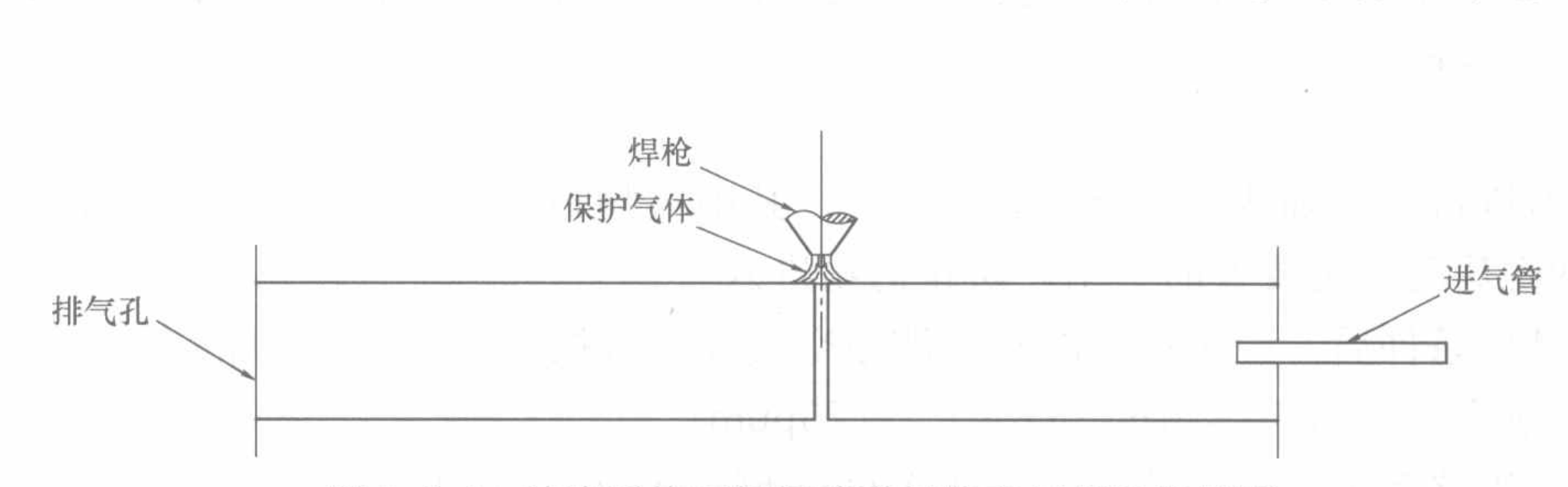
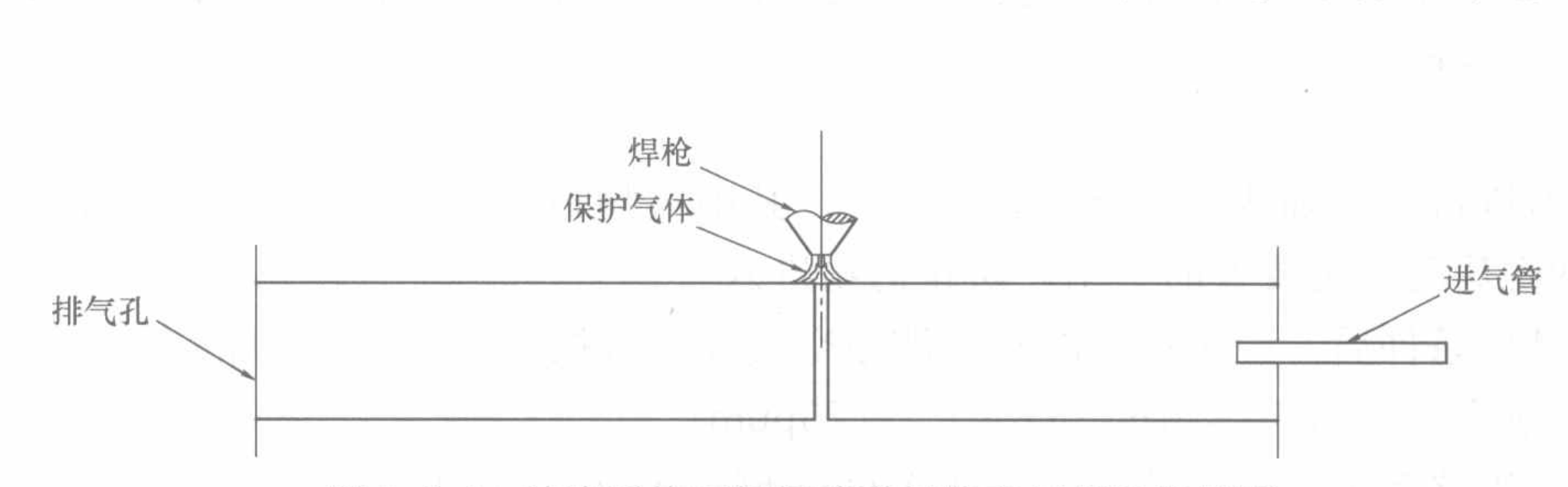
潔淨系統不鏽鋼管道焊接充氬保護設定圖
4.管道點焊定位前,接頭處可用靠模等工具保證管道間的同軸度,使整個管路在一條直線上。測量平直度應在距接口中心200毫米處進行測量。
5.潔淨系統不鏽鋼管道點焊應當採用氬弧焊,點焊點應均值對稱布置,根據管徑大小選擇點焊數一般在3~12點之間。
6.對潔淨系統不鏽鋼管道進行氬弧焊作業時,首先應對管內沖氬裝置和焊縫接頭固定情況進行檢查確認,以保證在進行焊接作業時使焊縫內外都始終保持在惰性氣體中完成整個焊接過程,從而獲得優良的焊縫質量。
7.焊接中,所選用鎢極應當選擇鈰鎢極。
8.選擇工程中各類規格、壁厚不等的不鏽鋼管試件用作自動氬弧焊焊接試驗,進行焊接工藝評定,從而確定送氣、電流、旋轉以及送絲值(用自熔式焊接時不用確定送絲參數),以作為自動焊焊接程式輸入參數,並進行模擬試焊。
9.按照工藝評定進行全位置焊接時,氬氣純度不得低於99.8%。同時,全位置焊接的自動焊機頭控制線長度不宜超過15米,避免因線路太長而影響作業電流、電壓等,從而影響焊接接頭質量。
10.焊接過程中,自動焊應按照設定好的原程式進行一次性完成整個焊接作業過程,不得對焊接作業過程進行干涉。
11.對管道進行焊接作業時,還應進行焊接接頭質量進行檢查,一般採用X光進行拍片。對吊頂、夾層中不便進行拍片檢查的,應當根據事先經拍片檢查合格所設定的同種規格型號的不鏽鋼管自動焊接編程程式進行焊接作業。
七、焊接拋光處理
1.對車間潔淨系統不鏽鋼管道進行焊接作業完成後,需要對焊縫進行拋光處理的,應當對管道焊縫用羊毛輪等拋光工具進行機械拋光至Ra≤0.8微米。
2.在機械拋光完成後再進行化學拋光處理,儘可能使焊縫光潔度與母材管道一致。
八、控制器件安裝
1.控制器件安裝前,首先對各控制器件逐個進行外觀檢查,對隔膜閥需要抽取10%進行拆卸後進行內部表面檢查。
2.外觀檢查合格後,按照相關要求對閥門等控制項做耐壓強度試驗。試驗應以每批(同牌號、同規格、同型號)數量中抽查10%。如有漏裂不合格的,應再抽查20%,如仍有不合格的則須逐個試驗。強度和嚴密性試驗壓力應為閥門出廠規定之壓力,並做好閥門試驗記錄。
3.車間潔淨系統管道安裝中,注射水(蒸餾水)、純化水、物料管道等都應採用不鏽鋼聚四氟乙烯隔膜閥,或採用衛生夾頭連線,並檢查填料是否符合GMP和工藝生產要求。
4.控制項安裝時,應仔細核對閥件的型號與規格是否符合設計要求。控制項上標示箭頭,應與介質流動方向一致。
5.測量儀表控制項安裝與受控管道之間管道距離應不大於6倍管徑或冷卻水不大於4倍關徑為宜,減少運行中的死角。
6.閥門使用上除應按相關規定執行外,對注射水、物料等潔淨管道上的閥門等控制器件與管道之間的連線方式上應採用衛生夾頭、法蘭連線,不得採用絲接進行,位置應符合設計要求,便於操作。
九、管道吹洗
1.管道試壓
(1)在對管道進行安裝確認後即進行通水沖洗,其中對物料、注射水、純化水等管道一般採用純化水進行沖洗。沖洗後的管道要及時封堵,防止污物進入。
(2)待具備試壓條件後,應採用潔淨水、潔淨空氣或氮氣按照設計要求和相關規範進行,試壓過程中採用的水所含氯離子含量不得超過25×10(25ppm)。
(3)通水後,管路系統中的調節閥,過濾器的濾網及有關儀表和控制項要在試壓吹洗前進行保護性拆除。
(4)試壓過程中對注射水、純化水等高潔淨級別管道一般採用純化水進行試壓,並穩壓30分鐘,同時劃定試壓禁區。試壓完成後應排盡積液。
(5)管道試壓按系統分段進行,既要滿足規範要求,又要考慮管材和閥件因高程靜壓增加的承受能力。水壓強度試驗的測試點設在管網的最低點對管網注水時,應先將管網內的空氣排淨,並緩緩升壓,達到試驗壓力後,穩壓30分鐘,目測管網應無泄漏和無變形,且壓力降不應大於0.05兆帕。
2.酸洗、鈍化
(1)試壓合格後建立酸洗鈍化清洗站(鈍化清洗站建立參見下圖),需要採用濕法鈍化對潔淨系統不鏽鋼管道進行鈍化處理。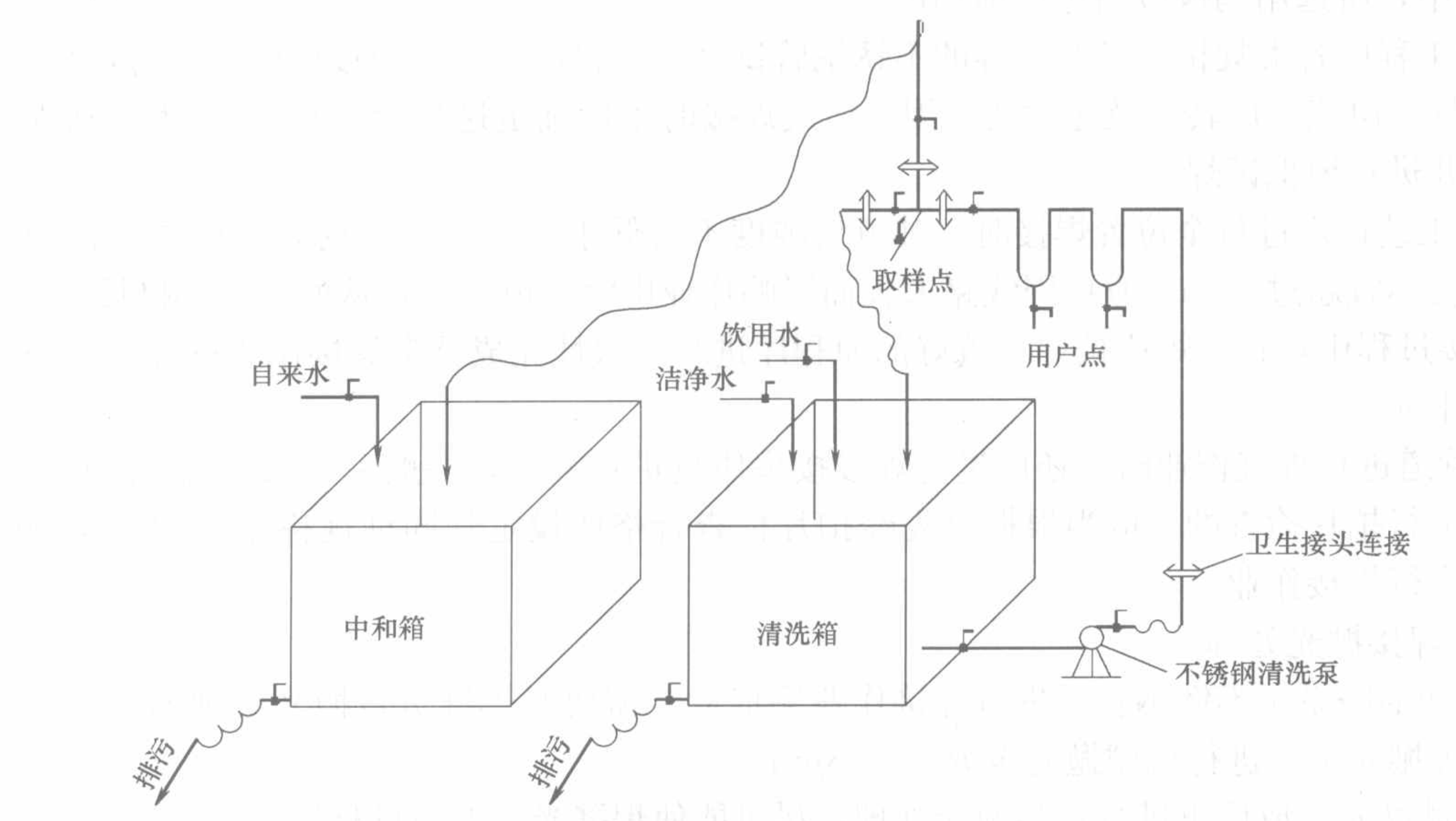
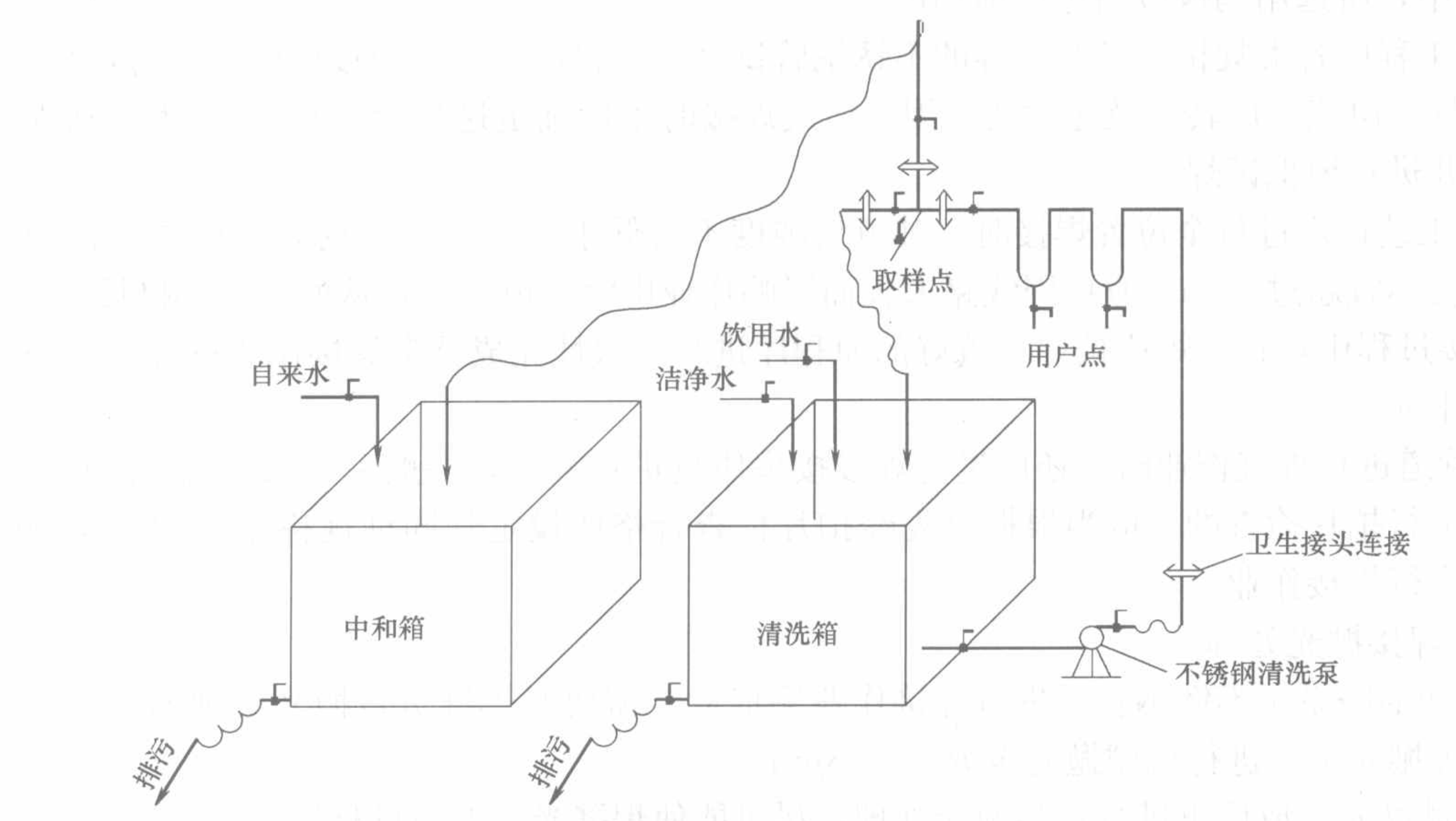
鈍化清洗站建立圖
(2)清洗站的動力泵應選耐酸泵,用衛生級接頭與潔淨系統管路進行連線,所連線的整個管路系統應呈一閉合迴路形式以便進行循環酸洗鈍化處理。
(3)0.1摩爾/升HCL溶液通過N1V1=N2V2(式中N1=0.1摩爾/升,N2=12摩爾/升,V1=1升,V2為所需濃鹽酸的體積數)計算出配製1000毫升0.1摩爾/升HCL溶液所需濃鹽酸(比重1.19,約12摩爾/升)的毫升數。然後用小量筒量取該毫升數的濃鹽酸,加入純化水中,並稀釋成1000毫升溶液,貯於玻塞細口瓶中,充分搖勻,並貼上標籤,註明試劑的名稱、配製日期,待用。
(4)1.0摩爾/升NaOH溶液通過NV=W/M×1000【式中N=1.0摩爾/升,V=1000毫升,M=40克(NaOH的摩爾質量),W為配製1000毫升10摩爾/升的NaOH溶液所需的NaOH克數】,計算出配製1000毫升1.0摩爾/升NaOH溶液所需的NaOH的克數,將所需的粒狀NaOH並在天平秤上稱出,然後置於1000毫升純化水中進行溶解,配製成溶液,貯於具有橡皮塞的細口瓶中,充分搖勻,並貼上標籤,註明試劑名稱、配製日期,待用。
(5)根據整個管路長度、管徑和清洗相計算出總容積,並根據容積配製出相應的溶液進行鈍化作業。在分別完成鹼洗和酸洗後,對整個迴路都應採用純化水進行30分鐘以上的沖洗。
(6)本道工序中分別用0.1摩爾/升HCL和1.0摩爾/升NaOH標準溶液來滴定清洗時的鹼洗溶液的OH變化情況、酸洗溶液的H變化情況來判定終點。循環鹼洗時,每隔5英寸用0.1摩爾/升HCL標準溶液(從取樣點取樣)進行測定一次。當連續3次0.1摩爾/升HCL用量無變化時,則表明鹼洗達到終點。酸洗進行30分鐘後,每隔5英寸需測定管路中的酸濃度,當最後三次酸濃度基本保持一致時,循環酸洗即達到終點。
(7)當鹼洗達到終點時,將管路回液管移至中和箱內,並向清洗箱內注入純化水或注射水。在中和箱內鹼液液位降至1/3時,開始緩慢地向中和箱內加入少量濃鹽酸,並用pH試紙檢測,取樣溶液呈中性時,打開排污閥進行排放。當管路中液體呈中性後,再把所有用戶點的閥門打開,將用戶點盲管中所有的鹼液排盡,然後將閥門關閉。
(8)當酸洗、鈍化達到終點後,便向清洗箱內注入純化水或注射水,並將管路中回液管轉換到中和箱內,同時向中和箱內緩慢加入NaOH顆粒中和清洗液,並用pH試紙測定中和箱內的pH值,當達到中性時即可排放。同時用pH試紙測定清洗箱內液體pH值,當達到中性,便可停止排放清洗液,同時讓管內液體繼續循環半個小時以上,然後將管內液體排放完畢。
3.管道吹掃
(1)用水沖洗的潔淨系統管道應採用潔淨水進行,對注射水(蒸餾水)、純化水、物料或其他需要用水沖洗的奧氏體不鏽鋼潔淨管道應當採用經化驗合格,氯離子含量不得超過25×10(25ppm)的注射水或純化水進行。
(2)沖洗時應採用較大動力的泵進行,保證最大流量,流速不低於1.5米/秒,並將整個管路系統連線成一個開環系統進行沖洗。沖洗時排放口不得接入注射水或純化水貯罐,應當排放在排水井、溝或指定位置,排放管道不得小於被沖洗管道截面積的60%。
(3)沖洗中各支管及排放口都應當進行沖洗,同時沖洗應當連續進行,一般沖洗時間不應少於15英寸。管道沖洗完成後還應將水排盡並經吹乾後方能投入使用。
(4)用氣體進行吹掃的潔淨系統管道需要選用潔淨空氣吹掃或清潔蒸汽進行,禁止採用污染的介質進行吹掃。吹掃壓力不得超過設計壓力,流速不得低於20米/秒。吹掃時應在排氣口設定一貼好潔淨白布的靶板檢驗,10分鐘內靶板無雜物即可。
(5)純蒸汽吹掃應以大流量,流速不低於30米/秒的速度進行,並應單根輪流進行吹掃,結果應符合設計檔案及相關規定。
十、管道絕熱安裝
1.金屬支吊架、明裝碳鋼管等除銹後一般刷防鏽漆二道,再刷調合漆一道、然後刷面漆一道。做好防腐後的管道要進行成品保護,防止防腐層的破壞。
2.管道的保溫應在防腐和水壓試驗合格後進行,保溫層的厚度按照規範要求進行。
3.對於醫藥潔淨室內管道絕熱還必須進行防護處理,以防止絕熱層對潔淨車間造成脫落、污染等。因而在潔淨室內應對絕熱層外表面採用鏡面不鏽鋼皮進行保護處理,滿足不產塵、無污染、不脫落的潔淨環境要求。
4.鏡面不鏽鋼皮應保護好外部光潔度,在彎角等需褶皺處應做成圓弧過渡的弧形保溫外殼。保溫的鏡面不鏽鋼皮在相互銜接處縱縫搭接長度應為30~50毫米,橫縫處為環形咬口式連線,以防止遇熱管殼膨脹因素的影響,見下圖1~下圖3。
5.不鏽鋼皮應做成封閉式保溫外殼。不鏽鋼皮用密封膠密封處必須採用無污染、不產塵、無脫落的密封膠密封,並做成圓弧過渡形狀。
6.管道防腐絕熱施工應當在試壓合格、鈍化工作完成和需要蒸汽吹掃的管道吹掃完成後進行。對於管道絕熱除需伴熱管道外都應單路進行,相應外表顏色應當符合國家或設計相關規定,對管道上進行介質流向標識處,標識顏色應能按相關規定體現內部所流何種介質。
十一、系統調試
1.管道系統調試應在設備調試合格後進行單系統管路調試。先手動啟動控制設備,檢查該系統在手動情況下是否正常。在手動正常情況下按照系統設計啟動控制系統檢查管路運行情況。同時對熱負荷介質輸送管道在調試階段或試運行階段應當對支、吊架逐個進行檢查並及時調整。單系統調試確認合格後,按照系統設計聯動試車,對整體安裝情況進行檢查。
2.系統調試正常運行後,模擬生產,並每隔1小時進行取樣,測電導率並與工藝及GMP要求進行對比,看是否達到標準。若未達到標準,則重複上述清洗過程進行再清洗,直至達到要求為止。
十二、消毒驗收
1.對物料、純蒸汽、純化水、注射水等介質輸送的潔淨管道都需進行消毒。消毒方法可採用巴氏消毒、臭氧消毒、紫外線水中殺菌、清潔蒸汽消毒,其中以選擇清潔蒸汽消毒為主,消毒溫度為121攝氏度,每個用點至少15分鐘。
2.純蒸汽消毒前應將整個管路系統連線成開環系統,使最終出口有利於蒸汽的順利排放,不會產生剩餘蒸汽凝結水排放不盡的情況發生。
3.當車間純蒸汽發生器經調試達到正常使用要求合格後,可就地使用,直接用設計的消毒系統對整個管路進行消毒。當需採用外部純蒸汽對本系統進行消毒時,被消毒的管道系統與清潔蒸汽之間的連線距離儘可能短,連線管道採用不鏽鋼管道或無污染、耐高溫的工程塑膠管道進行連線。
4.當消毒完成後,應當用注射水對所消毒液體介質輸送管道進行清洗,清洗時間不應短於20分鐘,同時開啟各用水點5分鐘以上。
5.工程實體完成並完成試車後,經消毒檢驗合格即可準備齊全相應的工程驗收資料通知監理組織驗收工作。
- 勞動力組織
《製藥車間潔淨系統管道安裝工法》根據工程規模大小可按照下表的工種分配方式進行組織施工,並根據工程量及進度動態調整。
序號 | 工種 | 參考人數 |
1 | 專業技術員 | 1 |
2 | 管工 | 2 |
3 | 電焊、氣割工 | 1 |
4 | 自動氬弧焊工 | 1 |
5 | 手工氬弧焊工 | 1 |
6 | 普工 | 4 |
7 | 電工(含維護電工1人) | 2 |
8 | 測量工 | 1 |
9 | 清洗操作工 | 3 |
10 | 化驗工 | 1 |
11 | 管工 | 1 |
12 | 氬弧焊工 | 1 |
13 | 探傷工 | 1 |
合計 | 20人 |
材料設備
《製藥車間潔淨系統管道安裝工法》材料無需特別說明的材料,機具規格型號應根據工程實際進行選用,一般使用的主要工機具如下表所示,數量以工程量大小而定。
序號 | 名稱 | 規格 | 備註 |
1 | 手工氬弧焊機 | TIG-200A | 潔淨不鏽鋼管道定位、焊接 |
2 | 電焊機 | BX-300 | 碳鋼管及支架等用 |
3 | 角向磨光機 | Φ100 | 去毛刺、打磨用 |
4 | 全自動氬弧焊機 | AUTOMATIG256 | 不鏽鋼全位置焊用 |
5 | 手拉葫蘆 | 2噸 | 起吊物品用 |
6 | 手鑽 | 0~25 | 支架安裝 |
7 | 台鑽 | 0~25 | 支架等鑽孔 |
8 | 不鏽鋼管材切割機 | Φ400 | 潔淨系統不鏽鋼下料 |
9 | 型材切割機 | Φ400 | 支架下料切割等 |
10 | 酸洗泵 | 2.2千瓦 | 鈍化作業 |
11 | 液化池 | 1000×500×600 | 鈍化、試壓蓄水用 |
12 | 中和箱 | 1300×800×600 | 中和鈍化工藝中液體用 |
13 | X射線探傷儀 | XXQ—2505 | 焊接工藝評定、焊縫檢查 |
質量控制
《製藥車間潔淨系統管道安裝工法》的質量控制要求如下:
一、工程質量控制標準
1、嚴格執行《潔淨室施工及驗收規範》JGJ 71—90、《藥品生產質量管理規範》(GMP)(1998年修訂)、《潔淨廠房設計規範》GB 50073-2001等潔淨室和製藥相關規範和設計規定。
2、參照《脫脂工程施工及驗收規範》HG 20202—2000、《工業金屬管道工程施工及驗收規範》GB 50235—97、《工業設備及管道絕熱工程質量檢驗評定標準》GB 50185—93、《現場設備、工業管道焊接工程施工及驗收規範》GB 50236—98等執行。
二、質量保證措施
1、建立有效的質量控制體系,根據質量控制項目按照隨作業、隨記錄、隨驗收要求做好質量過程控制。
2、加強材料採購驗收,所用材料必須保證合格證、材質證明書等資料齊全,對高潔淨級別使用316L、304材質等不鏽鋼還應當送檢復驗,保證潔淨系統管道材質、控制器部件(閥門、檢測儀器和儀表等)的質量。
3、對潔淨車間不鏽鋼管道焊接時確保施工環境必須符合現場焊接作業條件。檢查是否具備足夠的照明度;現場應具備避風條件,保證氬弧焊在無風環境下作業等條件。做好焊接接頭拍片檢查,對吊頂、夾層無法或不利於拍片場地時應採用先試焊拍片檢查,然後按拍片檢查合格焊縫所設定的參數對同等潔淨管道進行施焊,以保證焊接接頭質量。
4、在安裝過程中,做到隨安裝、隨檢查、隨記錄,以控制安裝過程中管道坡度、立管垂直度、支盲管段距離、控制器部件安裝質量。
5、做好工序交接工作,堅持上道工序合格再進行下道工序作業。
安全措施
採用《製藥車間潔淨系統管道安裝工法》施工時,除應執行國家、地方的各項安全施工的規定外,尚應遵守注意下列事項:
一、堅持認真貫徹落實“安全第一,預防為主,綜合治理”的方針,根據國家有關規定、條例,結合施工單位實際情況和工程特點。組成項目經理負責下的專職安全員和班組兼職安全員以及工地安全用電負責人的直線型安全文明施工監督實施控制體系,執行安全生產責任制,為現場安全文明施工提供操作性強的管理保障。
二、對現場人員做好日常性的安全教育,要做到“班前講安全、班後評安全;開展安全日、安全月活動;新工人和參加安裝的普工進行安全應知應會和安全操作規程的教育。
三、施工現場內危險的深坑、施工預留孔、洞等處,應有防護設施,或掛危險標誌。
四、材料、構件、設備、現場機具和作業環境等按照相關防火、防風、防雷、防觸電等安全規定及安全施工要求進行布置,拆除的控制閥門等部件的裝箱箱板和廢料等應及時清理,防止釘傷,隨時清理地面上的油污,以免使人滑倒跌傷。
五、正確使用防護用品和防護設施,對剛焊接完畢的管道接頭,應避免手或身體與直接接觸,以免燙傷。
六、在吊頂作業或檢查時,應打開弔頂照明燈,如遇施工期間不具備吊頂照明條件的,要用安全行燈或手電筒等進行照明。避免因光線不明而引發管道安裝質量、碰傷等事故的發生。
七、管道清洗、脫脂、鈍化作業的場地,要通風良好,有防護措施並制定安全應急預案,同時應將排放液體經處理達到排放要求後排放到指定地點。
八、潔淨車間內作業人員應做到隨走隨清理現場施工垃圾,用具堆放整齊,做到有序施工、文明施工。
九、在潔淨室環氧地坪施工完成後,安裝工程作業人員必須保護好現場地坪。在作業區域的地面上敷設軟性材料既不劃傷地坪,又不會對室內造成污染,還能避免作業工具等劃傷地坪的保護層,並方便現場作業垃圾的堆放和清理,使作業的施工用具或管材等有序堆放在上面。
十、現場施工作業用的氧、乙炔等易燃、易爆等物品放置位置應當符合規範要求,氧、乙炔等壓力容器安裝安全閥和壓力表,避免暴曬、碰撞,氧氣瓶要嚴防沾油脂,乙炔發生器應具有防回火的安全裝置。
十一、與電焊、氣焊、氬弧焊工在一起操作施工時,應注意防止電焊或氣焊弧光傷眼睛。
十二、在吊裝管材等物品時所採用吊裝的鋼絲繩、卸扣和捯鏈等,應符合起吊重量的要求,所吊物品不得有鬆動或脫、滑落現象,對現場作業所使用的起重工具應當6個月進行一次荷重試驗;各種起吊機械和工具在使用前,應試吊檢查。
十三、現場有危險作業區域的,應當設定警戒線和掛上警示牌,不許外人進入。
十四、管道系統調試期間,檢查各排放口或進行排放口試排水,特別是在系統循環鈍化期間各排放口所排出的液體應當排放到專用耐腐蝕桶中,避免給潔淨車間內部造成污染。
環保措施
《製藥車間潔淨系統管道安裝工法》的環保措施如下:
一、固體物污染控制
無污染建渣等固體廢棄物應堆放至業主指定位置進行;對於可回收利用的固體廢棄物應當進行集中回收再利用;對於有污染、有毒等固體廢棄物也必須集中統一回收,並按照相關規定在指定地點填埋、回收處理等。
二、氣體污染控制
1、施工中所用氣體介質應當隨時對包裝情況進行檢查並妥善保管,避免因包裝損壞發生氣體泄漏造成經濟損失、環境污染甚至發生安全事故。
2、對作業過程中所產生的氣體污染應當採取稀釋、禁止等措施以降低甚至消除對環境造成的污染。
三、液體污染控制
1、當酸洗完成後,應採用氫氧化鈉溶液中和廢酸液,直至酸液呈中性後才能排放到污水溝或污水井中。
2、當鹼洗完成後,廢鹼液不能直接排放,套用稀硝酸或稀鹽酸中和廢鹼液,直至溶液呈中性後才能排放。
3、工程施工作業過程中的廢四氯化碳溶液不能直接排放,套用密閉桶封裝,並在陰涼處保存回收處理。
4、施工作業中達到排放要求的廢水應當在規定渠道中進行排放。
四、噪聲污染控制
1、施工過程中對作業時會產生噪聲的施工環節應當在隔聲篷或房間等環境中進行施工,當現場無條件單獨設定隔聲加工房時應當採取增設臨時隔聲壁、板等措施進行控聲,以減少對周圍環境造成影響。
2、對需要在產生噪聲環節中進行施工的作業人員應當做好勞動保護。
五、對施工中產生的輻射性、強光刺激等,應當採取禁止措施將影響區域縮小在儘可能小的空間內,以減小或避免對周圍環境造成污染,同時操作人員應當按要求規範作業做好勞動保護。
效益分析
《製藥車間潔淨系統管道安裝工法》的效益分析如下:
一、社會效益分析
運用該工法對潔淨系統管道安裝作業,彌補了國家相關規範文本對製藥工程中的不足,最大限度地控制了按照規範進行管道安裝對製藥工藝生產所造成不必要的污染,要求達到優良的高級別潔淨管道焊接接頭難度也得到降低,從而提高整個工程安裝質量,滿足藥品生產和GMP認證的需要。工程施工中產生的焊接弧光、噪聲等公害也得到最大的降低,取得社會效益。
二、經濟效益分析
該工法由於採用合理的管道工藝設定、自動焊接技術和合理優異的酸洗鈍化技術,提高了工程質量,降低了施工難度,有效預防了不合格品的出現和解決了工藝生產中污染控制問題,能順利實現GMP認證和生產工藝要求,降低作業成本,形成經濟效益。在“成都生物製品研究所細菌性疫苗生產車間安裝工程”中,潔淨系統管道安裝部分工程造價為4148896元,通過施工工藝改進、科學組織管理,實際套用成本為3415329元,節約成本733567元。
註:施工費用以2005-2006年施工材料價格計算
套用實例
《製藥車間潔淨系統管道安裝工法》在“成都生物製品研究所細菌性疫苗生產車間安裝工程”中得到了成功套用,具體情況如下:
該工程是成都生物製品研究所投資12000多萬元(安裝單項工程契約額達3106萬元),按國際標準設計建成(2005年前)中國最先進、生產規模最大的細菌性疫苗生產車間,生產設施和設備自動化程度高,具標準化水平的製藥工程。工程實施要求嚴格參照國際相關標準執行,並要在很短的工期內完成11.68噸的車間潔淨系統不鏽鋼管道安裝任務。而通過該工法的實際套用,使該工程最後達到了生產工藝要求,順利通過驗收,並於2004年1月一次性通過GMP認證,經過一年的生產運行,業主給予了高度的認可和評價。在單項安裝契約額近600萬的“四川科倫大藥廠大輸液車間GMP改造工程”和單項安裝工程契約額達365萬的“華西醫科大學製藥廠異地技術改造機電安裝工程”以及“中牧股份鄭州生物滅活疫苗車間安裝工程”和“世紀華洋凍乾粉針車間GMP改造工程”等項目中,該工法也得到成功套用,使業主在進行GMP認證過程中一次性通過。證明了該工法具有實際套用價值和推廣性。
榮譽表彰
2008年1月31日,中華人民共和國住房和城鄉建設部以“建質[2008]22號”檔案發布《關於公布2005-2006年度國家級工法的通知》,《製藥車間潔淨系統管道安裝工法》被評定為2005-2006年度國家二級工法。