《管道環焊縫相控陣全自動超音波檢測工法》是中國石油天然氣管道局第一工程分公司完成的工程建設類施工工法;主要完成人是張宏亮、李健、韓國軍、王成強、賈世民;該工法適用於利用多通道、聲聚焦、分區掃查的全自動超音波檢測系統,對壁厚為7~50毫米的鋼質石油和天然氣長輸、集輸及其他油氣管道對接環焊縫電弧焊的全自動焊焊縫的檢測。
《管道環焊縫相控陣全自動超音波檢測工法》主要特點是:用一組探頭取代單個探頭、自動化取代人工的操作、檢測速度快;對危險性大面積型缺欠敏感,能夠測定缺欠的自身高度;全自動超音波具有更低的返修率;自動焊焊接機組,可實時控制焊接過程,及時避免缺欠;因自動化程度高,提高了工作效率,減少了人工探傷所帶來的誤操作。
2011年9月30日,《管道環焊縫相控陣全自動超音波檢測工法》被中華人民共和國住房和城鄉建設部評定為國家二級工法。
基本介紹
- 中文名:管道環焊縫相控陣全自動超音波檢測工法
- 工法編號:YJGF73-2002
- 類別:工程建設類
- 審批單位:中華人民共和國住房和城鄉建設部
- 主要榮譽:國家二級工法(2009-2010年度)
- 完成單位:中國石油天然氣管道局第一工程分公司
- 主要完成人:張宏亮、李健、韓國軍、王成強、賈世民
形成原因,工法特點,操作原理,適用範圍,工藝原理,工藝流程,操作要點,材料設備,質量控制,安全措施,環保措施,效益分析,套用實例,榮譽表彰,
形成原因
21世紀國中國長輸管道焊接技術不斷發展,採用全自動焊焊接技術,工作效率高,但產生的缺欠主要是面積型缺欠;為了更好地控制工程質量,提高工作效率,及時跟蹤自動焊檢測,糾正焊接參數,控制焊接過程,採用中國以外先進的全自動超音波檢測技術。所謂全自動超音波檢測就是指將焊縫沿厚度方向分成若干個分區,每個分區用兩個通道檢測,因此要求系統是多通道。每個分區用一對或兩對聚焦探頭檢測熔合線上的缺欠,體積型缺欠用非聚焦探頭檢測。檢測結果以圖像形式顯示,分為A掃描、B掃描及TOFD(超音波衍射時差法)等3種顯示方式。掃查器在管道環向自動聲耦合、自動掃查,即可對整個焊縫厚度方向的分區進行全面檢測,自動將檢測結果和聲耦合顯示在圖像上。
全自動超音波檢測技術在西氣東輸工程上成功套用,取得良好的效果。其所用的長輸管道對接環焊縫全自動相控陣超音波檢測裝置曾經被認定為2002年度中國國家重點新產品,具有一定的先進性。為使全自動超音波檢測成功經驗得到推廣套用,中國石油天然氣管道局第一工程分公司在工程實踐基礎上,完成了《管道環焊縫相控陣全自動超音波檢測工法》。
工法特點
《管道環焊縫相控陣全自動超音波檢測工法》特點如下:
全自動超音波檢測與手動超音波檢測方法的最大區別是:用一組探頭取代單個探頭、自動化取代人工的操作、電腦採集數據,實現了自動化檢測、檢測速度快,在現場即可出檢測結果,自動記錄、自動存檔,用幾張光碟即可實現對缺欠的記錄,對危險性大的面積型缺欠敏感如裂紋、未熔合等,能夠測定缺欠的自身高度;而射線檢測對面積型缺欠不敏感,易漏檢。全自動超音波與射線檢測相比具有更低的返修率,通過斷裂力學“工程臨界分析法”(ECA)的評判標準進行評判可以減少不必要的返修。全自動超聲檢測可以緊跟自動焊焊接機組,這避免了傳統方式的“死後驗屍”式的檢測方式,可實時控制焊接過程,及時避免類似缺欠的多次發生。同時因自動化程度高,提高了工作效率,減少了人工探傷所帶來的誤操作。
操作原理
《管道環焊縫相控陣全自動超音波檢測工法》操作原理包括如下方面:
適用範圍
《管道環焊縫相控陣全自動超音波檢測工法》的適用範圍是:
1、該工法適用於利用多通道、聲聚焦、分區掃查的全自動超音波檢測系統,對壁厚為7~50毫米的鋼質石油和天然氣長輸、集輸及其他油氣管道對接環焊縫電弧焊的全自動焊焊縫的檢測。
2、該工法不適用於管徑小於150毫米的鋼質管道環焊縫的檢測。
3、該工法不適用於壁厚不一致的管道對接環焊縫。
工藝原理
《管道環焊縫相控陣全自動超音波檢測工法》的工藝原理如下:
一、系統結構
全自動超聲檢測系統由計算機系統、超聲系統和機械系統3部分組成,參見下圖: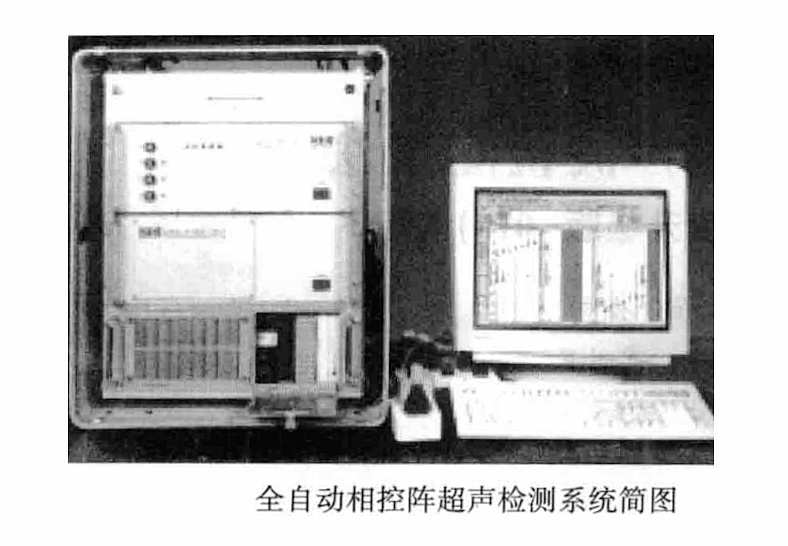
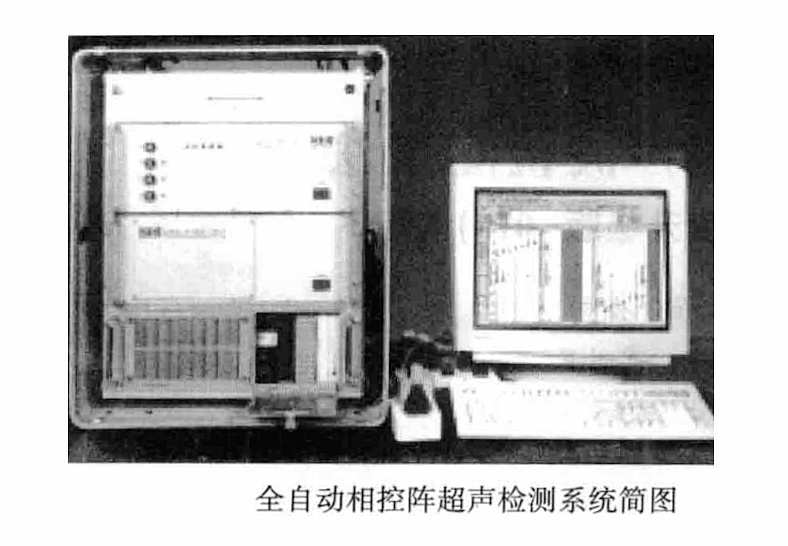
全自動相控陣超聲檢測系統簡圖
其中:
計算機系統主要包括顯示器、主機、光碟機、印表機等部件。
超聲系統主要包括同步脈衝發生器、相控陣探頭等部件。
機械系統主要包括電機、水泵、行走機構等部件。
二、檢測原理
利用超音波能在鋼材中傳播,並且超音波遇到缺欠會產生反射回波的聲學原理而實現超音波檢測的。檢測採用區域分割法,將焊縫沿厚度方向分成若干個分區,每個分區用一對或兩對聚焦探頭檢測熔合線上的缺欠,體積型缺欠用非聚焦探頭檢測,檢測結果以圖像形式顯示,分為A掃描、B掃描及TOFD等3種顯示方式(參見下圖)。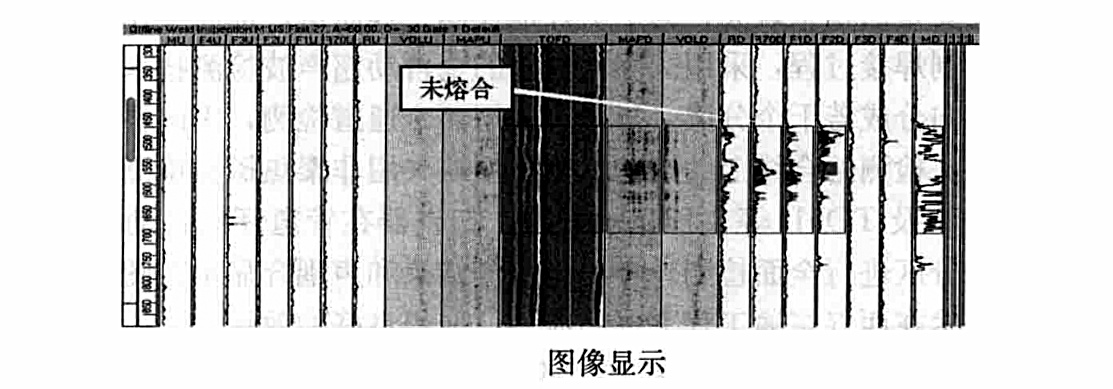
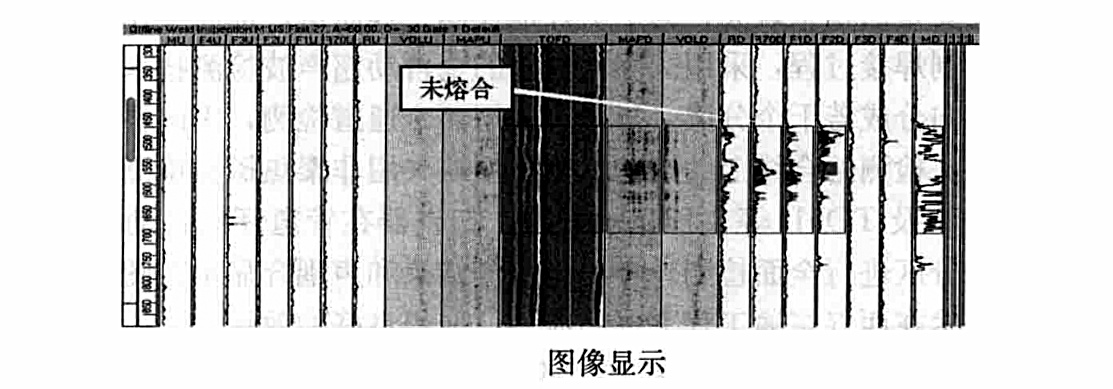
檢測圖像顯示
掃查器在管道環向自動聲耦合、自動掃查,即可對整個焊縫厚度方向的分區進行全面檢測,自動將檢測結果和聲耦合顯示在圖像上,然後再對檢測結果綜合分析、評定。
三、相控陣列
相控陣列是換能器晶片的組合,為確定不連續性的形狀,大小和方向提供出比單個或多個換能器系統更大的能力。有3種主要陣列類型:直線形、面狀(或鑲嵌式)和環形。在一個相控陣列中,規定的相位轉換是用電子系統控制並為超聲發射通向每個換能器。相控陣列除有效地控制發射的超聲束的形狀和方向外,還實現和完善了複雜的無損檢測套用要求的兩個條件:動態聚焦和實時掃描,參見下圖:

相控陣掃描圖
工藝流程
《管道環焊縫相控陣全自動超音波檢測工法》的操作工藝流程如下: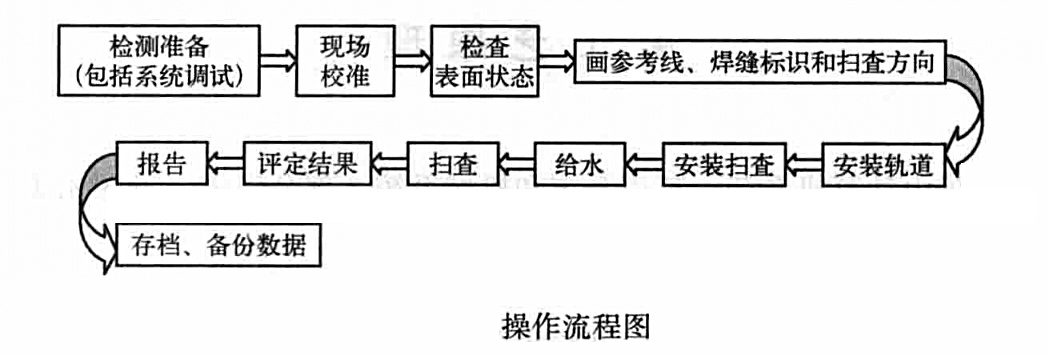
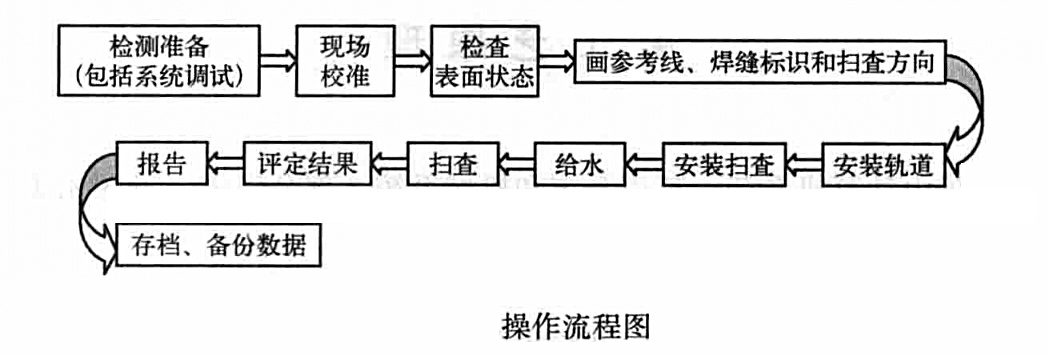
操作流程圖
操作要點
《管道環焊縫相控陣全自動超音波檢測工法》的操作要點是整個工藝流程的重點,須按如下步驟進行。
一、準備工作
1、開機前檢查各處電源電纜及信號電纜接頭是否有鬆動。
2、無論使用何種電源,啟動系統之前都應先啟動UPS,然後將轉換開關扳到UPS側,以防止突然斷電或電壓突變對系統的衝擊。
3、開水泵前,檢查水箱的水量和節流閥的位置。
二、啟動系統
首先啟動計算機系統,然後啟動超聲系統和機械系統,最後進入設定模式,再進入系統調試。
三、系統調試
系統調試在試塊上進行。系統調試分為分區調試和總體調試,在校準試塊上按如下順序進行調試:
1、分區調試
(1)參數設定
將受檢焊縫坡口參數,輸入到全自動超音波系統模擬焊縫坡口示意圖中,理論計算出選擇正確的探頭配置參數;然後將掃查器放在校準試塊軌道上,確定探頭距試塊上模擬焊縫中心線的位置,最後將探頭位置鎖緊,將其位置固定。注意探頭距焊縫中心線的距離必須準確測量,必須保證上下游端探頭距焊縫中心線距離相等。
(2)帶狀圖的調試(A掃描的調試)
探頭位置固定後,移動掃查器從根焊區開始對每個分區人工反射體(即槽或Φ2平底孔)分別調試,直到最後一個填充區為止。每個分區的靈敏度確定為人工反射體的最大波高達到滿幅度的80%,即為該區的基準靈敏度;每個區閘門起點在坡口前至少3毫米,閘門的終點至少超過焊縫中心線1毫米。注意鈍邊區設定模式要採用自收自發模式而不能採用串列掃查模式。
(3)體積通道的調試(B掃描的調試)
移動掃查器,用試塊上根部槽和61.5x45°的平底孔來調節B掃描,B掃描靈敏度確定為在人工反射體基準波高(80%)的基礎上再提高6分貝;B掃描的範圍要能滿足該通道所負責的區域,根據具體檢測對象可計算該範圍。
(4)TOFD的調試
將掃查器移動到試塊上完好部位來調節TOFD,將TOFD水平橫向縱波的幅度調節到滿幅度的50%,即為該通道靈敏度。TOFD的範圍不要過大,剛好能覆蓋水平橫向波和底面反射波為好,且不得將底面變形波包括在內。
(5)驗證帶狀圖閘門
將掃查器移動到通孔處,看帶狀圖閘門是否能將通孔覆蓋,若能,則閘門長度符合要求;若不能,則將閘門長度加長,使其覆蓋通孔。
(6)耦合通道的調試
將掃查器移動到試塊上完好部位,採用“一收一發”模式進行調節,將最大波調節到滿幅度80%,再提高6分貝,即為耦合通道的靈敏度;但現場檢測時必須在管道上重新調試耦合通道,以管道上調試為準,這樣做符合實際。注意耦合通道調試時不得使聲束的反射點處於焊縫上下表面上。要注意使探頭充水排空。
(7)溫控探頭校準
設定溫度控制探頭,隨時監測檢測溫度。
(8)編碼器校準
按儀器規定的順序進行校準編碼器。
(9)圓周掃查速度的設定
圓周掃查速度應按下式計算:
Vc ≦ Wc · PRF/3
式中:
Vc——圓周掃查速度,(毫米/秒);
Wc——探頭在檢測有效距離處的最窄聲束寬度(用半波高度法測量),(毫米);
PRF——探頭的有效脈衝重複頻率,(合資)。
(10)記錄的設定(生成視圖)
按一定順序確定通道生成視圖。每個通道的輸出信號均應在顯示器上顯示,對於每個主反射體,應在焊縫中心線兩側對稱顯示,也可用圖像(B掃描、TOFD)顯示。
2、總體調試
(1)系統參數選定後,用與現場掃查相同的速度對試塊上每個反射體進行掃查。
(2)將掃查器移到零點,開始掃查校準試塊,分析掃查記錄的試塊校準圖,看主反射體波幅是否在70~99%之間,相鄰反射體之間覆蓋是否在6~24分貝之間,若是,則可進行檢測;若不是,則重新調試,直到滿足要求為止。
(3)顯示器上顯示的編碼位置精度:記錄反射體間的顯示編碼位置相對於實際圓周位置的誤差是否為±2毫米;若不是,則對編碼器重新校準。
(4)耦合監視通道的調試,記錄系統的耦合監視通道顯示不良區域超過缺欠的最小允許長度時,應重新調試。
四、現場檢測
1、現場布置
現場校準:檢測前,將掃查器放在試塊上進行系統校準,看試塊校準圖是否滿足標準要求,若滿足,則進行檢測;若不滿足,則重新進行調試,直到滿足要求為止。
2、受檢表面狀態
檢測開始前,檢測人員必須檢查焊縫表面狀態必須滿足該工法對受檢材料的外觀要求,方可進行檢測。
(1)探頭移動區的寬度一般為焊縫兩側各150毫米範圍。
(2)焊縫兩側探頭移動區內,管子制管內外焊縫(如螺旋焊縫、直焊縫)套用機械方法打磨至與母材齊平,打磨後焊縫余高應不大於0.5毫米,且應與母材圓滑過渡。
(3)探頭移動區內不得有防腐塗層(如環氧粉末)、飛濺、鏽蝕、油垢及其他外部雜質。
3、畫參考線及焊縫檢測標識
(1)參考線是保證檢測結果的主要標識。焊接對口前,必須有專人劃參考線,參考線用於安裝掃查器軌道。在檢測之前,應在管表面畫一個參考線,參考線在檢測區一側距兩坡口中心線的距離一般不應小於40毫米,參考線位置誤差為±0.5毫米。
(2)每道焊縫應有檢測標識,在平焊位置還應有起始標記和掃查方向標記。起始標記套用“0”表示,掃查方向標記用箭頭表示,通常沿介質流動方向順時針用記號筆劃定,所有標記應對掃查無影響。注意掃查起點必須與標識原點重合。
4、軌道安裝
(1)每天應當清洗軌道的接頭,去除軌道卷邊(包括試塊上的)。
(2)安裝軌道必須由2人進行,分別位於管子兩側。
(3)安裝軌道時,調整軌道位置必須用銅錘敲擊軌道邊緣。
(4)必須將軌道安裝於距參考線130毫米處,能保證軌道邊緣距焊縫中心線距離滿足170±0.5毫米。
5、安裝掃查器
(1)注意保護好掃查器主電纜線,避免檢測過程中行車時將其壓壞。
(2)安裝掃查器應由2人進行,分別位於管子兩側。
(3)掃查器安裝完,看掃查器能否在軌道上自由移動,若能方可掃查。
(4)掃查器在軌道上運行時,若出現卡的現象,應立即按下急停鈕。
(5)掃查時,在管線兩側的操作者應當確保掃查器的安全;掃查器運動到仰臉處的時候操作者應當採取相應措施防止掃查器跌落。
(6)掃查器掃查一周后,移回到原點,由一人從一側仰臉部位推到另一側,另一個人要握住掃查器上的把手,將其移到原點。注意不得用手拽主電纜,將其移動到原點。
6、掃查
(1)由超聲Ⅱ級以上並取得專業考試的掃查員操作,由考試合格的人員承擔分析掃查數據及評定結果。
(2)掃查之前,必須先打開水泵,待水流量正常後方可以掃查。掃查前應預先潤濕受檢表面,特別是焊縫仰臉處。
(3)檢測過程每隔2小時或掃查完10道焊口後(以時間短者為準)以及檢測工作結束後,利用試塊進行校準,每個主反射的波幅應在滿幅度的70~99%之間,若滿足,則符合要求;若低於滿幅度的70%,應對其檢查的焊縫重新檢測;若高於滿幅度的99%,應對其檢測結果重新評定。
(4)圓周位置精確度的校驗
掃查器上編碼器的零點與管子上零位置重合,掃查至1/4、1/2和3/4圓周位置時,顯示器上顯示的編碼位置應與管道上的位置相對應,其誤差為±10毫米,否則應重新校準。
(5)耦合監視的校驗
在檢測過程中,記錄系統的耦合監視通道顯示不良區域超過缺欠的最小允許長度時,應對耦合不良區域及時處理重新檢測。
(6)溫差的校驗
溫度變化影響聲速變化。當探頭楔塊溫差變化超過10℃時,整個系統應重新調試,並對其檢測過的焊縫重新檢測。
7、評定結果
(1)評定由取得AUT考試資格的人員進行評定,由相應資格人員審核;對評定人員評定的結果必須重新複評一遍。評定審核後可發出檢測報告。
(2)每條焊縫掃查完後,立即評定結果。
(3)評定工藝卡。
檢測人員要根據具體的檢測對象制訂評定工藝卡。
五、報告存檔
1、報告
(1)報告作為檢測結果的永久性記錄,至少包括:工程名稱、管口編號、坡口形式、材質、規格、驗收標準、檢測人員(級別)、審核人員(級別)、檢測日期、評定結果、監理及檢測單位蓋章等,報告所要求的事項必須填寫完全、準確,必須是完全合格的報告,才能進入存檔程式。
(2)報告一式兩份,一份交給監理公司,一份檢測公司存檔。
(3)審核人員對檢測報告必須認真審核,做到準確無誤。
2、存檔
(1)超音波數據的存儲由各全自動超音波機組的機組長負責。接到監理的指令完成一天的檢測任務後,應當將硬碟內當天的檢測數據備份到可擦寫的光碟上。
(2)每一樁號的焊縫數據在該部分檢測工作完成後,統一記錄到唯讀光碟上,一式兩份保存。
(3)返修口的數據單獨備份並存儲。
(4)存儲光碟的標識,在光碟的背面寫明盤內所存數據的起止焊口編號,在光碟內應有記事本檔案記錄盤內所有焊口編號的信息。
(5)所有存儲的光碟均應填寫超聲數據存儲記錄,該記錄應與光碟一起存儲備查。
(6)掃查記錄和報告由檢測公司存檔,保存期應不少於5年。
(7)全自動超音波機組人員必須記錄操作日誌,將檢測過程中遇到的問題、校準後的靈敏度及溫差等都應記錄在操作日誌中。
六、勞動組織
(一)全自動超音波檢測人員滿足下面要求
1、檢測人員必須取得超音波無損檢測人員的資格證書,獲得Ⅱ級以上資格證書人員進行檢測,Ⅰ級人員僅做檢測的輔助工作。
2、從事全自動超音波檢測人員還應進行設備性能、調試、評定等培訓,並經理論和實際考試合格,方可從事檢測工作。
(二)人員配置
數據判讀/操作員2名(各1名),掃查員2名,力工2名,司機1名,總計7人。
材料設備
《管道環焊縫相控陣全自動超音波檢測工法》所需材料設備包括:
一、檢測材料
1、試塊
試塊的材料應取自現場管道,業主還應向檢測公司提供焊接工藝及附加要求,試塊的設計圖樣,必須經業主認可,方可製作。試塊製作後,經國家指定計量機構標定,並調試合格,方可使用。按Q/SYXQ7-2002西氣東輸管道工程管道對接環焊縫全自動超音波檢測標準要求製作的典型試塊,參見下圖:

試塊上人工反射體布置示意圖
2、軌道
軌道長度應為管道外徑(管子外徑加上兩倍的防腐層厚度)的周長。
3、其他材料
耦合劑:一般使用普通自來水即可,不能有雜質,硬度適中。冬季使用乙醇與水以適當比例混合,具體比例可以根據當地的溫度情況調整。
列印墨盒:根據印表機具體型號採用。建議使用佳能S400SP彩色噴墨印表機,該印表機具有兩種接口(USB、並行口),使用1個黑色墨盒和3個彩色墨盒,具有容量大,墨盒不帶記憶晶片,可以注墨使用的特點,日後可以節省一筆可觀的耗材費用。
列印紙:一般使用A4紙70克複印紙。
勞動保護材料可根據檢測公司和業主要求配備。
二、機具設備
1、主要設備Pipe WIZARD系統1套,包括:工業計算機1台,數據採集器1台,電機驅動控制器1台,掃查器及主電纜1套,水泵1台,其他輸入輸出設備1套。
2、工程檢測車1輛:要求可裝載整套設備和工具,裝載一定數量的耦合劑,且有獨立的供電系統(電瓶或發電機)。
3、主要工具:現場維修維護工具包1套,軌道裝卸工具1套。
質量控制
施工單位採用《管道環焊縫相控陣全自動超音波檢測工法》應遵守Q/SYXQ7-2002《西氣東輸管道工程管道對接環焊縫全自動超音波檢測標準》的相關規定。
安全措施
施工單位採用《管道環焊縫相控陣全自動超音波檢測工法》應注意實施的安全措施是:
1、需裝備通用個人防護用品,工作服、帽靴眼鏡及防水手套和圍裙(掃查員用)。
2、行車安全:用電安全及在現場對人員設備的保護為重點,關鍵要保護好主電纜。
環保措施
施工單位採用《管道環焊縫相控陣全自動超音波檢測工法》應遵守中國國家和當地的環境保護政策法規和相關規定,並制定實施具體環保措施。
效益分析
《管道環焊縫相控陣全自動超音波檢測工法》的效益分析,以西氣東輸工程1、2、15、23四個標段為例,具體情況如下:
該工程自2001年9月20日到2003年3月30日期間實際完成的工作量和工期如下:
實際工作量:14614道焊口,實際工期約12個月。
使用的設備:全自動超音波設備4台,專用工程檢測車4輛,共投資(24.5x8.3+35)x4=953.4萬元人民幣。
使用全自動超音波檢測和射線檢測費用比較,以西氣東輸工程投標價計算,全自動超音波檢測單口價為325元,射線檢測單口價為415元。
全自動超音波檢測費用:14614道x325元=474.955萬元;
射線檢測費用:14614道x415元=606.481萬元;
綜上所述,採用《管道環焊縫相控陣全自動超音波檢測工法》的檢測費用比一般射線檢測費用節約131.526萬元。
註:施工費用以2009-2010年施工材料價格計算
套用實例
《管道環焊縫相控陣全自動超音波檢測工法》套用實例概況,參見下表:
工程項目名稱 | 地點 | 開竣工日期 | 工程量 | 套用效果 | 備註 |
---|---|---|---|---|---|
西氣東輸1標段 | 新疆 | 2001年9月20日~2002年8月31日 | 約82千米, 共6862道焊口 | 很好 | 中國國內首次使用沙漠地段 |
西氣東輸2標段 | 新疆 | 2002年7月4日~2003年7月31日 | 約61千米, 共5071道焊口 | 很好 | 沙漠地段 |
西氣東輸15標段 | 陝西 | 2002年4月1日~2003年3月30日 | 約13千米, 共1055道焊口 | 很好 | 山區地段 |
西氣東輸23標段 | 安徽 | 2002年4月1日~2003年3月30日 | 約20千米, 共1626道焊口 | 很好 | 水網地段 |
榮譽表彰
2011年9月30日,中華人民共和國住房和城鄉建設部審定《2009-2010年度國家二級工法名單(升級版)》,以建質[2011]154號檔案公布,《管道環焊縫相控陣全自動超音波檢測工法》被評定為中國國家二級工法。