除了正常一次注水泥技術外,我們將不是一次通過套管內注水泥的方法均列為特殊固井技術。由於井下情況變化大,為保證注水泥質量,在水泥漿注入方法,工序、工具,工藝上有很多變化。特殊工藝固井方法主要有,大口徑深井套管固井、延遲固井技術、大斜度定向井注水泥、可溶性地層(鹽岩段)固井工藝、尾管及尾管回接固井工藝、酸性氣井或含硫氣勢注水泥、多級注水泥技術,高溫井注水泥工藝等。
基本介紹
- 中文名:特殊固井技術
- 外文名:special cementing technology
- 定義:正常一次注水泥技術外的固井技術
- 領域:石油、天然氣開採
- 分類:深井套管固井、延遲固井技術等
- 套用舉例:貴州赤水地區官渡構造的固井
簡介,技術分類,內管注水泥,尾管固井工藝,分級注水泥,我國套用實例,
簡介
在正常的井眼條件和常規注水泥作業的情況下,只要正確運用注水泥理論,遵循有關作業程式與規定,並選擇符合標準的注水泥材質,其固井質量均能得到保證。隨著鑽井領域逐步擴大,鑽遇的油氣藏類型日益增多,鑽井技術進步迅速,加之地下及地麵條件的複雜性,注水泥作業面臨更多的複雜情況和特殊條件,根據其作業特點,我們稱之為“特殊固井技術”。
技術分類
內管注水泥
內管注水泥就是當大尺寸套管下至預定深度後坐定,從套管內再下入注替水泥的內管的方法。內管注水泥適用於井比較淺且是大井眼、大尺寸套管時,尤其在沒有大尺寸膠塞時,為了防止注水泥及替鑽井液過程在管內發生竄槽、頂替鑽井液量過大、時間太長,也用於防止產生過大的上頂力。在沒得到測井的情況下,可以保證水泥返至地面。內管注水泥常用於339.7~660.4 mm的套管。
圖1 內管注水泥技術
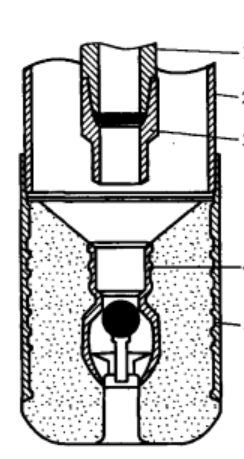
內管注水泥裝置見圖1。當套管下至預定位置後,使管柱在井口固定,一般坐定於導管上,從套管內下入鑽桿或油管,插入特製管鞋的引座內,通過鑽桿或油管注替水泥。當替鑽井液結束後上提內管,特製管鞋上的回壓閥關閉,控制套管外水泥漿倒流。
尾管固井工藝
用鑽桿把尾管管柱送到待封井段,其頂部懸掛在上一層套管內的套管柱上的固井工藝叫尾管固井。
圖2 常規尾管注水泥流程

使用尾管可以節約套管,減輕鑽機負荷和降低施工壓力,而且有利於保護油氣層,解決深井、複雜井中常規固井無法解決的技術問題。尾管固井可以降低成本,是比較受歡迎的一種完井方法,在井身結構設計上廣泛得到套用。尾管頂部為懸掛器,懸掛在上層套管內壁上,懸掛重疊長度一般在50~150 m。
一般常用的尾管柱(串)結構是:引鞋+尾管鞋+幾根套管+回壓閥+一根套管+生鐵圈+套管+尾管懸掛器+鑽桿。如果懸掛器沒有反扣倒扣裝置,懸掛器之上還應有一對正反扣接頭。
尾管固井工具主要包括:浮箍、回壓閥、膠塞、懸掛器、回接裝置、脫掛裝置、封隔器、短方鑽桿、水泥頭等。
分級注水泥
一口井的注水泥作業可分為二級或三級完成。分級箍是分級注水泥的關鍵部件,作用原理如圖3所示。分級注水泥是先注下部井段的水泥,然後再註上段的水泥。分級注水泥,可降低環空靜液柱壓力,從而不僅減少了注水泥作業發生井漏的可能性,而且降低了施工壓力,縮短了固井時間。同時還可防止或能夠減少水泥漿失重造成的油、氣、水上竄現象,有利於提高固井的質量。此外,還可選擇最佳井段進行水泥封固,節約水泥,降低固井成本,油田現場上多數採用二級注水泥。
圖3 分級箍作用原理

常用的分級注水泥工藝有三種類型:正規的非連續式的雙級注水泥、非正規連續式的雙級注水泥及三級注水泥。以下是其中兩種的介紹:
(一)正規非連續式雙級注水泥程式
圖4 非連續式正規雙級注水泥流程圖

非連續式雙級注水泥流程如圖4所示。這種方法油田現場使用得較多。具體做法是:當第一級按正常套管注水泥方法注完水泥並碰壓後,井口卸壓,證實下部浮鞋浮箍工作可靠,水泥漿不回流。再打開分級箍注水泥孔眼,可進行第二級注水泥工序。當分級箍孔眼打開恢復循環,可依據井下情況,立即或延遲開始進行第二級注水泥工作。注水泥前可調整井下鑽井液性能,按設計注入前置液及水泥漿,注水泥結束後置入關閉塞,碰壓,並且使注水泥孔永久關閉。
(二)非正規連續式雙級注水泥程式
連續式雙級注水泥程式如圖5所示。當一級水泥漿返至設計深度,按間隔量置入打開塞,隨後注入二級水泥漿。在第一級水泥漿被替到預計位置時,第二級水泥漿所推送的打開塞已打開分級箍上注水泥孔,二級水泥漿由孔返出,按間隔量隨之置入關閉塞,由此達到頂替出二級水泥漿並碰壓和關閉注水泥孔眼的目的。
圖5 非正規連續式雙級注水泥程式

非連續式與連續式在附屬檔案方面的差別主要體現在打開塞上,前者是重力式,置入後在鑽井液中以自由落體形式下落至分級箍位置,後者由水泥漿推替至分級箍位置。
我國套用實例
超高密度固井技術
貴州赤水地區官渡構造石炭系茅口組一直是受關注含氣層位,但是該地區多次鑽探嘗試都未能鑽達目的層,主要的瓶頸就是嘉陵江組的超高壓氣層或鹽水層不能克服,該層地層壓力係數達2.7以上,壓穩極為困難,尤其是固井時缺乏超高密度水泥漿。20世紀90年代在該構造有多口井鑽遇超高壓鹽水層,但由於缺乏超高密度水泥漿封固而提前完井,未達到鑽探目的。
套用緊密堆積理論,研製開發了密度範圍在2.60~3.00 g/cm3超高密度水泥漿,通過合理調配加重材料和粒度最佳化,使水泥漿的可泵性和穩定性之間得到協調統一,可實現常規工藝連續配注超高密度水泥漿。
超高密度水泥漿具有良好的綜合性能:API失水小於50 mL,高溫高壓24h抗壓強度大於14 MPa,水泥漿流動度大於21 cm,沉降穩定性小於0.03 g/cm3;整體性能滿足固井工程要求。
超高密度水泥漿體系在中國石化重點勘探井官深1井進行了套用,而此前該地區相同構造的井均因鑽遇高壓層時由於缺乏超高密度水泥漿技術而無法進行正常固井完井工作,最終被迫封井。官深1井鑽進至井深2955.34 m時,遇高壓鹽水層,後採用2.78 g/cm3鑽井液恢復鑽進至設計井深3700 m,在三開技術直徑為273.1 mm套管固井時,要求採用2.80 g/cm3水泥漿固井,隔離液、壓塞液及保護液密度均為2.75 g/cm3,固井注水泥作業共注入33 m3平均密度2.79 g/cm3的超高密度水泥漿,水泥漿最高密度2.82 g/cm3隔離液和水泥漿均創造了國內最高密度紀錄。超高密度水泥漿技術較好地解決了油氣勘探穿越超高壓層的瓶頸問題,為加快更廣泛的油氣勘探步伐提供了保障。