煉鋼脫硫反應是在煉鋼以及鋼液爐外精煉過程中脫除有害雜質硫的物理化學反應。生產低硫鋼要在高爐煉鐵、鐵水預處理、煉鋼、鋼液爐外精煉各個環節均進行認真的脫硫。還要依據產品對硫的不同要求,對整個生產流程的脫硫操作進行最最佳化控制,以使脫硫成本達到最低。
基本介紹
- 中文名:煉鋼脫硫反應
- 外文名:desulphurization in steelmaking
- 套用:鋼鐵冶煉
- 目的:脫除有害雜質硫
- 學科:冶金工程
- 類型:還原渣、氣化、氧化渣脫硫
介紹,氧化渣的脫硫,金屬成分對脫硫的影響,還原渣的脫硫,氣化脫硫,脫硫反應的速率,
介紹
在煉鋼以及鋼液爐外精煉過程中脫除有害雜質硫的物理化學反應。硫在鋼凝固時成為硫化物析出在晶粒界上,如果硫化物是FeS,其熔點為1195℃,在軋鋼時晶界熔化而鋼破裂,稱為“熱脆”。鋼中加入錳後,析出的硫化物變為MnS,熔點提高到1530℃,熱脆現象可以避免,但MnS在軋鋼時沿軋向延伸,使鋼材在橫向上失去連續性。對於條、棒類鋼材的危害還不嚴重,但對於要求各個方向的性能均為良好的板、管類鋼材,硫的危害就大了。硫還惡化鋼的韌性,圖1為德國生產的管線用鋼之含硫量隨年代的變化,與之相對應,衝擊韌性水平自然也隨著時代而提高。生產低硫鋼要在高爐煉鐵、鐵水預處理、煉鋼、鋼液爐外精煉各個環節均進行認真的脫硫。還要依據產品對硫的不同要求,對整個生產流程的脫硫操作進行最最佳化控制,以使脫硫成本達到最低。
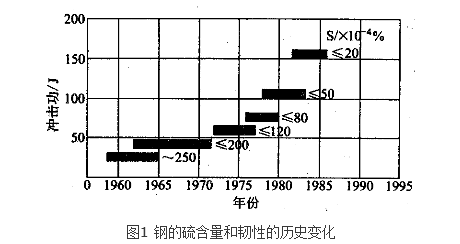
氧化渣的脫硫
脫硫以在還原條件下進行最為有利,從以下各生產環節的硫分配比可以看出:
高爐 | 鐵水預處理 | 頂吹轉爐 | 爐外精煉 | |
(%S)/[%S] | 30~40 | 400~500 | 5~8 | ~1000 |
氧化熔煉操作的轉爐煉鋼過程中硫分配比最小。然而鹼性氧化渣也有脫硫能力。對此可用爐渣離子理論清楚地說明。根據離子理論,硫在渣中以S-形態存在,鹼性氧化物分解成為O和各種金屬陽離子。鋼液中的硫吸收2個電子才能進入渣中成為S-,這是一個陰極反應。為了保持電中性,同時要有一個釋放電子的陽極反應同時發生:
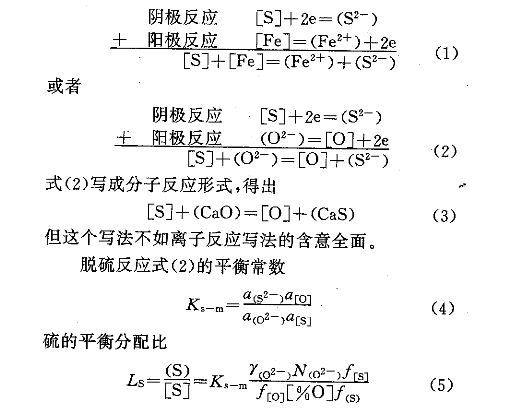
根據以上脫硫反應的特點,要想提高硫分配比,也就是增強脫硫效果,需要的基本條件有:(1)增大渣—鋼反應平衡常數Ks-m。Ks-m與溫度成正比,即脫硫是放熱反應,提高溫度有利於脫硫。(2)增大渣中O2-濃度。鹼性氧化物產生O,所以增大爐渣鹼度有利於脫硫。(3)減小鋼中氧活度。也就是說還原條件有利於脫硫,而氧化條件不利於脫硫。(4)渣中(FeO)對脫硫有雙重作用。一方面,(FeO)產生Fe2+,它們是氧化性的標誌,增大(FeO)使[%O]增加,不利於脫硫;另一方面,(FeO)又可分解產生O,對於低鹼度渣,(FeO)的有利作用可更凸顯一些。實驗室試驗表明,純氧化鐵渣和鋼液間硫分配比仍有3.6。所以說,氧化渣有一定的脫硫能力。(5)增大渣量有利於脫硫。因為大渣量可以容納較多的硫。有些煉鋼操作者為了確保鋼中硫合格,往往採取大渣量操作。然而大渣量增加了石灰消耗,也增加了鐵的損失,惡化了傳熱條件,增大能量消耗。所以大渣量是一種不應提倡的操作。
金屬成分對脫硫的影響
從式(5)可以看出,增大金屬中硫活度係數f[s]可以增大硫分配比。鋼液中各元素對f[s]的影響是不同的,根據實驗測定,增大f[s]的元素是B、C、Si、Al、P等,減小f[s]的元素有Ti、Mn、V等。生鐵中含有很多的碳和矽,所以煉鐵時硫活度係數比煉鋼時高得多。據計算,生鐵中f[s]=3~4,鋼中f[s]≈1。這就是說,使用同樣的脫硫熔劑,對生鐵脫硫比對鋼脫硫其效率要高3~4倍。鐵水預處理之所以成為非常理想的脫硫方法,這也是原因之一。
還原渣的脫硫
在電弧爐煉鋼還原期和爐外精煉時,用還原渣處理鋼液,脫硫能力顯著增大。最常用的還原渣是白渣和鋁酸鈣渣。還原渣有很強的脫硫能力,硫分配比可達50~80或更大。(FeO)對脫硫有很大影響,(FeO)由0.89%降到0.44%,硫分配比由62增大到87。還原渣脫硫同時也進行鋼液的脫氧,會使鋼中Si、Al等含量增加,它們也參與脫硫反應:
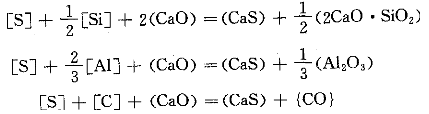
還原渣脫硫反應在爐內未達到平衡,所以在出鋼時要渣鋼混出,利用出鋼時鋼流下落的動能使渣與鋼乳化混合,促進脫硫反應的進行。
氣化脫硫
20世紀50年代,中國在側吹轉爐煉鋼中發現除了進入渣中的硫和留在鋼中的硫以外,還有一部分硫轉入氣相。而且隨著終渣氧化鐵的增高,進入氣相的硫的比例增大。王國忱對氣化脫硫問題作了詳細的研究。含硫的氣體有S2、SO2、COS、CS2等,氧化性氣氛中是SO2,還原性氣氛中是COS或CS2。在氧化熔煉中,鋼液中的硫直接被氧化成SO2而去掉是不可能的,因為在煉鋼條件下,硫對氧的親和力比碳對氧的親和力小得多。只有進入渣中的硫,在鐵離子的參與下,可能被氧化成氣體而脫除,反應如下:
6(Fe)+(S-) +2 (O-) = 6(Fe) +SO2
所以氣化脫硫的比例隨渣中氧化鐵的增大而增大。然而過高的氧化鐵意味著鐵耗增加,脫硫操作仍應以高鹼度渣脫硫為主。特別是鐵水預處理和爐外精煉的發展,有效脫硫的方法更多了,氣化脫硫並沒有特別重要的意義。
脫硫反應的速率
煉鋼脫硫是渣—鋼界面反應,反應包括3個環節:(1)鋼液中硫向界面傳質;(2)在界面上的化學反應;(3)硫在渣相內傳質離開界面。脫硫反應是電化學反應,在高溫下進行得很快,不是脫硫速率的限制環節。渣和鋼兩相中的傳質均可能是速率控制環節。根據一些人對鋼液中硫的傳質係數所作的測定,證明傳質速率決定於界面上的流動速度。流動速度越大,傳質越快。另外渣—鋼界面反應和界面積大小有關,增大界面積的有效方法是使渣、鋼乳化。電弧爐還原渣下出鋼時,增大鋼流落差,加大渣、鋼接觸,可促進脫硫的進行。鋼液爐外精煉時,必須吹氬或用電磁攪拌,才能使渣子有效脫硫。鋼包噴吹脫硫粉劑,具有極大的反應面積,脫硫速率快,是有效的脫硫方法。