液壓穿孔即穿孔機的液壓系統。
穿孔是熱軋無縫鋼管生產中最重要的變形工序之一,毛管的壁厚精度直接影響熱軋成品管的壁厚精度。在穿孔過程中,頂桿偏移、毛管甩動是引起毛管壁厚不均的主要原因。為了將頂桿準確地控制在軋制中心線上,限制毛管在軋制過程中的甩動,穿孔機後台設定有多架定心導向裝置。通過四輥定心裝置的最佳化液壓系統,高效、經濟地解決了這些問題。
基本介紹
- 中文名:液壓穿孔
- 主要包括:液壓系統
- 主要產品:穿孔機液壓系統
穿孔機四輥定心裝置液壓系統的新設計,機械方案設計,液壓系統設計,穿孔機頂桿小車液壓系統,頂桿小車液壓系統工作原理,液壓系統故障分析及排除,
穿孔機四輥定心裝置液壓系統的新設計
機械方案設計
四輥定心裝置安裝在穿孔機牌坊出口側,液壓缸的液壓驅動上下滑塊控制定心輥抱頂桿和抱毛管的位置;定心輥裝配在上下滑塊上,滑塊在機架的U型滑道里上下移動,U型滑道保證了定心輥前後左右方向的定位;液壓缸與滑塊通過球面墊撓性連線,以防止滑塊在上下移動中因摩擦力的不均衡而卡位,造成液壓缸缸桿頭部斷裂。通過調整調節限位塊2的位置來控制四輥定心裝置的毛管開口度,同時也為液壓系統2提供了校正基準。
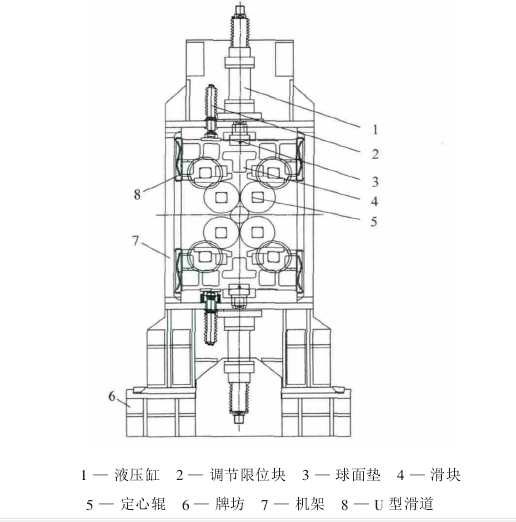
液壓系統設計
四輥定心裝置在穿孔生產中的主要作用是:
①定位頂桿,保證頂頭的穿孔中心線與軋制中心線在一條線上;
②支撐頂桿,與後台5架三輥定心裝置共同使頂桿形成一個連續的梁,保證頂桿在穿孔過程中有足夠的剛度,也使其能繞軋制中心線旋轉;
③導向毛管,毛管穿軋至四輥定心裝置時,定心輥能快速有效打開,對毛管進行導向,使毛管中心線與軋制中心線在一條線上,減小頂桿的振動。
液壓缸帶內置位移感測器與比例閥構成位置閉環控制(液壓系統1)如圖2所示,此液壓系統使四輥定心裝置能實現上述功能。
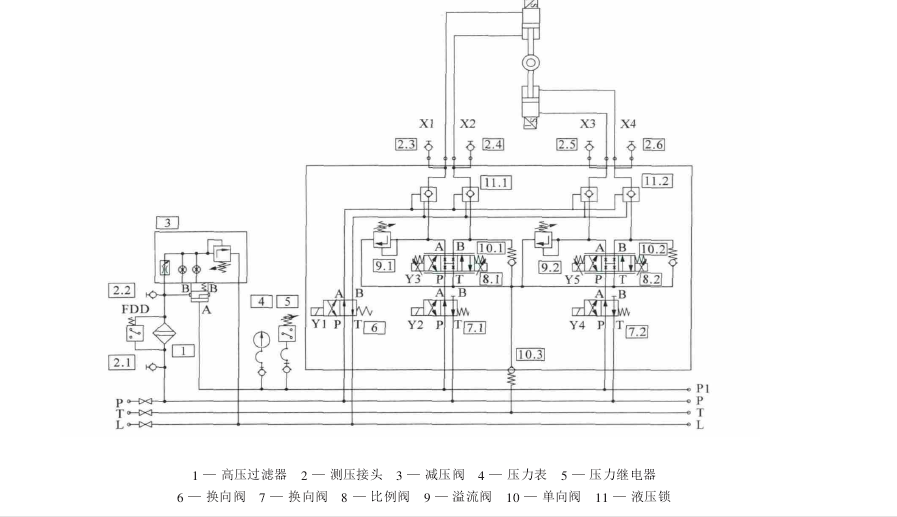
兩種液壓系統的工作原理如下。
(1)液壓系統1
通過位置閉環來實現定心輥抱頂桿位和抱毛管位。
圖2中減壓閥根據毛管和頂桿規格設定不同值,保證定心輥有足夠的力抱頂桿而又不抱死;定心輥抱毛管時壓力需切換到系統壓力,以保證其有足夠的剛度對毛管進行導向;通過位移感測器與比例閥位置閉環控制毛管開口度的大小。
(2)液壓系統2
通過串聯油缸實現上下定心輥同步動作,換向閥5.1實現定心輥的抱頂桿和抱毛管,換向閥5.2實現定心輥的修正和標定。
減壓閥1是保證定心輥有足夠的力抱頂桿又不抱死,當頂桿小車帶動頂桿(頂頭)運行至工作位Y1b得電減壓後的壓力經單向閥4、換向閥5.1、單向節流閥6.1傳入上缸上腔,由於上下液壓缸的下腔通過鋼管串接成連通體,上下缸同步運動,下缸上腔的油液回油箱,完成四輥定心裝置的同步定心;當毛管穿軋至四輥定心裝置時,熱檢發訊Y1a得電四輥定心裝置同步打開至毛管位,四輥定心裝置機架上的調節限位塊調節毛管開口度的大小。由於四輥定心裝置工作環境的惡劣、油液黏度的變化、活塞密封的老化以及管接頭液壓油的滲漏等原因會造成四輥定心裝置的不同步和累計誤差,直接影響頂桿定心不準,頂頭偏離穿軋中心線,造成毛管壁厚不均。為此設計了專門的補償修正迴路,在每次抱毛管位完成後FD2發訊Y2b得電對上下液壓缸的下腔連通體進行泄漏補償,保證每次抱頂桿都能將頂桿準確地控制在軋制中心線上。同時為了防止補償油液的擾動造成下缸的過校正,在設計液壓缸時,將上下液壓缸的上活塞桿設計為Φ110 mm,常規採用液壓系統1,但該液壓系統一次投資大、運營成本高、維修難度大,且對現場點檢人員和技術人員的水平要求高。因此採用全新的設計思路:去掉缸內位移感測器,增加兩個調節限位塊;設計出液壓系統2,常規液壓缸與常規閥構成串聯同步控制迴路(液壓系統2)如圖3所示。
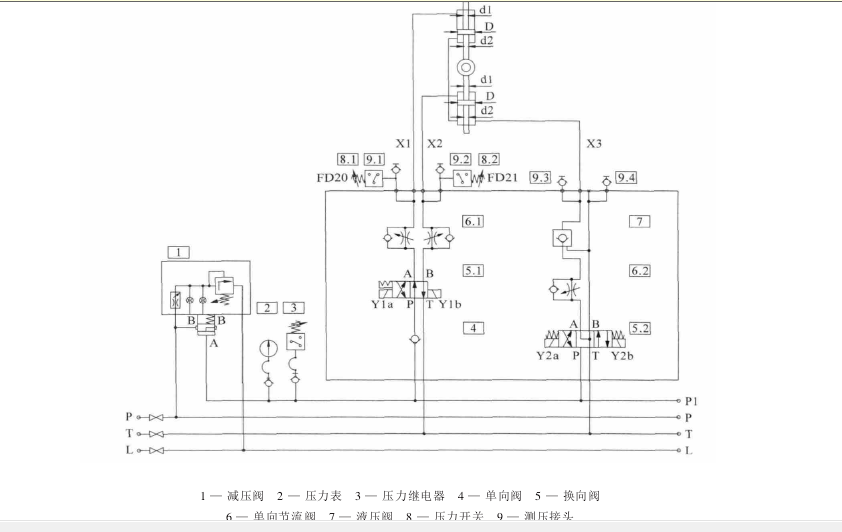
下活塞桿設計為Φ125mm,上腔面積為10603mm2,下腔面積為7834mm2,上下腔面積比1.35;同時在液壓系統上增設進油節流閥6.2,通過調節進油節流閥的開口度,進一步防止液壓油補償時的擾動,雙重保險保證了校正的準確性和可靠性。設定單向閥4可防止頂桿在穿軋過程中的不規則跳動,保證頂頭中心線與穿軋中心線在一條線上。多方面考慮的設計,保證了四輥定心裝置的準確定心和強有力的導向功能。
穿孔機頂桿小車液壓系統
頂桿小車液壓系統工作原理
驅動頂桿小車移動的擺動缸如圖4所示,4個缸筒分別為4個小柱塞缸,其中左右2個缸筒共用1個柱塞,柱塞中間位置為人字齒條,模數為2,上下兩個柱塞缸對稱,兩個人字齒同時咬合中間的齒輪,當1、4缸同時進(回)油,2、3同時回(進)油時,兩個柱塞同時反向運動,柱塞帶動中心齒輪轉動,中心軸再帶動曲臂槓桿往復動作。其液壓原理圖如圖4所示,工作過程如下。
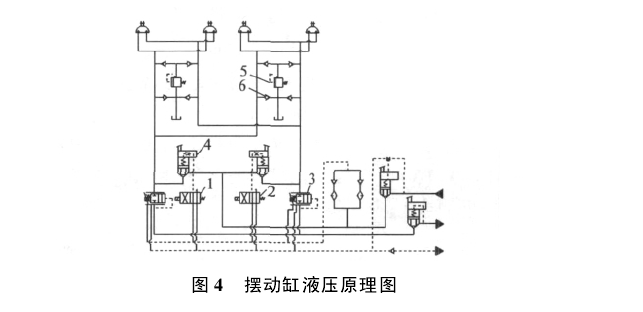
當具備軋制條件,頂桿小車前進時,控制油路的換向閥1得電,打開主迴路的插裝閥4,油液進入擺動缸2、3,同時閥3得電,擺動缸1、4的油液經由比例節流閥3回油箱,通過調整比例節流閥的輸入電流大小以控制節流閥的開口度大小,從而實現回油節流以控制頂桿小車的速度。當頂桿小車接近水平位置時,由位置感測器檢測並發出信號,改變比例節流閥的輸入電流大小,減小比例節流閥的開口度(此時比例節流閥的開口度通常為7%左右),頂桿小車改為慢速,直至到達水平位置,頂桿小車趴在水平導軌上。由於採用回油節流,快慢速轉換時,後腔(1、4缸)會產生很高的瞬時高壓,由溢流閥5溢流(調定壓力為20MPa),節流的同時又使回油腔產生背壓,用來克服頂桿小車在前進過程中曲臂越過其幾何重心後產生的負負載加速現象,同時由於負負載,供油腔產生的瞬時真空由橋式溢流迴路中的單向閥6來補油。
液壓系統故障分析及排除
擺動缸在使用過程中出現漏油現象,且漏油逐漸增大(由於更換擺動缸至少需要2h以上,一般擺動缸的漏油都是維持生產或作短封處理,等待廠里安排時間檢修更換),隨後發現穿孔機在軋鋼咬入時,頂桿小車突然抬起返回一段距離,停留在中間位置,出現類似於前卡事故(前卡為管坯未穿透而造成的穿孔機卡料事故,根據頂桿穿透的位置不同分為前卡、中卡和後卡),同時穿孔主機跳停,無法正常軋鋼,且事故連續出現。
根據以往經驗,電氣人員更換了PLC控制板,現象仍未消除,排除了電氣故障。為查找原因,現場維護人員將閥台上所有電磁鐵插頭拔掉,在不受電氣控制的情況下,發現頂桿小車在水平工作位置停穩後,約2、3s後頂桿小車曲臂慢慢拱起一小段距離,離開水平死點位置,在5°角左右的位置停止。現場運行維護人員將擺動缸兩腔管線分別接上壓力表測得當時壓力一腔由12.5MPa快速下降至0,另一腔壓力隨後由10MPa降至2.5MPa,先後更換比例節流閥和插裝閥,仍沒有效果,後調整背壓閥,勉強維持軋鋼。針對上面的故障現象,維修人員分析壓力降至為0的一腔為供油腔,此時頂桿小車在不平衡力作用下向上運動,當重新獲得平衡停止時,頂桿小車拱起約5°角的位置。頂桿小車拱起後,前台推鋼機推動管坯咬入時,由於曲臂已不在死點位置,起不到止推作用,被管坯和頂桿頂起,造成類似於前卡的是事故。此次故障中,漏油比較嚴重,後腔12.5MPa的壓力很快降為0,也就是在1、2s,壓力已低於7.5MPa,使得管坯還未咬入時,頂桿小車已經拱起。以往擺動缸漏油時,沒有發生這種現象的原因,一是漏油腔不是2、3腔,而是1、4腔,不會發生這種事故,另一種原因是雖然是2、3腔漏油,但漏油尚小,12.5MPa的壓力下降較慢,還沒有降到7.5MPa時,管坯已經咬入軋制,也不會發生這種事故。運行人員班中調整溢流閥壓力可以維持生產的原因是溢流閥的壓力由20MPa降至10MPa以下甚至更低,使得前腔的10MPa的背壓已建立不起來,這樣使得後腔還沒有降到這個數值,管坯就已經開始咬入軋制了。這樣做好像排除了故障,能維持軋鋼,但由於溢流閥壓力調低,背壓建立不起來,負負載時頂桿小車無背壓加速下降,快慢速轉換時又不能建立起瞬時高壓,起不到減速的作用,造成頂桿小車下拍嚴重,撞擊下導軌,使得缸體和曲臂受衝擊較大,很容易損壞設備,同時漏油也沒有得到很好解決,增加能耗。