簡介,用途,簡史,工作原理,工作介質,結構,驅動系統,結構型式,分類,產品用途,技術條件,成形技術,優勢,優點,工藝套用,範圍,特點,選裝配置,技術參考資料,保養制度,保養及維護,安全操作事項,二級保養,常見故障,單柱式液壓機受力分析,
簡介
液壓機(又名:
油壓機)液壓機是一種利用液體靜壓力來加工金屬、塑膠、橡膠、木材、粉末等製品的機械。它常用於壓制工藝和壓製成形工藝,如:鍛壓、衝壓、冷擠、校直、彎曲、翻邊、薄板拉深、粉末冶金、壓裝等等。
它的原理是利用
帕斯卡定律製成的利用
液體壓強傳動的
機械,種類很多。當然,用途也根據需要是多種多樣的。如按傳遞
壓強的液體種類來分,有油壓機和水壓機兩大類。
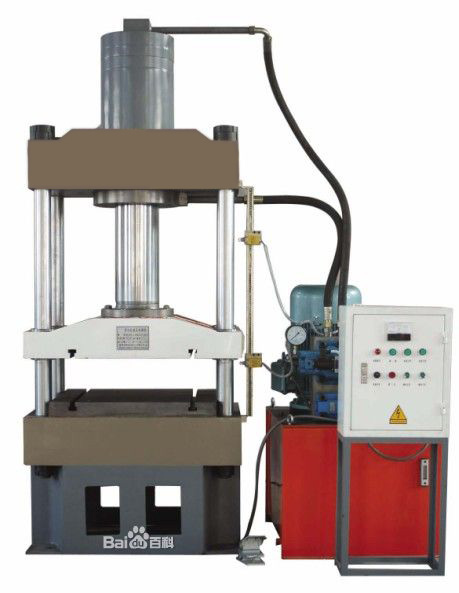
水壓機產生的總
壓力較大,常用於
鍛造和衝壓。鍛造水壓機又分為模鍛水壓機和自由鍛水壓機兩種。模鍛水壓機要用
模具,而自由鍛水壓機不用模具。我國製造的第一台萬噸水壓機就是
自由鍛造水壓機。
用途
液壓機是一種以液體為工作介質,用來傳遞能量以實現各種工藝的
機器。液壓機除用於
鍛壓成形外,也可用於矯正、壓裝、打包、壓塊和壓板等。液壓機包括
水壓機和油壓機。以水基液體為工作介質的稱為水壓機,以油為工作介質的稱為油壓機。液壓機的規格一般用公稱工作力(千牛)或公稱
噸位(噸)表示。鍛造用液壓機多是水壓機,噸位較高。為減小設備尺寸,大型鍛造水壓機常用較高壓強(35兆帕左右),有時也採用 100兆帕以上的超高壓。其他用途的液壓機一般採用 6~25兆帕的工作壓強。油壓機的噸位比水壓機低。

簡史
1795年,
英國的J.布拉默套用帕斯卡原理髮明了水壓機,用於打包、榨植物油等。到19世紀中期,英國開始把水壓機用於鍛造,水壓機遂逐漸取代了超大型蒸汽
鍛錘。到19世紀末,
美國製成126000千牛自由鍛造水壓機。此後,全世界先後製造20餘台10萬千牛級的自由鍛造水壓機,其中中國製造的有2台(見彩圖)。隨著電動高壓泵的出現和完善,鍛造水壓機也向較小噸位方向發展。20世紀50年代後出現了小型快速鍛造水壓機,可進行相當於30~50千牛鍛錘所做的工作。40年代,
德國製成180000千牛的巨型模鍛水壓機,此後全世界先後製成180000千牛以上的模鍛水壓機18台,其中中國製造的一台為300000千牛。
工作原理
液壓機的工作原理。大、小柱塞的面積分別為
S2、
S1,柱塞上的作用力分別為
F2、
F1。根據帕斯卡原理,密閉液體壓強各處相等,即
F2/
S2=
F1/
S1=p;
F2=
F1(
S2/
S1)。表示液壓的增益作用,與
機械增益一樣,力增大了,但功不增益,因此大柱塞的運動距離是小柱塞運動距離的
S1/
S2倍。
液壓機基本原理是油泵把液壓油輸送到集成插裝閥塊,通過各個單向閥和溢流閥把液壓油分配到油缸的上腔或者下腔,在高壓油的作用下,使油缸進行運動.液壓機是 利用液體來傳遞壓力的設備。液體在密閉的容器中傳遞壓力時是遵循帕斯卡定律。四柱液壓機的液壓傳動系統由動力機構、控制機構、執行機構、輔助機構和工作介質組成。動力機構通常採用油泵作為動力機構,一般為積式油泵。為了滿足執行機構運動速度的要求, 選用一個油泵或多個油泵。低壓(油壓小於2.5MP)用齒輪泵;中壓(油壓小於6.3MP)用葉片泵;高壓(油壓小於32.0MP)用柱塞泵。各種可塑性 材料的壓力加工和成形,如不鏽鋼板的擠壓、彎曲、拉深及金屬零件的冷壓成形,同時亦可用於粉末製品、砂輪、膠木、樹脂熱固性製品的壓制。
工作介質
液壓機所用的工作介質的作用不僅是傳遞壓強,而且保證機器工作部件工作靈敏、可靠、壽命長和泄漏少。液壓機對工作介質的基本要求是:①有適宜的流動性和低的可壓縮性,以提高傳動的效率;②能防鏽蝕;③有好的潤滑性能;④易於密封;⑤性能穩定,長期工作而不變質。液壓機最初用水作為工作介質,以後改用在水中加入少量乳化油而成的乳化液,以增加潤滑性和減少鏽蝕。19世紀後期出現了以礦物油為工作介質的油壓機。油有良好的潤滑性、防腐蝕性和適度的粘性,有利於改善液壓機的性能。20世紀下半葉出現了新型的水基乳化液,其乳化形態是“油包水”,而不是原來的“水包油”。“油包水”乳化液的外相為油,它的潤滑性和防蝕性接近油,且含油量很少,不易燃燒。但水基乳化液價格較貴,限制了它的推廣。
結構
驅動系統
液壓機的驅動系統主要有泵直接驅動和泵-蓄能器驅動兩種型式。泵直接驅動 這種驅動系統的泵向液壓缸提供高壓工作液體,配流閥用來改變供液方向,溢流閥用來調節系統的限定壓強,同時起安全溢流作用。這種驅動系統環節少,結構簡單,壓強能按所需的工作力自動增減,減少了電能消耗,但須由液壓機的最大工作力和最高工作速度來決定泵及其驅動
電機的容量。這種型式的驅動系統多用於中小型液壓機,也有用泵直接驅動的大型(如120000千牛)自由鍛造水壓機。
驅動系統泵-蓄能器驅動 在這種驅動系統中有一個或一組蓄能器。當泵所供給的高壓工作液有餘量時,由蓄能器儲存;而當供給量不足於需要時,便由蓄能器補充供給。採用這種系統可以按高壓工作液的平均用量選用泵和
電動機的容量,但因為工作液的壓強是恆定的,電能消耗量較大,並且系統的環節多,結構比較複雜。這種驅動系統多用於大型液壓機,或者用一套驅動系統驅動數台液壓機。
結構型式
按作用力的方向區分,液壓機有立式和臥式兩種。多數液壓機為立式,擠壓用液壓機則多用臥式。按結構型式分,液壓機有雙柱、四柱、八柱、焊接框架和多層鋼帶纏繞框架等型式,中、小型立式液壓機還有用C型架式的。C型架式液壓機三面敞開,操作方便,但剛性差。衝壓用的焊接框架式液壓機剛性好,前後敞開,但左右封閉。在上傳動的立式四柱自由鍛造液壓機中,
油缸固定在上樑中,柱塞與活動橫樑剛性連線,活動橫樑由立柱導向,在工作液的壓強作用下上下移動。橫樑上有可以前後移動的
工作檯。在活動橫樑下和工作檯面上分別安裝上砧和下砧。工作力由上、下橫樑和立柱組成的框架承受。 採用泵-蓄能器驅動的大、中型的自由鍛水壓機常採用三個工作缸,以得到三級工作力。工作缸外還設有向上施加力的平衡缸和回程缸。
結構分類
按結構形式現主要分為:四柱式、單柱式(C型)、臥式、立式框架、萬能液壓機等。
按用途主要分為金屬成型、折彎、拉伸、沖裁、粉末(金屬,非金屬)成型、壓裝、擠壓等。
大型
鍛造液壓機是能夠完成各種自由鍛造工藝的
鍛造設備,是鍛造行業使用最廣泛的設備之一。目前有800T、1600T、2000T、2500T、3150T、4000T、5000T等系列規格的鍛造
液壓機。
該液壓機適用於可塑性材料的壓制工藝。如粉末製品成型、
塑膠製品成型、冷(熱)擠壓金屬成型、薄板拉伸以及橫壓、彎壓、翻透、校正等工藝。
四柱液壓機可分為四柱兩梁液壓機、四柱三梁液壓機、四柱四梁液壓機等。
單臂液壓機(單柱液壓機)
可擴展工作範圍,利用三面空間,加長液壓缸行程(可選裝),最大可伸縮260mm-800mm,可預置工作壓力;液壓系統散熱裝置。
龍門式液壓機
可對機器零部件進行裝配、拆卸、校直、壓延、拉伸、折彎、沖孔等工作,真正實現一機多用。該機工作檯能上下移動,大小擴展了機器開合高度,使用更方便。
雙柱液壓機
本系列產品適用於各類零部件的壓裝、調彎整形、壓印壓痕、翻邊、沖孔及小零件的淺拉伸;金屬粉末製品的成型等加工工藝。採用電動控制,設有點動及半自動循環,可保壓延時,並具有良好的滑塊導向性,操作方便、易於維修、經濟耐用。根據用戶的需要可增設熱工儀表、頂出缸、行程數顯、計數等功能。
產品用途
本設備特別適合於中心載荷零件的彎曲、成型、翻邊等多種工藝,配上沖裁緩衝裝置後,還可以用於沖孔,落料加工,是船舶行業、壓力容器行業、化工等行業的首選產品。
用於金屬薄板零件的拉伸成型、翻遍、彎曲和衝壓等工藝,也可用於一般的壓制工藝,可根據用戶需要增加沖裁緩衝、打料、移動工作檯等裝置。
除了用於鍛壓成形外,三梁四柱液壓機也可用於矯正、壓裝、打包、壓塊和壓板等。
還可用於軸類零件的壓制工藝,型材的校準、扣壓、壓裝工藝以及板材零件的彎曲、爭辯、定型、壓印、套型、拉伸、可塑性材料的壓制工藝,如衝壓、彎曲、翻邊薄拉伸等作業,也可以從事校正、壓裝、塑膠製品及粉末製品的壓製成型作業。因其套用範圍廣泛也被稱為萬能液壓機.
技術條件
1.液壓機的圖樣及技術檔案的技術要求,應符合有關現行標準的規定,並應按照規定程式經過批准後,方可用於生產。
2.設計應布局合理,造型美觀,使用性能安全可靠,操縱靈敏輕便,手操縱力不大於49N(5kgf) 腳踏力不大於78?4N(8kgf)。
3.重要的導軌付及立柱、活(柱)塞等應採取耐磨措施。滑塊導軌工作而(或鋃條面)與機身 尋軌工作面應保持必要的硬度差。
4.重量超過15kg的零部件、元件或裝備等均須便於吊運和安裝,必要時應設有起吊孔或起吊 鉤(環)。
5.整體或部分包裝的油壓機及其零部件,應符合運輸和裝載的現行標準和有關規定。
6.分裝的零部件,應有相關的安裝識別標記,其中板式或管式閥等安裝時須有正確的定向措施,其中管路和液壓元件的通道口應有防塵措施。
成形技術
優勢
與傳統的衝壓工藝相比,
液壓成形工藝在減輕重量、減少
零件數量和模具數量、提高剛度與
強度、降低生產成本等方面具有明顯的技術和經濟優勢,在工業領域尤其是
汽車工業中得到了越來越多的套用。
在汽車工業及
航空、
航天等領域,減輕結構質量以節約運行中的能量是人們長期追求的目標,也是
先進制造技術發展的趨勢之一。液壓成形(hydroforming)就是為實現結構輕量化的一種先進制造技術。
液壓成形也被稱為“內高壓成形”,它的基本原理是以管材作為坯料,在管材內部施加超高壓液體同時,對管坯的兩端施加軸向推力,進行補料。在兩種外力的共同作用下,管坯材料發生塑性變形,並最終與模具型腔內壁貼合,得到形狀與
精度均符合技術要求的中空零件。
優點
對於空心變截面
結構件,傳統的製造工藝是先衝壓成形兩個半片,然後再焊接成整體,而液壓成形則可以一次整體成形沿構件截面有變化的空心結構件。與衝壓焊接工藝相比,液壓成形技術和工藝有以下主要
優點:
1. 減輕質量,節約材料。對於汽車發動機托架、散熱器支架等典型零件,液壓成形件比衝壓件減輕20%~40%;對於空心階梯軸類零件,可以減輕40%~50%的重量。
2.減少零件和模具數量,降低模具費用。液壓成形件通常只需要1套模具,而衝壓件大多需要多套模具。液壓成形的發動機托架零件由6個減少到1個,散熱器支架零件由17個減少到10個。
3. 可減少後續機械加工和組裝的焊接量。以
散熱器支架為例,散熱面積增加43%,焊點由174個減少到20個,工序由13道減少到6道,
生產率提高66%。
4. 提高強度與剛度,尤其是疲勞強度,如液壓成形的散熱器支架,其剛度在垂直方向可提高39%,水平方向可提高50%。
5. 降低生產成本。根據對已套用液壓成形零件的統計分析,液壓成形件的生產成本比衝壓件平均降低15%~20%,模具費用降低20%~30%。
工藝套用
範圍
液壓成形工藝在汽車、航空、航天和管道等行業有著廣泛的套用,主要適用於:沿構件軸線變化的圓形、
矩形或異型截面空心結構件,如汽車的排氣系統異型管件;非圓截面空心框架,如發動機托架、儀錶盤支架、車身框架(約占汽車質量的11%~15%);空心軸類件和複雜管件等。圖2即為液壓成形工藝套用於汽車工業中所製造出的一些典型零件。
液壓成形工藝的適用材料包括
碳鋼、
不鏽鋼、
鋁合金、銅合金及鎳合金等,原則上適用於冷成形的材料均適用於液壓成形工藝。主要針對汽車配件廠,電子廠,電器廠,熱處理廠,車輛配件廠,齒輪廠,空調配件廠
特點
1.按照功能和用途可得分為:
粉末成型液壓機汽車重梁液壓機非金屬專用液壓機機械修理液壓機炭素製品液壓機麿料製品液壓機陶瓷製品液壓機
2.按照類型又可分為:
3.按照噸位大小分為:
63噸液壓機 |
100噸液壓機
|
150噸液壓機
|
200噸液壓機
|
250噸液壓機 |
300噸液壓機
|
315噸液壓機
|
500噸液壓機
|
630噸液壓機 |
800噸液壓機
|
選裝配置
主要功能
防頂缸電子裝置
壓裝大型變速器齒輪及軸
校正前橋
校正變形工件
拆裝圓柱錐形軸承
吏換汽車離合器膜簧
壓裝軸承軲軸承外環
更換反作用桿橡膠總成
拆裝各種緊配合零部件
換離合器片止動銷緩衝簧
鉚、切、投後橋盆齒鉚釘
壓裝活塞銷、轉向節銷及各種銷套
主要部件採用45號整體鑄鋼並調質處理
工作檯採用活動式心盤結構
技術參考資料
公稱壓力
| kn
| 3150
|
液體最大壓力
| mpa
| 31
|
滑塊行程
| mm
| 400
|
最大開口高度
| mm
| 650
|
立柱中心距(左右×前後)
| mm
| 800×500
|
工作檯有效面積(左右×前後)
| mm
| 700×700
|
工作檯外形尺寸(左右×前後)
| mm
| 1000×700
|
工作檯高度
| mm
| 680
|
機器占地面積
| mm
| 2150×900
|
機器高度
| mm
| 2400
|
電機功率
| kw
| 11
|
保養制度
保養及維護
1.工作用油推薦採用32號、46號抗磨液壓油,使用油溫在15~60攝氏度範圍內。
2.油液進行嚴格過濾後才允許加入油箱。
3.工作油液每一年更換一次,其中第一次更換時間不應超過三個月;
4.滑塊應經常注潤滑油,立柱外表露面應經常保持清潔,每次工作前應先噴注
機油。
5.在公稱壓力500T下集中載荷最大允許偏心40mm。偏心過大易使立柱拉傷或出現其它不良現象。
6.每半年校正檢查一次壓力表;
7.機器較長期停用,應將各加部位表面擦洗乾淨並塗以防鏽油。
安全操作事項
1.不了解機器結構性能或操作程式者不應擅自開動機器;
2.機器在工作過程中,不應進行檢修和調整模具;
3.當機器發現嚴重漏油或其它異常(如動作不可靠、噪聲大、振動等)時應停車分析原因,設法排除,不得帶病投入生產:
4.不得超載或超過最大偏心距使用:
5.嚴禁超過滑塊的最大行程,模具閉合高度最小不得小於600mm。
二級保養
1.工具機運行5000小時進行二級保養。以維修工人為主,操作工人參加。除執行一級保養內容外應做好下列工作,並測繪易損件。提出備品配件。
2.首先切斷電源進行保養工作。(見下表)
序號 保養部位 保養內容及要求
一 橫樑立柱導軌 1.檢查、調整排掛橫樑平面、立柱導軌、導套、滑塊、壓板,使之達到運動平穩,符合工藝要求。
2.修復或更換缺損零件。
二 液壓潤滑 1.拆洗、檢修電磁閥,研磨閥門,閥芯。
2.清洗檢查油泵油缸柱塞修光毛刺,更換油封
3校驗壓力表
4.修復或更換嚴重磨損零件
5.開車檢查各油缸、柱塞運行平穩,無爬行。支持閥能使活動橫樑準確停在任何位置,壓力降滿足工藝要求。
三 電器 1.清洗電動機,檢查軸承,更新潤滑脂
2.修復或更換損壞元件。
3.電器符合設備完好標準要求。
四 精度 1.校準工具機水平,檢查調整修復精度。
2.精度符合設備完好標準要求。
液壓機的保養和維護還是需要專人、專業、專職的去維護,這樣才可以用的時間更久些!
常見故障
金屬擠壓液壓機運行中,有時會有螺栓脫落,掉入液壓缸內對柱塞壁造成嚴重劃傷。問題出現後,傳統方法根本無法實現現場修復,只能是拆卸後運往生產廠家進行補焊加工或報廢更換。由於沒有備件更換,重新生產配件或返廠維修時間無法掌控,長時間停機給企業造成嚴重經濟損失,同時還要支付高額的加工或修復費用。為了滿足企業連續化生產的要求,需要找到方便快捷、簡單有效的維修手段來解決該設備問題,最大程度減少企業的停機停產時間並降低維修維護費用。可以採用高分子複合材料的方法進行現場修復
操作步驟:
1.用氧-乙炔火焰烤劃傷部位(掌握溫度,避免表面退火),將常年滲金屬表面的油烤出來,烤到沒有火花四濺。
2.將劃傷部位用角磨機表面處理,打磨深度1毫米以上,並沿缸筒外壁打磨出溝槽,最好是燕尾槽。劃傷兩端鑽孔加深,改變受力情況。
3.用脫脂棉蘸丙酮或無水乙醇將表面清洗乾淨。
4.將調和均勻修復材料塗抹到劃傷表面;第一層要薄,要均勻且全部覆蓋劃傷面,以確保材料與金屬表面最好的粘接,再將材料塗至整個修復部位後反覆按壓,確保材料填實並達到所需厚度,使之比缸筒外壁表面略高。
5.材料在24℃下完全達到各項性能需要24小時,為了節省時間,可以通過鹵鎢燈提高溫度,溫度每提升11℃,固化時間就會縮短一半,最佳固化溫度70℃。
6.材料固化後,用細磨石或刮刀,將高出缸筒外壁表面的材料修復平整,施工完畢。
單柱式液壓機受力分析
單柱式液壓機機架可按其對稱面簡化為平面機架,其受力簡圖可堪稱平面曲桿和直桿的組合,如圖所示。
曲桿O-O部分主要受軸向力和彎矩的作用,剪力可忽略不計。根據曲桿的計算公式,在O-O段任一截面(由角度θ定)的彎矩M及軸向力N分別為
M=P(l+rcosθ)N=Pcosθ
對於直桿部分(見圖2-72中O-B段)
M=P(l+r)
N=P
單柱式液壓機受力分析圖