沸騰床加氫的特點
在重渣油加氫體系中,沸騰床是由氣、液、固構成的三相反應系統,其中氣相主要為氫氣和部分烴蒸汽;液相為烴原料未蒸發的重組分;固相為設計獨特的催化劑,其在反應時處於流化態。沸騰床反應器的結構如圖1所示。
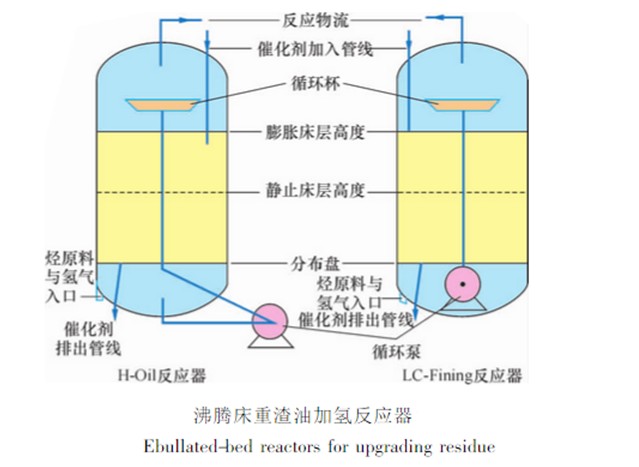
圖1
原理
沸騰床反應器的催化劑通常為擠壓物,活性組分為鎳-鉬或鎳-鈷金屬。反應器中的催化劑由液體反應物和富氫氣體向上提升而處於流化狀態,原料油和氣體進入反應器內經分配器在反應器催化劑床層進行重新分配。
沸騰床反應器中的催化劑床層高度由循環液體流速控制。液體流速可以通過改變循環泵的轉速來調節。沸騰狀態的操作方式可以降低反應器的壓力降,混合效果好,床層接近等溫操作。因此,沸騰床反應器的操作類似於
連續攪拌釜式反應器(CSTR)。沸騰床技術使用線上加排系統,新鮮催化劑可以不斷地加入反應器,待生催化劑可以不斷從反應器排出,從而保持反應器催化劑的活性穩定。沸騰床反應系統的運轉時間與催化劑活性無關,而是與反應生成物中的沉積物量有關,一般沉積物量限制在0.8%~1.0%。
沸騰床反應器結構
國外H-Oil工藝和LC-Fining工藝的反應器結構基本相同,反應器的技術核心包括流體分布系統、分離循環系統和催化劑的線上加排系統,其中流體分布系統主要包括流體預分配器和分布盤,它可使氣液流體均勻進入反應器的催化劑床層;而分離循環系統主要由循環杯、下導管和循環泵構成,用於氣液分離和提供床層膨脹的循環液體;線上加排系統主要用於新鮮催化劑的線上加入和待生催化劑的線上排出。這兩種工藝的主要區別在於H-Oil技術使用外置的高壓循環泵,為外循環操作方式;而LC-Fining技術將循環泵內置反應器底部,為內循環操作方式。如圖2所示。
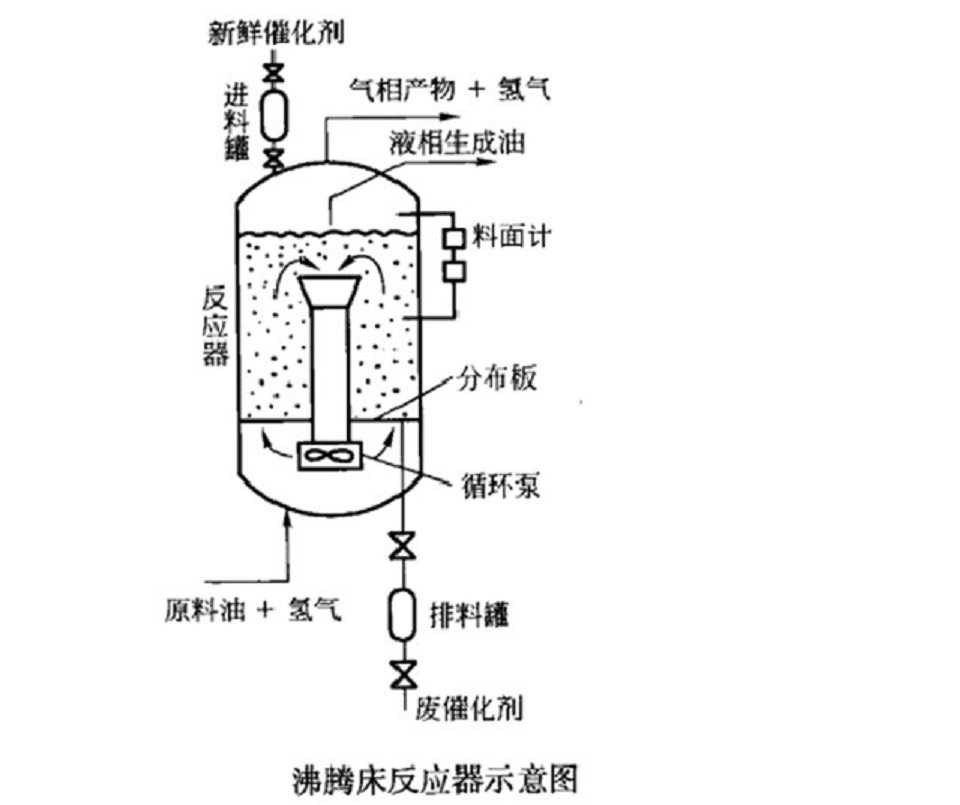
圖2
1、流體分布系統
流體分布系統主要包括流體預分配器和分布盤。流體預分配器位於沸騰床反應器底部的高壓室中,分布盤將高壓室和裝有催化劑的有效沸騰床反應區隔開。反應器流體分布設計不合理將造成操作困難,如高壓室結焦、流體在催化劑床層分布不均、局部沸騰床層出現塌陷、催化劑床層有焦炭生成等。這些問題將縮短催化劑壽命,導致裝置頻繁停工,縮短正常的操作時間。
(1)流體預分配器
流體預分配器設定在沸騰床的高壓室中,由帶有至少兩個擋板的環形噴嘴構成,擋板與流體流動方向垂直,最靠近反應器內部的擋板是實心板,其他的擋板中央開口,擋板之間彼此平行且有一定間距,擋板與噴嘴的中心線成45°~90°,設定這些擋板可以使液體物流呈放射狀進入高壓室,以便液體物流與氣體均勻混合。在通常的重質油改質工藝中,流體經過帶有擋板的噴嘴分布器的壓力降為流體經預分配器和分布盤總壓力降的5%~25%。如果液體直接注入高壓室會形成滯留區,而高壓室沒有催化劑並且液體溫度很高則容易結焦。而採用帶擋板的噴嘴可以使氣液充分混合,並且液體以放射狀進入高壓室,可以增強高壓區的返混效果,不易形成滯留區,從而避免結焦。
(2)分布盤
沸騰床反應器的分布盤位於高壓室上部,分布盤將高壓室與裝有沸騰床催化劑的有效反應區
分開。分布盤上有許多帶有泡帽的孔,類似於蒸餾塔中使用的分布盤,但它需經特殊改造後才能用於沸騰床反應器。分布盤上的泡帽數根據泡帽直徑、泡帽間距、分布盤直徑和循環管線下導管直徑來估算和設計。經分布盤的流體壓力降為20~35kPa。使用多段分布盤,可以實現進入沸騰床反應器的氣液均勻分布。多段分布盤包括由覆蓋泡帽的多個流體管組成的上部主分布盤和由多個流體管構成的下部次分布盤。分布盤不但能保證貫穿整個反應器橫界的油和氣分布均勻,也可以防止催化劑落入反應器底部的高壓區。
2、分離循環系統
分離循環系統主要由循環杯、下導管和循環泵構成。
(1)循環杯
循環杯用於氣液分離,它將循環回反應器的氣體量降到最低。循環杯包括帶有內部螺旋狀膜的提升管,沿反應器軸向上升的氣液混合物通過提升管時,混合物流速瞬間增大,而當氣液混合物從提升管上部流出後,由於流體流經橫截面積驟然增大,液體與氣體的流速差顯著增加,從而有利於氣液分離。提升管的下端低於反應器液面高度。氣體通過循環杯後升至反應器頂部,部分液體經下導管循環回反應區。液體經循環迴路與新鮮原料和氫氣混合進入沸騰床反應器,其餘的液體從反應器排出作為液體產品。
當反應器中的液面高度低於循環杯頂部時,物流不能經過循環杯、下導管、提升管、泡帽和反應區進行循環,這將導致液體滯留,出現過熱點,帶來操作問題。使用浮動的循環杯可以避免循環液體量不足、設備和催化劑受損進而造成加氫裝置停工和下游設備操作不平穩等問題。
(2)下導管
下導管是反應器內等徑拉長的流體返回管線。它上端與循環杯相連,下部與循環泵相連。當反應器內的液面高度低於下導管的頂部開口時,液體無法進入循環泵,沿著下導管的長度方向設定多個孔可以解決這一難題。
(3)循環泵
循環泵使沸騰床反應器的液相物流從循環杯經下導管和分布盤循環。循環泵提供足夠的循環量將初始固定的催化劑床層提升和膨脹成沸騰狀。循環泵是箱式馬達泵,它將離心泵和籠式誘導發動機結合到單個密封裝置中。循環流體系統改進後使箱式馬達泵適用於輸送538℃含有蒸汽和固體的液體。
沸騰床反應器由於設有線上加排系統,具有廣泛的原料適應性,產品性質穩定並能實現長周期運轉。催化劑的線上加排系統包括催化劑線上加入系統和催化劑線上排出系統。
(1)催化劑線上加入系統
催化劑線上加入系統通常包括催化劑加料漏斗,催化劑加料罐、連線管線和閥門,其中催化劑加料漏斗經管線與催化劑加料罐相連,加料罐的頂部設有放空閥和氫氣加壓閥,催化劑加料罐經催化劑加料管線與反應器相連,在催化劑加料管線上裝有一個或多個閥門,該管線還與引入
惰性氣體的管線相通,催化劑加料管線深入到反應器內部,其末端位於反應器液面下方和沸騰狀的催化劑床層上方。當需要將新鮮催化劑加入反應器時,首先關閉催化劑加料罐與反應器之間的閥門,然後打開放空閥將加料罐放空,經惰性氣體引入管線將氮氣引入到催化劑加料罐中,除去殘餘的氫氣,氮氣吹掃結束後,關閉放空閥和氮氣吹掃閥,採用氣體傳輸或液體傳輸或靠重力作用將加料漏斗中的新鮮催化劑經管線加入到催化劑加料罐中,然後關閉管線上的閥門,經氫氣加壓閥向催化劑加料罐充入氫氣,使得催化劑容器中的壓力基本等於反應器壓力。然後打開催化劑加料罐與反應器連線管線的閥門,使得催化劑靠重力進入反應器。
(2)催化劑線上排出系統
催化劑線上排出系統包括待生催化劑排出罐、連線管線及閥門。待生催化劑排出罐經催化劑排出管線與反應器的底部相連,管線上設有一個或多個閥門。伸入待生催化劑容器的管線長度最好為整個容器高度的15%~40%。在待生催化劑排出罐的上部設有能通入高壓蒸汽、惰性氣體及高壓清潔油的閥門,在容器下部設有排放閥。從反應器排放待生催化劑前,先關閉反應器底部和待生催化劑排放罐連線管線上的閥門,然後將待生催化劑上部的高壓清潔油閥門打開,將罐中充滿與反應液體相溶的液相物質,該液體可為室溫或加熱到93℃,隨後往排出罐中吹入氮氣等惰性氣體,以除去殘餘的氧氣,再打開高壓氫氣閥門向罐內充入氫氣至反應壓力,打開反應器底部與待生催化劑排出罐相連管線上的閥門,待生催化劑由於重力作用從反應器底部進入待生催化劑排出罐,同時容器中等體積的液體向上流入反應器,在此過程中,熱的催化劑顆粒與冷液體逆流接觸,上升流體冷卻催化劑。待生催化劑進入待生催化劑排出罐,
直至其充滿並逐漸在管線中累積。當管線和容器都充滿催化劑時,經高壓清潔油閥門向排出罐中加入高壓液體油將待生催化劑管線中的
固體催化劑顆粒反衝入沸騰床反應器中,同時清洗管線及管線上的閥門,然後迅速關閉閥門。將待生催化劑排出罐卸壓至常壓,放空罐中含有的油氣。將氮氣等惰性氣體引入罐中除去剩餘的氫氣後,打開待生催化劑底部的閥門放出催化劑和攜帶的液體。應注意待生催化劑與反應器液體之間的密度差應該控制在320.4~961.1kg/m。
反應器的優點和缺點
沸騰床加氫反應器由於其獨特的結構和操作模式使其具有如下優點:
①操作靈活,可以在高或低轉化率下操作;
②可以周期性地從反應器中回收或添加催化劑,在不停工的情況下可以保持催化劑的反應活性;
③通過循環泵使催化劑床層膨脹30%~50%,保證催化劑固體顆粒之間有足夠大的自由空間;可以避免由原料夾帶或反應過程產生的固體微粒在穿越催化劑床層過程中產生累積、床層堵塞或床層壓力降增加的問題;
④使用小粒徑催化劑能顯著降低擴散的限制,提高了反應速率,也不易發生金屬沉積堵塞催化劑孔道的情況;
⑤良好的熱轉移,使催化劑床層的過熱最小化,並能減少焦炭形成;
⑥沸騰床反應器近似於等溫操作,在工業化的沸騰床裝置中,反應器中任何兩點的溫度差都低於5℃,可以避免局部過熱。
但國外的沸騰床加氫反應器也存在如下缺點:
①沸騰床為全返混反應體系,與固定床的活塞流反應體系相比,轉化率低,這可以通過將幾個沸騰床反應器串聯得到部分改善;
②催化劑易發生磨損,所以要求催化劑必須具有較強的機械穩定性和抗磨損能力;
③由於沸騰床使用較小尺寸的催化劑顆粒,並且反應器中催化劑的固含率較低,使得沸騰床反應器的體積大於固定床和移動床的反應器;
④催化劑消耗量較大;
⑤需要密切監測反應器停滯區域,阻止該區域的擴大,它會導致操作不穩定;
⑥沸騰床反應通常在高溫下操作,所以容易形成沉積物;
⑦沸騰床反應器的設計和工業放大要比其他反應器更加困難,因為這涉及多種因素:原料組成、催化劑性質、催化作用和反應動力學、流體力學、催化劑小球與床層之間的熱量和質量傳遞等。