為了滿足設計、製造、維修和普及的需要,在輸入代碼、坐標系統,加工指令、輔助功能及程式格式等方面,國際上已經形成了兩種通用的標準,即國際標準化組織(ISO)標準和美國電子工業學會(EIA)標準。數控加工程式是由各種功能字按照規定的格式組成的。正確地理解各個功能字的含義,恰當的使用各種功能字,按規定的程式指令編寫程式,是編好數控加工程式的關鍵。
基本介紹
- 中文名:數控程式
- 外文名: NC program
概述
數控編程人員必須掌握與數控加工相關內容的知識,包括數控加工原理、數控工具機及其原理、工具機坐標系,數控程式結構和常用數控指令等。
數控加工工藝分析和規劃將影響數控加工的加工質量和加工效率,因此,數控加工工藝分析和規劃是數控編程的核心內容。主要包括有加工區域的劃分和規劃,刀軌形式與走刀方式的選擇,刀具及機械參數的設定和加工工藝參數的設定。
分類
手工編程是編程員直接通過人工完成零件圖工藝分析、工藝和數據處理、計算和編寫數控程式、輸入數控程式到程式驗證整個過程的方法。手工編程非常適合於幾何形狀不太複雜、程式計算量較少的零件的數控編程。相對而言,手工編程的數控程式較短,編製程序的工作量較少。因此,手工編程廣泛用於形狀簡單的點位加工和直線、圓弧組成的平面輪廓加工中。
自動編程是一種利用計算機輔助編程技術的方法,它是通過專用的計算機數控編程軟體來處理零件的幾何信息,實現數控加工刀位點的自動計算。對於複雜的零件,特別是具有非圓曲線曲面的加工表面,或者零件的幾何形狀並不複雜,但是程式編制的工作量很大,或者是需要進行複雜的工藝及工序處理的零件,由於這些零件在編製程序和加工過程中,數值計算非常繁瑣,程式量很大,如果採用手工編程往往耗時多、效率低、出錯率高,甚至無法完成,這種情況下就必須採用自動編程。
現在廣泛使用的自動編程是CAD/CAM圖形互動自動編程,CAD/CAM圖形自動編程系統的特點利用CAD軟體的圖形編輯功能將零件的幾何圖形繪製到計算機上,在圖形互動方式下進行定義、顯示和編輯,得到零件的幾何模型;然後調用CAM數控編程模板,採用人機互動的方式定義幾何體、創建加工坐標系、定義刀具,指定被加工部位,輸入相應的加工參數,確定刀具相對於零件表面的運動方式,確定加工參數,生成進給軌跡,經過後置處理生成數控加工程式。整個過程一般都是在計算機圖形互動環境下完成的,具有形象、直觀和高效的優點。
基本結構
程式編號: 001
程式內容: N001 G92 X40.0 Y30.0 ;
N002 G90 G00 X28.0 T01 S800 M03 ;
N003 G01 X-8.0 Y8.0 F200 ;
N004 X0 Y0 ;
N005 X28.0 Y30.0 ;
N006 G00 X40.0 ;
程式結束段: N007 M02 ;
(1)程式編號
採用程式編號地址碼區分存儲器中的程式,不同數控系統程式編號地址碼不同,如日本FANUC6數控系統採用o作為程式編號地址碼;美國的AB8400數控系統採用P作為程式編號地址碼;德國的SMK8M數控系統採用%作為程式編號地址碼等。
(2)程式內容
程式內容部分是整個程式的核心,由若干個程式段組成,每個程式段由一個或多個指令字構成,每個指令字由地址符和數字組成,它代表工具機的一個位置或一個動作,每一程式段結束用“;”號。
(3)程式結束段
以程式結束指令M02或M30作為整個程式結束的符號。
程式段格式
一個完整的數控加工程式是若l幹個程式段組成的。程式段格式:指程式段中的字、字元和數據的安排形式。
字地址可變程式段格式:每個字長不固定,各個程式段中的長度和功能字的個數都是可變的。
地址可變程式段格式中,在上一程式段中寫明的、本程式段里又不變化的那些字仍然有效,可以不再重寫。這種功能字稱之為續效字。
一般格式為:
(1)程式開始符、結束符
程式開始符、結束符是同一個字元,ISO代碼中是%,EIA代碼中是EP,書寫時要單列一段。
(2)程式名
程式名有兩種形式:一種是英文字母O和1~4位正整數組成;另一種是由英文字母開頭,字母數字混合組成的。一般要求單列一段。
(3)程式主體
程式主體是由若干個程式段組成的。每個程式段一般占一行。
(4)程式結束指令
程式結束指令可以用M02或M30。一般要求單列一段。
加工程式的一般格式舉例:
% // 開始符
O1000 // 程式名
N10 G00 G54 X50 Y30 M03 S3000
N20 G01 X88.1 Y30.2 F500 T02 M08 // 程式主體
N30 X90
……
N300 M30 // 結束符
%
N30 G01 X88.1 Y30.2 F500 S3000 T02 M08
N40 X90(本程式段省略了續效字“G01,Y30.2,F500,S3000,T02,M08”,但它們的功能仍然有效)
在程式段中,必須明確以下幾點的對應關係:
移動目標:終點坐標值;
沿怎樣的軌跡移動:準備功能字;
進給速度:進給功能字F;
切削速度:主軸轉速功能字S;
使用刀具:刀具功能字T;
工具機輔助動作:輔助功能字M。
分隔設定固定順序程式段格式
這種程式段格式是在字與字之間用分隔設定“HT”(在EIA代碼中用TAB)隔開,而且預先規定了代碼字的順序,因此,根據分隔設定出現的順序,就可判定其功能。不需要的字以及本段程式內與上一段程式內的相同功能的字可省略,但其相應的分隔設定必須保留,如下列程式所示。由此可見,這一格式不直觀,編程不方便,現已基本上不採用。
00l HT 3162 HT 1630 HT2 HT6 HT1 LF
002 HT 12365 HT HT HT HT LF
003 HT 3162 HT 28621HT 1 HT 5 HT 0 LF
常用指令
1、坐標字:用來設定工具機各坐標的位移量由坐標地址符及數字組成,一般以X、Y、Z、U、V、W等字母開頭,後面緊跟“+”或“-”及一串數字。該數字一般以脈衝當量為單位,不使用小數點,如果使用小數表示該數,則基本單位為mm。
2、準備功能字(簡稱G功能):指定工具機的運動方式,為數控系統的插補運算作準備,由準備功能地址符“G”和兩位數字所組成,G功能的代號已標準化,一些多功能工具機,已有數字大於100的指令。
常用G指令:坐標定位與插補;坐標平面選擇;固定循環加工;刀具補償;絕對坐標及增量坐標等。
3、進給功能字:指定刀具相對工件的運動速度,進給功能字以地址符“F”為首,後跟一串字代碼,單位mm/min,在進給速度與主軸轉速有關時,如進行車螺紋、攻絲或套扣等加工時,使用的單位還可為mm/r。
三位數代碼法:F後跟三位數字,第一位為進給速度的整數位數加“3”,後二位是進給速度的前二位有效數字。如1728mm/min指定為F717。
二位數代碼法:F後跟二位數字,規定了與00—99相對應的速度表,除00與99外,數字代碼由01向98遞增時,速度按等比關係上升,公比為1.12。如F21速度11.2mm/min,F54速度500mm/min。
一位數代碼法:對速度檔較少的工具機F後跟一位數字,即0—9來對應十種預定的速度。
直接指定法:在F後按照預定的單位直接寫上要求的進給速度。
4、主軸速度功能字:指定主軸旋轉速度,以地址符S為首,後跟一串數字。 數字的意義、分檔方法及對照表與進給功能字通用,只是單位為:r/min。
5、刀具功能字:當系統具有換刀功能時,刀具功能字用以選擇替換的刀具,以地址符T為首,其後一般跟二位數字,該數代表刀具的編號。
6、輔助功能字:用於工具機加工操作時的工藝性指令,以地址符M為首,其後跟二位數字(M00—M99),常用M指令:主軸的轉向與啟停;冷卻液的開與停;指定機械的夾緊與鬆開;指定工作檯等的固定直線與角位移;說明程式停止或紙帶結束等。
7、模態指令和非模態指令:G指令和M指令均有模態和非模態指令之分。
模態指令:也稱續效指令,按功能分為若干組,表2第2列中標有相同字母的為同組。模態指令一經程式段中指定,便一直有效,直到出現同組另一指令或被其他指令取消時才失效,與上一段相同的模態指令可省略不寫。
非模態指令:非續效指令,僅在出現的程式段中有效,下一段程式需要時必須重寫(如G04)。
例如:
N001 G91 G01 X10 Y10 Z-2 F150 M03 S1500;
N002 X15;
N003 G02 X20Y20I20 J0;
N004 G90 G00 X0 Y0 Z100 M02;
說明:
1)第一段出現三個模態指令G91、G01、M03,因他們不同組而均續效,其中G91功能延續到第四段出現G90時失效;G01功能在第二段中繼續有效,至第三段出現G02時被取消;M03功能直到第四段M02生效時才失效。
2)表2第(3)欄有“*”和表3第(5)欄有“*”者為非模態指令,其功能僅在出現的程式段中有效。
3)表3第(2)欄有“*”的M指令,其功能與同段其他指令的動作同時開始。表3第(3)欄有“*”的M指令,其功能與同段其他指令動作完成後才開始。
標準代碼
1、字元與代碼
字元:用來組織、控制或表示數據的一些符號,如數字、字母、標點符號、數學運算符等。數控系統只能接受二進制信息,用“0”和“1”組合的代碼來表達。國際上廣泛採用兩種標準代碼:
(1)ISO國際標準化組織標準代碼
(2)EIA美國電子工業協會標準代碼
在現代大多數數控工具機上這兩種代碼都可以使用。數控工具機的零件加工程式,可通過撥碼盤、鍵盤、穿孔紙帶、磁帶及磁碟等介質輸入數控裝置中,
ISO代碼為補偶代碼。ISO代碼最多能表示的字元個數為2的7次方,等於128。
EL4代碼為補奇代碼。在EIA代碼中,每行代碼孔的個數為奇數;EIA代碼最多能表示的字元個數為2的6次方等於64。
從以上對兩種代碼的比較可知,ISO代碼具有信息量大、可靠性高等優點,所以目前世界各國都采ISO代碼;但由於EIA代碼發展較早,已有的數控工具機中,有一些採用的是EIA代碼,也有一些工具機既可用ISO代碼又可用EIA代碼。現在我國規定新產品一律採用BO代碼。
2、字
字:指一系列按規定排列的字元,作為一個信息單元存儲、傳遞和操作。由一個英文字母與隨後的若干位十進制數字組成。這個英文字母稱為地址符。
如:“X2500”是一個字,X為地址符,數字“2500”為地址中的內容。
3、字的功能
組成程式段的每一個字都有其特定的功能含義,以下是以FANUC-0M數控系統的規範為主來介紹的,實際工作中,請遵照工具機數控系統說明書來使用各個功能字。
(1) 順序號字N
順序號字:又稱程式段號或程式段序號。順序號位於程式段之首,由順序號字N和後續數字組成。順序號字N是地址符,後續數字一般1~4位正整數。順序號實際上是程式段的名稱。數控系統不是按順序號的次序來執行程式,而是按照程式段編寫時的排列順序逐段執行。
順序號的作用:
對程式的校對和檢索修改;
作為條件轉向的目標,即作為轉向目的程式段的名稱。
有順序號的程式段可以進行復歸操作,這是指加工可以從程式的中間開始,或回到程式中斷處開始。
一般使用方法:編程時將第一程式段冠以N10,以後以間隔10遞增的方法設定順序號,這樣,在調試程式時如果需要在N10和N20之間插入程式段時,就可以使用N11、N12。
(2)準備功能字G
準備功能字的地址符是G,又稱為G功能或G指令,是建立工具機或控制系統工作方式的一種指令。後續數字一般1~3位正整數。
尺寸字用於確定工具機上刀具運動終點的坐標位置。
第一組 X,Y,Z,U,V,W,P,Q,R 用於確定終點的直線坐標尺寸;
第二組 A,B,C,D,E 用於確定終點的角度坐標尺寸;
第三組 I,J,K 用於確定圓弧輪廓的圓心坐標尺寸。
(4)進給功能字 F
進給功能字的地址符是F,又稱為F功能或F指令,用於指定切削的進給速度。
(5)主軸轉速功能字 S
主軸轉速功能字的地址符是S,又稱為S功能或S指令,用於指定主軸轉速。
(6)刀具功能字 T
刀具功能字的地址符是T,又稱為T功能或T指令,用於指定加工時所用刀具的編號。
(7)輔助功能字 M
輔助功能字的地址符是M,後續數字一般1~3位正整數,又稱為M功能或M指令,用於指定數控工具機輔助裝置的開關動作。
數控坐標系
1、工具機坐標系的確定
(1)工具機相對運動的規定
工件相對靜止,而刀具運動。
在工具機上,始終認為工件靜止,而刀具是運動的。這樣編程人員在不考慮工具機上工件與刀具具體運動的情況下,就可以依據零件圖樣,確定工具機的加工過程。
(2)工具機坐標系的規定
標準工具機坐標系中X、Y、Z坐標軸的相互關係用右手笛卡爾直角坐標系決定。
在數控工具機上,工具機的動作是由數控裝置來控制的,為了確定數控工具機上的成形運動和輔助運動,必須先確定工具機上運動的位移和運動的方向,這就需要通過坐標系來實現,這個坐標系被稱之為工具機坐標系。
例如銑床上,有工具機的縱向運動、橫向運動以及垂向訩動。在數控加工中就應該用工具機坐標系來描述。
2、標準工具機坐標系中X、Y、Z坐標軸的相互關係用右手笛卡爾直角坐標系決定:
直角坐標系
1)伸出右手的大拇指、食指和中指,並互為90度。則大拇指代表X坐標,食指代表Y坐標,中指代表Z坐標。
2)大拇指的指向為X坐標的正方向,食指的指向為Y坐標的正方向,中指的指向為Z坐標的正方向。
3)圍繞X、Y、Z坐標旋轉的旋轉坐標分別用A、B、C表示,根據右手螺旋定則,大拇指的指向為X、Y、Z坐標中任意一軸的正向,則其餘四指的旋轉方向即為旋轉坐標A、B、C的正向。
(3)運動方向的規定
增大刀具與工件距離的方向即為各坐標軸的正方向。
(二)工具機加工坐標系的設定
1、數控銑床(FANUC0M)加工坐標系的設定步驟
在選擇了被加工零件圖樣,並確定了編程原點位置後,可按以下方法進行加工坐標系設定:
(1)準備工作
工具機回參考點,確認工具機坐標系;
(2)裝夾工件毛坯
通過夾具使零件定位,並使工件定位基準面與工具機運動方向一致;
(3)對刀測量
用簡易對刀法測量,方法如下: X、Y向對刀方法
用直徑為φ10的標準測量棒、塞尺對刀,得到測量值為X , Y ,Z值 。
(4)計算設定值
將前面已測得的各項數據,按設定要求運算。
(5)設定加工坐標系
將開關放在 MDI 方式下,進入加工坐標系設定頁面。輸入數據為:
X= -392.626 Y= -246.460 Z= -32.033
表示加工原點設定在工具機坐標系的X= -392.626 Y= -246.460 Z= -32.033 的位置上。
(6)校對設定值
對於初學者,在進行了加工原點的設定後,應進一步校對設定值,以保證參數的正確性。
校對工作的具體過程如下:在設定了G54加工坐標系後,再進行回工具機參考點操作,其顯示值為
X +392.626
Y +246.460
Z +32.033
這說明在設定了G54加工坐標系後,工具機原點在加工坐標系中的位置為:
X +392.626
Y +246.460
Z +32.033
這反過來也說明G54的設定值是正確的。
2、加工坐標系設定的操作。
3、注意事項
(1)G54~G59設定加工坐標系的方法是一樣的,但在實際情況下,工具機廠家為了用戶的不同需要,在使用中有以下區別:利用G54設定工具機原點的情況下,進行回參考點操作時工具機坐標值顯示為G54的設定值,且符號均為正;利用G55~G59設定加工坐標系的情況下,進行回參考點操作時工具機坐標值顯示零值。
(2)G92指令與G54~G59指令都是用於設定工件加工坐標系的,但在使用中是有區別的。G92指令是通過程式來設定、選用加工坐標系的,它所設定的加工坐標系原點與當前刀具所在的位置有關,這一加工原點在工具機坐標系中的位置是隨當前刀具位置的不同而改變的。
(3)G54~G59指令是通過MDI在設定參數方式下設定工件加工坐標系的,一旦設定,加工原點在工具機坐標系中的位置是不變的,它與刀具的當前位置無關,除非再通過MDI 方式修改。
(4)本課程所例加工坐標系的設定方法,僅是FANUC系統中常用的方法之一,其餘不一一例舉。其它數控系統的設定方法應按隨機說明書執行。
4、常見錯誤
當執行程式段G92 X 10 Y 10時,常會認為是刀具在運行程式後到達X 10 Y 10 點上。其實, G92指令程式段只是設定加工坐標系,並不產生任何動作,這時刀具已在加工坐標系中的 X10 Y10點上。
G54~G59指令程式段可以和G00、G01指令組合,如G54 G90 G01 X 10 Y10時,運動部件在選定的加工坐標系中進行移動。 程式段運行後,無論刀具當前點在哪裡,它都會移動到加工坐標系中的X 10 Y 10 點上。
編程坐標系
編程坐標系編程人員根據零件圖樣及加工工藝等建立的坐標系。
編程坐標系一般供編程使用,確定編程坐標系時不必考慮工件毛坯在工具機上的實際裝夾位置。
編程原點是根據加工零件圖樣及加工工藝要求選定的編程坐標系的原點。
編程原點應儘量選擇在零件的設計基準或工藝基準上,編程坐標系中各軸的方向應該與所使用的數控工具機相應的坐標軸方向一致。
程式調試要點
(一)目的和要求
1、進一步熟悉數控車床的操作
通過試切對刀、簡腳踏車削循環、複合車削循環的程式調試,進一步熟悉數控車床的操作
2、掌握數控車削加工的對刀操作方法及工件坐標系的建立
掌握數控車削試切對刀的基本操作,用G92、G54~G59、Txxxx指令建立工件坐標系的幾種方法。
試切外圓作X向對刀,試切端面作Z向對刀;
G92是以當前位置點作為參照點、G54及T指令則是以工具機零點作為參照點來建立坐標系的。由於工具機原點不會改變,故用G54和T指令比用G92方便。
有多把刀具時使用T指令則更方便。
3、掌握簡腳踏車削循環程式的編寫規則及其套用
簡單循環是指用一個程式行取代多個基本指令程式行功能的簡化編程手段,包括以車外圓方式為主的G80和以車端面方式為主的G81。了解掌握指令格式中坐標數據的算法及指令的套用。
簡單循環編程僅用於一個台肩的階梯軸的加工,從棒料到台肩需要多個簡單循環程式行。
4、掌握複合車削循環的編程及其在車削加工中的套用
複合循環則是指僅用一個程式行就能實現多個台肩的階梯軸加工的更為方便的簡化編程手段,包括以車外圓方式為主的G71、以車端面方式為主的G72和走固定形狀路線的G73。了解掌握它們的編程規則和套用場合。
G71適於車削長軸類,G72適於加工盤類迴轉零件,G73為等餘量粗切方式,適於鑄鍛半成型毛坯件的車削。
複合循環不是一個孤立的程式行,依賴於精車輪廓的程式數據。
(二)重點和難點
重點:數控車床的坐標系建立方法、複合車削循環編程與套用
難點:數控車床的對刀、簡單循環中切削起點坐標的確定、複合循環程式編寫規則。
(三)方法和技巧
認真聽講、及時上機練習以幫助消化。
探索各類循環指令編程格式的書寫規律,比較異同以增進記憶。
二、銑削對刀、刀補程式的調試
(一)目的和要求
1、掌握數控銑削加工的對刀方法
僅使用一把刀具的銑削對刀,就是通過刀具刀位點(銑刀底面中心)作為媒介建立工件坐標系和工具機坐標系坐標數據間的聯繫。找到刀具在工件坐標中的坐標和同一位置處刀具在工具機坐標系中的坐標,即可推算出工件原點在工具機坐標系中的坐標,這就是對刀的目的。
對刀的方法主要有尋邊、找中,既可用刀具直接對刀,也可藉助於電子尋邊器對刀。尋邊時需要考慮刀具或尋邊器的半徑大小,找中時可不需考慮。
Z向對刀必須使用刀具直接對刀,可藉助固定高度的Z軸設定器來對刀。
2、熟練掌握數控銑床的坐標系建立及設定操作;
建立工件坐標系可用G92或G54~G59指令。
G92是以當前位置點位參照,對程式執行時刀具的當前位置有要求;
G54等是以工具機原點為參照點,通過對刀找到工件原點在工具機坐標系中的坐標,將該坐標賦給G54既可
3、掌握數控銑削加工中刀具半徑補償編程及套用;
由於刀具刀位點(刀刃底面中心)和刀具切削刃行走的軌跡不重合,兩者相差一個刀具半徑大小,因而需要考慮刀具半徑補償。
刀徑補償有人工預補償和工具機自動補償兩種方式。人工預刀補編程不具通用性,故可讓工具機來自動進行刀補運算。
了解刀補的載入、卸載過程及B、C功能刀補算法對合理使用刀補很關鍵。
4、進一步了解數控銑床的結構組成、加工控制原理;
5、 熟練掌握銑削程式的輸入調試過程;
(二)重點和難點
重點:銑削對刀操作、刀具半徑補償編程套用
難點:坐標系構建、工具機自動刀具半徑補償的編程規則
(三)學習方法和技巧
重點掌握G54構建工件坐標系的坐標推算方法,則對刀就不難理解。
在工件外或廢料區下刀,刀補加、卸載設計在引入、引出直線段內,其它的就直接按輪廓圖紙尺寸編程,是刀補編程的總原則。
數控程式設計師
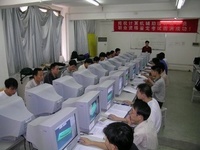