串聯蒸發冷凝液化流程也叫階式製冷循環流程。主要用於基本負荷型天然氣液化裝置。級聯式液化流程的基本原理是較低溫度級的循環將熱量轉移給相鄰的較高溫度級的循環,通過換熱器的熱量交換,逐步降低天然氣的溫度,直至天然氣被液化、過冷,經節流降壓後獲得低溫常壓態液化天然氣(LNG)。
基本介紹
- 中文名:串聯蒸發冷凝液化流程
- 外文名:Series evaporation condensation liquefaction process
- 別名:階式製冷循環流程
- 領域:天然氣液化
- 出現時間:1939 年
- 優點:能耗較低、操作穩定、適應性強
液化流程,液化實例,套用特點,
液化流程
串聯蒸發冷凝液化流程也叫階式製冷循環、復疊式液化流程。是1939 年首先套用於液化天然氣產品,裝於美國的Cleveland,採用NH3、C2H4 為第一、第二級製冷劑。 經典階式製冷循環由三個獨立的製冷系統組成。
第一級採用丙烷做製冷劑,經過淨化的天然氣在丙烷冷卻器中冷卻到-35~-40℃,分離出戊烷以上的重烴後進入第二級冷卻。由丙烷冷卻器中蒸發出來的丙烷氣體經壓縮機增壓,水冷卻器冷卻後重新液化,並循環到丙烷冷卻器。第二級採用乙烯做製冷劑,天然氣在第二級中被冷卻到-80~-100℃,並被液化後進入第三級冷卻。第三級採用甲烷做製冷劑,液化天然氣在甲烷冷卻器中被過冷到-150~-160℃,然後通過節流閥降壓,溫度降到-162℃後,用泵輸送到LNG 貯槽。甲烷冷卻器中蒸發出來的氣體經增壓、水冷後,在丙烷冷卻器中冷卻、在乙烯冷卻器中液化後,循環到甲烷冷卻器。
天然氣經過各個換熱器後的出口溫度一般為:第1個丙烷換熱器出口 273K;第2個丙烷換熱器出口 253K;第3個丙烷換熱器出口 233K;第1個乙烯換熱器出口213K;第2個乙烯換熱器出口193K;第3個乙烯換熱器出口173K;第1個甲烷換熱器出口153K;第2個甲烷換熱器出口133K;第3個甲烷換熱器出口113K。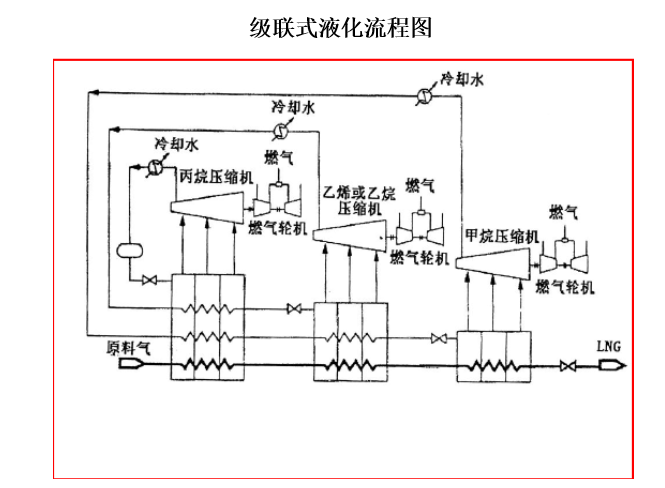
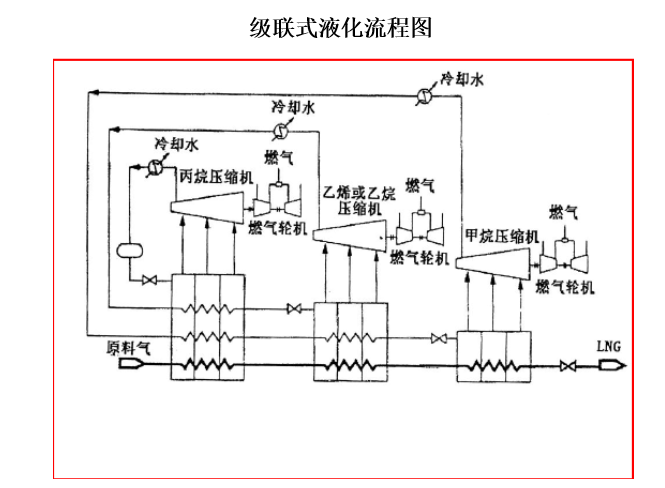
液化實例
右圖為串聯蒸發冷凝液化流程的示意網,圖中列處了運行參數。丙烷經壓縮達到1206 kPa,經節流後壓力降41kPa,溫度為-35℃,然後丙烷流過3個換熱器,依次冷卻乙烯、甲烷和天然氣。乙烯經壓縮達到2MPa,經丙烷預冷和節流後壓力降至41 kPa,溫度為-100℃,然後乙烯流過2個換熱器,依次冷卻甲烷和天然氣。甲烷經壓縮達到3.24MPa,經丙烷、乙烯預冷和節流後壓力降至41kPa,溫度為-155℃,然後進換熱器冷卻天然氣 在該流程中需液化的天然氣增壓至3.8MPa後,經水、丙烷、乙烯和甲烷冷卻後,壓力為3.65MPa、溫度降為-150℃;最後節流後進一步降壓降溫為0.1034MPa、-162℃。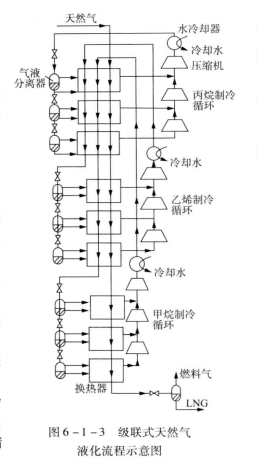
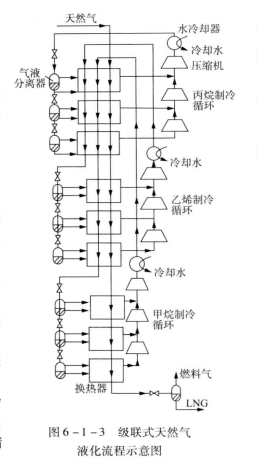
套用特點
級聯式液化流程的優點是能耗較低,因製冷劑為純物質,故無配比問題。各製冷系統與天然氣液化系統彼此獨立,相互影響較少,操作較穩定,適應性較強。
經典階式製冷循環,包含幾個相對獨立、相互串聯的冷卻階段,由於製冷劑一般使用多級壓縮機壓縮,因而在每個冷卻階段中,製冷劑可在幾個壓力下蒸發,分成幾個溫度等級冷卻天然氣,各個壓力下蒸發的製冷劑進入相應的壓縮機級壓縮。各冷卻階段僅製冷劑不同,操作過程基本相似。從發展來看,最初興建LNG 裝置時就用階式製冷循環的著眼點是:能耗最低,技術成熟,無需改變即可移植用於LNG 生產。
隨著發展要求而陸續興建新的LNG 裝置,這時經典的階式製冷循環就暴露出它固有的缺點:
1)經典的階式製冷循環由三個獨立的丙烷、乙烯、甲烷製冷循環復迭而成。機組多(三台壓縮機)、冷劑用量大、級間管路連線複雜,導致造價高昂;
2)為使實際級間操作溫度儘可能與原料天然氣的冷卻曲線(Q-T 曲線)貼近,以減少熵增,提高效率。可是隨著效率的提高,工藝流程也將變得十分複雜。
3)需要相當一部分資金購置和貯存製冷劑。