中空鋼的斷面形狀有六角形、方八角形、圓形、正方形、菱形等。國內外使用最多的是H19、H22、H25、H32、H35 六角形和R19、R25、R32、R38、R46、R52 等圓形中空鋼。釺具是鑿岩爆破中必不可少的工具,而釺桿是釺具的重要組成部分,中空鋼主要用於生產鑿岩釺桿。
基本介紹
- 中文名:中空鋼
- 外文名:Hollow steel
- 學科:冶金工程
- 領域:冶煉
- 形狀:圓形、正六角形或其他形狀
- 特點:中心有圓孔道
簡介
半連軋機組工藝設備情況
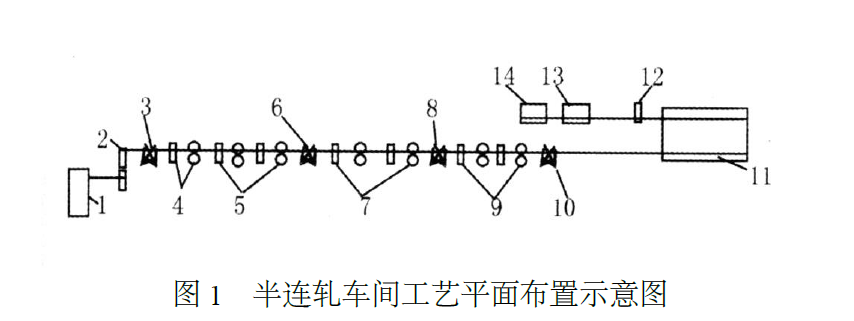
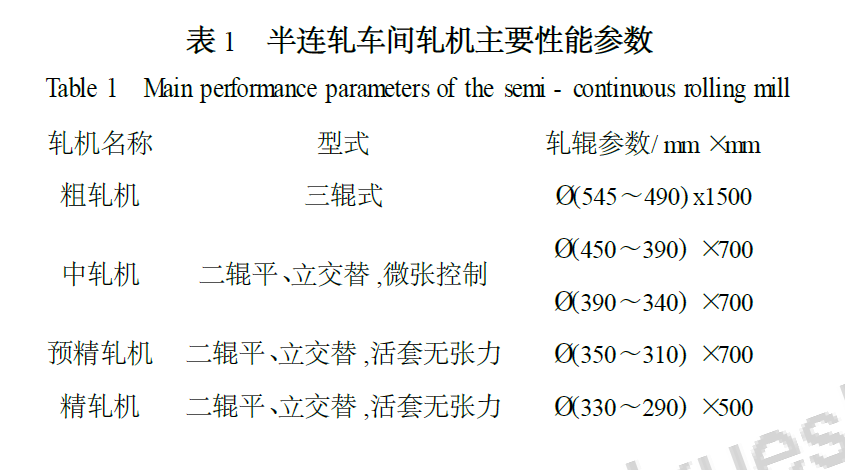
中空鋼的斷面形狀有六角形、方八角形、圓形、正方形、菱形等。國內外使用最多的是H19、H22、H25、H32、H35 六角形和R19、R25、R32、R38、R46、R52 等圓形中空鋼。釺具是鑿岩爆破中必不可少的工具,而釺桿是釺具的重要組成部分,中空鋼主要用於生產鑿岩釺桿。
中空鋼的斷面形狀有六角形、方八角形、圓形、正方形、菱形等。國內外使用最多的是H19、H22、H25、H32、H35 六角形和R19、R25、R32、R38、R46、R52 等圓形中...
指採用特定的工藝直接澆注出帶有中心孔的鋼錠的鑄錠方法。通常採用下注法澆注小型中空鋼錠。由中空鋼錠軋出的各種中空鋼材經熱處理後具有較高的強度、硬度及耐衝擊...
《鑿岩釺桿用中空鋼》是2008-8-19發布的圖書。...... 《鑿岩釺桿用中空鋼》是2008-8-19發布的圖書。中文名 鑿岩釺桿用中空鋼 標準號 GB/T 1301-2008 ...
2.3.1 JISG4401——2000碳素工具鋼2.3.2 JISG4404——2000合金工具鋼2.3.3 JISG4403——2000高速工具鋼2.3.4 JISG4410——1984中空釺桿鋼...
不鏽鋼鋼管,是一種不易生鏽的中空鋼管。...... 不鏽鋼鋼管(Stainless Steel)是一種中空的長條圓筒狀鋼材...6.焊接電弧長度,焊接普通鋼時,以2~4mm為佳,而焊接...
ZK35SiMnMoV中空鋼,力學性能硬度 :≤43HRC,熱處理規範淬火880℃~900℃,油,標準GB/T1301—1994。...
ZK55SiMnMo中空鋼是一種化學成份為碳 C :0.50~0.60、矽 Si:0.10~1.40等,標準為GB/T1301—1994,硬度為≤53HRC的中空鋼材。...
2.1.6 YB/T5322——2006碳素工具鋼絲 2.1.7 GB/T1301——2008鑿岩釺桿用中空鋼 2.1.8 GB/T1299——2000合金工具鋼 2.1.9 YB/T095——1997合金...
日本的特殊鋼概念包括合金鋼、中高碳鋼和抗拉強度大於590MPa高強度鋼,德、法與日本相似。美國的特殊鋼包括不鏽鋼加合金鋼(含碳工鋼、中空鋼和高強度低合金鋼),...
釺桿是井巷工程連線鑽頭和鑿岩的機具。礦山井巷工程一般使用的釺桿為六角中空鋼和中空園鋼,六角中空鋼的內切園直徑為22mm和25mm,中空園鋼的外徑為32mm和38mm,...
其它品種主要是一些專用的優質型材。包括中空鋼、氧氣瓶料、冷鐓鋼、工業純鐵、熱軋易切鋼、D60、S/5A、F18、F11等,後面幾種都是軍工用料。...
湖南久千釺具有限公司(原湘潭永安釺具有限公司)位於毛主席的故鄉湘潭市,於2005年成立,公司主營55SiMnMo六角中空鋼(鋼體商標為“久千5501”)及B22各種規格的釺桿...
本書系統、全面地介紹了釺具的服役條件、受力分析、破斷機理、影響使用壽命的因素及對材質的要求,釺鋼鋼種設計原理與各國常用釺鋼鋼種,中空鋼的各種冶軌生產工藝,...
我國現有20餘家企業生產掘進鑽車用釺具產品,由於受原材料中空鋼及加工設備限制,產品的質量一直不十分理想。21世紀,我國將進一步擴大鐵路和公路建設項目投資,液壓...
⒗60t中空鋼錠凝固過程數值模擬,橫向,1997-1999,主要研究人員蔡臨寧期刊論文 蔡臨寧,物流系統規劃,機械工業出版社:北京,2003-10-29...
事實上他們為中空鋼結構,具有很好的避雷效果。八達嶺長城特區辦文物管理科丁海濤介紹稱,這是國內首次引入仿真樹避雷針,這些仿真樹避雷針每顆價格20餘萬元。 [1] ...
主要生產 Ф 19 、 22 、 25mm 中空釺桿、 22mm ~ 27mm×35mm ~ 42mm 菱形中空鋼及麻花鑽桿、 YC-25 、 YC-70 液壓錘釺系列、 Ф 28mm ~ 46mm ...
彎曲型鋼用彎曲成型的方法可以生產用熱軋方法不能生產的複雜斷面 型鋼、薄壁型鋼以及中空型鋼。用彎曲型鋼代替普通熱軋型鋼可 以減輕結構重量,減少製造工作量並能節省...
據建研院物理所測試,單玻鋼,鋁窗的傳熱係數為64W/M2K;單玻塑鋼窗的傳熱...斷橋鋁門窗,採用隔熱斷橋鋁型材和中空玻璃,具有節能、隔音、防噪、防塵、防水等...
6.6 GB/T 5952—1986 碳素工具鋼絲6.7 GB/T 1301—1994 鑿岩纖桿用中空鋼6.8 GB/T 095—1997 合金工具鋼6.9 YB/T 095—1997 合金工具絲...
(3層以上)鋼化玻璃地面,複合中空鋼化玻璃地面,這些地面材料的共同點是全是用...按採用的結構特點分為:鋼結構玻璃地面,木結構玻璃地面,玻璃結構玻璃地面,其它...
煤機用刮板鋼、槽幫鋼,煤機用高強度圓環鏈用鋼,煤礦重要用途鋼絲繩,平衡用扁鋼絲繩,密封鋼絲繩,面接觸鋼絲繩,礦用流體輸送用電焊鋼管,鑿岩釺桿用中空鋼,鑿岩用...
和澆後的凝固期間,有利於夾雜物上浮,有利於自下而上的順序凝固和冒口鋼水的...鍛造鋼錠還有一些特殊形式,如空心鋼錠(中空鋼錠)和無冒口鋼錠。空心鋼錠外形與...
4、陽光板陽光房:(優點)骨架用斷橋鋁中間填上中空玻璃鋼,通透性好,保溫隔熱好。(缺點):造價比較高。陽光房基本的四周立柱是必須的,加上頂面承托彩鋼板或者鋼化...
電渣重熔爐的套用範圍很廣,不僅可用來生產航空軸承鋼、高溫合金、精密合金和某些有色金屬等,還可用來生產上百噸重的大型優質合金鋼錠、大型扁錠或板錠、中空鋼錠...