專利背景
21世紀以來,隨著中國製造業的快速發展,國產數控設備與流水線開始大量進入各個領域,一個尖銳的矛盾很快浮出水面——先進的設備,配不到先進的國產機械刀具,不得不配洋刀。國際模具及五金塑膠產業供應商協會秘書長羅百輝表示,優質硬質合金切削刀具在中國已經成為加工企業所需的主力刀具,被廣泛地套用於汽車及零部件生產、模具製造、航空航天等重工業領域,但中國刀具企業主要是大量生產高速鋼刀以及一些低檔標準刀具,完全沒有考慮到市場飽和度和企業所需,最終把具有高附加值、高科技含量的中高端刀具市場拱手讓給中國以外企業。
截至2016年5月,在已開發國家硬質合金刀具已占刀具的主導地位,比重達70%,而高速鋼刀具正以每年1%~2%的速度縮減,所占比例已降至30%以下。而在中國,有資料顯示,中國刀具2016年5月之前的年銷售額大約為145億元,其中大部分刀具屬於低端產品,仍是高速鋼標準刀具,加工效率和加工精度都較低,常用於傳統工具機和低精度工具機上,而優質硬質合金刀具所占的比重不足25%,與中國以外差距較大。但中國製造業所需的優質硬質合金刀具已經占到刀具市場的50%以上,這種盲目生產已經嚴重滿足不了中國製造業對優質硬質合金刀具日益增長的需求,從而形成了中高端市場的真空狀態,最終被中國以外企業所占據。
除中高端市場空白,中國刀具製造企業還普遍存在產品附加值低,傳統的加工方式與個性化的市場需求相脫節,原材料熱處理技術水平低,資源浪費等問題。雖然中國電工鋼有了突飛猛進的發展,但仍普遍存在質量差而成本高的問題。除了材料質量外,使用各種鋼件刀具產生的切口質量及其給後續工序帶來的質量問題,也是導致整體行業質量低下的重要因素。生產效率低、產品質量差、利潤薄,未來將會給中國刀具行業帶來生存和發展危機。因此,電機製造業及有色薄型金屬加工業的許多廠家試圖改變現狀,紛紛進口中國以外分切刀具,但有些進口刀具和原有國產設備不配套,同時後期修刀極其困難,而且價格昂貴,迫使一些廠家也不得不放棄進口刀具,繼續使用高速鋼刀具。
2016年5月之前,中國一些刀具廠家也曾試圖開發硬質合金分條刀,但因缺乏技術和關鍵專業人員,截至2016年5月只能開發生產普通的硬質合金刀具,而由於刀具刃口對質量要求較高,加工難度大,普通硬質合金難以滿足分切刀刃的加工要求,無法製作優質的硬質合金分條刀。 如,中國專利申請(申請號201310485442.5,公開號CN103540823A)公開了一種適用於製造高精加工用刀具的硬質合金材料,該硬質合金包括金屬碳化物粉末和金屬粘結劑組成的硬質合金基體,還包括塗層,其中金屬碳化物粉末選用各組分質量百分比為碳化鎢40~50%、碳化鉻3~8%、碳化鈦5~9%、碳化釩5~10%、碳化鈮2~5%、碳化鉭6~11%,金屬粘結劑選用鈷,其質量百分比為12~18%,塗層選用金剛石CVO塗層。該申請案的硬質合金具有高硬度、高耐磨性的特點,高速切削時磨損率較低,同時還具有良好的抗氧化性、耐熱性和化學穩定性,但該申請案的硬質合金與基體之間的潤濕性相對較差,其所含碳化鈮、碳化鉭含量較高,而碳化鈮、碳化鉭都是價格非常昂貴的稀有金屬,且該申請案的塗層技術要求高、設備昂貴,一台塗層設備需耗資上千萬,不能廣泛套用於一般企業。
因此,基於中國硬質合金分條刀的性能相對較差,難以滿足加工需求的現狀,亟需研究出一種綜合性能良好且成本較低的硬質合金分條刀。發明人一直致力於高性能硬質合金分條刀的研究,通過大量試驗研究對2016年5月之前的硬質合金分條刀的原料組分及加工工藝進行最佳化設計,並取得了優異成果,具體見發明人於2014年04月21日申請的申請號為201410161479.7的發明專利,該申請案在一定程度上從配料上有效解決了因濕磨分散不良帶來的孔隙和Co相分布不均等問題,從而製取了優質混合料,加工出高性能高精度分切剪下刀具,該申請案的刀具具備高硬度、高強度、強耐磨等優點,其質量和綜合使用性能均居中國領先地位。但發明人在使用過程中發現,該申請案中最終所得硬質合金分條刀的使用性能仍不能完全滿足中國對分切刀刃的要求,還不能有效解決當加工一些對質量要求較高的產品時需要進口中國以外刀具的問題,且刀片的使用壽命有待進一步提高。
發明內容
專利目的
《一種高性能硬質合金新材料分條分切刀及其加工方法》的目的在於克服中國2016年5月之前的硬質合金分條刀難以滿足金屬板材的加工要求,優質硬質合金刀具主要依賴於從中國以外進口的不足,提供了一種高性能硬質合金新材料分條分切刀及其加工方法。截至2016年5月,該發明的方法能夠有效克服中國已有分條刀存在的上述不足,顯著改善了硬質合金分條分切刀的使用性能,使其能夠滿足各種金屬板材的加工要求,保證金屬板的加工質量,且延長了分條刀的使用壽命。
技術方案
《一種高性能硬質合金新材料分條分切刀及其加工方法》的一種高性能硬質合金新材料分條分切刀,該分條分切刀採用粉末冶金工藝製成,其原料的各組分按如下質量百分比組成:
更進一步地,所述的抑制劑為多元複合抑制劑,由如下質量百分比的組分組成:0.5-0.8%VC、0.6-1.0%Cr3C2和0.3-0.5%TaC。
該發明的一種高性能硬質合金新材料分條分切刀的加工方法,該分條分切刀的加工包括以下步驟:
步驟一、配料:將分條分切刀的各組分分別按照質量百分比進行稱量並混合;
步驟二、濕磨、壓制:將步驟一中得到的混合粉料進行濕磨、乾燥並制粒,然後將混合粉料壓製成坯;
步驟三、燒結:將壓製成型後的坯料置於燒結爐中進行燒結,燒結結束後採用水冷
方式進行冷卻即得分條分切刀的粉末冶金毛坯;
步驟四、機加工:將燒結後得到的粉末冶金毛坯先後進行粗加工和精加工,即得該發明的高性能硬質合金新材料分條分切刀。
更進一步地,步驟二中的濕磨是將稱好的混合料放入濕磨機中研磨68-72小時,濕磨介質為無水酒精,且酒精與混合粉料的質量比為(3.2-3.5):1。
更進一步地,步驟二中混合粉料經濕磨、乾燥並制粒後的粒度控制在80-140目之間,松裝密度控制在3.9-4.2克/平方厘米,然後採用500-630噸的四柱壓力機將粉末壓製成坯。 更進一步地,步驟三中坯料燒結的具體過程如下:
(1)室溫~320℃:將坯料由室溫加熱至320℃,加熱時間為75-90分鐘;
(2)320~370℃:將坯料由320℃加熱至370℃,控制加熱時間為25-30分鐘,然後於370℃進行保溫110-120分鐘;
(3)370~450℃:將坯料由370℃加熱至450℃,控制加熱時間為55-60分鐘,然後於450℃下保溫50-60分鐘;
(4)450~800℃:將坯料由450℃加熱至800℃,控制加熱時間為110-115分鐘;
(5)800~1200℃:將坯料由800℃加熱至1200℃,控制加熱時間為100-110分鐘,然後於1200℃下保溫40-45分鐘;
(6)1200~1350℃:將坯料由1200℃加熱至1350℃,控制加熱時間為50-60分鐘,然後於1350℃下保溫20-27分鐘;
(7)1350℃~最終燒結溫度:將坯料由1350℃加熱至最終燒結溫度,控制加熱時間為18-21分鐘,最後於最終燒結溫度下燒結35-45分鐘;
(8)冷卻階段:燒結結束後,先自然冷卻,用滑閥泵抽真空,當溫度下降至1200℃,調節轉子流量計,將Ar氣流量調至最大,往爐膛充Ar氣,當降溫至800℃時,爐門汽缸打開,啟動快冷風機對坯料進行快速冷卻,並控制爐膛壓力在1~10兆帕。
更進一步地,所述的最終燒結溫度控制為1390℃~1410℃。
更進一步地,步驟三中燒結所用燒結爐包括燒結爐爐體,燒結爐爐體內部由外向內依次設有保溫層和發熱體,所述發熱體內部設有石墨內膽,該石墨內膽通過脫蠟管道與補蠟裝置相連通,所述的補蠟裝置內部填充有高導熱金屬環。
更進一步地,所述的補蠟裝置包括依次相連的一級補蠟器、二級補蠟器和三級補蠟器,其中,一級補蠟器和二級補蠟器內均填充有高導熱金屬環,三級補蠟器內部不含高導熱金屬環,且三級補蠟器通過管道與滑閥真空泵相連。
更進一步地,所述的一級補蠟器為臥式結構,二級補蠟器為立式結構,且二級補蠟器內部設有支架,沿支架高度方向設有交替分布的懸掛臂,所述的高導熱金屬環懸掛於所述懸掛臂,且懸掛臂與支架之間的夾角為30-70°。
改善效果
《一種高性能硬質合金新材料分條分切刀及其加工方法》具有如下顯著效果:
(1)該發明的一種高性能硬質合金新材料分條分切刀,通過對分條分切刀的原料組分及配比進行最佳化設計,從而在保證刀片具有較高硬度和耐磨性的基礎上,仍能保持優異的衝擊韌性和抗斷裂性能,滿足各種金屬板材對分條刀的分切要求,能夠有效避免當加工一些對質量要求較高的產品時需要進口中國以外刀具的問題,且刀片的使用壽命得到顯著延長。
(2)該發明的一種高性能硬質合金新材料分條分切刀的加工方法,通過對刀片的原料組分、配比及加工工藝進行最佳化設計,所得刀片的綜合使用性能能夠滿足要求,刀片晶粒尺寸細小,組織均勻緻密,孔隙明顯變小且減少,從而保證了金屬板材的分切質量,提高了分條分切刀的整體質量。
(3)該發明的一種高性能硬質合金新材料分條分切刀的加工方法,通過對刀片坯料的燒結工藝進行最佳化設計,從而保證了燒結後坯料的緻密性和均勻性,有效克服了粉末冶金毛坯的金相組織中易出現孔洞,從而導致刀圈在後續加工中易出現缺口的不足。且通過燒結工藝的最佳化有效保證了對燒結爐內石蠟氣的脫除效果,有利於保證燒結爐的正常工作。
(4)該發明的一種高性能硬質合金新材料分條分切刀的加工方法,通過對燒結爐的結構進行最佳化設計,從而進一步改善了燒結爐內坯料燒結的均勻性以及其脫蠟、補蠟效果,使刀片的燒結性能及質量得到有效保證。
附圖說明
圖1為《一種高性能硬質合金新材料分條分切刀及其加工方法》的燒結爐的結構示意圖;
示意圖中的標號說明:1、燒結爐爐體;2、保溫層;3、發熱體;4、石墨內膽;5、主真空管道;501、第一高真空蝶閥;6、脫蠟管道;601、第二高真空蝶閥;701、一級補蠟器;702、二級補蠟器;703、三級補蠟器;8、儲蠟罐;9、高導熱金屬環;10、支架;101、懸掛臂;11、波紋管;12、滑閥真空泵。
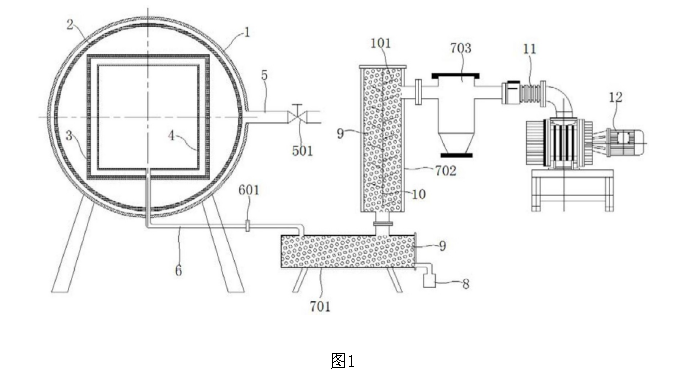
技術領域
《一種高性能硬質合金新材料分條分切刀及其加工方法》屬於硬質合金刀具技術領域,更具體地說,涉及一種高性能硬質合金新材料分條分切刀及其加工方法。
權利要求
1.《一種高性能硬質合金新材料分條分切刀及其加工方法》所述分條分切刀採用粉末冶金工藝製成,其原料的各組分按如下質量百分比組成:
該分條分切刀的加工包括以下步驟:步驟一、配料:將分條分切刀的各組分分別按照質量百分比進行稱量並混合;所述CT指
鄰苯二酚;
步驟二、濕磨、壓制:將步驟一中得到的混合粉料進行濕磨、乾燥並制粒,然後將混合粉料壓製成坯;
步驟三、燒結:將壓製成型後的坯料置於燒結爐中進行燒結,燒結結束後進行冷卻即得分條分切刀的粉末冶金毛坯;所述燒結爐包括燒結爐爐體(1),燒結爐爐體(1)內部由外向內依次設有保溫層(2)和發熱體(3),所述發熱體(3)內部設有石墨內膽(4),該石墨內膽(4)通過脫蠟管道(6)與補蠟裝置相連通,所述的補蠟裝置內部填充有高導熱金屬環(9);所述的補蠟裝置包括依次相連的一級補蠟器(701)、二級補蠟器(702)和三級補蠟器(703),其中,一級補蠟器(701)和二級補蠟器(702)內均填充有高導熱金屬環(9),三級補蠟器(703)內部不含高導熱金屬環(9),且三級補蠟器(703)通過管道與滑閥真空泵(12)相連;
步驟四、機加工:將燒結後得到的粉末冶金毛坯先後進行粗加工和精加工,即得高性能硬質合金新材料分條分切刀。
2.根據權利要求1所述的一種高性能硬質合金新材料分條分切刀的加工方法,其特徵在於:步驟二中的濕磨是將稱好的混合料放入濕磨機中研磨68-72小時,濕磨介質為無水酒精,且酒精與混合粉料的質量比為(3.2-3.5):1。
3.根據權利要求1所述的一種高性能硬質合金新材料分條分切刀的加工方法,其特徵在於:步驟二中混合粉料經濕磨、乾燥並制粒後的粒度控制在80-140目之間,松裝密度控制在3.9-4.2克/平方厘米,然後採用500-630噸的四柱壓力機將粉末壓製成坯。
4.根據權利要求1所述的一種高性能硬質合金新材料分條分切刀的加工方法,其特徵在於:步驟三中坯料燒結的具體過程如下:
(1)室溫~320℃:將坯料由室溫加熱至320℃,加熱時間為75-90分鐘;(2)320~370℃:將坯料由320℃加熱至370℃,控制加熱時間為25-30分鐘,然後於370℃進行保溫110-120分鐘;
(3)370~450℃:將坯料由370℃加熱至450℃,控制加熱時間為55-60分鐘,然後於450℃下保溫50-60分鐘;
(4)450~800℃:將坯料由450℃加熱至800℃,控制加熱時間為110-115分鐘;(5)800~1200℃:將坯料由800℃加熱至1200℃,控制加熱時間為100-110分鐘,然後於1200℃下保溫40-45分鐘;
(6)1200~1350℃:將坯料由1200℃加熱至1350℃,控制加熱時間為50-60分鐘,然後於1350℃下保溫20-27分鐘;
(7)1350℃~最終燒結溫度:將坯料由1350℃加熱至最終燒結溫度,控制加熱時間為18-21分鐘,最後於最終燒結溫度下燒結35-45分鐘;
(8)冷卻階段:燒結結束後,先自然冷卻,當溫度下降至1200℃,調節轉子流量計,將Ar氣流量調至最大,往爐膛充Ar氣,當降溫至800℃時,爐門汽缸打開,啟動快冷風機對坯料進行快速冷卻,並控制爐膛壓力在1~10兆帕。
5.根據權利要求4所述的一種高性能硬質合金新材料分條分切刀的加工方法,其特徵在於:所述的最終燒結溫度控制為1390℃~1410℃。
6.根據權利要求1-5中任一項所述的一種高性能硬質合金新材料分條分切刀的加工方法,其特徵在於:所述的一級補蠟器(701)為臥式結構,二級補蠟器(702)為立式結構,且二級補蠟器(702)內部設有支架(10),沿支架(10)高度方向設有交替分布的懸掛臂(101),所述的高導熱金屬環(9)懸掛於所述懸掛臂(101),且懸掛臂(101)與支架(10)之間的夾角為30-70°。
實施方式
該實施例的一種高性能硬質合金新材料分條分切刀,該分條分切刀採用粉末冶金工藝製成,其原料的各組分按如下質量百分比組成:
上述抑制劑為多元複合抑制劑,由如下質量百分比的組分組成:0.7%VC、0.6%Cr
3C
2和0.3%TaC。其中,該實施例的Co指鈷粉,VC指
碳化釩,Cr
3C
2指
碳化鉻,TaC指
碳化鉭,CT指鄰苯二酚,WC指碳化鎢粉。該實施例根據粉末冶金工藝方式,精選超細晶粒硬質碳化物WC和粘結金屬Co粉,根據條件加入微量元素作為抑制劑(碳化物),同時根據研磨機理加入十八酸作為活化物質,提高粉末顆粒的表面能,增加粉末濕磨時的分散性,有利於燒結時WC顆粒的緻密性重排;選擇超細WC(BET>1.5平方米/克)和Co粉材料,並在配料上進行創新改進,從而使硬質合金在燒結後得到組織緻密均勻,且綜合性能良好的坯料。
值得說明的是,發明人於2014年04月21日申請的申請號為201410161479.7的發明專利所公開的分條分切刀的原料組分雖然與本專利較為接近,但發明人在使用過程中發現,上述申請案的刀片在使用過程中其硬度和耐磨性相對較好,但刀片的衝擊韌性及抗裂紋敏感性則較差,在衝擊力的作用下易發生刀片變形及脆斷現象,從而影響金屬板材的分切效果,使分條分切刀的使用壽命受到影響,仍難以滿足中國加工業對分切刀刃的要求。此外,上述申請案中刀片的組織及性能相對不均勻,從而使刀片質量及使用壽命受到影響。發明人結合刀片的加工要求,通過大量實驗研究對刀片的原料組分和配比以及加工工藝進行最佳化設計,從而在保證刀片具有較高硬度和耐磨性的基礎上,仍能保持優異的衝擊韌性和抗斷裂性能,滿足各種金屬板材對分條刀的分切要求,能夠有效避免當加工一些對質量要求較高的產品時需要進口中國以外刀具的問題,且刀片的使用壽命得到顯著延長。
但在研究過程中,令發明人異常困擾的是,2016年5月之前的硬質合金刀具為了保證具有較高的硬度和耐磨性,通常通過提高WC的含量來實現,從而導致刀具的脆性較大,在使用過程中易發生脆斷現象;而當WC含量相對較低時,刀具的硬度和耐磨性則難以滿足使用要求。因此,當發明人試圖單純通過降低WC的含量、提高Co的含量來提高分條刀的韌性及抗斷裂性能時效果並不是很理想,尤其是WC及Co含量的微小下調即可能會引起刀片硬度及耐磨性的大幅下降,從而難以滿足質量要求。基於以上問題的存在,發明人一方面通過對刀片原料的組分配比進行最佳化設計,使各組分之間的協調作用得到更好發揮,另一方面還通過大量實驗對刀片的加工工藝進行最佳化,通過原料組分與工藝的配合,彌補了硬質合金刀片存在的硬度、耐磨性與衝擊韌性、抗斷裂性能之間的矛盾,使所得分條分切刀的綜合使用性能達到最優狀態,且所得刀片的組織及性能相對較均勻,其使用壽命得到顯著延長。
該實施例的上述高性能硬質合金新材料分條分切刀的加工方法,其特徵在於:該分條分切刀的加工包括以下步驟:
步驟一、配料:將分條分切刀的各組分分別按照質量百分比進行稱量並混合;
步驟二、濕磨、壓制:將步驟一中稱好的各組分混合後放入濕磨機中進行濕磨,濕磨介質為無水酒精,且酒精與混合粉料的質量比為3.2:1,濕磨時間為68小時,且濕磨機使用過程中每24小時放氣一次,從而保證濕磨效果,使混合料充分混合均勻,保證了後續所得刀片性能的均勻性。濕磨結束後,將混合料進行真空乾燥並制粒,然後採用600噸的四柱壓力機將混合料壓製成坯。上述混合粉料經真空乾燥並制粒後,物料粒度控制在100目左右,松裝密度控制在3.9克/平方厘米,從而能夠有效抑制燒結過程中晶粒的長大,保證所得硬質合金刀具的晶粒度滿足分切要求,且同時有助於保證燒結後坯料的緻密性,使孔隙明顯變小且減少,防止坯料組織分布不均勻,有利於使製備刀具的綜合性能滿足要求。
步驟三、燒結:將壓製成型後的坯料置於燒結爐中進行燒結,燒結結束後進行冷卻即得分條分切刀的粉末冶金毛坯。
發明人在加工過程中發現,壓製成型坯料的燒結工序能使多孔的毛坯脫蠟、收縮緻密成為具有一定組織和相應性能的製品,燒結工藝對最終製品的金相組織及硬質合金刀具的硬度、耐磨性等使用性能至關重要。例如,採用2016年5月之前的燒結工藝進行燒結,所得粉末冶金毛坯的金相組織中易出現孔洞,從而導致刀片在後續加工中易出現缺口,且當燒結工藝參數選擇不當時,易造成硬質合金物理性能參數不達標,Ms點偏高,從而使刀片硬度降低,難以滿足使用要求。因此,發明人通過大量實驗對硬質合金刀片的燒結工藝進行最佳化設計。
該實施例中,分條分切刀坯料的燒結過程如下:
(1)室溫~320℃:將坯料由室溫加熱至320℃,加熱時間為75分鐘;
(2)320~370℃:將坯料由320℃加熱至370℃,控制加熱時間為30分鐘,然後於370℃進行保溫120分鐘;
(3)370~450℃:將坯料由370℃加熱至450℃,控制加熱時間為60分鐘,然後於450℃下保溫53分鐘;
(4)450~800℃:將坯料由450℃加熱至800℃,控制加熱時間為110分鐘;
(5)800~1200℃:將坯料由800℃加熱至1200℃,控制加熱時間為110分鐘,然後於1200℃下保溫45分鐘;
(6)1200~1350℃:將坯料由1200℃加熱至1350℃,控制加熱時間為50分鐘,然後於1350℃下保溫20分鐘;
(7)1350℃~最終燒結溫度:將坯料由1350℃加熱至最終燒結溫度,控制加熱時間為21分鐘,最後於最終燒結溫度下燒結35分鐘;最終燒結溫度的具體數值根據原料的組分及配比控制為1390℃~1410℃,該實施例中最終燒結溫度取1400℃。
(8)冷卻階段:燒結結束後,先自然冷卻,當溫度下降至1200℃,調節轉子流量計,將Ar氣流量調至最大,往爐膛充Ar氣,當降溫至800℃時,爐門汽缸打開,啟動快冷風機對坯料進行快速冷卻,並控制爐膛壓力在7兆帕。
其中,室溫~450℃屬於脫蠟階段,由於在刀片坯料壓制過程中通常需要加入適量的石蠟,而這些石蠟對最終產品的內部品質沒有任何影響,因此需要在燒結工序中先將石蠟脫除。如果脫除方法不當,或石蠟脫除不乾淨,殘留的石蠟將附著在保溫層和爐壁上產生腐蝕,從而影響燒結爐的使用性能,且殘留的石蠟在後續燒結過程會以碳或其化合物的形式存在於製品當中,從而影響製品的總碳控制。因此,發明人通過大量實驗及生產經驗,對該階段的燒結工藝進行最佳化設計,採用分段加熱,並嚴格控制各段的加熱速率,從而保證了對燒結爐內石蠟氣的脫除效果。脫蠟階段開始運行時,向燒結爐內通入氬氣,並將氬氣流量控制為0.25立方米/小時,從而能夠進一步保證石蠟氣的脫除效果,保證石蠟的完全脫除。此外,370~450℃階段屬於大量脫蠟時間段,刀片在該段加熱時極易產生裂紋,因此該階段的脫蠟效果會直接影響刀片的質量,發明人根據實驗研究結果及多年的實踐經驗,對該段加熱速率進行有效控制,從而能夠有效防止產生裂紋,保證刀片的質量。
450~最終燒結溫度屬於高真空燒結階段,通過主真空管道進行抽真空,需控制此階段的真空度≤80Pa以內,通過對該過程的燒結溫度及加熱時間進行最佳化控制,從而能夠進一步保證刀片組織的緻密性及均勻性,且由於抑制劑碳化物在超微晶複合材料中分散極為均勻,從而保證了燒結時WC晶粒長大得到了更加有效的控制,從而使刀片的硬度、耐磨性及衝擊韌性、抗斷裂性能均滿足加工需求,有效克服了2016年5月之前硬質合金刀具粉末冶金毛坯的金相組織中易出現孔洞,從而導致刀圈在後續加工中易出現缺口的不足。此外,燒結過程中對燒結爐內石蠟的脫除效果也較好,從而保證了燒結爐以及所得坯料的使用性能。 為了進一步保證燒結爐內坯料燒結的均勻性以及脫蠟、補蠟效果,該實施例對燒結爐的結構進行了最佳化設計。如圖1所示,該實施例的燒結爐包括燒結爐爐體1,燒結爐爐體1內部由外向內依次設有保溫層2和發熱體3,所述發熱體3內部設有石墨內膽4,將待燒結坯料置於石墨內膽4中進行燒結,從而可以有效避免發熱體3直接進行熱輻射,防止坯料受熱不均勻,存在溫度梯度,發生邊緣粉化的現象,從而保證了刀具的燒結質量。上述石墨內膽4通過脫蠟管道6與補蠟裝置相連通,向燒結爐內通入氬氣作為載氣,從而可以將坯料燒結過程中產生的石蠟氣通過脫蠟管道6排出,且通過載氣脫蠟可以使燒結爐內外形成壓力差,有利於保證爐內氣氛的統一,進一步使坯料燒結性能保持均勻。該實施例中是在石墨內膽4及對應的燒結爐爐體1、保溫層2和發熱體3底部對應開設供脫蠟管道6穿過的孔道,孔道的尺寸與脫蠟管道6的外徑向匹配,脫蠟管道6直接伸入到石墨內膽4內部,從而可以有效避免石蠟氣由石墨內膽4向外擴散至燒結爐爐體1,在爐殼表面發生粘接,且進一步保證了石墨內膽4內氣氛的統一。
該實施例中,所述燒結爐爐體1內部還通過主真空管道5與羅茨泵相連,從而可以通過羅茨泵對燒結爐進行抽真空,保證燒結爐爐體1內部的真空度滿足要求,從而保證燒結質量。上述主真空管道5上設有第一高真空蝶閥501,脫蠟管道6上設有第二高真空蝶閥601,從而可以對燒結爐內的抽真空及排蠟氣過程進行開啟、關閉。
該實施例的補蠟裝置的器壁採用夾套結構,且夾套均與冷熱水供應裝置相連,從而可以控制補蠟裝置的工作狀態,保證其補蠟效果。燒結爐內脫蠟過程中,坯料中逐步揮發的石蠟蒸汽,在滑閥泵抽力及輔助氣體氬氣的作用下,通過脫蠟管道6連續不斷的帶入補蠟裝置,控制冷熱水供應裝置向補蠟裝置的夾套內供應冷水,對石蠟氣進行冷卻和凝固,從而對石蠟進行補集。上述補蠟裝置內部還填充有高導熱金屬環9,該金屬環可以選用銅環或鋁環,該實施例的高導熱金屬環9採用金屬銅環,石蠟氣穿過金屬環之間的間隙進行冷卻,從而可以進一步加速石蠟氣的冷卻,且增大石蠟氣在同一石蠟器內的傳熱接觸面積,延長石蠟氣在同一石蠟器內的停留和冷卻時間,防止由於氣流流動過快,石蠟氣來不及進行冷卻而隨氣流一起直接排放,造成石蠟氣捕捉不完全。
為了進一步保證補蠟完全,該實施例的補蠟裝置包括依次相連的一級補蠟器701、二級補蠟器702和三級補蠟器703(值得說明的是,補蠟器的個數並不局限於三個,具體個數可根據實際需要進行設定),其中一級補蠟器701和二級補蠟器702內均填充有高導熱金屬環9,三級補蠟器703內部不含高導熱金屬環9。所述一級補蠟器701採用臥式結構,二級補蠟器702採用立式結構,且一級補蠟器701的底部設有出蠟孔,該出蠟孔通過管道與儲蠟罐8相連,從而可以使一級補蠟器701和二級補蠟器702內冷凝得到的液態石蠟通過出蠟孔進入儲蠟罐8,從而對石蠟進行存儲。二級補蠟器702內部沿其中心軸向設有支架10,且沿支架10高度方向設有交替分布的懸掛臂101,所述的高導熱金屬環9懸掛於所述懸掛臂101,懸掛臂101與支架10之間的夾角可根據實際情況加工為30-70°,該實施例中為30°,從而改善了二級補蠟器702內氣流的流通狀況,便於石蠟氣的捕捉,大大提高了其捕捉效果,保證石蠟氣經過一級補蠟器701和二級補蠟器702後基本被捕捉完。所述的三級補蠟器703通過管道與滑閥真空泵12相連,由於進入三級補蠟器703的石蠟氣含量已較少,因此三級補蠟器703內無需填充高導熱金屬環9。通過上述三個補蠟器的設定可以保證補蠟完全,阻止石蠟蒸汽進入真空泵,污染真空泵,導致真空泵的抽力下降。該實施例中三級補蠟器703與滑閥真空泵12之間的連線管道上設有波紋管11,從而能夠有效防止上述連線管道隨真空泵12一起震動過程中發生脫落。
當脫蠟階段結束後,控制冷熱水供應裝置向補蠟裝置的夾套內供應熱水,開始對捕蠟器融蠟,融蠟時間為130分鐘,從而能夠有效防止下次開爐發生堵蠟現象,保證補蠟效果。
步驟四、機加工:將燒結後得到的粉末冶金毛坯按照實際分切要求及圖紙設計先後進行粗加工和精加工,即得該發明的高性能硬質合金新材料分條分切刀。如表1所示是該實施例1的產品與2016年6月之前市場上鋰電分切刀片使用的主要刀具綜合性能對照表。由表中可以看出,該實施例製備的硬質合金新材料分條分切刀的硬度與普通鎢鋼刀具相差不大,但其抗彎強度、斷裂韌性均明顯高於普通鎢鋼刀具,且該實施例製備的硬質合金新材料分條分切刀的使用壽命及切口質量也遠遠由於普通鎢鋼刀具及高速鋼刀具。
主要技術參數指標 | 實施例的產品 | 普通鎢鋼刀具 | 高速鋼刀具 |
---|
產品型號 | | | |
---|
硬度(HRA) | | | |
---|
抗彎強度(牛/平方毫米) | | | |
---|
斷裂韌性 | | | |
---|
使用壽命 | | | |
---|
適用設備 | | | |
---|
刀面形式 | | | |
---|
粗糙度 | | | |
---|
平行度 | | | |
---|
修刀時間 | | | |
---|
切口質量 | | | |
---|
綜合採用新材料及獨特刀具設計技術和加工工藝,製造出優質特高耐磨性和特高強度的硬質合金新材料滾剪刀,使該刀具不僅適合於電工鋼加工行業及有色金屬薄型材料的縱剪設備使用,同時能滿足不同行業剪下縱切要求;而且有非常好的性價比。其使用壽命分別是普通合金刀具的近數倍,高速鋼刀具的數十倍,價格只高1倍和4倍。
該實施例的一種高性能硬質合金新材料分條分切刀,該分條分切刀採用粉末冶金工藝製成,其原料的各組分按如下質量百分比組成:
上述抑制劑為多元複合抑制劑,由如下質量百分比的組分組成:0.5%VC、0.8%Cr3C2和0.5%TaC。
該實施例的上述高性能硬質合金新材料分條分切刀的加工方法,其特徵在於:該分條分切刀的加工包括以下步驟:
步驟一、配料:將分條分切刀的各組分分別按照質量百分比進行稱量並混合;
步驟二、濕磨、壓制:將步驟一中稱好的各組分混合後放入濕磨機中進行濕磨,濕磨介質為酒精,且酒精與所有原材料的質量比為3.3:1,濕磨時間為70小時,且濕磨機使用過程中每22小時放氣一次,從而保證濕磨效果,使混合料充分混合均勻,保證了後續所得刀片性能的均勻性。濕磨結束後,將混合料進行真空乾燥並制粒,然後採用550噸的四柱壓力機將球磨好的粉末壓製成坯。該實施例中混合料經真空乾燥並制粒後,物料粒度控制在110目左右,松裝密度控制在4克/平方厘米。
步驟三、燒結:將壓製成型後的坯料置於燒結爐中進行燒結,燒結結束後進行冷卻即得分條分切刀的粉末冶金毛坯。該實施例中,分條分切刀坯料的燒結過程具體如下: (1)室溫~320℃:將坯料由室溫加熱至320℃,加熱時間為85分鐘;
(2)320~370℃:將坯料由320℃加熱至370℃,控制加熱時間為28分鐘,然後於370℃進行保溫115分鐘;
(3)370~450℃:將坯料由370℃加熱至450℃,控制加熱時間為55分鐘,然後於450℃下保溫57分鐘;
(4)450~800℃:將坯料由450℃加熱至800℃,控制加熱時間為115分鐘;
(5)800~1200℃:將坯料由800℃加熱至1200℃,控制加熱時間為108分鐘,然後於1200℃下保溫40分鐘;
(6)1200~1350℃:將坯料由1200℃加熱至1350℃,控制加熱時間為52分鐘,然後於1350℃下保溫27分鐘;
(7)1350℃~最終燒結溫度:將坯料由1350℃加熱至最終燒結溫度,控制加熱時間為20分鐘,最後於最終燒結溫度下燒結38分鐘;該實施例中最終燒結溫度為1390℃。
(8)冷卻階段:燒結結束後,先自然冷卻,當溫度下降至1200℃,調節轉子流量計,將Ar氣流量調至最大,往爐膛充Ar氣,當降溫至800℃時,爐門汽缸打開,啟動快冷風機對坯料進行快速冷卻,並控制爐膛壓力在10兆帕。
該實施例中燒結爐的結構基本同實施例1,其區別在於:一級補蠟器701和二級補蠟器702內均填充有金屬鋁環,且二級補蠟器702中懸掛臂101與支架10之間的夾角優選為60°,從而保證了二級補蠟器702的最佳補蠟效果。脫蠟階段開始運行時,向燒結爐內通入氬氣,並將氬氣流量控制為0.4立方米/小時,當脫蠟階段結束後,控制冷熱水供應裝置向補蠟裝置的夾套內供應熱水,開始對捕蠟器融蠟,融蠟時間為130分鐘,從而能夠有效防止下次開爐發生堵蠟現象,保證補蠟效果。該實施例所得分條分切刀的使用性能及使用壽命均優於實施例1。
該實施例的一種高性能硬質合金新材料分條分切刀,該分條分切刀採用粉末冶金工藝製成,其原料的各組分按如下質量百分比組成:
上述抑制劑為多元複合抑制劑,由如下質量百分比的組分組成:0.6%VC、1.0%Cr3C2和0.4%TaC。
該實施例的上述高性能硬質合金新材料分條分切刀的加工方法,其特徵在於:該分條分切刀的加工包括以下步驟:
步驟一、配料:將分條分切刀的各組分分別按照質量百分比進行稱量並混合;
步驟二、濕磨、壓制:將步驟一中稱好的各組分混合後放入濕磨機中進行濕磨,濕磨介質為無水酒精,且酒精與所有原材料的質量比為3.4:1,濕磨時間為72小時,且濕磨機使用過程中每20小時放氣一次,從而保證濕磨效果,使混合料充分混合均勻,保證了後續所得刀片性能的均勻性。濕磨結束後,將混合料進行真空乾燥並制粒,然後採用500噸的四柱壓力機將球磨好的粉末壓製成坯。該實施例中混合料經真空乾燥並制粒後,物料粒度控制在140目左右,松裝密度控制在4.2克/平方厘米。
步驟三、燒結:將壓製成型後的坯料置於燒結爐中進行燒結,燒結結束後進行冷卻即得分條分切刀的粉末冶金毛坯。該實施例中,分條分切刀坯料的燒結過程具體如下: (1)室溫~320℃:將坯料由室溫加熱至320℃,加熱時間為90分鐘;
(2)320~370℃:將坯料由320℃加熱至370℃,控制加熱時間為25分鐘,然後於370℃進行保溫110分鐘;
(3)370~450℃:將坯料由370℃加熱至450℃,控制加熱時間為58分鐘,然後於450℃下保溫50分鐘;
(4)450~800℃:將坯料由450℃加熱至800℃,控制加熱時間為113分鐘;
(5)800~1200℃:將坯料由800℃加熱至1200℃,控制加熱時間為100分鐘,然後於1200℃下保溫42分鐘;
(6)1200~1350℃:將坯料由1200℃加熱至1350℃,控制加熱時間為57分鐘,然後於1350℃下保溫22分鐘;
(7)1350℃~最終燒結溫度:將坯料由1350℃加熱至最終燒結溫度,控制加熱時間為18分鐘,最後於最終燒結溫度下燒結40分鐘;該實施例中最終燒結溫度為1410℃。
(8)冷卻階段:燒結結束後,先自然冷卻,當溫度下降至1200℃,調節轉子流量計,將Ar氣流量調至最大,往爐膛充Ar氣,當降溫至800℃時,爐門汽缸打開,啟動快冷風機對坯料進行快速冷卻,並控制爐膛壓力在1兆帕。
該實施例中燒結爐的結構基本同實施例1,其區別在於:一級補蠟器701和二級補蠟器702內均填充有金屬鋁環,且二級補蠟器702中懸掛臂101與支架10之間的夾角為45°。脫蠟階段開始運行時,向燒結爐內通入氬氣,並將氬氣流量控制為0.5立方米/小時,當脫蠟階段結束後,控制冷熱水供應裝置向補蠟裝置的夾套內供應熱水,開始對捕蠟器融蠟,融蠟時間為140分鐘,從而能夠有效防止下次開爐發生堵蠟現象,保證補蠟效果。該實施例所得分條分切刀的使用性能較好,與實施例1接近。
該實施例的一種高性能硬質合金新材料分條分切刀,該分條分切刀採用粉末冶金工藝製成,其原料的各組分按如下質量百分比組成:
上述抑制劑為多元複合抑制劑,由如下質量百分比的組分組成:0.8%VC、0.9%Cr3C2和0.5%TaC。
該實施例的上述高性能硬質合金新材料分條分切刀的加工方法,其特徵在於:該分條分切刀的加工包括以下步驟:
步驟一、配料:將分條分切刀的各組分分別按照質量百分比進行稱量並混合;
步驟二、濕磨、壓制:將步驟一中稱好的各組分混合後放入濕磨機中進行濕磨,濕磨介質為酒精,且酒精與所有原材料的質量比為3.5:1,濕磨時間為69小時,且濕磨機使用過程中每21小時放氣一次,從而保證濕磨效果,使混合料充分混合均勻,保證了後續所得刀片性能的均勻性。濕磨結束後,將混合料進行真空乾燥並制粒,然後採用630噸的四柱壓力機將球磨好的粉末壓製成坯。該實施例中混合料經真空乾燥並制粒後,物料粒度控制在80目左右,松裝密度控制在4.1克/平方厘米。
步驟三、燒結:將壓製成型後的坯料置於燒結爐中進行燒結,燒結結束後進行冷卻即得分條分切刀的粉末冶金毛坯。該實施例中,分條分切刀坯料的燒結過程具體如下: (1)室溫~320℃:將坯料由室溫加熱至320℃,加熱時間為87分鐘;
(2)320~370℃:將坯料由320℃加熱至370℃,控制加熱時間為30分鐘,然後於370℃進行保溫118分鐘;
(3)370~450℃:將坯料由370℃加熱至450℃,控制加熱時間為57分鐘,然後於450℃下保溫60分鐘;
(4)450~800℃:將坯料由450℃加熱至800℃,控制加熱時間為112分鐘;
(5)800~1200℃:將坯料由800℃加熱至1200℃,控制加熱時間為105分鐘,然後於1200℃下保溫44分鐘;
(6)1200~1350℃:將坯料由1200℃加熱至1350℃,控制加熱時間為60分鐘,然後於1350℃下保溫24分鐘;
(7)1350℃~最終燒結溫度:將坯料由1350℃加熱至最終燒結溫度,控制加熱時間為21分鐘,最後於最終燒結溫度下燒結45分鐘;該實施例中最終燒結溫度為1395℃。
(8)冷卻階段:燒結結束後,先自然冷卻,當溫度下降至1200℃,調節轉子流量計,將Ar氣流量調至最大,往爐膛充Ar氣,當降溫至800℃時,爐門汽缸打開,啟動快冷風機對坯料進行快速冷卻,並控制爐膛壓力在4兆帕。
該實施例中燒結爐的結構基本同實施例1,其區別在於:一級補蠟器701和二級補蠟器702內均填充有金屬鋁環,且二級補蠟器702中懸掛臂101與支架10之間的夾角為70°。脫蠟階段開始運行時,向燒結爐內通入氬氣,並將氬氣流量控制為0.3立方米/小時,當脫蠟階段結束後,控制冷熱水供應裝置向補蠟裝置的夾套內供應熱水,開始對捕蠟器融蠟,融蠟時間為135分鐘,從而能夠有效防止下次開爐發生堵蠟現象,保證補蠟效果。該實施例所得分條分切刀的使用性能較好,與實施例1接近。
榮譽表彰
2019年5月16日,《一種高性能硬質合金新材料分條分切刀及其加工方法》獲得安徽省第六屆專利獎優秀獎。