《一種精陶質衛生陶瓷坯體及其製造方法》是惠達衛浴股份有限公司於2010年3月10日申請的發明專利,該專利的申請號為2010101206060,公布號為CN101811858A,授權公布日為2010年8月25日,發明人是王彥慶、宋子春、楊暉、曹和平、樊立永、董子紅、馮賀生、王春金、董志軍。
《一種精陶質衛生陶瓷坯體及其製造方法》所述坯體原料包括如下質量份的物質:球土10-30,高嶺土20-35,瓷土5-15,石英5-15,煅燒高嶺土10-25,矽灰石5-15。該發明優選精陶質坯體原料及添加比例,控制莫來石、石英等晶相含量,減少玻璃相含量,降低其高溫塑性形變,達到降低精陶質衛生陶瓷變形的目的;在降低坯體吸濕膨脹的同時,提高坯體在200℃的熱膨脹係數,使釉面承受較高的壓應力,因而提高了產品的抗龜裂性能,保證其具有足夠長的使用壽命。
2019年9月29日,《一種精陶質衛生陶瓷坯體及其製造方法》獲2018年河北省專利獎優秀獎。
(概述圖為《一種精陶質衛生陶瓷坯體及其製造方法》摘要附圖)
基本介紹
- 中文名:一種精陶質衛生陶瓷坯體及其製造方法
- 公布號:CN101811858A
- 公布日:2010年8月25日
- 申請號:2010101206060
- 申請日:2010年3月10日
- 申請人:惠達衛浴股份有限公司
- 地址:河北省唐山市丰南區黃各莊鎮
- 發明人:王彥慶、宋子春、楊暉、曹和平、樊立永、董子紅、馮賀生、王春金、董志軍
- Int.Cl.:C04B33/00(2006.01)I
- 代理機構:石家莊冀科專利商標事務所有限公司
- 代理人:曹淑敏、周曉萍
- 類別:發明專利
專利背景,發明內容,專利目的,技術方案,改善效果,附圖說明,權利要求,實施方式,榮譽表彰,
專利背景
衛浴空間裝飾設計的藝術化和個性化,對衛浴產品的製造提出了更高的標準要求,特別是對大尺寸產品的規整度提出了較高要求。陶瓷製品的尺寸越大,其燒成難度也越大,除產品易開裂外,產品表面變形、邊緣變形、整體扭曲等質量問題是造成產品不合格的主要原因之一。衛生陶瓷產品一般是瓷質坯體,經過1200~1250℃的高溫燒成之後,吸水率不大於0.5%,在高溫燒成過程中,由於玻璃相迅速軟化,在重力作用下,產生彎曲變形缺陷是玻璃相過多的瓷質衛生陶瓷坯體難以克服解決的。瓷質衛生陶瓷自身高液相含量決定了其高變形的固有特性。對於瓷質衛生陶瓷而言,無論是原料、成型、乾燥、燒成工序,還是產品結構設計的改進,都只是從外部因素進行的非本質改進,始終無法從根本上解決製品變形大的問題。
與瓷質衛生陶瓷相比,陶質衛生陶瓷在製造大尺寸、高規整度的產品方面,具有天然的優勢。然而,陶質衛生陶瓷由於吸水率高,在使用過程中容易吸濕膨脹而產生釉面後期龜裂的致命缺點,縮短了產品的使用壽命。而且傳統陶質衛生陶瓷坯料顆粒粗大,釉面針孔多,需使用化妝土來遮蓋坯體以減少釉面針孔,但使用化妝土導致生產工藝複雜,容易產生滾釉等缺陷,產品合格率低。因此,陶質衛生陶瓷需在採用精陶質坯體基礎上,要研究更為合適的精陶質坯體配方及生產工藝,以期獲得更低的變形度、良好的釉面質量及較長的使用壽命。
發明內容
專利目的
《一種精陶質衛生陶瓷坯體及其製造方法》用於克服2010年3月前已有技術的缺陷而提供一種釉面質量好、使用壽命長、生產成本低、產品合格率高的精陶質衛生陶瓷坯體及其製造方法。
技術方案
一種精陶質衛生陶瓷坯體,其特別之處是,所述坯體原料包括如下質量份的物質:球土10-30,高嶺土20-35,瓷土5-15,石英5-15,煅燒高嶺上10-25,矽灰石5-15。
上述精陶質衛生陶瓷坯體,所述坯體原料加入如下質量份的物質:高嶺石5-15,長石2-5。
上述精陶質衛生陶瓷坯體,所述坯體原料由如下質量份的物質組成:球土20,高嶺土20,瓷土15,石英10,煅燒高嶺土17,矽灰石10,高嶺石5,長石3。
上述精陶質衛生陶瓷坯體製造方法,它包括原料稱取、泥漿製備、注漿成型、脫模乾燥等步驟,所述泥漿製備步驟的主要工藝參數如下:泥漿濃度(克/200毫升)360-380,細度(350目篩余%)6-10,吸漿速度(毫米/45分鐘)5-6.5,流動性V0(秒)50-70。
改善效果
《一種精陶質衛生陶瓷坯體及其製造方法》通過優選精陶質坯體原料及合理控制各原料的添加比例,控制莫來石、石英等晶相含量,減少玻璃相含量,降低其高溫塑性形變,達到降低精陶質衛生陶瓷變形的目的;在降低坯體吸濕膨脹的同時,提高坯體在200℃的熱膨脹係數,使釉面承受較高的壓應力,因而提高了精陶質衛生陶瓷成品的抗龜裂性能,保證其具有足夠長的使用壽命。以該發明坯體製造的衛生陶瓷產品,總收縮率低於7%以下,標準變形度在7毫米以下,可以減少衛生陶瓷製品在乾燥及燒成過程中的開裂缺陷和變形缺陷,釉面針孔缺陷少,無需使用化妝土來減少針孔,簡化了生產工藝,提高了生產效率和產品合格率。該發明方法可從根本上解決瓷質衛生陶瓷坯體收縮大、變形大的問題,適合用於製造瓷質衛生陶瓷坯體無法滿足設計要求的大尺寸、結構複雜的產品。
附圖說明
圖1是瓷質衛生陶瓷坯體XRD圖譜;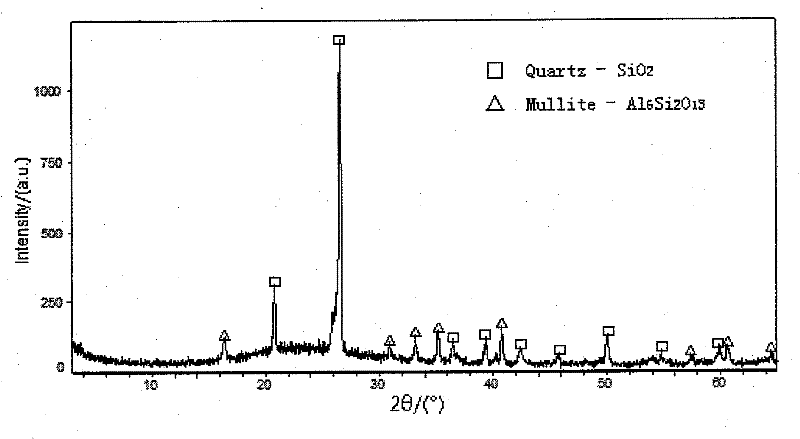
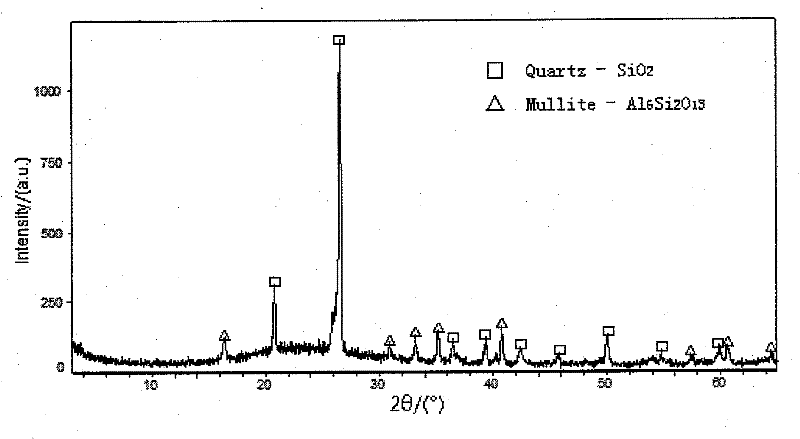
圖1
圖2是《一種精陶質衛生陶瓷坯體及其製造方法》精陶質衛生陶瓷坯體XRD圖譜。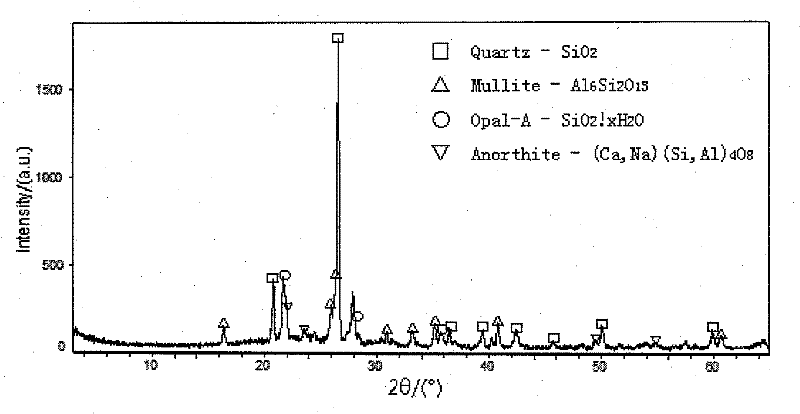
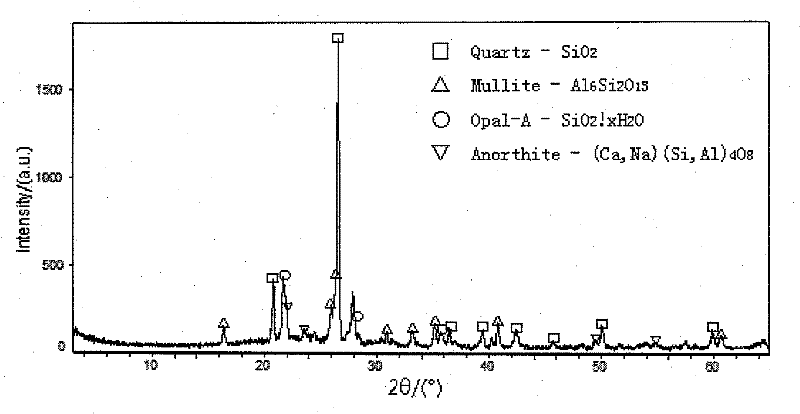
圖2
權利要求
1.一種精陶質衛生陶瓷坯體,其特徵在於,所述坯體原料包括如下質量份的物質:球土10-30,高嶺土20-35,瓷土5-15,石英5-15,煅燒高嶺土10-25,矽灰石5-15。
2.根據權利要求1所述的精陶質衛生陶瓷坯體,其特徵在於:所述坯體原料加入如下質量份的物質:高嶺石5-15,長石2-5。
4.根據權利要求1或2或3所述的精陶質衛生陶瓷坯體製造方法,它包括原料稱取、泥漿製備、注漿成型、脫模乾燥等步驟,其特徵在於:所述泥漿製備步驟的主要工藝參數如下:泥漿濃度(克/200毫升)360-380,細度(350目篩余%)6-10,吸漿速度(毫米/45分鐘)5-6.5,流動性V0(秒)50-70。
實施方式
《一種精陶質衛生陶瓷坯體及其製造方法》針對普通陶質衛生陶瓷及瓷質衛生陶瓷存在的諸多問題,對陶質衛生陶瓷坯體原料配比進行了深入研究和大量試驗,優選出精陶質坯體原料組成物及各原料的添加比例。所述精陶質衛生陶瓷坯體原料中通過適量添加煅燒高嶺土,控制莫來石、石英等晶相含量,減少玻璃相含量,降低其高溫塑性形變,達到降低精陶質衛生陶瓷變形的目的。採用該發明的精陶質坯體配方製造衛生陶瓷產品,其乾燥收縮率在3%以下,燒成收縮率在4%以下,總收縮率在7%以下,標準變形度在7毫米以下,減少衛生陶瓷製品在乾燥及燒成過程中的開裂缺陷,減少燒成過程中的變形缺陷,提高製品的製造精度及合格率。原料中通過適量添加矽灰石與石英,在降低坯體的吸濕膨脹的同時,提高坯體在200℃的熱膨脹係數,使釉面承受較高的壓應力,因而提高了衛生陶瓷成品的抗龜裂性能,保證其具有足夠長的使用壽命。該發明原料配比克服了單純使用矽灰石,雖然能夠解決釉面龜裂缺陷,但卻引起坯體燒成抗折強度降低,從而導致運輸、使用過程中容易破裂損壞的問題;克服了單純採用提高坯體在200℃的熱膨脹係數,雖然能夠解決釉面龜裂缺陷,但卻會引起釉面剝落、產品風驚炸裂的問題。
以下結合實施例對《一種精陶質衛生陶瓷坯體及其製造方法》原料組成機理進行詳述:
實施例原料配方見表1:
/ | 原料配比(質量份) | |||||||
---|---|---|---|---|---|---|---|---|
球土 | 高嶺土 | 瓷土 | 高嶺石 | 石英 | 煅燒高嶺土 | 長石 | 矽灰石 | |
實施例1 | 10 | 35 | 10 | 15 | 15 | 10 | 0 | 5 |
實施例2 | 10 | 30 | 13 | 10 | 15 | 10 | 2 | 10 |
實施例3 | 10 | 30 | 15 | 5 | 15 | 10 | 0 | 15 |
實施例4 | 10 | 30 | 15 | 5 | 5 | 25 | 0 | 10 |
實施例5 | 10 | 30 | 15 | 0 | 5 | 25 | 0 | 15 |
實施例6 | 10 | 30 | 15 | 5 | 15 | 10 | 5 | 10 |
實施例7 | 30 | 20 | 5 | 10 | 15 | 10 | 0 | 10 |
實施例8 | 20 | 20 | 15 | 5 | 10 | 17 | 3 | 10 |
上述原料化學成分見表2:
/ | LOI | SiO2 | Al2O3 | Fe2O | TiO2 | CaO | MgO | K2O | Na2O |
球土 | 11.79 | 55.15 | 26.44 | 1.65 | 0.73 | 0.77 | 0.63 | 2.01 | 0.67 |
高嶺土 | 11.45 | 44.91 | 36.1 | 1.74 | 1.34 | 0.97 | 0.64 | 1.29 | 0.67 |
瓷土 | 2.29 | 77.46 | 12.99 | 0.7 | 0.15 | 0.77 | 0.47 | 4.67 | 0.76 |
高嶺石 | 3.98 | 75.82 | 15.22 | 0.8 | - | 0.94 | 0.24 | 1.75 | 0.84 |
石英 | 99.56 | - | 0.09 | - | - | - | - | - | - |
煅燒高嶺土 | 0.18 | 54.45 | 42.85 | 0.18 | 0.49 | 1.03 | 0.2 | 0.45 | 0.37 |
長石 | 0.47 | 72.88 | 14.1 | 0.3 | - | 0.65 | 0.45 | 6.94 | 4.43 |
矽灰石 | 1.68 | 50.16 | 0.28 | 0.8 | 70.14 | 45.32 | 0.7 | 0.32 | 0.23 |
瓷質衛生陶瓷坯體與《一種精陶質衛生陶瓷坯體及其製造方法》上述各實施例的精陶質衛生陶瓷坯體的物理性能見表3:
/ | 吸漿速度(毫米/45分鐘) | 乾燥收縮率(%) | 燒成收縮率(%) | 總收縮率(%) | 變形度(毫米) | 吸水率(%) | 乾燥抗折強度(兆帕) | 燒成抗折強度(兆帕) | 200℃膨脹係數(10-6/K) | 吸濕膨脹率(%) | 抗龜裂性能 |
瓷質衛生陶瓷坯體 | 6.1 | 3.1 | 9.5 | 12.3 | 23.6 | 0.2 | 5.4 | 81.2 | 5.3 | - | 無裂 |
實施例1 | 6.3 | 2.6 | 3.9 | 6.4 | 7.5 | 10.1 | 5.3 | 58.6 | 8.6 | 0.22 | 稀疏裂紋 |
實施例2 | 6.2 | 2.6 | 3.6 | 6.1 | 6.9 | 10.8 | 5.3 | 53.5 | 7.7 | 0.09 | 無裂 |
實施例3 | 6.1 | 2.5 | 3.4 | 5.8 | 6.6 | 11.8 | 5.4 | 45.8 | 6.3 | 0.06 | 無裂 |
實施例4 | 6.2 | 2.4 | 3.1 | 5.4 | 5.3 | 13.5 | 5.3 | 43.2 | 5.4 | 0.16 | 稀疏裂紋 |
實施例5 | 6.2 | 2.3 | 3.1 | 5.3 | 5.1 | 13.9 | 5.2 | 39.3 | 5.8 | 0.08 | 無裂 |
實施例6 | 6.3 | 2.5 | 4.3 | 6.7 | 8.6 | 8.2 | 5.3 | 72.5 | 7.5 | 0.09 | 無裂 |
實施例7 | 5.1 | 2.8 | 3.2 | 5.9 | 5.8 | 8.8 | 6.5 | 65.4 | 8.1 | 0.07 | 無裂 |
實施例8 | 5.8 | 2.5 | 3.2 | 5.6 | 6.5 | 9.6 | 5.8 | 63.8 | 7.3 | 0.07 | 無裂 |
從表3可看出,《一種精陶質衛生陶瓷坯體及其製造方法》所有實施例坯體的收縮、變形均遠遠低於瓷質衛生陶瓷坯體。實施例1的矽灰石含量較低,釉面出現稀疏裂紋;實施例2、3的釉面中矽灰石含量的增加,釉面無龜裂現象。實施例4釉面出現稀疏裂紋,而實施例5比實施例4的矽灰石含量多,則實施例5無龜裂現象;這表明隨著矽灰石含量的增加,釉面抗龜裂能力增強。
實施例3與2相比,矽灰石含量增加,雖然抗龜裂能力提高,但燒成抗折強度下降;可見矽灰石含量必須控制在合理的範圍之內。
實施例2與實施例4的矽灰石含量相同,但實施例4的高嶺石和石英含量較少,煅燒高嶺土的含量較多,導致配方化學組成中的SiO2含量降低、Al2O3含量增加,使200℃的熱膨脹係數降低,致使實施例4坯體的釉面所受的壓應力減小,所以釉面出現稀疏裂紋。這表明隨著配方中高SiO2含量的高嶺石和石英的減少,相應的高Al2O3含量的煅燒高嶺土的增加,坯體的抗龜裂能力下降;因此要提高釉面抗龜裂能力,就要增加石英等高SiO2含量的原料。
實施例6與實施例2坯體的釉面均無龜裂現象,但實施例6的長石含量增加,使坯體的吸水率下降、燒成抗折強度提高,同時也使坯體的燒成收縮、總收縮、變形增加;因此為了兼顧吸水率、燒成抗折強度與收縮、變形的平衡,長石的含量需控制在合理的範圍之內,以小於5(質量份)為宜。
實施例7與實施例2相比,球土的含量大幅增加,是坯體的乾燥強度大幅提高,這有利於減少成型坯體的開裂;但同時也使坯體的吸漿速度下降,這會延長注漿工人操作時間,降低生產效率,並且縮短注漿模型使用壽命,因此,球土的含量應控制在合理的範圍之內,以小於30(質量份)為宜。
實施例8的各項性能指標均較為理想,是《一種精陶質衛生陶瓷坯體及其製造方法》的精陶質衛生陶瓷坯體配方的優選方案。
參看圖1、圖2,X-射線衍射儀對瓷質衛生陶瓷坯體和實施例8的坯體礦物組成進行XRD分析比較可看出知,實施例8坯體的石英、莫來石晶相含量比瓷質坯體均大幅增加,玻璃相含量大幅降低,這是精陶質坯體具有遠低於瓷質坯體變形度的根本原因。由圖2可知,實施例8坯體產生了鈣長石晶相,表明坯料中的矽灰石在高溫燒結過程中與鉀長石或鈉長石發生反應,一部分形成鈣長石,一部分形成鈣玻璃相,晶體比玻璃具有更低的表面能,不發生吸濕膨脹。鈣長石的生成,有利於降低坯體的吸濕膨脹率,含鈣的玻璃相比含鹼金屬玻璃相具有較高的化學穩定性,不易被水溶析,吸濕膨脹低。因此,在坯料中引入矽灰石,可降低坯體的吸濕膨脹率,保證了釉面的抗龜裂能力。
《一種精陶質衛生陶瓷坯體及其製造方法》精陶質衛生陶瓷坯體的製造方法,包括原料稱取、泥漿製備、注漿成型、脫模乾燥等步驟。
在泥漿製備步驟中,將按照配方量稱取的原料加入水、電解質,在球磨機中研磨至350目篩余細度占6-10%;經過過篩、除鐵、陳腐,調整泥漿性能至合適,製備成注漿成型用泥漿,泥漿成型性能工藝參數見表4。
精陶質泥漿 物理性能 | 濃度 (克/200毫升) | 細度 (350目篩余%) | V0(秒) | V30(秒) | 吸漿速度 (毫米/45分鐘) |
控制範圍 | 360-380 | 6-10 | 50-70 | 110-130 | 5-6.5 |
與2010年3月前已有技術相比,《一種精陶質衛生陶瓷坯體及其製造方法》主要的區別是泥漿的顆粒細度要細很多。泥漿的顆粒度越細小,反應活性越高,這使造成釉面針孔的雜質的高溫分解過程提前,在釉面熔融之前即充分分解排出,從而可以減少釉面針孔缺陷的發生。由於產品釉面針孔缺陷很少,無需使用化妝土來減少針孔,簡化了生產工藝,消除了因使用化妝土不當而造成的滾釉等缺陷,提高了生產效率和產品合格率。2010年3月前已有技術由於陶質泥漿的顆粒粗大,雜質在釉面熔融之後仍然繼續大量揮發逸出,冷卻後在釉層表面留下針孔缺陷,故需要在坯體與釉層之間使用化妝土抑制有害雜質氣體的揮發以減少針孔,這樣雖然減少了針孔缺陷,但卻增加工藝的複雜性,不但增加了生產成本,而且增加了滾釉等其它缺陷的發生率。
將調整好性能的泥漿注入所需的產品的石膏模型或樹脂模型中,採用石膏模型注漿在60~90分鐘之間,採用樹脂模型高壓注漿在30~60分鐘之後脫模。脫模後的試樣先在30-50℃的環境下乾燥12小時,然後再放入電熱乾燥箱中,在105~110℃下乾燥12小時;將脫模後的產品放置在乾燥室內進行乾燥,根據溫濕度曲線控制乾燥溫度和濕度,最高幹燥溫度一般小於80℃,濕度小於90%。
《一種精陶質衛生陶瓷坯體及其製造方法》精陶質衛生陶瓷坯體,採用手工或機械手方法,將性能調整合適的釉漿噴塗於坯體表面,釉層總厚度為0.4~1.0毫米。所述釉漿的適宜物理性能見表5。
釉漿物理性能 | 濃度(克/200毫升) | 350目篩余(%) | 流動性V0(秒) | 乾燥速度(分鐘/5毫升) |
控制範圍 | 355-365 | 0.05-0.1 | 50-100 | 15-30 |
將乾燥好的施釉的試樣與產品放在隧道窯或梭式窯內燒成衛生陶瓷製品,燒成制度如下:燒成周期為16~21小時,最高燒成溫度為1200~1250℃,保溫時間為30~60分鐘,氧化氣氛。
榮譽表彰
2019年9月29日,《一種精陶質衛生陶瓷坯體及其製造方法》獲2018年河北省專利獎優秀獎。