專利背景
截至2011年4月,鋼渣處理方法很多,相對成熟的工業化方法有熱潑法、熱悶法、水淬法以及風淬法等。熱潑法能處理各種形態
鋼渣,但處理周期長,占地大,環境污染嚴重。池式熱悶法經歷三代改進後,從當初的800℃左右固態鋼渣入池到現在的液態渣直接入池,處理鋼渣的適應性擴大,同時,處理後的鋼渣穩定性好;但是,池式熱悶處理法以工程機械作業為主,自動化作業程度低,崗位作業環境差。風淬法與水淬法相似,只是冷卻介質不同。風淬法與水淬法只能處理液態鋼渣,同時,經風淬法與水淬法處理後的鋼渣粉磨功耗高。
發明內容
專利目的
《一種熔融鋼渣餘熱有壓熱悶處理方法》的目的是提供一種熔融鋼渣餘熱有壓熱悶處理方法。
技術方案
《一種熔融鋼渣餘熱有壓熱悶處理方法》的實施步驟為:
1)傾倒熔融鋼渣,將溫度為800℃-1600℃的熔融鋼渣傾倒於鋼渣預處理室中;
2)輥壓破碎,對鋼渣預處理室內的熔融鋼渣表面噴水霧冷卻並通過輥壓破碎裝置進行輥壓破碎至一定的溫度、粒度,所述的輥壓破碎裝置包括破碎輥與行走台車,所述一定的溫度為200-800℃,所述一定的粒度為300毫米以下,所述的噴水霧與輥壓破碎為交替進行或同時進行;
3)推渣,輥壓破碎裝置將預處理室內已冷卻的塊狀高溫鋼渣推至卸料口入渣槽內;
4)轉運,轉運台車將盛有所述塊狀高溫鋼渣的渣槽轉運至餘熱有壓熱悶罐;
5)消解,對所述的塊狀高溫鋼渣表面噴水產生蒸汽且在交變的蒸汽壓力下消解f-CaO、f-MgO使鋼渣自解粉化,噴水流量隨熱悶罐內的蒸汽壓力變化而自動調整。在某一噴水流量下,當蒸汽壓力隨時間呈正相關時,增大噴水流量;反之,減小噴水流量,蒸汽壓力≥0.1兆帕的消解時間為1-1.5小時。
6)出渣,待罐內溫度小於100℃時,停止噴水霧,打開罐門出渣。
改善效果
《一種熔融鋼渣餘熱有壓熱悶處理方法》占地空間小,無污染,自動化程度高,鋼渣水冷破碎效率高,鋼渣經餘熱有壓自解後性能穩定,適用於建材行業。
附圖說明
圖1為《一種熔融鋼渣餘熱有壓熱悶處理方法》的俯視圖。
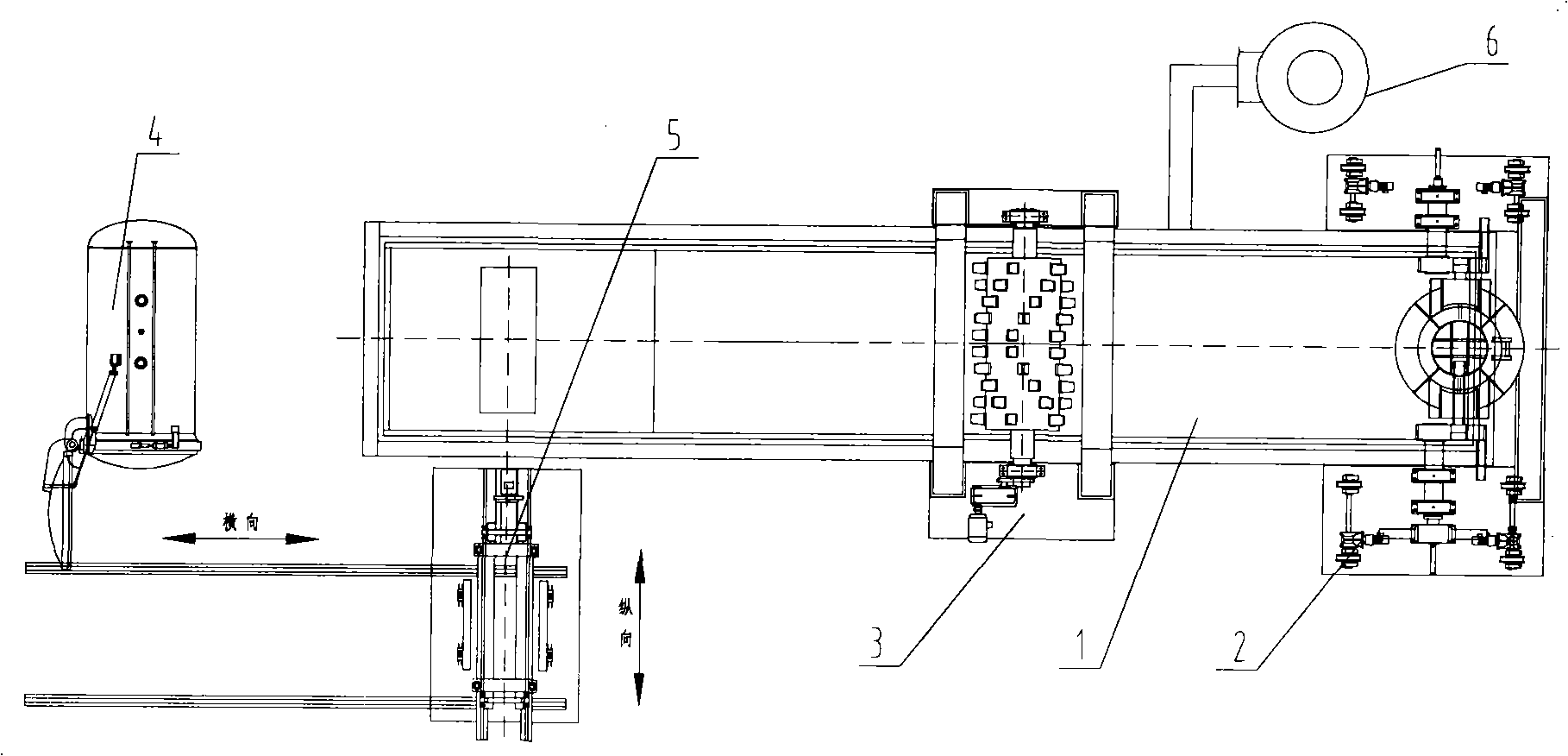
圖1
圖2為圖1中的主視圖。

圖2
附圖主要符號說明:1、鋼渣預處理室;2、渣罐傾翻車裝置;3、輥壓破碎裝置;4、餘熱有壓熱悶罐;5、轉運台車;6、排蒸汽除塵裝置。
技術領域
《一種熔融鋼渣餘熱有壓熱悶處理方法》涉及冶煉行業熔融鋼渣的處理方法,屬於
固體廢棄物處理領域,特別是熔融鋼渣的熱悶處理領域。
權利要求
1.《一種熔融鋼渣餘熱有壓熱悶處理方法》特徵在於,包括以下步驟:
1)傾倒熔融鋼渣,將熔融鋼渣傾倒於鋼渣預處理室中;
2)輥壓破碎,對鋼渣預處理室內的熔融鋼渣表面噴水霧冷卻並通過輥壓破碎裝置進行輥壓破碎至一定的溫度、粒度;
3)推渣,輥壓破碎裝置將鋼渣預處理室內已冷卻的塊狀高溫鋼渣推至卸料口入渣槽內;
4)轉運,轉運台車將盛有所述塊狀高溫鋼渣的渣槽轉運至餘熱有壓熱悶罐:
5)消解,對所述的塊狀高溫鋼渣表面噴水產生蒸汽且在交變的蒸汽壓力下消解f-CaO、f-MgO使鋼渣自解粉化。
2.根據權利要求1所述的一種熔融鋼渣餘熱有壓熱悶處理方法,其特徵在於,在所述的步驟1)中,所述的熔融鋼渣的溫度為800℃-1600℃。
3.根據權利要求1所述的一種熔融鋼渣餘熱有壓熱悶處理方法,其特徵在於,在所述的步驟2)中,所述的噴水霧與輥壓破碎為交替進行或同時進行。
4.根據權利要求1所述的一種熔融鋼渣餘熱有壓熱悶處理方法,其特徵在於,在所述的步驟2)中,所述一定的溫度為200-800℃,所述一定的粒度為300毫米以下。
5.根據權利要求1所述的一種熔融鋼渣餘熱有壓熱悶處理方法,其特徵在於,在所述的步驟2)、步驟3)中,所述的輥壓破碎裝置包括破碎輥與行走台車。
6.根據權利要求1所述的一種熔融鋼渣餘熱有壓熱悶處理方法,其特徵在於,在所述的步驟5)中,噴水流量隨熱悶罐內的蒸汽壓力變化而自動調整。
7.根據權利要求6所述的一種熔融鋼渣餘熱有壓熱悶處理方法,其特徵在於,在所述的步驟5)中,在某一噴水流量下,當蒸汽壓力隨時間呈正相關時,增大噴水流量;反之,減小噴水流量。
8.根據權利要求1所述的一種熔融鋼渣餘熱有壓熱悶處理方法,其特徵在於,在所述的步驟5)中,蒸汽壓力≥0.1兆帕的消解時間為1-1.5小時。
9.根據權利要求1所述的一種熔融鋼渣餘熱有壓熱悶處理方法,其特徵在於,還包括步驟6):
出渣,待罐內溫度小於100℃時,停止噴水霧,打開罐門出渣。
實施方式
實施例1(鋼渣溫度為1600℃)
1)啟動渣罐傾翻車裝置3將盛有熔融鋼渣的渣罐送入鋼渣預處理室1內,傾倒熔融鋼渣後退出,此時鋼渣溫度為1600℃,鋼渣為熔融液態;
2)對熔融液態鋼渣進行打水冷卻,液態鋼渣表面迅速
結殼,冷卻水汽化後經排蒸汽除塵系統6排出;
3)停止噴水,啟動輥壓破碎裝置3對鋼渣表面硬殼進行初次破碎;
4)初次破碎完畢後,硬殼下的液態鋼渣再次被暴露,停止輥壓破碎,二次打水,使液態鋼渣再次結殼;
5)啟動輥壓破碎裝置2進行二次破碎,如此重複步驟2)-5),經4次噴水與破碎後,此時鋼渣溫度為800℃,粒度小於150毫米;
6)再次啟動輥壓破碎裝置3將破碎完畢的固態鋼渣推入渣槽並通過轉運台車5送入餘熱有壓熱悶罐4;
7)餘熱有壓熱悶罐4對高溫固態鋼渣進行有壓熱悶處理。
具體操作是:啟動熱悶罐噴水裝置對罐內鋼渣進行噴水,計算機系統依據罐內蒸汽壓力變化自動調整噴水流量,壓力變化作為控制變數,噴水流量作為被控變數,控制方式採用模糊-PID串級控制,蒸汽壓力≥0.1兆帕的消解時間為1.5小時,待罐內溫度小於100℃時,停止噴水霧,打開罐門出渣。
實施例2(鋼渣溫度為1100℃)
1)啟動渣罐傾翻車裝置2將盛有熔融鋼渣的渣罐進入鋼渣預處理室1內,傾倒熔融鋼渣後退出,此時鋼渣溫度為1100℃,鋼渣為固液混合態;
2)對熔融液態鋼渣進行打水冷卻,液態鋼渣表面迅速結殼,冷卻水汽化後經排蒸汽除塵系統6排出;
3)停止噴水,啟動輥壓破碎裝置3對鋼渣表面硬殼進行初次破碎;
4)初次破碎完畢後,硬殼下的液態鋼渣再次被暴露,二次打水,使液態鋼渣再次結殼;
5)啟動輥壓破碎裝置3進行二次破碎,如此重複步驟2)-5),經3次噴水與破碎後,此時鋼渣溫度為600℃,粒度小於200米;
6)再次啟動輥壓破碎裝置3將破碎完畢的固態鋼渣推入餘熱有壓熱悶罐4;
7)餘熱有壓熱悶罐4對高溫固態鋼渣進行有壓熱悶處理。
具體操作是:啟動熱悶罐噴水裝置對罐內鋼渣進行噴水,計算機系統依據罐內蒸汽壓力變化自動調整噴水流量,壓力變化作為控制變數,噴水流量作為被控變數,控制方式採用模糊-PID串級控制,蒸汽壓力≥0.1兆帕的消解時間為1.3小時,待罐內溫度小於100℃時,停止噴水霧,打開罐門出渣。
實施例3(鋼渣溫度為850℃)
1)啟動渣罐傾翻車裝置2將盛有熔融鋼渣的渣罐送入鋼渣預處理室1內,傾倒熔融鋼渣後退出,此時鋼渣溫度為850℃;
2)對熔融鋼渣同時進行打水冷卻及輥壓破碎,冷卻水汽化後經排蒸汽除塵系統6排出;
3)噴水及輥壓破碎10分鐘後,停止預處理,此時鋼渣溫度為300℃,粒度小於250毫米;
4)再次啟動輥壓破碎裝置3將破碎完畢的固態鋼渣推入餘熱有壓熱悶罐4;
5)餘熱有壓熱悶罐4對高溫固態鋼渣進行有壓熱悶處理。
具體操作是:啟動熱悶罐噴水裝置對罐內鋼渣進行噴水,計算機系統依據罐內蒸汽壓力變化自動調整噴水流量,壓力變化作為控制變數,噴水流量作為被控變數,控制方式採用模糊-PID串級控制,蒸汽壓力≥0.1兆帕的消解時間為1.1小時,待罐內溫度小於100℃時,停止噴水霧,打開罐門出渣。
榮譽表彰
2016年12月7日,《一種熔融鋼渣餘熱有壓熱悶處理方法》獲得第十八屆中國專利優秀獎。