專利背景
連鑄設備裝置是一台雙流弧形板坯連鑄機,配有潤滑脂集中潤滑系統,潤滑部位有結晶器振動及快速換台部位、扇形段軸承和出坯輥道。連鑄設備的功能主要是將鋼水通過冷卻形成固體的鋼坯,其整個過程設備處於惡劣的環境中,其生產工況有高溫、多塵、水淋、低速重載和氧化鱗片進人等特點。實踐證明,只有高質量的潤滑脂才能很好的滿足這些潤滑工況。如扇形段的軸承外部溫度一般在180~260℃之間,要求潤滑脂在高溫下不結焦,不硬化,防止堵塞潤滑脂輸送管道和軸承卡死。異型坯連鑄是在低速重載的條件下進行的,對潤滑脂的極壓性能有一定的要求,但一般極壓添加劑,在高溫下分解成S、N、P等元素的氣體,失去原有的極壓性能,不但污染環境,而且造成設備腐蝕。無機物添加劑,如硼酸鹽和輕鈣等填料,雖然高溫性能很好,但有其致命的缺點:灰分高,高溫分解造成管線堵塞。連鑄機設備中,採用潤滑脂潤滑的有鋼包迴轉台、結晶器、引錠桿、二冷區夾輥及側導輥、拉矯機、傳送輥道及切割機等部位。潤滑脂因高溫流失、硬化和水淋損失,經常使連鑄機軸承受到損害。近年來,連鑄設備用脂有一定的發展,但高溫碳化和硬化問題必須引起注意。隨著冶金行業飛速發展,節能降耗成為關注的問題。對連鑄機使用的潤滑脂提出了更高的要求,連鑄機潤滑脂要具有良好的耐高溫性能,蒸發損失減小,高溫下不變稀、不流失且不易氧化,起到良好的潤滑作用;能夠克服高溫流失、硬化和水淋損失的缺點,有效地防止氧化鱗片進人軸承,從而減少軸承損壞。同時要求具有較高的承載能力和抗摩擦性能,滿足設備在多塵和衝擊負荷下潤滑的要求;具有良好的泵送性能和低的結焦傾向,不堵塞管線,滿足集中供脂潤滑系統;具有較長的使用壽命等。
發明內容
專利目的
《一種專用於冶金行業連鑄機的潤滑脂及其製備方法》要解決的技術問題是提供一種專用於冶金行業連鑄機的潤滑脂及其製備方法,所述的潤滑脂具有優良的高低溫性能,良好的機械安定性、膠體安定性、氧化安定性、抗水性和泵送性,突出的極壓抗磨性和抗腐蝕防鏽性,且製備方法簡單、易操作,產品使用效果好。
技術方案
《一種專用於冶金行業連鑄機的潤滑脂及其製備方法》提供一種專用於冶金行業連鑄機的潤滑脂,所述潤滑脂原料組分按重量份數比為:基礎油A30-50份、基礎油B10-20份、石油磺酸鈣30-50份、乙醇0.3-0.8份、石油醚1-1.5份、醋酸0.5-1份、脂肪酸2.5-3份、
硼酸0.5-1份、水1-2份、
氫氧化鈣2.5-3份、碳酸鈣0.5-1份、抗氧劑1-2份、防鏽劑0.5-1份、極壓劑0.6-1.5份。優選的,所述基礎油A為高粘度深度精製的礦物油150BS,所述基礎油B為酯類合成基礎油,所述抗氧劑為磷酸丁辛基鋅鹽,所述防鏽劑為烯基丁二酸,所述極壓抗磨劑為磷酸三甲酚酯。一種專用於冶金行業連鑄機的潤滑脂的製備方法,所述製備方法,具體包括以下步驟:(1)按配方比例將30%-50%的基礎油A投入反應釜內,並升溫到40-60℃; (2)將配方比例的石油磺酸鈣、乙醇、
石油醚、醋酸按順序投入到反應釜內並攪拌均勻,繼續升溫,當溫度達到80-100℃時,恆溫反應50-70分鐘;(3)反應完成後,升溫至100-120℃,加入脂肪酸、硼酸和水,攪拌3-5分鐘後加入氫氧化鈣進行皂化反應,保持溫度100-120℃,反應時間為20-40分鐘;(4)皂化反應結束後,升溫至130-140℃時加入碳酸鈣和剩餘基礎油A,然後繼續升溫進行煉製,升溫至200-230℃時,停止升溫,攪拌20-40分鐘,得混合物;(5)將步驟(4)攪拌均勻的混合物轉入到調和釜中,循環攪拌,加入配方比例的基礎油B和抗氧劑,當溫度降到120-140℃時,進行攪拌煉製;(6)當溫度降到90-110℃時,將防鏽劑、極壓抗磨劑加入到調和釜中,並攪拌均勻,得混合物;(7)將步驟(6)的混合物循環攪拌20-40分鐘後,在20-30兆帕壓力下均質、脫氣,然後取樣進行檢測,得潤滑脂。
改善效果
《一種專用於冶金行業連鑄機的潤滑脂及其製備方法》技術方法公開的潤滑脂具有優良的高低溫性能,良好的機械安定性、膠體安定性、氧化安定性、抗水性和泵送性,突出的極壓抗磨性和抗腐蝕防鏽性,主要適用於各種連鑄機大包迴轉台齒圈,連鑄機二冷區、扇形段、拉矯機、輸送輥道軸承等部位的潤滑,也適用於鋼鐵工業軋機軋輥軸承等設備及其他高溫、重負荷、多水場合設備的潤滑,適用溫度在-30℃~260℃環境中,該發明公開的潤滑脂有以下特點:
1、優異的耐高溫性能和氧化安定性:滴點指標是反映其高溫性能的直觀指標之一,該發明技術方法公開的潤滑脂滴點可達到300℃以上,高溫下潤滑脂不會變成液體,再回復到一般溫度時,它能完全回復到原先組織,這與其他潤滑脂不同,該發明技術方法公開的潤滑脂可較長時間在260℃工作環境下使用,其他脂會出現炭化、變硬或變成膠質狀物質,而該產品仍保持柔軟的油脂狀結構,因此具有良好的抗氧化能力。
2、優異的泵送性:在各種潤滑系統中,潤滑脂集中潤滑是供給大量潤滑點潤滑的最有效、最經濟的方法。潤滑脂的低析油性、老化傾向小和良好的泵送性是判斷潤滑脂能夠集中潤滑的重要依據。《一種專用於冶金行業連鑄機的潤滑脂及其製備方法》技術方法公開的潤滑脂在貯存期間具有低析油性、低溫流動性和抗老化能力,適合於潤滑脂集中潤滑系統。連鑄機集中潤滑系統泵送管線很長,特別是在冬季需要潤滑產品具有良好的低溫泵送性,《一種專用於冶金行業連鑄機的潤滑脂及其製備方法》技術方法公開的潤滑脂體系中含有大量的球形碳酸鈣,在低溫下,這種顆粒阻止了基礎油凝結的趨勢,並憑藉其自身晶體間的滾動和晶層間的滑移,降低了低溫啟動阻力,《一種專用於冶金行業連鑄機的潤滑脂及其製備方法》技術方法公開的潤滑脂即使在-30℃的條件下,也能滿足集中潤滑系統的要求。
3、優異的潤滑和抗水性能:該發明技術方法公開的潤滑脂密度大於水的密度,抑制了由於密度小而浮於水分子表面、脫離潤滑點的趨勢,用在潮濕、浸水和有水沖洗的地方,具有優良的抗水性能,可最大限度地克服遇水乳化的問題,保證了良好的潤滑。
4、優異的防鏽性和極壓抗磨性能:該發明技術方法公開的潤滑脂稠化劑本身就是一種防鏽劑,基礎脂就具有防鏽和抗腐蝕性能,因此在防鏽性能上沒有其他潤滑脂可與之相比,不加防腐劑的該類潤滑脂基礎脂在軸承防鏽試驗中也可達要求,銅片、鋼片腐蝕試驗均合格,即使不加任何添加劑,該發明技術方法公開的潤滑脂仍然具有十分良好的極壓抗磨性能,原因是非牛頓體高鹼性磺酸鈣、硼酸鈣、醋酸鈣、羥基硬脂酸鈣以及它們的相互作用,起到極壓抗磨作用。同時選用的高粘度深度精製的礦物油,在高負荷下仍能很好的形成優異的油膜厚度,PD能達到6000牛以上。
5、優異的機械安定性和粘附性:《一種專用於冶金行業連鑄機的潤滑脂及其製備方法》技術方法公開的潤滑脂經10萬次剪下後錐入度基本不變,保證了該產品不會因運轉後產品變稀流失;具有極強的粘附性,不會因高速運轉而發生甩脂現象。
技術領域
《一種專用於冶金行業連鑄機的潤滑脂及其製備方法》涉及潤滑油脂領域,具體涉及一種專用於冶金行業連鑄機的潤滑脂及其製備方法。
權利要求
1.《一種專用於冶金行業連鑄機的潤滑脂及其製備方法》的特徵在於 :所述潤滑脂原料組分按重量份數比為:基礎油 A30-50 份、基礎油 B 10-20 份、石油磺酸鈣 30-50 份、乙醇 0.3-0.8 份、石油醚 1-1.5 份、醋酸 0.5-1 份、脂肪酸 2.5-3 份、硼酸 0.5-1 份、水 1-2 份、氫氧化鈣 2.5-3份、碳酸鈣 0.5-1 份、抗氧劑 1-2 份、防鏽劑 0.5-1 份、極壓劑 0.6-1.5 份;所述基礎油A 為高粘度深度精製的礦物油 150BS,所述基礎油 B 為酯類合成基礎油,所述抗氧劑為磷酸丁辛基鋅鹽,所述防鏽劑為烯基丁二酸,所述極壓抗磨劑為磷酸三甲酚酯。
2.根據權利要求 1 所述的一種專用於冶金行業連鑄機的潤滑脂的製備方法,其特徵在於:所述製備方法,具體包括以下步驟:(1)按配方比例將 30%-50% 的基礎油 A 投入反應釜內,並升溫到 40-60℃ ;(2)將配方比例的石油磺酸鈣、乙醇、石油醚、醋酸按順序投入到反應釜內並攪拌均勻,繼續升溫,當溫度達到 80-100℃時,恆溫反應 50-70 分鐘;(3)反應完成後,升溫至 100-120℃,加入脂肪酸、硼酸和水,攪拌 3-5 分鐘後加入氫氧化鈣進行皂化反應,保持溫度 100-120℃,反應時間為 20-40 分鐘;(4)皂化反應結束後,升溫至 130-140℃時加入碳酸鈣和剩餘基礎油 A,然後繼續升溫進行煉製,升溫至200-230℃時,停止升溫,攪拌 20-40 分鐘,得混合物;(5)將步驟(4)攪拌均勻的混合物轉入到調和釜中,循環攪拌,加入配方比例的基礎油 B 和抗氧劑,當溫度降到 120-140℃時,進行攪拌煉製;(6)當溫度降到 90-110℃時,將防鏽劑、極壓抗磨劑加入到調和釜中,並攪拌均勻,得混合物;(7)將步驟(6)的混合物循環攪拌 20-40 分鐘後,在 20-30兆帕 壓力下均質、脫氣,然後取樣進行檢測,得潤滑脂。
實施方式
《一種專用於冶金行業連鑄機的潤滑脂及其製備方法》所述潤滑脂原料組分按重量份數比為:基礎油A30-50份、基礎油B10-20份、石油磺酸鈣30-50份、乙醇0.3-0.8份、石油醚1-1.5份、醋酸0.5-1份、脂肪酸2.5-3份、硼酸0.5-1份、水1-2份、
氫氧化鈣2.5-3份、碳酸鈣0.5-1份、抗氧劑1-2份、防鏽劑0.5-1份、極壓劑0.6-1.5份,所述基礎油A為高粘度深度精製的礦物油150BS,所述基礎油B為酯類合成基礎油,所述抗氧劑為磷酸丁辛基鋅鹽,所述防鏽劑為烯基丁二酸,所述極壓抗磨劑為磷酸三甲酚酯。該發明所述製備方法,具體包括以下步驟:將20千克基礎油A投入反應釜內,並升溫到40-60℃,將40千克石油磺酸鈣、0.5千克乙醇、1.5千克石油醚、1千克醋酸按順序投入到反應釜內並攪拌均勻,繼續升溫,當溫度達到80-100℃時,恆溫反應50-70分鐘,反應完成後,升溫至100-120℃,加入3千克脂肪酸、1千克硼酸和1千克水,攪拌3-5分鐘後加入2.5千克氫氧化鈣進行皂化反應,保持溫度100-120℃,反應時間為20-40分鐘,皂化反應結束後,升溫至130-140℃時加入1千克碳酸鈣和剩餘的20千克基礎油A,然後繼續升溫進行煉製,升溫至200-230℃時,停止升溫,攪拌20-40分鐘,得混合物,將混合物轉入到調和釜中,循環攪拌,加入20千克基礎油B和1千克抗氧劑,當溫度降到120-140℃時,進行攪拌煉製,當溫度降到90-110℃時,將防鏽劑、極壓抗磨劑加入到調和釜中,並攪拌均勻,得混合物,將混合物循環攪拌20-40分鐘後,在20-30兆帕壓力下均質、脫氣,然後取樣進行檢測,得潤滑脂。該發明技術方法公開的潤滑脂綜合了複合鋰基潤滑脂、聚脲潤滑脂、複合鋁基潤滑脂等潤滑脂的優點,內在性能非常好,尤其是套用於高溫、潮濕、水流、腐蝕、重載、衝擊負荷存在的惡劣環境時性能優勢明顯,且成本較低,具有良好的發展前景。經檢測,該發明技術方法公開的潤滑脂的各項指標如下:
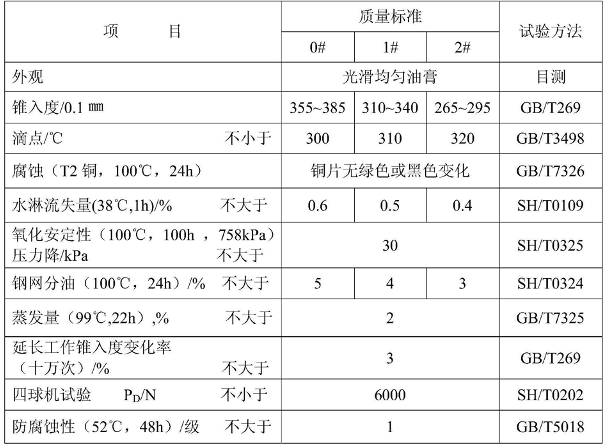
指標
榮譽表彰
2021年8月16日,《一種專用於冶金行業連鑄機的潤滑脂及其製備方法》獲得安徽省第八屆專利獎優秀獎。