專利背景
滌綸高強絲具有強度高、耐磨性好、彈性好等特點,是
滌綸工業絲的一個特殊品種。截至2017年8月,全球主要沿用滌綸工業絲的生產路線,可以紡制強度為6.0厘牛/分特克斯左右的中高強滌綸長絲,主要工藝過程包括:將聚合物在螺桿加壓機中熔融擠出,但不經過濾的熔體在擠出紡絲過程中產品質量不穩定,噴絲板損壞嚴重,造成生產成本上升,擠出的的熔體粘度一般在0.4分升/克—0.65分升/克間,粘度較低,不能滿足高粘度的紡絲要求,接著經噴絲孔擠出形成細流、側吹風冷卻、絲條上油卷繞成型,紡絲速度在600—1000米/分鐘之間,製得所需的中高強度的滌綸絲,但是這種中高強度的滌綸絲線密度低、強度弱、彈性差、容易出線頭、易起褶皺。
發明內容
專利目的
《一種基於熔體紡絲法生產滌綸高強絲的工藝》的目的在於提供一種基於熔體紡絲法生產滌綸高強絲的工藝,在熔體紡絲傳統工藝基礎上,增加了自動排渣過濾裝置和液相增粘裝置,提高了熔體粘度,降低了生產成本。
技術方案
《一種基於熔體紡絲法生產滌綸高強絲的工藝》包括聚合物熔融擠壓—熔體過濾—液相增粘—噴絲孔擠出形成細流—側吹風冷卻—絲條上油—卷繞成型工藝步驟,具體步驟如下:
(1)聚合物熔融擠壓:聚合物自料斗進入螺桿擠壓機進行熔融;
(2)熔體過濾:熔融後的聚合物熔體進入自動排渣過濾裝置中,熔體依次經過緩衝第一篩網、緩衝第二篩網進行粗濾,接著經過濾網過濾得到純淨的熔體;濾渣通過大孔墊板進入到錐形收納腔中;過濾後純淨的熔體通過自動單向閥經電磁流量計流向保溫管道內,根據流量設定值,自動單向閥自動開啟關閉,自動單向閥關閉時,伴隨擠出機的持續出料,將收納腔中的濾渣帶出,進入到收集罐,通過透明管道觀察,無濾渣時,關閉電磁閥,自動單向閥即開啟;
(3)液相增粘:保溫管道下端設定第一分支管和第二分支管兩個分支,第一分支管和第二分支管下端連線了相同的液相增粘反應釜,過濾後的低粘度熔體進入分配器進行分配後進入釜心內反應成膜,釜壁上設有第一加熱絲和第二加熱絲,根據成膜反應溫度進行加熱,膜因重力作用均勻流下,得到高粘度熔體,反應產生的小分子副反應物分別從第一閥門和第二閥門被真空吸出;
(4)噴絲孔擠出形成細流:反應後的高粘度熔體從釜心底端分別流向兩個液相增粘反應釜的底端,再從反應釜的底端閥門流出匯聚在管道處,將匯聚後的熔體輸送至紡絲箱體,再經計量泵進入紡絲組件後從噴絲頭擠出細流,由緩冷加熱器加熱;
(5)擠出的細流再由側吹風裝置冷卻成型,然後進入紡絲甬道;
(6)絲條上油卷繞成型:滌綸紡絲經油輪在絲表面上油,經導絲盤拉伸,進行高溫、鬆弛熱定型、卷繞成型,製得成品。
進一步,步驟(1)所述的紡絲螺桿熔融溫度為302℃—326℃。
進一步,步驟(2)所述的自動排渣過濾裝置與螺桿擠壓機通過螺栓水平螺接;所述的緩衝第二篩網孔徑為緩衝第一篩網的五分之一。
進一步,步驟(2)所述的電磁流量計設定在保溫管道入口與自動單向閥之間。
進一步,步驟(2)所述的自動單向閥自動開啟關閉的條件為:當流量≥1.2立方米/分鐘時,正常運行,當流量<1.2立方米/分鐘時,自動單向閥關閉,電磁閥隨即開啟;自動單向閥、電磁流量計與電磁閥通過無線磁電連線。
進一步,步驟(3)所述的低粘度熔體粘度為0.53分升/克—0.66分升/克,高粘度熔體粘度為0.98分升/克—1.21分升/克。
進一步,步驟(3)所述的反應成膜的條件為反應溫度為295℃—325℃、停留時間為80—105分鐘、釜內真空度70帕—120帕。
進一步,步驟(4)所述的緩冷加熱溫度為320℃,高度為330毫米。
進一步,步驟(5)所述的冷卻成型,吹風溫度為21℃,濕度為75%,風速為0.55m/s;所述的紡絲甬道設計為錐形,設計有多孔,平衡內外氣流。
進一步,步驟(6)所述的高溫、鬆弛熱定型的溫度為200℃—248℃;卷繞成型的工藝速度為4665米/分鐘。
進一步,所述的的滌綸高強絲成品線密度為866分特克斯,強度為6.6厘牛/分特克斯—8.5厘牛/分特克斯,彈性模數為97—146厘牛/分特克斯,變異係數<3.2%。
改善效果
《一種基於熔體紡絲法生產滌綸高強絲的工藝》在
熔體紡絲傳統工藝基礎上,增加了自動排渣過濾裝置和液相增粘裝置,自動排渣過濾裝置與螺桿擠壓機通過螺栓水平螺接,其中設有無線磁電連線的自動單向閥、電磁流量計和電磁閥,根據流量設定值,自動單向閥和電磁閥可自動開啟關閉;熔體依次經過緩衝第一篩網、緩衝第二篩網進行粗濾,接著經過濾網過濾得到純淨的熔體;濾渣則伴隨擠出機的持續出料將濾渣帶出。在過濾裝置下方設定了兩個相同的液相增粘反應釜,熔體粘度由0.53分升/克—0.66分升/克增加到0.98分升/克—1.21分升/克。得到的滌綸高強絲成品線密度為866分特克斯,強度為6.6厘牛/分特克斯—8.5厘牛/分特克斯,彈性模數為97—146厘牛/分特克斯,變異係數<3.2%,強度高,彈性好,且降低了生產成本。
附圖說明
圖1為《一種基於熔體紡絲法生產滌綸高強絲的工藝》一種熔體紡絲傳統工藝示意圖。
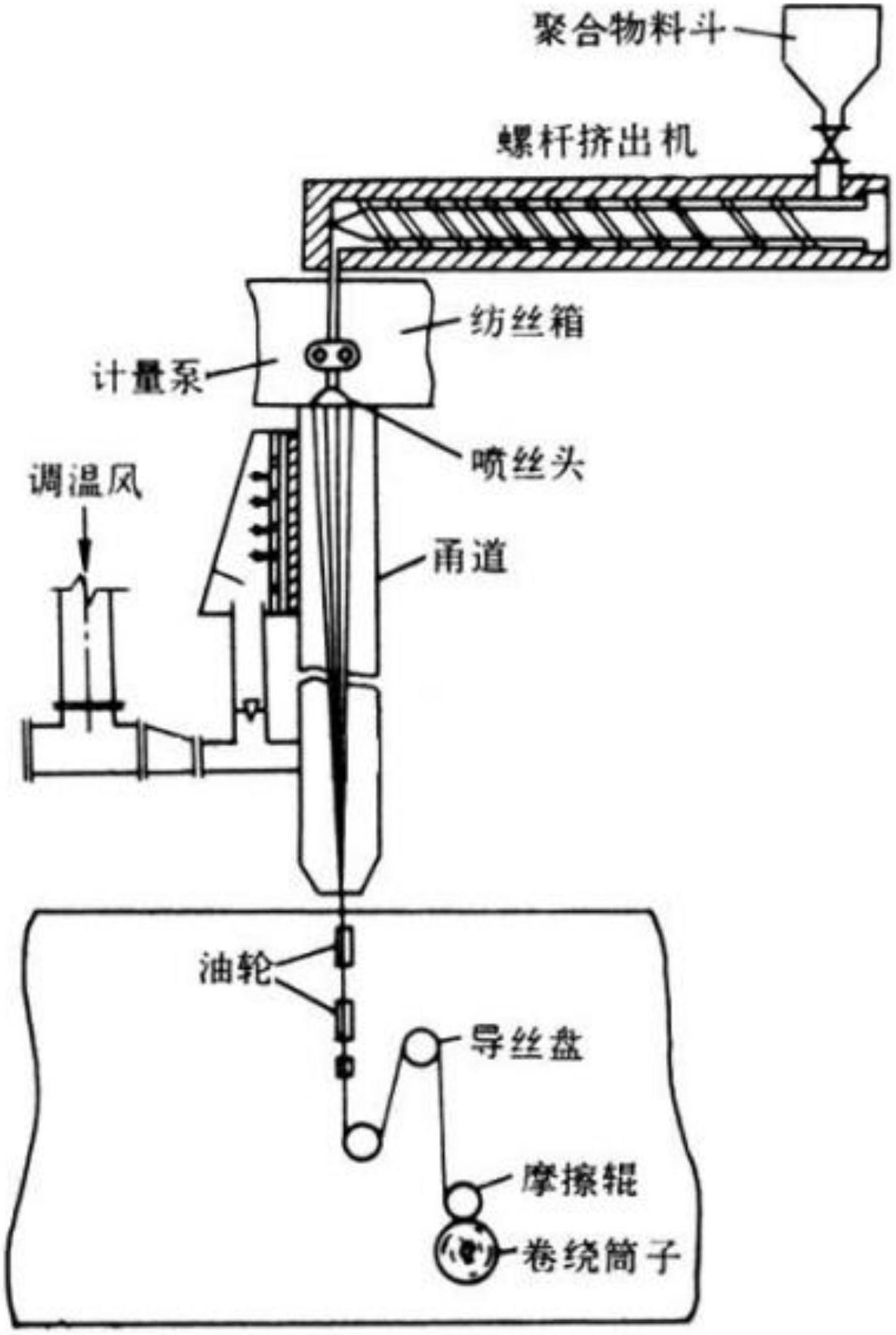
圖1
圖2為《一種基於熔體紡絲法生產滌綸高強絲的工藝》一種基於熔體紡絲法生產滌綸高強絲的工藝結構示意圖。

圖2
圖2附圖示註:1、料斗;2、螺桿擠壓機;3、螺栓;4、緩衝第一篩網;5、緩衝第二篩網;6、過濾網;7、自動單向閥;8、大孔墊板;9、錐形收納腔;10、電磁流量計;11、保溫管道;12第一分支管、;13、第二分支管;14、第一閥門;15、第二閥門;16、釜壁;17、分配器;18、第一加熱絲;19釜心、;20、第二加熱絲;21、底端閥門;22、管道;23、電磁閥;24、收集罐;25、透明管道。
技術領域
《一種基於熔體紡絲法生產滌綸高強絲的工藝》涉及紡絲技術領域,具體涉及一種基於熔體紡絲法生產滌綸高強絲的工藝。
權利要求
1.一種基於熔體紡絲法生產滌綸高強絲的工藝,其特徵在於:包括聚合物熔融擠壓—熔體過濾—液相增粘—噴絲孔擠出形成細流—側吹風冷卻—絲條上油—卷繞成型工藝步驟,具體步驟如下:
(1)聚合物熔融擠壓:聚合物自料斗進入螺桿擠壓機進行熔融;
(2)熔體過濾:熔融後的聚合物熔體進入自動排渣過濾裝置中,熔體依次經過緩衝第一篩網、緩衝第二篩網進行粗濾,接著經過濾網過濾得到純淨的熔體;濾渣通過大孔墊板進入到錐形收納腔中;過濾後純淨的熔體通過自動單向閥經電磁流量計流向保溫管道內,根據流量設定值,自動單向閥自動開啟關閉,自動單向閥關閉時,伴隨擠出機的持續出料,將收納腔中的濾渣帶出,進入到收集罐,通過透明管道觀察,無濾渣時,關閉電磁閥,自動單向閥即開啟;
(3)液相增粘:保溫管道下端設定第一分支管和第二分支管兩個分支,第一分支管和第二分支管下端連線了相同的液相增粘反應釜,過濾後的低粘度熔體進入分配器進行分配後進入釜心內反應成膜,釜壁上設有第一加熱絲和第二加熱絲,根據成膜反應溫度進行加熱,膜因重力作用均勻流下,得到高粘度熔體,反應產生的小分子副反應物分別從第一閥門和第二閥門被真空吸出;
(4)噴絲孔擠出形成細流:反應後的高粘度熔體從釜心底端分別流向兩個液相增粘反應釜的底端,再從反應釜的底端閥門流出匯聚在管道處,將匯聚後的熔體輸送至紡絲箱體,再經計量泵進入紡絲組件後從噴絲頭擠出細流,由緩冷加熱器加熱;
(5)擠出的細流再由側吹風裝置冷卻成型,然後進入紡絲甬道;
(6)絲條上油卷繞成型:滌綸紡絲經油輪在絲表面上油,經導絲盤拉伸,進行高溫、鬆弛熱定型、卷繞成型,製得成品。
2.根據權利要求1所述的一種基於熔體紡絲法生產滌綸高強絲的工藝,其特徵在於:步驟(1)中熔融溫度為302℃—326℃。
3.根據權利要求1所述的一種基於熔體紡絲法生產滌綸高強絲的工藝,其特徵在於:步驟(2)所述的自動排渣過濾裝置與螺桿擠壓機通過螺栓水平螺接;所述的緩衝第二篩網孔徑為緩衝第一篩網的五分之一。
4.根據權利要求1所述的一種基於熔體紡絲法生產滌綸高強絲的工藝,其特徵在於:步驟(2)所述的電磁流量計設定在保溫管道入口與自動單向閥之間。
5.根據權利要求1所述的一種基於熔體紡絲法生產滌綸高強絲的工藝,其特徵在於:步驟(2)所述的自動單向閥自動開啟關閉條件為:當流量≥1.2立方米/分鐘時,正常運行,當流量<1.2立方米/分鐘時,自動單向閥關閉,電磁閥隨即開啟;自動單向閥、電磁流量計與電磁閥通過無線磁電連線。
6.根據權利要求1所述的一種基於熔體紡絲法生產滌綸高強絲的工藝,其特徵在於:步驟(3)所述的低粘度熔體粘度為0.53分升/克—0.66分升/克,高粘度熔體粘度為0.98分升/克—1.21分升/克。
7.根據權利要求1所述的一種基於熔體紡絲法生產滌綸高強絲的工藝,其特徵在於:步驟(3)所述的反應成膜的條件為反應溫度為295℃—325℃、停留時間為80—105分鐘、釜內真空度70帕—120帕。
8.根據權利要求1所述的一種基於熔體紡絲法生產滌綸高強絲的工藝,其特徵在於:步驟(4)所述的緩冷加熱器溫度為320℃,緩冷加熱器的高度為330毫米。
9.根據權利要求1所述的一種基於熔體紡絲法生產滌綸高強絲的工藝,其特徵在於:步驟(5)所述的冷卻成型,吹風溫度為21℃,濕度為75%,風速為0.55m/s;所述的紡絲甬道設計為錐形,設計有多孔,平衡內外氣流。
10.根據權利要求1所述的一種基於熔體紡絲法生產滌綸高強絲的工藝,其特徵在於:步驟(6)所述的高溫、鬆弛熱定型的溫度為200℃—248℃;卷繞成型的工藝速度為4665米/分鐘。
實施方式
如圖1所示,一種熔體紡絲傳統工藝,包括聚合物熔融擠壓—噴絲孔擠出形成細流—側吹風冷卻—絲條上油卷繞成型工藝步驟;
(1)聚合物熔融擠壓:聚合物自料斗1進入螺桿擠壓機2進行熔融,紡絲螺桿熔融溫度為310℃,熔融後擠出;
(2)噴絲孔擠出形成細流:擠出的熔體粘度為0.59分升/克,將熔體輸送至紡絲箱體,再經計量泵進入紡絲組件後從噴絲頭擠出,由緩冷加熱器加熱,緩冷加熱溫度為320℃,高度是330毫米;
(3)擠出的細流再由側吹風裝置冷卻成型,吹風溫度為21℃,濕度為75%,風速:0.55m/s。然後進入紡絲甬道,紡絲甬道設計為錐形,設計有多孔,平衡內外氣流;
(4)絲條上油卷繞成型:滌綸紡絲經油輪在絲表面上油,經導絲盤拉伸,在溫度為232℃的條件下,進行高溫、鬆弛熱定型;並在工藝速度890米/分鐘的範圍內卷繞成型,製得成品。本實施例生產的滌綸高強絲,線密度為1286分特克斯,強度為3.6厘牛/分特克斯—5.7厘牛/分特克斯,彈性模數為33—65厘牛/分特克斯,變異係數<6.4%;成品滌綸線密度低、強度弱、易起褶皺。
如圖2所示,一種基於熔體紡絲法生產滌綸高強絲的工藝,包括包括聚合物熔融擠壓—熔體過濾—液相增粘—噴絲孔擠出形成細流—側吹風冷卻—絲條上油—卷繞成型工藝步驟。
(1)聚合物熔融擠壓:聚合物自料斗1進入螺桿擠壓機2進行熔融,紡絲螺桿熔融溫度為310℃;
(2)熔體過濾:熔融後的聚合物熔體進入與螺桿擠壓機2通過螺栓3水平螺接的自動排渣過濾裝置中,熔體依次經過的緩衝第一篩網4、緩衝第二篩網5進行粗濾,最後經過濾網6過濾得到純淨的熔體。濾渣通過大孔墊板8進入到錐形收納腔9中。保溫管道11入口與自動單向閥7間設有電磁流量計10,過濾後純淨的熔體通過自動單向閥7經電磁流量計10流向保溫管道11內,當流量≥1.2立方米/分鐘時,正常運行,當流量<1.2立方米/分鐘時,自動單向閥7關閉,電磁閥23開啟,伴隨擠出機的持續出料,將收納腔9中的濾渣帶出,進入到收集罐24,通過透明管道25觀察,無濾渣時,關閉電磁閥23,自動單向閥7即開啟;
(3)液相增粘:進入保溫管11的熔體粘度為0.61分升/克,為低粘度熔體,保溫管道11下端設定第一分支管12和第二分支管13兩個分支,第一分支管12和第二分支管13下端連線
了相同的液相增粘反應釜,低粘度熔體進入分配器17進行分配後進入釜心19內反應成膜,釜壁16上設有第一加熱絲18和第二加熱絲20,根據成膜反應溫度進行加熱,膜因重力作用均勻流下,反應溫度為300℃、停留時間為96分鐘、釜內真空度113帕,反應產生的小分子副反應物分別從第一閥門14和第二閥門15被真空吸出,反應後的熔體粘度為1.01分升/克,為高粘度熔體;
(4)噴絲孔擠出形成細流:反應後的高粘度熔體從釜心底端分別流向兩個液相增粘反應釜的底端,再從反應釜的底端閥門21流出匯聚在管道22處,將匯聚後的高粘度熔體輸送至紡絲箱體,再經計量泵進入紡絲組件後從噴絲頭擠出,由緩冷加熱器加熱,緩冷加熱溫度為320℃,高度是330毫米;
(5)同實施例1步驟(3);
(6)絲條上油卷繞成型:滌綸紡絲經油輪在絲表面上油,經導絲盤拉伸,在溫度為232℃的條件下,進行高溫、鬆弛熱定型;並在工藝速度4665米/分鐘的範圍內卷繞成型,製得成品。該實施例生產的滌綸高強絲,線密度為866分特克斯,強度為6.6厘牛/分特克斯—8.5厘牛/分特克斯,彈性模數為97—146厘牛/分特克斯,變異係數<3.2%。
榮譽表彰
2021年8月16日,《一種基於熔體紡絲法生產滌綸高強絲的工藝》獲得安徽省第八屆專利獎優秀獎。