電弧爐無渣出鋼技術是電弧爐煉鋼完畢出鋼時鋼渣分離,將渣子留在爐內,鋼水流入鋼包中的出鋼技術。常見的方法有虹吸出鋼法、中心底出鋼法、偏心爐底出鋼法等
基本介紹
- 中文名:電弧爐無渣出鋼技術
- 外文名:EAF tapping withoutslag
- 領域:鋼鐵冶煉
- 常用方法:偏心底出鋼
- 學科:冶金工程
- 目的:去除爐渣
介紹,電弧爐煉鋼,虹吸出鋼法,中心底出鋼法,偏心爐底出鋼法,其他無渣出鋼技術,套用效果,
介紹
隨著冶金技術的不斷發展,電弧爐煉鋼法逐步由電爐獨立冶煉發展成電弧爐—爐外精煉爐雙聯的兩步煉鋼工藝。在電弧爐內完成熔化、氧化甚至只完成熔化、升溫任務,即將初煉鋼液倒入精煉爐(鋼包)內,由精煉爐完成脫氧、脫硫及合金化等任務。在這裡,出鋼是兩步化煉鋼的中間環節,氧化性爐渣不宜隨鋼液帶入精煉爐。也即傳統的鋼渣混出的出鋼法不能滿足爐外精煉技術的要求,由此引發了多種電弧爐無渣出鋼技術的開發和套用。較重要的有虹吸出鋼法、中心底出鋼法和偏心底出鋼法3種,其中又以偏心底出鋼套用最為廣泛。
電弧爐煉鋼
利用電弧的熱效應加熱爐料進行熔煉的煉鋼方法。交流電通過3個石墨電極輸入爐內,在電極下端與金屬料之間產生電弧,利用電弧的高溫直接加熱爐料,使煉鋼過程得以進行。電弧爐煉鋼以廢鋼為主要原料,根據爐襯材質和造渣材料不同,有鹼性法和酸性法之分。最常用的是鹼性法。電弧爐煉鋼以電能作熱源,避免了氣體熱源所含硫分對鋼的污染;操作工藝靈活,爐渣和爐氣均可調控成氧化性或還原性;強還原性可使爐料中所含的貴重元素鉻、鎳、鎢、鉬、釩、鈦等極少燒損;爐溫高、易控制;產品質量高。
電弧爐煉鋼的基本工藝包括扒渣補爐、裝入金屬爐料、送電、熔化、氧化、還原精煉和出鋼。按照所冶煉鋼種特點的不同,可有不同的操作方法,傳統的工藝主要是具有熔化、氧化、還原三個期的操作,還原期採用擴散脫氧和沉澱脫氧,需造白渣或電石渣,每爐冶煉要3~4h,電耗高達600~700kWh/t。隨著技術的不斷發展,電弧爐煉鋼工藝也發生了很大變化,熔化期採用輔助能源加速熔化,如噴吹油—氧、天然氣—氧或煤粉—氧,每爐熔化時間縮短了15~20min,電耗可減少50~60kWh/t;氧化期採取提前脫磷、強化用氧、噴粉造泡沫渣、快速升溫等措施,可使氧化脫碳量從傳統工藝的0.3%降低到0.1%~0.15%,從而氧化期可縮短時間50%以上。還原期則將傳統工藝中的擴散脫氧為主改為沉澱脫氧為主,擴散脫氧為輔,不僅能達到預期的精煉效果,鋼質量有保證且縮短還原時間60%以上。工藝的改進在鋼水質量得到保證的同時,生產率亦隨之提高20%左右,電耗降低10%~15%,電極消耗降低8%左右,取得可觀的經濟效益。
虹吸出鋼法
20世紀70年代末期,聯邦德國克虜伯鋼公司(Krupp Stahl AG)開發了一種簡易的鋼渣分離技術,即根據虹吸原理,把電弧爐原水平出鋼口改為傾斜式,出鋼口爐內端埋入鋼液內一定的深度,爐外端高於鋼液面,如圖1所示。出鋼口與水平面成18°~30°傾角,出鋼時爐體傾倒約20°~30°,工藝上採用留鋼留渣操作,留鋼量約為10%左右,留渣效果普遍可達90%以上。80年代虹吸出鋼技術在歐洲得到了較為廣泛的套用。
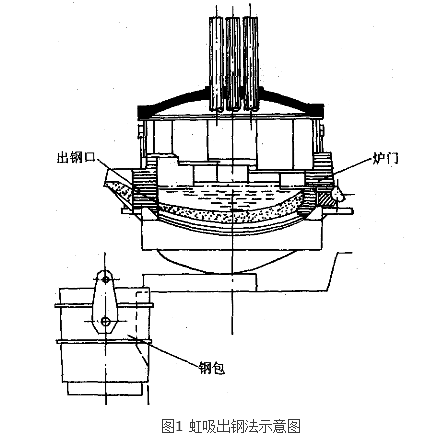
中心底出鋼法
為了擴大爐壁水冷麵積,提高爐體壽命,德國曼內斯曼—德馬克公司(MANNES-MANN-DEMAG AG)和蒂森特殊鋼公司(ThyssenEdelstahlwerke AG)合作開發了中心底出鋼技術並獲成功,第1座中心底出鋼(CBT)電弧爐於1979年投入生產。它的出鋼口設在爐底中心部位,取消了原出鋼槽,並且出鋼口向下,從而使出鋼時的水平拋物線鋼流改變為豎直向下的鋼流。這一技術是電弧爐出鋼法的重大改進。儘管出鋼時不需搖動爐體,爐壁的水冷麵積得到最大值,但卻由於出鋼時產生渦流而不能實現完全無渣出鋼,故套用不廣。
偏心爐底出鋼法
曼內斯曼—德馬克和蒂森兩公司與丹麥特殊鋼廠合作,在中心底出鋼的基礎上,開發了偏心底出鋼(EBT)技術。即在爐底後部增加一個鼻狀出鋼箱,把出鋼口系統置於出鋼箱的下部(如圖2)。第1座偏心爐底出鋼電弧爐於1983年在丹麥特殊鋼廠投產。因偏心爐底出鋼電弧爐具有搖爐角度小(約12°),留鋼量控制準確,留渣效果最佳等特點,立即得到了廣泛的套用。到1990年世界上採用這一技術的電爐已超過50座。
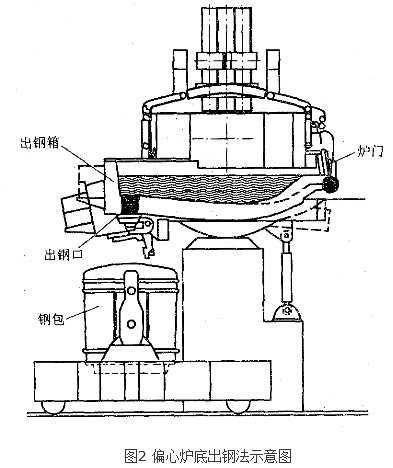
其他無渣出鋼技術
(1)美國懷汀(Whiting)公司側面爐底出鋼系統(SBT),類似於虹吸出鋼法,但出鋼口是採用塞桿開閉的;
(2)加拿大恩普科(Empco)公司開發的水平無渣出鋼系統(SF—HOT),類似於偏心爐底出鋼系統,但出鋼口採用水平布置,出鋼鋼流控制藉助於滑動水口進行控制;
(3)美國富奇(Fuch)公司開發的一種偏心爐底出鋼系統(OBT),類似於中心底出鋼法,但出鋼口偏離爐底中心線一定距離,出鋼口布置相當於在EBT電爐出鋼箱與爐底接觸處,但沒有出鋼箱。
套用效果
各種無渣出鋼技術在生產上的套用效果不盡相同,但其主要效果可概括為6個方面:(1)因爐渣留在爐內,加入鋼包中的合金元素的收得率高,Mn可達95%,Si可達90%,鋼包渣線部位耐材壽命提高5%;(2)精煉爐的精煉效果加強,鋼液成分均勻、穩定,雜質元素、氣體及非金屬夾雜物含量大大降低;(3)出鋼快、鋼流集中,出鋼時,鋼流垂直向下,鋼包接受鋼水時可用帶孔的鋼包蓋蓋住,使出鋼時熱損失減少,因此出鋼溫度也可以降低;(4)出鋼時電爐傾爐角減小,爐壁水冷麵積增加,耐火材料消耗降低。並且軟電纜的長度可以縮短;(5)因留鋼留渣操作,熔化期電弧穩定;並因提前形成熔池,縮短了冶煉時間;(6)因留渣操作,降低了渣料消耗和化渣能耗。