鋼液真空提升脫氣法是早期出現的鋼液真空處理技術之一。由聯邦德國Dortmund Horder公司1956年設計製造,取公司名稱的頭兩個字母命名為DH真空脫氣法,簡稱DH法。
基本介紹
- 中文名:鋼液真空提升脫氣法(DH法)
- 外文名:DHvacuum degassing
- 出現時間:1956年
- 發明人:Dortmund Horder公司
- 簡稱:DH法
- 設備:真空室、提升機構、加熱裝置等
設備構成
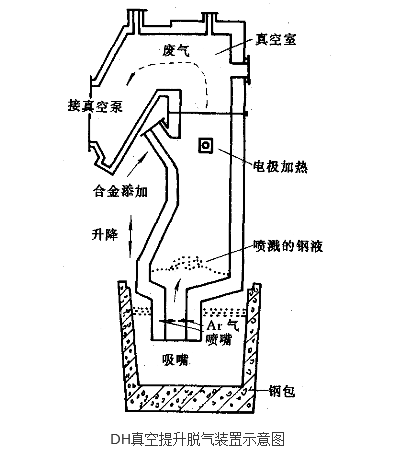
鋼液真空提升脫氣法是早期出現的鋼液真空處理技術之一。由聯邦德國Dortmund Horder公司1956年設計製造,取公司名稱的頭兩個字母命名為DH真空脫氣法,簡稱DH法。
鋼液真空提升脫氣法是早期出現的鋼液真空處理技術之一。由聯邦德國Dortmund Horder公司1956年設計製造,取公司名稱的頭兩個字母命名為DH真空脫氣法,簡稱DH法。設備構成真空提升脫氣設備主要由真空室、提升機構、...
已採用的鋼液真空處理技術有:鋼液真空脫氣、鋼液倒包真空處理,鋼液真空提升脫氣法(DH法)、鋼液真空循環脫氣法(RH法)以及真空鑄錠。冶金效果 (1)去除鋼中的氣體,減少鋼中的發紋、氫致裂紋和層狀斷裂缺陷等的出現率,從而提高鋼材...
鋼水真空處理的方法大致可以分為四類:液面脫氣法、滴流脫氣法、提升脫氣法和循環脫氣法。鋼液在真空中的脫氣反應為:脫氫:脫氮:脫氧:由上述反應式可見,鋼中的平衡氣體含量與熔池溫度和氣相中該氣體分壓有關。減壓是各類真空處理的...
真空提升脫氣法 真空提升脫氣法是1956年德國多特蒙特(Dortmund)和豪特爾(Horder)冶金聯合公司首先發明使用的,簡稱DH法。DH法的設備如圖5-3所示:由真空室(鋼殼內襯耐火材料)及提升機構,加熱裝置(電極加熱裝置或噴燃氣,噴油加熱),合金...
此方法是聯邦德國於1955年開發使用的,其裝置是一個帶有移動頂蓋的真空室,上置中間包;把澆鑄用的鋼包放在室內;頂蓋上有觀察孔和使鋼液注入室內的注鋼孔。技術簡介 倒包滴流脫氣法(Ladle dripping degassing)是一種鋼液真空處理技術。...
1956~1959年研究成功了鋼液真空提升脫氣法(DH)和鋼液真空循環脫氣法(RH)。1965年以來,真空電弧加熱脫氣(VAD)爐、真空吹氧脫碳爐(VOD)和氮氧(AOD)爐以及餵線法(WF)和LF鋼包爐、鋼包喻噴粉法(IP)等先後出現。到90年代已有幾十種...
5.1 真空冶金原理 5.1.1 真空冶金的一般規律——壓力對化學平衡的影響 5.1.2 真空下碳還原固體金屬氧化物能力的提高 5.1.3 鋼液的真空脫氧 5.1.4 鋼液的真空脫氣 5.2 鋼液滴流脫氣法 5.3 真空提升脫氣法(DH法)5.3.1...
此階段UHP爐套用+LF+RH法聯合使用,使鋼中氧含量降到(5~10)×10-6,這對於與連續澆注相匹配是必不可少的。此外,為進一步改善真空脫氣的效果,還開發和採用了霧化真空脫氣法、循環真空脫氣法(通稱DH法)生產真空脫氣軸承鋼。冶煉法...
20RH和DH的設備和工藝 20.1RH法(真空循環脫氣法)20.2DH法(真空提升法)20.3RH和DH的精煉效果 參考文獻 21鋼桶吹氬及CAB、CAS-OB的設備和工藝 21.1鋼桶吹氬 21.2用氮氣處理鋼液 21.3大氣下吹氬的發展 21.4帶蓋鋼桶吹氬...