《石化過程中基於定性SDG的故障混合診斷方法》是中國石油化工股份有限公司和中國石油化工股份有限公司青島安全工程研究院於2010年9月26日申請的專利,該專利的申請號為2010102919347,公布號為CN102004486A,授權公布日為2011年4月6日,發明人是牟善軍、張衛華、姜春明、王春利、李傳坤、姜巍巍。
《石化過程中基於定性SDG的故障混合診斷方法》提取工藝流程的關鍵節點在故障狀態下的特徵數據,存入專家知識庫;結合PCA、模糊邏輯和主元分析,得到基於SDG的故障診斷的混合算法,對於建立的SDG模型,自動推理進行HAZOP,把分析結果以故障症兆、故障原因、傳播路徑和不利後果以及處理措施以專家知識的形式存在故障知識庫中。混合專家知識系統主要由專家系統和HAZOP分析結果構成。解決故障診斷技術在故障檢測與診斷的速度、診斷完備性與準確性、診斷解析度以及魯棒性等方面的問題。
2016年12月7日,《石化過程中基於定性SDG的故障混合診斷方法》獲得第十八屆中國專利優秀獎。
(概述圖為《石化過程中基於定性SDG的故障混合診斷方法》摘要附圖)
基本介紹
- 中文名:石化過程中基於定性SDG的故障混合診斷方法
- 公布號:CN102004486A
- 授權日:2011年4月6日
- 申請號:2010102919347
- 申請日:2010年9月26日
- 申請人:中國石油化工股份有限公司、中國石油化工股份有限公司青島安全工程研究院
- 地址:北京市朝陽區朝陽門大街22號
- 發明人:牟善軍、張衛華、姜春明、王春利、李傳坤、姜巍巍
- Int.Cl.:G05B23/00(2006.01)I
- 代理機構:北京中偉智信專利商標代理事務所
- 代理人:張岱
- 類別:發明專利
專利背景,發明內容,專利目的,改善效果,附圖說明,技術領域,權利要求,實施方式,榮譽表彰,
專利背景
石油化工生產過程由於感測器漂移、設備失效、工藝波動或操作錯誤等原因,導致生產運行中經常出現異常工況狀態,輕則影響產品質量、生產調度計畫,重則會出現生產事故,造成人員傷亡和巨大的經濟損失。
如何從海量的生產數據中挖掘出有效的信息,及時識別出存在的異常工況,找出導致異常工況產生的原因,預測該異常工況發展下去可能產生的後果,提出相應的措施,進行有效的異常工況管理,避免產生嚴重後果,是確保企業安全運行的重要環節。
上述過程的核心技術是對過程的故障診斷。2010年9月前可以用於工業系統故障識別和診斷的方法主要分為兩大類,一類是基於模型的方法,另一類是基於歷史數據的方法。基於模型的故障診斷方法又可分為定量模型法和定性模型法。
定量模型法需要準確測試過程的動態特性,由於很難獲取過程對象的精確定量動態模型,此方法實用性受到限制,而基於定性數學模型的故障診斷方法得到重視和發展。基於定性數學模型的故障識別和診斷方法中,圖論方法是最有實用價值的一種,其中符號定向圖(SDG,Signed Directed Graph)方法前景十分看好。
基於歷史數據的故障診斷方法必須依據對過程系統已知的先驗知識,此類方法不能離開歷史數據,對新出現的故障沒有識別能力。基於歷史數據的故障診斷方法又可分為定量方法和定性方法。定性方法中套用最廣的是基於規則的專家系統,又稱為淺層知識專家系統。
基於歷史數據的故障診斷定量方法又分統計學方法和非統計學方法兩大類。兩類方法都是對實時數據的抽樣進行特徵提取的方法。統計學方法包括主元分析法(PCA)、部分最小二乘法(PLS)等。基於歷史數據的故障診斷定量方法的非統計學方法即常用的神經網路法。
截至2010年9月,基於半定量的方法得到重視和發展。所謂半定量是結合隨機理論、模糊集理論、加權方法等,在定性故障診斷方法中加入定量信息,使定量方法和定性方法優勢互補,例如模糊SDG方法、SDG-PCA方法、SDG-PLS方法等。
對比上述的故障診斷方法,由於定量模型法基於精確數學模型,所以具有比較好的早期感知能力和解析度,但是它對噪音和虛假信號的魯棒性很差,而且複雜系統的精確模型很難得到,當工藝流程改變時,適應能力也很差。統計分類法和神經網路法易於使用,對噪音的魯棒性也較好,然而對於新故障或未知故障的診斷無能為力。以美國和日本相關研究表明能在石化過程中真正實用的方法大概也莫過於基於規則的專家系統、PCA方法和SDG方法。
由於故障識別與診斷面對的是多變的、複雜的過程系統,2010年9月前,尚沒有一種方法能普遍適用於各種工業的多種故障診斷的需要。因此將數種實用的方法並行或者相互融合取長補短是可行的發展方向。針對石化過程的特點,《石化過程中基於定性SDG的故障混合診斷方法》以複雜系統的數據處理和故障診斷為研究目標,提出了適合石化工業的故障監測與診斷的關鍵算法。
發明內容
專利目的
《石化過程中基於定性SDG的故障混合診斷方法》提供一種石化過程中基於定性SDG的故障混合診斷方法,通過提出一套基於定性SDG的、融合多種定量故障診斷技術的實用故障診斷方法,解決故障診斷技術在故障檢測與診斷的速度、診斷完備性與準確性、診斷解析度以及魯棒性等方面的問題;結合SDG-HAZOP技術,對所採用的模型與算法進行靜態和動態檢驗,確保故障診斷模型與算法的準確性與完備性,並將HAZOP分析結果作為專家知識庫,用於線上故障診斷。
《石化過程中基於定性SDG的故障混合診斷方法》所述故障混合診斷方法建立了一個三層的層次診斷模型:
1)第一層是專家系統模組
將所述專家系統模組與生產過程中的實際流程相連線,採集來自生產現場的實時數據,提取工藝流程的關鍵節點在故障狀態下的特徵數據,存入專家知識庫。實時監測時,如果這些節點的狀態剛好落進知識庫定義好的狀態,那就得到結論:2010年9月前已進入某種故障狀態,原因和後果即可確定。這樣異常工況管理系統可直接得到被監測工藝的非正常工況結論。此時軟體系統不用進入後邊的推理算法,大幅減少了系統的推理時間。
2)第二層是綜合診斷模組
利用SDG方法進行故障診斷,診斷結果完備性高,但是由於定性推理的多義性導致解析度較低。結合PCA、模糊邏輯和主元分析,得到基於SDG的故障診斷的混合算法,進入混合算法後,首先以PCA方法對實時數據進行監測,當監測到過程發生異常波動時,則利用各種方法求得偏離點以供SDG進行推理:1)利用PCA對實時數據計算,得到各點的殘差方法以求得偏離點;2)實時數據根據SDG模型的動態閾值,求得達到一定偏離的點。隨後,運用SDG算法進行故障推理,得到相容通路,即故障傳播路徑,先後送入採用模糊邏輯的SDG推理引擎進行故障診斷,根據各傳播路徑的相容度和靈敏度信息進行排序,結合混和專家知識庫系統,得到故障的原因、後果以及處理措施等;
對於建立的SDG模型,自動推理進行HAZOP,採用關鍵變數“拉偏”,搜尋故障傳播路徑,把分析結果以故障症兆、故障原因、傳播路徑和不利後果以及處理措施以專家知識的形式存在故障知識庫中。在實際情形中,以SDG故障診斷的結果中故障路徑做為關鍵字去知識庫中搜尋處理方案,可以大大節省運算時間,提高運算速度。
這樣,以SDG方法為基礎,融合多種診斷方法,相互配合補充,發揮各自的優點,形成了基於SDG的故障診斷混合算法,提高了診斷效率。
3)第三層是混合專家知識系統
該混合專家知識系統主要由專家系統和HAZOP分析結果構成。
在第二層的綜合診斷模組中,採集到的現場數據首先送到PCA算法模組,用於診斷整個裝置或單元的工藝狀態是否正常,隨後先後送入SDG推理引擎進行故障診斷,此時的SDG節點和通路的閾值採用模糊邏輯算法,將SDG模型中的節點和支路狀態模糊化。
所述PCA算法模組,包括以下步驟:
a.以PCA方法對實時數據進行監測,採集實時數據,建立主元模型;
b.計算殘差;
c.建立PCA-SDG模型;
d.對於已經賦值的SDG模型進行雙向推理,得到故障傳播路徑。
基於模糊邏輯的SDG故障診斷的一般算法:
a.SDG節點的模糊包括閾值上下限的模糊,採集DCS上現場儀表的高高報、高報、低報、低低報數據,根據試驗得到SDG中各節點的閾值縮放因子,以所述數據為基礎,乘以閾值縮放因子,將報警限的範圍放大或縮小一定的倍數,從而得到適用於SDG推理的模糊閾值;
b.SDG節點的模糊還包括實時測量值對閾值的模糊,通過引入隸屬度表示,在某一時刻,獲得SDG模型中各節點的實際測量值,並計算得到其相對於模糊閾值的隸屬度;
c.將系統因果變數間的穩態增益定義為SDG支路的靈敏度,由人工設定。
d.從某一發生偏離的節點出發,進行前向推理和反向推理,找出所有相容通路,把每一條相容通路中各節點的隸屬度和各支路的靈敏度分別相乘,得出整條相容通路的相容度和靈敏度;
e.考慮相容通路的節點數目不同的影響,把每條相容通路的相容度根據節點數取幾何平均值,靈敏度根據支路數取幾何平均值;
f.綜合考慮相容通路的相容度和靈敏度大小,進行優先權排隊,並自動解釋造成當前報警的原因和危險傳播路徑;
g.每隔一個選定的時間間隔重複以上步驟a-f,以便實時跟蹤現場故障情況。
所述隸屬度的函式取值算法有如下兩種:
a.三角型隸屬函式
將閾值考慮為一條三角,在原上下限B和A的位置拓寬一段偏離,偏離的絕對值設為D,上限閾值的隸屬度函式μi(x)由式(1)表示,下限閾值的隸屬度函式μi(x)由式(2)表示,


b.二次分布型隸屬函式
將閾值考慮為一條曲線,則上限閾值的隸屬度函式μi(x)由式(3)表示,下限閾值的隸屬度函式μi(x)由式(4)表示,其中,B和A表示原上下限的位置,


將隸屬度值的絕對值作為節點相容程度。
SDG模型的支路狀態模糊通過支路的靈敏度實現,對於SDG模型中的每一個因果支路,其靈敏度定義為:

其中,ΔB——後果節點的相對偏離;ΔA——原因節點的相對偏離;採用SDG-HAZOP對SDG的模型與算法進行靜態和動態檢驗。
但由於實際生產的複雜性,將支路的靈敏度取“高”、“偏高”、“偏低”、“低”四種定性狀態,由人工設定,在計算模組內部分別對應“0.8”、“0.6”、“0.4”、“0.2”。這是因為,對於生產過程中兩個相互影響的變數,其影響程度是基本不變的。
所述混合專家系統包括以通用人工智慧軟體Clips為核心的專家系統以及以HAZOP分析結果為基礎的專家知識庫。
改善效果
《石化過程中基於定性SDG的故障混合診斷方法》利用了SDG完備性好的優勢,可以推理出故障源點和故障傳播路徑;發揮了PCA作為一種統計學方法的優勢,能夠高效的處理大量數據,並且對故障的監測反應靈敏;結合模糊邏輯的動態閾值、支路的靈敏度,對推理結果進行有效的定量化。由於採用SDG-HAZOP技術對所採用的模型與算法進行靜態和動態檢驗,模型的完備性和準確性都有很大提高。因此,基於定性SDG融合多種半定量的故障診斷技術能夠在故障檢測與診斷的速度、故障診斷的完備性與準確性、診斷的解析度以及魯棒性等問題上超越2010年9月前的單純使用一種故障診斷方法的技術。
附圖說明
附圖1為基於SDG的多種故障診斷方法融合的診斷層次模型的示意圖;
附圖2為SDG的模糊閾值的示意圖;
附圖3為一個簡單SDG模型;
附圖4為基於SDG的多種故障診斷方法融合的算法工作原理的示意圖。
技術領域
《石化過程中基於定性SDG的故障混合診斷方法》涉及石化過程中的故障診斷方法,特別涉及一種基於定性SDG的混合模糊邏輯和主元分析的故障診斷方法。
權利要求
1.一種石化過程中基於定性SDG的故障混合診斷方法,在中控室配置伺服器,所述伺服器與生產過程中的實際流程通過區域網路相連,採集來自生產現場的實時數據,並通過公共網路與客戶端相連線,該方法建立了一個三層的層次診斷模型:
1)第一層是專家系統模組
提取工藝流程的關鍵節點在故障狀態下的特徵數據,存入專家知識庫;實時監測時,如果關鍵節點的狀態在專家知識庫定義好的狀態中,則能夠得出結論:已經進入某種故障狀態,原因和後果即可確定;
2)第二層是綜合診斷模組
結合PCA、模糊邏輯和主元分析,得到基於SDG的故障診斷的混合算法,進入混合算法後,首先以PCA方法對實時數據進行監測,當監測到異常波動時,求出偏離點以供SDG進行故障推理;
隨後,運用SDG算法進行故障推理,得到相容通路,即故障傳播路徑,隨後先後送入採用模糊邏輯的SDG推理引擎進行故障診斷,結合混和專家知識庫系統,得到故障的原因、後果以及處理措施;對於建立的SDG模型,自動推理進行HAZOP,搜尋故障傳播路徑,把分析結果以故障症兆、故障原因、傳播路徑和不利後果以及處理措施以專家知識的形式存在故障知識庫中;
3)第三層是混合專家知識系統
該混合專家知識系統主要由專家系統和HAZOP分析結果構成。
2.如權利要求1所述的故障混合診斷方法,其特徵在於,採集到的現場數據首先送到PCA算法模組,用於診斷整個裝置或單元的工藝狀態是否正常,隨後先後送入SDG推理引擎進行故障診斷,此時的SDG節點和通路的閾值採用模糊邏輯算法,將SDG模型中的節點和支路狀態模糊化。
3.如權利要求2所述的故障混合診斷方法,其特徵在於,所述PCA算法模組,包括以下步驟:
a.以PCA方法對實時數據進行監測,採集實時數據,建立主元模型;
b.計算殘差;
c.建立PCA-SDG模型;
d.對於已經賦值的SDG模型進行雙向推理,得到故障傳播路徑。
4.如權利要求2所述的故障混合診斷方法,其特徵在於,
a.SDG節點的模糊包括閾值上下限的模糊,採集DCS上現場儀表的高高報、高報、低報、低低報數據,根據試驗得到SDG中各節點的閾值縮放因子,以所述數據為基礎,乘以閾值縮放因子,將報警限的範圍放大或縮小一定的倍數,從而得到適用於SDG推理的模糊閾值;
b.SDG節點的模糊還包括實時測量值對閾值的模糊,通過引入隸屬度表示,在某一時刻,獲得SDG模型中各節點的實際測量值,並計算得到其相對於模糊閾值的隸屬度;
c.將系統因果變數間的穩態增益定義為SDG支路的靈敏度,由人工設定;
d.從某一發生偏離的節點出發,進行前向推理和反向推理,找出所有相容通路,把每一條相容通路中各節點的隸屬度和各支路的靈敏度分別相乘,得出整條相容通路的相容度和靈敏度;
e.考慮相容通路的節點數目不同的影響,把每條相容通路的相容度根據節點數取幾何平均值,靈敏度根據支路數取幾何平均值;
f.綜合考慮相容通路的相容度和靈敏度大小,進行優先權排隊,並自動解釋造成當前報警的原因和危險傳播路徑;
g.每隔一個選定的時間間隔重複以上步驟a-f,以便實時跟蹤現場故障情況。
5.如權利要求4所述的故障混合診斷方法,其特徵在於,所述隸屬度的函式取值算法有如下兩種:
a.三角型隸屬函式
將閾值考慮為一條三角,在原上下限B和A的位置拓寬一段偏離,偏離的絕對值設為D,上限閾值的隸屬度函式μi(x)由式(1)表示,下限閾值的隸屬度函式μi(x)由式(2)表示,


b.二次分布型隸屬函式
將閾值考慮為一條曲線,則上限閾值的隸屬度函式μi(x)由式(3)表示,下限閾值的隸屬度函式μi(x)由式(4)表示,其中,B和A表示原上下限的位置,


將隸屬度值的絕對值作為節點相容程度。
6.如權利要求1-5任一所述的故障混合診斷方法,其特徵在於,採用SDG-HAZOP對SDG的模型與算法進行靜態和動態檢驗。
7.如權利要求1-5任一所述的故障混合診斷方法,其特徵在於,所述混合專家系統包括以通用人工智慧軟體Clips為核心的專家系統以及以HAZOP分析結果為基礎的專家知識庫。
實施方式
《石化過程中基於定性SDG的故障混合診斷方法》提出了一個建立快速、表達簡便的層次診斷模型,該層次模型由三層構成,如附圖1所示。
1)第一層是一個專家系統模組
提取工藝流程的關鍵節點(根據操縱經驗得出)在故障狀態下的徵兆,存入專家知識庫。實時監測時,如果這些節點的狀態剛好落進知識庫定義好的狀態,那就得到結論:2010年9月前已進入某種故障狀態,原因和後果即可確定。這樣異常工況管理系統可直接得到被監測工藝的非正常工況結論。此時軟體系統不用進入後邊的推理算法,大幅減少了系統的推理時間。
2)第二層是運用SDG、模糊邏輯、PCA等技術的綜合診斷模組:
利用SDG方法進行故障診斷,診斷結果完備性高,但是由於定性推理的多義性導致解析度較低。結合PCA、模糊邏輯等各方法的優缺點,得到基於SDG的故障診斷的混合算法。其實質是,實時數據進入混合算法後,首先以PCA方法對過程數據進行監測,當監測到過程發生異常波動時,則利用各種方法求得偏離點以供SDG進行推理:1)利用PCA對實時數據計算,得到各點的殘差方法以求得偏離點;2)實時數據根據SDG模型的動態閾值,求得達到一定偏離的點。
隨後運用SDG算法進行故障推理,得到相容通路,即故障傳播路徑。根據各傳播路徑的相容度和靈敏度信息進行排序,結合混和專家知識庫系統,得到故障的原因、後果以及處理措施等。
對於建立的SDG模型,對其進行計算機自動推理進行HAZOP,採用關鍵變數“拉偏”,搜尋故障傳播路徑,把分析結果以故障症兆、故障原因、傳播路徑和不利後果以及處理措施以專家知識的形式存在故障知識庫中。在實際情形中,以SDG故障診斷的結果中故障路徑做為關鍵字去知識庫中搜尋處理方案,可以大大節省運算時間,提高運算速度。
這樣,以SDG方法為基礎,融合多種診斷方法,相互配合補充,發揮各自的優點,形成了基於SDG的故障診斷混合算法,提高了診斷效率。
3)第三層是混合專家知識系統
該混合專家知識系統主要由專家系統和HAZOP分析結果構成。
以下是對融合的算法進一步的說明
一、基於SDG的多種故障診斷方法融合的算法
1.採用模糊邏輯的SDG算法
將模糊邏輯引入SDG模型,主要是利用模糊算法將SDG模型中的節點和支路狀態模糊化,以利用定量信息進行半定量的故障診斷。
1.1SDG節點的模糊
SDG節點的模糊包括閾值上下限的模糊和實時測量值的模糊。
1.1.1閾值上下限的模糊
在實際生產中,絕大多數變數都有一個操作範圍,在這個操作範圍內,變數都認為是正常的,故可對所有變數即節點定義一個正常帶。試驗表明,如果直接使用DCS的閾值做為SDG的閾值,對於某些故障,一些節點可能起到傳播故障的作用,但由於沒有達到DCS的報警閾值,故在SDG中不產生偏差,從而相容通路推理到這些節點時被打斷,造成了相容通路的不連續性。採用縮小的DCS閾值可以解決這個問題。該文提出利用“閾值縮放因子”來得到用於SDG推理的節點閾值。具體方法是以DCS上現場儀表的高高報、高報、低報、低低報數據為基礎,在他們的基礎上乘以一個閾值縮放因子,將報警限的範圍放大或縮小一定的倍數。該因子取經驗值,其大小可由試驗得到。
如附圖2所示:將DCS變數閾值區域縮小,形成SDG節點閾值。閾值被分為三個區域:上限帶,正常帶,下限帶。
1.1.2實時值對閾值的隸屬度
SDG節點實時值對閾值的模糊通過引入隸屬度的方法實現。當節點值落在正常帶時,隸屬度μi(x)值為0。超出正常帶,μi(x)為±1。某節點i的閾值隸屬度μi(x)的取值限制在閉區間(0,1)以內,其值的大小表示了節點變數i的當前值x對閾值界限的隸屬程度。只有當隸屬度μi(x)=1時,x達到閾值界限。當μi(x)=0時,x沒有達到閾值界限。例如當μi(x)=0.6時,x達到了閾值界限的60%。
該算法用到的閾值隸屬函式取值算法有如下兩種:
1)三角型隸屬函式
如果將閾值考慮為一條三角,在原上下限B和A的位置拓寬一段偏離,偏離的絕對值設為D。則上限閾值隸屬度函式μi(x)由式(1)描述,如下的三角式隸屬函式(a)所示。同理下限閾值的隸屬度函式μi(x)由式(2)描述,如下的三角式隸屬函式(b)所示。


三角式隸屬函式:
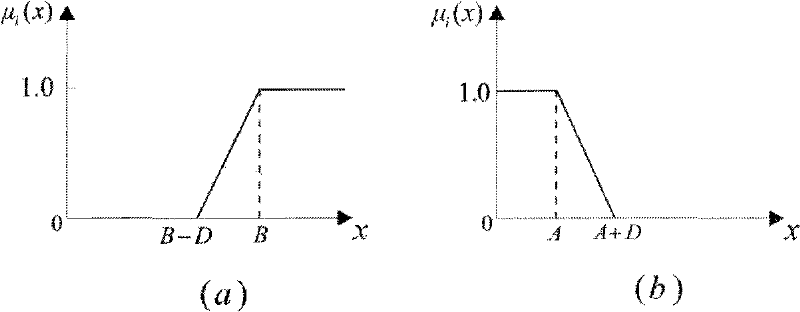
2)二次分布型隸屬函式
基於三角的隸屬函式將節點的偏離假定為線性的、單調的變化。在實際過程中常見的規律可能是非線性的,因此在有條件實測的前提下,應當考慮隸屬度函式的類型儘可能適應實際過程在不同量程範圍的變化規律。如果將閾值考慮為一條曲線,則上限閾值的隸屬度函式μi(x)由式(3)描述,如下的二次分散式隸屬函式(a)所示。同理下限閾值的隸屬度函式μi(x)由式(4)描述,如下的二次分散式隸屬函式(b)所示。


二次分散式隸屬函式

採用上述的基於三角的模糊隸屬度後,需將相容通路的判定規則稍作改變。引入節點相容程度的概念,即節點相容程度等於當前原因節點的隸屬度值的絕對值(0至1之間的某一值),當相容度等於1時為完全相容,當相容度等於0時為不相容。同時需要引入通路相容程度的概念,只要某一相容通路的各節點相容度都大於0,就作為相容通路的候選。
在推理得到的多條候選相容通路中通路相容度最大者為可信度最高。採用上述方法後,既能加寬閾值範圍,又能兼顧靈敏度的要求。
1.2SDG支路靈敏度的模糊
將系統因果變數間的穩態增益(支路靈敏度)定義為SDG的模糊集合。
即:對於SDG模型中的每一個因果支路
其靈敏度定義為:


式(5)中:ΔB——後果節點的相對偏離;ΔB=(後果變數實測值-後果正常工況值)/(後果變數上限-後果變數下限);ΔA——原因節點的相對偏離;ΔA=(原因變數實測值-原因正常工況值)/(原因變數上限-原因變數下限)。
對於附圖3所示的一個簡單SDG模型,在某一時刻,由於B的增大,導致C的增大,此時A也增大,但變化很小,且A對C的影響很小。如果採用式(5)計算μ,則計算μCA時會出現較大誤差,因為A對C的影響很小。此時可將支路的靈敏度取“高”、“偏高”、“偏低”、“低”四種定性狀態,由人工設定,在計算模組內部分別對應“0.8”、“0.6”、“0.4”、“0.2”。這是因為,對於生產過程中兩個相互影響的變數,其影響程度是基本不變的。
綜上所述,可以得到基於模糊邏輯的SDG故障診斷的一般算法:
(1)以DCS中各變數的報警限為基礎,根據試驗得到SDG中各節點的閾值縮放因子,從而得到適用於SDG推理的模糊閾值;
(2)在某一時刻,獲得SDG模型中各節點的實際測量值,並計算得到其相對於模糊閾值的隸屬度;
(3)從某一發生偏離的節點出發,進行前向推理和反向推理,找出所有相容通路,把每一條相容通路中各節點的隸屬度和各支路的靈敏度分別相乘,得出整條相容通路的相容度和靈敏度;
(4)考慮相容通路的節點數目不同的影響,把每條相容通路的相容度根據節點數取幾何平均值,靈敏度根據支路數取幾何平均值。
(5)綜合考慮相容通路的相容度和靈敏度大小,進行優先權排隊,並自動解釋造成當前報警的原因和危險傳播路徑;
(6)每隔一個選定的時間間隔重複以上步驟,以便實時跟蹤現場故障情況。
由上述模糊邏輯與SDG的結合算法可知,在SDG中引入模糊邏輯,使閾值由固定值變為一個區間,可以有效解決閾值多變的問題。同時,在SDG的節點上引入相容度,在SDG的支路中引入靈敏度,為傳統的定性SDG增加了定量的信息。這樣,既利用了傳統SDG完備性好的優點,又可以通過定量的方式剔除部分虛假信息,從而大大提高了基於SDG模型進行故障診斷的解析度。
如果單純採用模糊邏輯和SDG結合,由於每個時刻都要計算節點和支路增益的變化率,計算量大大增加,雖然提高了解析度,卻影響了故障診斷的速度。引入主元分析方法,可有效緩解這個問題。
2.主元分析與SDG相結合的故障診斷方法
主元分析方法(Principle Component Analysis,PCA),作為一種基於信號處理的數據驅動方法,已廣泛套用於工業過程故障診斷中。但由於方法本身的局限性,PCA方法不能夠準確的指出故障源,因此PCA與SDG方法的結合,有著重要的意義。
利用PCA殘差與SDG結合進行故障診斷主要分為如下幾步:
1)採集數據,建立主元模型。
2)計算殘差。利用建立好的主元模型,計算測量值xnew的得分矩陣:tnew=xnewP。預測值:
。殘差:
。


3)建立PCA-SDG模型。依據上一步得到的殘差,設定殘差閾值,並建立PCA-SDG模型。當發現殘差超過殘差閾值時,表明生產過程產生異常,殘差超過其閾值且為正的變數,在對應的SDG節點上記為“+”;超過閾值且為負的變數,在對應的SDG節點上記為“-”;否則記為“0”。這樣PCA-SDG模型就建立起來了。
4)對於已賦值的SDG模型進行雙向推理,得到故障傳播路徑。
PCA-SDG方法中,殘差閾值的確定是很重要的。因為在用SDG進行故障診斷之前,對於每個測量變數都需要確定高、低閾值。閾值上、下限範圍過寬,節點變數在閾值上、下限以內其狀態可看作為正常狀態,推理“引擎”無法搜尋出故障傳播的路徑,會導致故障診斷的靈敏度和預測性差。反之,閾值上、下限範圍過窄,會導致靈敏度過高或預報警過早,而實際過程還處於安全範圍,即故障沒有發生。閾值的設定在PCA-SDG故障診斷方法中是一個關鍵,在處理這個問題時,有人提出將高閾值在
和
之間,低閾值設在
和
之間(其中,Qα有固定的計算公式),也可以根據經驗設定閾值。通常情況下,殘差閾值可由經驗來確定。




3.基於SDG的融合故障診斷
前面介紹了SDG和模糊邏輯結合,解決了節點的閾值固定的問題,實現了閾值的動態化,提高了解析度;SDG和主元分析結合,可以快速提高推理速度。但是如果僅僅兩兩結合,仍然不能根本同時解決動態閾值問題和快速推理問題。
如附圖3所示,為故障診斷算法工作原理,採集到的現場數據首先送到PCA算法模組,用於診斷整個裝置或單元的工藝狀態是否正常,如果T值大於設定的閾值,則確定工藝狀態異常,找出主要參數的貢獻率,按照貢獻率的大小,做為優先權,先後送入SDG推理引擎進行故障診斷。此時的SDG的節點和通路的閾值採用模糊邏輯算法。三種方法結合,既解決了由於節點數目增多,推理速度慢的現象,又同時解決了解析度的問題。
這種以SDG方法為基礎,融合多種診斷方法,相互配合補充,發揮各自的優點,形成了基於SDG的故障診斷融合算法,提高了診斷效率。
二、SDG模型檢驗
1.SDG故障診斷模型非正式檢驗
SDG故障診斷模型非正式檢驗主要涉及工藝原理審查和基於經驗的審查與模型簡化三方面的內容。
工藝原理審查和基於經驗的審查人員可以由另外的熟悉SDG建模的人員擔當,有利於克服模型開發者的思維慣性所導致的“盲點”,當然最好在模型開發者的配合下完成檢驗。檢驗時應當參考被建模過程的帶控制點的工藝流程圖、相關的工藝、設備和自控設計資料、所有相關生產數據、歷史記錄曲線、工藝操作說明等。檢驗人員應當從工藝基本原理(動量傳遞原理、物料傳遞原理、熱量傳遞原理、反應動力學原理)出發,對SDG模型的因果影響關係逐一檢查。這一過程相當於重複建模過程,並對建模過程的每一步結論進行原理性審查。
採用SDG技術進行故障診斷最常見的問題是診斷的解析度低,即診斷結果給出過多的次要結論或無效結論。導致SDG故障診斷解析度低的問題比較複雜,涉及多種因素,例如SDG模型中包括較多不可觀測節點、推理方法不當、SDG模型結構不合理、閾值設定範圍不正確、故障徵兆含糊等。其中SDG模型結構不合理所導致的故障診斷解析度低的問題可以通過基於經驗的SDG模型簡化方法得到一定程度的緩解。SDG模型簡化原則如下。
以下原則不一定解決所有問題,但加以考慮會提高SDG建模質量。
1)可觀測變數節點的合併與簡化原則
該節點與干擾源及故障傳播關係不大者可取消。
2)不可觀測變數節點的合併與簡化原則
(1)不可觀測變數節點的狀態未知,在故障診斷套用中應儘量取消。
(2)潛在的根節點,例如故障源,雖然不可觀測,如果取消可能改變正確SDG的結構,則不能隨意取消。
(3)對於中間不可觀測變數節點,當有多條支路通過時須慎重。例如,取消該節點會引出實際中不可能的偽相容通路或消掉了不該取消的危險傳播路徑。
3)兩節點間存在多支路的合併與簡化原則
找出占支配地位的支路,消去非支配地位的支路。
(1)用於故障診斷時,可根據現場數據或經驗判定支配地位的支路。
(2)如果負反饋支路屬於非控制反饋變數(例如自衡現象),且不足以補償或抵消干擾的傳播時,該支路可取消。
(3)如果可以得到相關數據,滿足半定量分析的條件,利用SDG分析找出占支配地位的支路,消去非支配地位的支路。
(5)合理修改SDG結構,減少該節點相關支路。
4)故障因素的引入按故障發生的機制和歷史事故經驗添加節點和支路。
5)非單調影響的單調化;非線性關係的分段線性化;如果非線性規律是單調變化,可以看成線性單調變化。
6)條件支路
故障診斷時,可以閉合自動控制反饋支路。
7)不考慮某種故障或危險時,取消與該變數的相關節點或支路。
2.SDG故障診斷模型靜態檢查
SDG故障診斷模型靜態檢查的主要目的是檢驗SDG模型結構是否合理。SDG模型結構合理性的內容包括:節點選定是否合理;因果關係描述是否合理;通過影響方程的數學推演判斷SDG模型結構的合理性;經SDG推理得到相關危險傳播的路徑後,從推理結果分析SDG模型能否達到設計意圖等。
1)因果關係對檢查
通過逐一檢驗SDG模型中的因果關係對,判斷所有表達的因果關係是否符合實際。當無法離線判斷時,可以採用仿真計算試驗,有條件時還可以線上試驗,但必須確保不干擾正常生產。檢查過程中最好進行非線性特性試驗,探明因果關係中是存在非線性影響,是何種非線性影響關係。
2)影響方程合理性檢查
SDG模型可以直接映射為影響方程,代數方程組或微分方程也可以轉化為定性影響方程,因此可以運用相關的數學方法檢查影響方程、代數方程或微分方程的結構合理性,從而推論SDG模型結構的合理性。例如定量微分方程可以通過求偏導轉化為定性影響方程,逐一檢查偏導的正確性,可以保證影響方程的正確性。
3)基於SDG-HAZOP的SDG故障診斷模型檢驗
採用SDG-HAZOP平台可以對SDG模型的靜態特性進行以下幾種檢驗:
(1)操作點可達性檢驗
該步驟中,由計算機採用逆向推理在SDG模型中自動推理檢驗操作點的偏離。該步驟的目的在於檢驗SDG模型對誤操作的識別能力。
(2)不利後果(故障)可達性檢驗
該步驟中,由計算機採用正向推理在SDG模型中自動推理檢驗後果是否發生。該步驟的目的在於檢驗SDG模型對故障後果的識別能力。
(3)節點的劇情關聯特性檢驗
確切的定義應當是中間過程變數節點的危險劇情關聯特性檢驗,即檢驗各中間過程變數節點可能有多少危險劇情通過。該步驟的目的在於選擇最佳SDG故障診斷的推理起始點。
(4)可觀測節點最佳化配置檢驗
凡是具有強危險劇情關聯的中間節點應當設定為可觀測節點。採用SDG方法進行故障診斷,只有首先解決可觀測節點的最佳化配置問題,才有可能從根本上保證SDG故障診斷的完備性和準確性。
在上述的SDG模型靜態特性檢驗步驟中,操作點可達性檢驗和不利後果(故障)可達性檢驗最為重要。
三、混合專家系統
混合專家系統主要由兩部分構成,一是以通用人工智慧軟體Clips為核心的專家系統,一是以HAZOP分析結果為基礎的專家知識庫。二者相輔相成,作為混合專家系統,對推理結果給出合理的解釋。
榮譽表彰
2016年12月7日,《石化過程中基於定性SDG的故障混合診斷方法》獲得第十八屆中國專利優秀獎。