《用於水泥基材料的複合型高性能膨脹劑》是中冶武漢冶金建築研究院有限公司於2010年11月9日申請的專利,該專利的公布號為CN102464463A,授權公布日為2012年5月23日,發明人是曾明、周紫晨、張建武、陳晶、張冰、李君。
《用於水泥基材料的複合型高性能膨脹劑》公開了一種用於水泥基材料的複合型高性能膨脹劑,屬於水泥基材料外加劑技術領域。選用脂膜石灰、天然硬石膏、石灰石、偶氮類化合物等多種材料作為膨脹組分。將脂膜石灰、天然硬石膏及石灰石按一定比例於磨機內粉磨至一定細度,繼而加入一定比例的偶氮化合物和分散劑混合均勻後即得到該發明的高性能複合型膨脹劑。該膨脹劑可以使得水泥基材料在塑性及硬化階段皆產生適宜膨脹;大幅提高所配製漿體的分散性和流動性能;提高材料的抗折及抗壓強度;同時,低鹼微氯,可提高水泥混凝土結構物的耐久性。
2020年7月14日,《用於水泥基材料的複合型高性能膨脹劑》獲得第二十一屆中國專利獎優秀獎。
基本介紹
- 中文名:用於水泥基材料的複合型高性能膨脹劑
- 申請人:中冶武漢冶金建築研究院有限公司
- 申請日:2010年11月9日
- 申請號:2010105361366
- 公布號:CN102464463A
- 公布日:2012年5月23日
- 發明人:曾明、周紫晨、張建武、陳晶、張冰、李君
- 地址:湖北省武漢市青山區和平大道1256號
- Int. Cl.:C04B24/12(2006.01)I
- 代理機構:武漢楚天專利事務所
- 代理人:石堅
- 類別:發明專利
專利背景,發明內容,專利目的,技術方案,改善效果,技術領域,權利要求,實施方式,操作內容,實施案例,榮譽表彰,
專利背景
水泥基材料在澆築硬化過程中,由於化學減縮、冷縮和乾縮等原因會引起體積收縮,嚴重者甚至導致材料的開裂。混凝土膨脹劑是一種與水泥、水拌合後經水化反應,能使水泥基材料產生一定體積膨脹的外加劑,用以補償水泥混凝土的收縮。對於一些特殊工程特別是對於後張預應力孔道灌漿等一些特殊部位,灌漿材料中必須使用膨脹劑,確保材料充滿預埋孔道和預應力筋之間的空隙以保護鋼筋不外露鏽蝕及保證預應力筋和混凝土構件之間有效的應力傳遞。
通常,在預應力孔道灌漿材料中是添加0.5/萬-1/萬的鋁粉做為膨脹劑,利用鋁粉反應產生氫氣的原理使水泥漿體產生塑性階段的膨脹。但研究表明:鋁粉膨脹劑引入的氫氣分子會使鋼筋產生“氫脆”,導致鋼筋內部形成微小的裂紋,對混凝土結構的耐久性產生危害,2010年前已被禁止使用於混凝土結構中。而其它常用的硫鋁酸鈣類膨脹劑、氧化鈣類膨脹劑、硫鋁酸鈣--氧化鈣類膨脹劑等,在摻加到水泥或混凝土中一般都在24小時-14天齡期內產生一定量的膨脹,而不能避免混凝土(或水泥漿體)在塑性階段(4小時內)的塑性沉降收縮,不能滿足預應力孔道灌漿的要求。2010年前,預應力孔道灌漿施工中,常出現質量問題:孔道中水泥漿未充滿,有空隙;水泥漿體硬化後收縮與孔道壁分離等。
2010年前膨脹劑產品一般採用天然礦物原料經過高溫處理製成,成本高,能耗大,不符合我國倡導的“低碳經濟”的理念;同時膨脹劑鹼含量較高,摻加量大,含氯,生產工藝相對複雜。此外,多數膨脹劑大都用量偏高,內摻量一般≥10%,存在對化學外加劑適應性較差而導致混凝土坍落度損失較快、較大的缺陷,不能很好地適應現代混凝土施工技術的要求。特別是針對預應力孔道灌漿、設備基座二次灌漿等一些特殊部位,要求灌漿料漿體在塑性階段產生微量的塑性膨脹,要求3小時自由膨脹率≥0.2%,這是2010年前技術中普通膨脹劑所不能達到的。
發明內容
專利目的
《用於水泥基材料的複合型高性能膨脹劑》提供一種用於水泥基材料的複合型高性能膨脹劑,該膨脹劑可使水泥基材料在塑性及硬化階段皆產生適宜的膨脹;大幅提高所配製漿體的分散性和流動性能;提高材料的抗折及抗壓強度。同時,低鹼微氯,一定程度上提高了水泥混凝土結構的耐久性。
技術方案
《用於水泥基材料的複合型高性能膨脹劑》的技術方案是:用於水泥基材料的複合型高性能膨脹劑由以下組份及重量百分數組成:
脂膜石灰10%~50%,SO3含量≥45%的無水硬石膏30%~70%,CaO含量≥35%的石灰石5%~45%,偶氮化合物0.1%~1%,分散劑0.1%~1%;
將上述前三種組份按重量百分數比例配合後放進球磨機內球磨,至比表面積達到300平方米/千克~600平方米/千克;再將磨細的上述三種組份的混合料、偶氮化合物和分散劑按比例加入混料機內,混合15分鐘~25分鐘,混勻後的細粉料即為用於水泥基材料的複合型高性能膨脹劑。
所述的脂膜石灰按以下方法製備:選用f-CaO含量≥50%的生石灰,在其中加入占生石灰總重量4‰~8‰的硬脂酸或硬脂酸鹽,置於磨機內粉磨至比表面積≥300平方米/千克、且0.08毫米方孔篩餘量小於10%時所得的粉料即為脂膜石灰粉。
所述的偶氮化合物是偶氮二甲醯胺,偶氮二異丁腈,偶氮二異庚腈之中的一種或多種的混合,所述偶氮化合物的顆粒平均粒徑為≤10微米,發氣量≥200毫升/克。
所述分散劑是三聚磷酸鈉、或六偏磷酸鈉,或葡萄糖酸鈉之中的一種或多種的混合。
所述膨脹劑用於水泥基材料時,膨脹劑的比例占水泥基材料總質量的8~10%。
改善效果
《用於水泥基材料的複合型高性能膨脹劑》的優點:該發明膨脹劑摻量低,以膠凝材料的質量計,添加比例僅為8%~10%,不僅節省了工程成本,而且其優異的膨脹性能,能有效地聯合補償水泥基材料早期收縮和後期收縮,有效地預防裂縫產生。膨脹組分中石灰顆粒表面的脂膜,有效地控制了石灰的水化速度,使膨脹能得到緩慢釋放;與此同時,由於石灰表面包裹的脂的作用,延長了產品的存放時間;用該膨脹劑配製成的漿體流動性大幅提高,製成的灌漿材料能良好地密實填充結構體內部,且保持優異的流動性能;該膨脹劑鹼含量低,可以預防混凝土潛在的鹼集料反應帶來的危害。
技術領域
《用於水泥基材料的複合型高性能膨脹劑》屬於水泥基材料外加劑技術領域,具體涉及一種用於水泥基材料的高性能複合型膨脹劑。
權利要求
1.一種用於水泥基材料的複合型高性能膨脹劑,其特徵在於:所述的膨脹劑由以下組份及重量百分數組成:
脂膜石灰10%~50%,SO3含量≥45%的無水硬石膏30%~70%,CaO含量≥35%的石灰石5%~45%,偶氮化合物0.1%~1%,分散劑0.1%~1%;
將上述前三種組份按重量百分數比例配合後放進球磨機內球磨,至比表面積達到300平方米/千克~600平方米/千克;再將磨細的上述三種組份的混合料、偶氮化合物和分散劑按比例加入混料機內,混合15分鐘~25分鐘,混勻後的細粉料即為用於水泥基材料的複合型高性能膨脹劑。
2.根據權利要求1所述的用於水泥基材料的複合型高性能膨脹劑,其特徵在於所述的脂膜石灰按以下方法製備:選用f-CaO含量≥50%的生石灰,在其中加入占生石灰總重量4‰~8‰的硬脂酸或硬脂酸鹽,置於磨機內粉磨至比表面積≥300平方米/千克、且0.08毫米方孔篩篩餘量小於10%時所得的粉料即為脂膜石灰粉。
3.根據權利要求1所述的用於水泥基材料的複合型高性能膨脹劑,其特徵在於所述的偶氮化合物是偶氮二甲醯胺,偶氮二異丁腈,偶氮二異庚腈之中的一種或多種的混合,所述偶氮化合物的顆粒平均粒徑為≤10微米,發氣量≥200毫升/克。
4.根據權利要求1所述的用於水泥基材料的複合型高性能膨脹劑,其特徵在於:所述分散劑是三聚磷酸鈉、或六偏磷酸鈉,或葡萄糖酸鈉之中的一種或多種的混合。
5.根據權利要求1~4中任一權利要求所述的用於水泥基材料的複合型高性能膨脹劑,其特徵在於:所述膨脹劑用於水泥基材料時,膨脹劑的比例占水泥基材料總質量的8~10%。
實施方式
操作內容
為解決上述技術問題,《用於水泥基材料的複合型高性能膨脹劑》是這樣來實現的:選用脂膜石灰、無水硬石膏、偶氮類化合物等多種材料作為複合膨脹組分。將脂膜石灰、無水硬石膏及石灰石按比例混合於球磨機內球磨使其達到規定的細度,繼而加入一定比例的偶氮化合物和分散劑,再在混料機內混合均勻後,即得到該發明的複合型高性能膨脹劑。
《用於水泥基材料的複合型高性能膨脹劑》複合膨脹劑的膨脹機理是:
《用於水泥基材料的複合型高性能膨脹劑》的複合膨脹劑內的膨脹組份都為反應性膨脹劑,其中偶氮類化合物,如偶氮二甲醯胺常用作塑膠、橡膠的發泡劑,分解溫度約205℃,室溫下穩定。複合膨脹劑按一定比例摻入到水泥混凝土中加水攪拌後,其中的部分水泥開始水化,部分石灰遇水消化,產生的水化產物對偶氮類化合物有活化作用,大大降低了其分解溫度,使偶氮類化合物分解為無害的氮氣、二氧化碳及少量的一氧化碳,這一反應在物料加水後即開始,約2-3小時後停止,產生的適量氣體促使水泥混凝土拌合物在塑性階段產生一定的體積增長,可補償拌合物塑性階段的沉降收縮。與傳統鋁粉型膨脹劑相比,不會使鋼筋產生“氫脆”,有利於混凝土結構的耐久性。塑性膨脹量的大小可通過偶氮化合物的摻加量控制,當用量少於0.1%時膨脹量過小作用不明顯;而當摻加量過大時,過多的氣體會導致拌合物酥鬆,導致結構體的破壞。
《用於水泥基材料的複合型高性能膨脹劑》的複合膨脹劑中摻入了一定量的脂膜石灰,由生石灰及硬脂酸或硬脂酸鹽按一定比例配合後,經粉磨而成,這是一種2010年前技術常用的膨脹劑。通常,生石灰遇水即消解生成氫氧化鈣,其反應式為:CaO+H2O→Ca(OH)2。此反應非常迅速,隨著反應的進行,物質體積可增大150~190%,同時放出大量的熱。但是,膨脹劑加入到水泥混凝土中有一個加水攪拌和澆築的過程,需要一定的時間,為了短暫延緩生石灰水化的速度,控制其膨脹產生在某一時段。所以在粉磨生石灰的同時,摻入一定數量的硬脂酸(或硬脂酸鹽)共同混磨,使生石灰細小顆粒的表面包裹一層蠟狀的硬脂酸膜,阻止水與石灰顆粒的直接接觸。脂膜石灰組分遇水後,石灰顆粒表面裹的硬脂酸(或硬脂酸鹽)在攪拌作用下將緩慢溶解,基本溶解完後石灰顆粒與水接觸,開始消化反應。該反應在遇水後即進行,最大膨脹值出現在2-4天內,並與環境溫度有一定關係,溫度高低會影響其最大膨脹值出現的時間。這一膨脹屬早中期膨脹,部分膨脹是在水泥石結晶結構網已形成後發生的,因此,石灰摻量應嚴格控制,當摻量過大時膨脹量過大易導致結構酥鬆破壞。
《用於水泥基材料的複合型高性能膨脹劑》的複合膨脹劑中的硬石膏採用天然硬石膏或工業硬石膏,屬於II型硬石膏,在水中的溶解度非常小,水化反應能力也非常緩慢。但由於複合膨脹劑中的石灰及水泥水化提供的鹼性環境,激發了硬石膏的反應能力,加快了硬石膏的溶解速度,當液相中的SO3濃度達到一定值時,溶出生成二水石膏,其水化反應式為:CaSO4+2H2O→CaSO4·2H2O,;另有部分SO3與水泥中的礦物成分鋁酸三鈣(C3A)反應,反應產物為鈣礬石,伴隨這兩個反應都產生一定的體積膨脹,其反應過程較長,可持續到20天以上。
經申請人用電鏡等儀器觀察證實,《用於水泥基材料的複合型高性能膨脹劑》的複合膨脹劑中的石灰石粉顆粒呈圓球形且表面光滑,在結構中能夠起到相對物理增水和滾珠軸承的作用,且石灰石中的碳酸鈣能夠和水泥熟料中的鋁酸鹽礦物產生水化反應,形成膨脹性的水化碳鋁酸鈣補償收縮。
《用於水泥基材料的複合型高性能膨脹劑》的複合膨脹劑中,脂膜石灰、硬石膏、偶氮化合物等三種材料的性能互補,其中石灰維持液相中鈣離子的飽和濃度,並為偶氮化合物、硬石膏的反應提供足夠的鹼性環境,降低鈣礬石的形成速度,對鈣礬石的形成和膨脹特性具有重要的影響。
《用於水泥基材料的複合型高性能膨脹劑》的複合膨脹劑中摻入分散劑(三聚磷酸鈉、或六偏磷酸鈉,或葡萄糖酸鈉之中的一種或多種的混合),主要作用在於分散劑能夠與鈣、鎂等金屬離子生成水溶性絡合物,延緩了水泥的水化,同時也在一定程度上延遲了膨脹劑膨脹性能的發揮,有效提高漿體的流動性並保證漿體流動性在一段時間內不損失,特別適合在高溫下的施工。
選擇將成分符合要求的石灰(f-CaO含量≥50%),加入4‰~8‰的硬脂酸(或硬脂酸鹽)於球磨機內球磨至0.08毫米方孔篩餘量小於10%時出料。再與符合要求的硬石膏粉(SO3含量≥45%,0.08方孔篩餘量小於10%)、石灰石粉(CaO含量≥35%,0.08方孔篩餘量小於10%)按一定比例一起於球磨機內混合磨細,比表面積達到300平方米/千克~600平方米/千克即可,再加入一定比例的偶氮化合物和分散劑混合均勻後即可得到複合型高性能膨脹劑。
實施案例
實施例1
以100千克複合型高性能膨脹劑為例,其配方是:
稱取脂膜石灰粉35千克,硬石膏粉45千克,石灰石粉19.3千克,混合磨細至比表面積達300平方米/千克~600平方米/千克,再加入偶氮二甲醯胺0.4千克,三聚磷酸鈉0.3千克,混合15分鐘。製成水泥混凝土複合型高性能膨脹劑。實驗材料用華新42.5級普通矽酸鹽水泥、聚羧酸高效減水劑,實驗配比為:水泥2760克,膨脹劑240克,減水劑6克,水灰比0.27,按照國家標準檢測,測試性能指標如下:
表1《用於水泥基材料的複合型高性能膨脹劑》檢測數據與施工規範技術性能比較
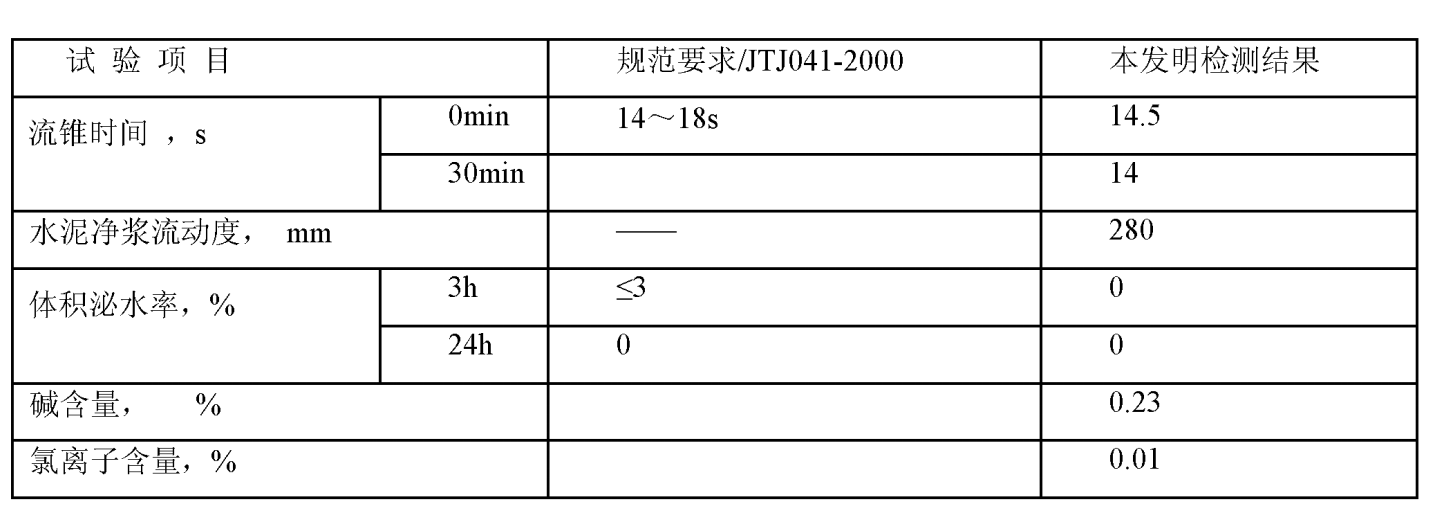
表1該發明檢測數據與施工規範技術性能比較
表2《用於水泥基材料的複合型高性能膨脹劑》檢測數據與混凝土膨脹劑規範要求指標比較
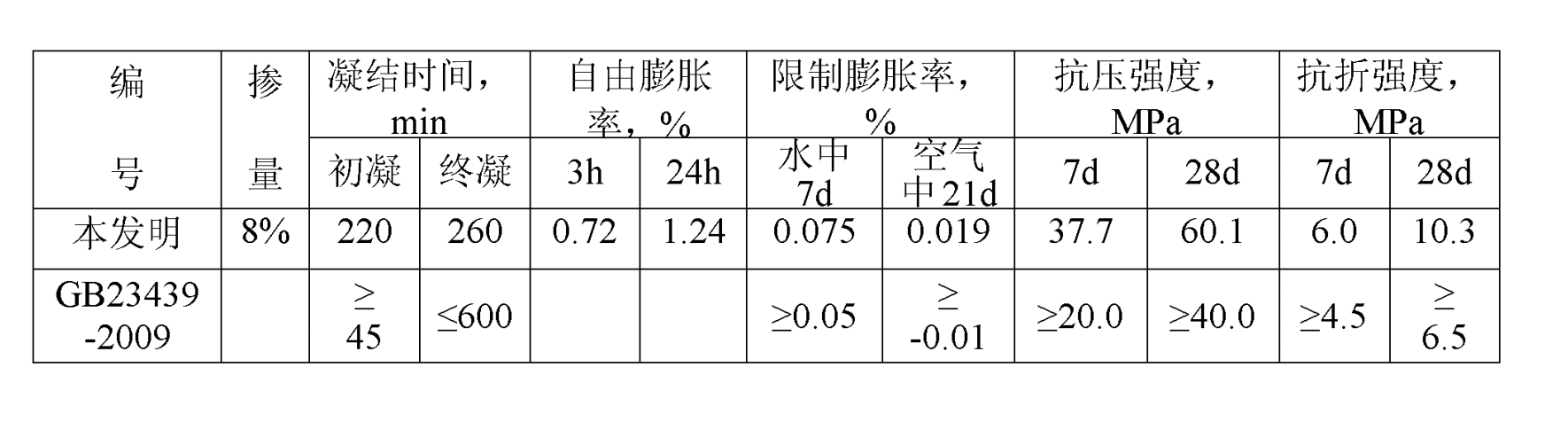
表2該發明檢測數據與混凝土膨脹劑規範要求指標比較
從表1、2顯示,檢測結果符合《混凝土膨脹劑》GB23439-2009及交通部JTJ041-2000標準要求,性能優越。表2中自由膨脹率為用戶要求。
實施例2
以100千克複合型高性能膨脹劑為例,其配方是:
稱取脂膜石灰30千克,硬石膏50千克,石灰石粉19.4千克,混合磨細至比表面積達300平方米/千克~600平方米/千克;再加入偶氮二甲醯胺和偶氮二異丁腈重量比1:1的混合物0.4千克,六偏磷酸鈉0.2千克。混合15分鐘。製成水泥混凝土複合型高性能膨脹劑。按照國家標準檢測,摻量占水泥基材料總質量的9%時,水中養護7天限制膨脹率為0.061%,空氣中養護21天限制膨脹率為0.022%,7天抗壓強度為36.2兆帕,28天抗壓強度為59.7兆帕,7天抗折強度為6.3兆帕,28天抗折強度為10.1兆帕,符合《混凝土膨脹劑》GB23439-2009標準要求;並且漿體3小時產生的塑性膨脹率為0.68%,24小時自由膨脹率為0.79%,解決了傳統材料在塑性階段都會產生的塑性沉降收縮問題。
榮譽表彰
2020年7月14日,《用於水泥基材料的複合型高性能膨脹劑》獲得第二十一屆中國專利獎優秀獎。