凸緣管使用的是柔性切割連枷的旋轉方式,用的是割草機內的連線螺桿。通過新穎的方法將螺桿連線到用於切割連枷釋放部分的切割端的各部件上。
基本介紹
- 中文名:凸緣管
- 套用領域:工業工程
凸緣管成形方法
凸緣管成形工藝現狀
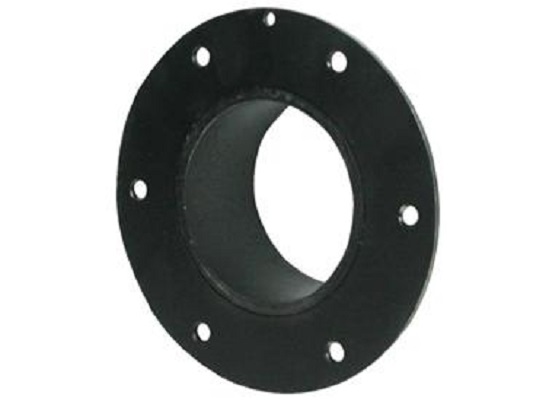
標準參數
公稱 通徑 DN | 管子 外徑 A | 連線尺寸 | 密封尺寸 | 法蘭 厚度 C | 法蘭 內徑 B | 法蘭 理論 重量 kg | |||||
法蘭管徑 D 系列1/系列2 | 螺栓孔中心圓直徑 K | 螺栓孔直徑 L 系列1/系列2 | 螺栓、螺柱 | d | f | ||||||
數量 n | 螺紋Th. 系列1/系列2 | ||||||||||
10 | 14 | 90 | 60 | 14 | 4 | M12 | 40 | 2 | 12 | 15 | 0.46 |
15 | 18 | 95 | 65 | 14 | 4 | M12 | 45 | 2 | 12 | 19 | 0.51 |
20 | 25 | 105 | 75 | 14 | 4 | M12 | 55 | 2 | 14 | 26 | 0.75 |
25 | 32 | 115 | 85 | 14 | 4 | M12 | 65 | 2 | 14 | 33 | 0.89 |
32 | 38 | 140/135 | 100 | 18 | 4 | M16 | 78 | 2 | 16 | 39 | 1.40 |
40 | 45 | 150/145 | 110 | 18 | 4 | M16 | 85 | 3 | 18 | 46 | 1.71 |
50 | 57 | 165/160 | 125 | 18 | 4 | M16 | 100 | 3 | 18 | 59 | 2.09 |
65 | 73 | 185/180 | 145 | 18 | 4 | M16 | 120 | 3 | 20 | 75 | 2.84 |
80 | 89 | 200/195 | 160 | 18 | 4 | M16 | 135 | 3 | 20 | 91 | 3.24 |
100 | 108 | 220/215 | 180 | 18 | 8 | M16 | 155 | 3 | 22 | 110 | 4.01 |
125 | 133 | 250/245 | 210 | 18 | 8 | M16 | 185 | 3 | 24 | 135 | 5.40 |
150 | 159 | 285/280 | 240 | 23 | 8 | M20 | 210 | 3 | 24 | 161 | 6.67 |
175 | 194 | 310 | 270 | 23 | 8 | M20 | 240 | 3 | 24 | 196 | 7.44 |
200 | 219 | 340/335 | 295 | 23 | 8 | M20 | 265 | 3 | 24 | 222 | 8.24 |
225 | 245 | 365 | 325 | 23 | 8 | M20 | 295 | 3 | 24 | 248 | 9.30 |
250 | 273 | 395/390 | 350 | 23 | 12 | M20 | 320 | 3 | 26 | 276 | 10.70 |
300 | 325 | 445/440 | 400 | 23 | 12 | M20 | 368 | 4 | 28 | 328 | 12.90 |
350 | 377 | 505/500 | 460 | 23 | 16 | M20 | 428 | 4 | 28 | 380 | 16.90 |
400 | 426 | 565 | 515 | 26/25 | 16 | M24/M22 | 482 | 4 | 30 | 430 | 21.80 |
450 | 480 | 615 | 565 | 26/25 | 20 | M24/M22 | 532 | 4 | 30 | 484 | 24.40 |
500 | 530 | 670 | 620 | 26/25 | 20 | M24/M22 | 585 | 4 | 32 | 534 | 27.70 |
600 | 630 | 780 | 725 | 30 | 20 | M27 | 685 | 5 | 36 | 634 | 39.40 |
700 | 720 | 895 | 840 | 30 | 24 | M27 | 800 | 5 | 36 | 715 | 53 |
800 | 820 | 1015/1010 | 950 | 34 | 24 | M30 | 905 | 5 | 38 | 817 | 67 |
900 | 920 | 1115/1110 | 1050 | 34 | 28 | M30 | 1005 | 5 | 38 | 918 | 76參考 |
1000 | 1020 | 1230/1220 | 1160 | 36/34 | 28 | M33/M30 | 1115 | 5 | 38 | 1020 | 90參考 |
1100 | 1120 | 1340 | 1270 | 36 | 28 | M33 | 1222 | 5 | 40 | 125參考 | |
1200 | 1220 | 1455/1450 | 1380 | 39/41 | 32 | M36 | 1325 | 5 | 44 | 1223 | 143參考 |
凸緣管新成形方案
凸緣管設計待解決的問題
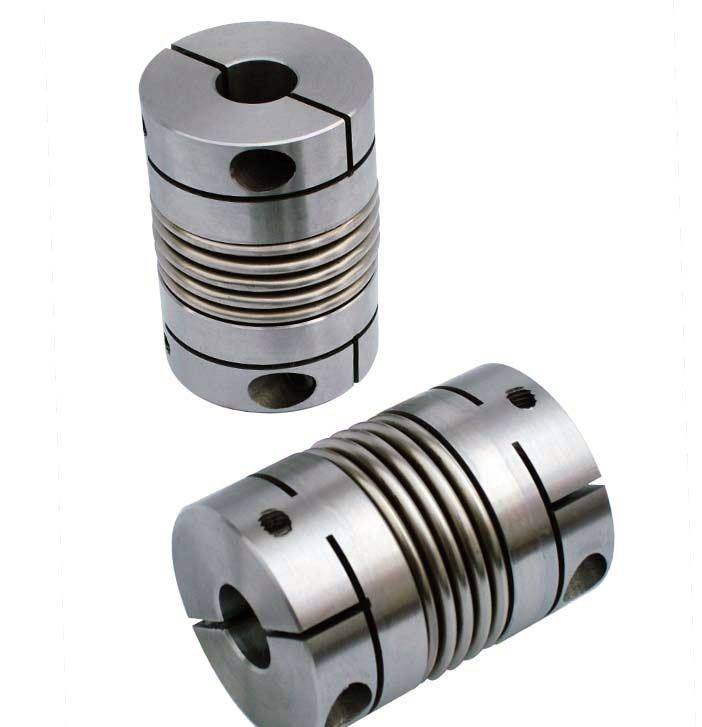