專利背景
傳統高磁感取向矽鋼的基本化學成分為Si2.0~4.5%,C0.03~0.10%,Mn0.03~0.2%,S0.005~0.050%,Als(酸溶鋁)0.02~0.05%,N0.003~0.012%,有的成分體系還含有Cu、Mo、Sb、B、Bi等元素中的一種或多種。
傳統高磁感取向矽鋼的製造方法為:首先用轉爐(或電爐)煉鋼,經二次精煉及合金化,連鑄成板坯;接著板坯在專用高溫加熱爐內加熱到約1400℃,並保溫45min以上,使有利夾雜物充分固溶;然後進行熱軋,層流冷卻後卷取,在熱軋板常化過程中矽鋼基體內析出細小、彌散的第二相質點,獲得有效抑制劑;再將熱軋板冷軋到成品厚度後脫碳退火,把鋼板中的
脫到不影響成品磁性能的程度(一般應在30ppm以下),並塗布以MgO為主要成分的退火隔離劑;再次進行高溫退火,在高溫退火過程中,鋼板發生二次再結晶、形成矽酸鎂底層並完成淨化處理(除去鋼中的S、N等對磁性有害的元素),獲得取向度高、鐵損低的高磁感取向矽鋼;最後經過塗布絕緣塗層和拉伸退火,得到商業套用形態的取向矽鋼產品。
傳統高磁感取向矽鋼製造方法的不足在於:為了使抑制劑充分固溶,加熱溫度最高需達到1400℃,這是傳統加熱爐的極限水平。此外,由於加熱溫度高,燒損大、加熱爐需頻繁修補,利用率低。同時,能耗高,熱軋卷的邊裂大,致使冷軋工序生產困難,成材率低,成本也高。
鑒於存在上述這些問題,在該技術領域內開展了大量降低取向矽鋼加熱溫度的研究。按照板坯加熱溫度範圍來區分,其主要改進路徑有兩種:一種是中溫板坯加熱工藝,板坯加熱溫度在1250~1320℃,採用AlN和Cu作為抑制劑;另一種是低溫板坯加熱工藝,板坯加熱溫度在1100~1250℃,採用滲氮方法導入抑制劑。
目前,低溫板坯加熱工藝發展較快,例如採用在1200℃以下進行板坯加熱,最終冷軋採用冷軋壓下率大於80%,並在脫碳退火過程中採用氨氣進行連續滲氮處理,經高溫退火獲得取向度較高的二次再結晶晶粒。該製造工藝的優點是可以實現較低成本地生產高磁感取向矽鋼(HiB),該矽鋼的典型磁感B8為1.88~1.92T。
低溫板坯加熱工藝抑制劑主要來源於脫碳退火後通過滲氮處理,使氮與鋼中原有的鋁結合,形成細小彌散的(Al,Si)N、(Mn,Si)N質點。同時,抑制劑還來源於板坯中已有的夾雜物,這些夾雜物在煉鋼澆鑄過程中形成,在板坯加熱過程部分固溶並在軋制過程中析出,常化退火調整夾雜物形態,對初次再結晶有著重要影響從而也會影響最終產品的磁性能。當初次晶粒尺寸與抑制力水平匹配時,二次再結晶予以完善,最終產品的磁性能優良。常化過程中析出的氮化物抑制劑雖然受到板坯中夾雜物形態的影響,但是板坯中夾雜物形態的控制是相當困難的,例如,在澆鑄過程中形成粗大的AlN在後續退火中難以固溶,導致初次晶粒尺寸穩定性控制的難度大,穩定獲得磁感B8≥1.93T的高等級HiB產品的機率低。此外,在成品厚度確定的條件下,通常採取的一些進一步降低鐵損的措施會導致磁感的降低,例如,提高Si含量或雷射刻痕等。磁感的降低使得這些降低鐵損的方法套用範圍受限。另一些提高磁感B8的方法,如在脫碳退火過程中快速加熱,則需要新增快速感應加熱或通電加熱等專用設備,投資成本增加。另外,快速升溫會增加成品底層缺陷,尤其是亮點狀缺陷的發生率。
專利公開號為CN1138107A,公開日為1996年12月18日,名稱為“高磁通密度低鐵損晶粒取向的電磁鋼板及其製造方法”的中國專利文獻公開了一種電磁鋼板,其含有Si:2.5~4.0wt%,Al:0.005~0.06wt%,並且該鋼板的各個晶粒之中,按面積率計,至少95%由直徑為5~50毫米的粗大的二次再結晶晶粒組成,其(001)軸相對於該鋼板的軋制方向在5°以內,而(001)軸相對於板面垂直方向在5°以內;在這種粗大的二次再結晶晶粒中或者晶界中,存在直徑為0.05~2毫米的細小晶粒,其(001)軸與粗大的二次晶粒的(001)軸的相對角度在2~30°。
專利公開號為JP8232020A,公開日為1996年9月10日,名稱為“方向性電磁鋼片的製造方法”的日本專利文獻涉及了一種生產廉價優異磁性的矽鋼片的製造方法,其步驟包括特定軋制速度的冷連軋和退火,調節至特定ppm的總氮含量,然後完成退火。該鋼片的重量百分配比為C:0.001~0.09%,矽:2~4.5%,酸溶鋁:0.01~0.08%,N:0.00010.004%,獨立或總數S和(或)硒:0.008~0.06%,銅:0.01~1%,錳:0.01~0.5%,少量的Bi、P、Sn、Pb、B、V、鈮等,餘量為Fe和其他不可避免的雜質。冷軋矽鋼的冷連軋率為75~95%,退火溫度為800~1000℃,退火時間為1300秒,總氮含量為50~1000ppm。
專利公開號為JP4337029A,公開日為1992年11月25日,名稱為“一種方向性電磁鋼板的一次再結晶燒結方法”的日本專利文獻公開了方向性電磁鋼板的製造方法,其主要涉及滲氮法取向矽鋼初次晶粒尺寸控制方法及提出根據Als、N與Si調整脫碳溫度的方法。
發明內容
專利目的
《一種高磁感取向矽鋼及其製造方法》的目的在於提供一種高磁感取向矽鋼及其製造方法,其在不新增設備的前提下,通過對鋼種成分的設計及對脫碳退火工藝的控制,獲得磁性能更優異的取向矽鋼產品,其磁感較普通取向矽鋼有明顯的提高,典型磁感B8>1.93T。
技術方案
《一種高磁感取向矽鋼及其製造方法》提供了一種高磁感取向矽鋼,其化學元素重量百分含量為:C:0.035~0.120%,Si:2.9~4.5%,Mn:0.05~0.20%,P:0.005~0.050%,S:0.005~0.012%,Als:0.015~0.035%,N:0.001~0.010%,Cr:0.05~0.30%,Sn:0.005~0.090%,V:≤0.0100%,Ti:≤0.0100%,微量元素Sb、Bi、Nb和Mo的至少其中之一,且滿足Sb+Bi+Nb+Mo:0.0015~0.0250%,餘量為Fe和其它不可避免的雜質;且(Sb/121.8+Bi/209.0+Nb/92.9+Mo/95.9)/(Ti/47.9+V/50.9)的值,即(Sb+Bi+Nb+Mo)/(V+Ti)的摩爾分數比,處於0.1~15範圍內。
進一步地,《一種高磁感取向矽鋼及其製造方法》所述的高磁感取向矽鋼,其初次晶粒尺寸Φ≤30微米,初次再結晶度P≥90%。
在本技術方案中,發明人通過添加微量元素Sb、Bi、Nb或Mo,並控制雜質元素V、Ti的含量,優先形成微量元素的碳、氮化合物,板坯中以TiN、TiC或VN為核心的MnS+AlN複合夾雜物數量大為減少。由於這些複合夾雜物尺寸粗大,在板坯加熱及後續退火過程中不能完全固溶,抑制效果差,而隨著(Sb+Bi+Nb+Mo)含量之和及(Sb+Bi+Nb+Mo)/(V+Ti)的摩爾分數比的增加,一方面微量元素及其形成的碳、氮化合物可作為輔助抑制劑,起到增強抑制力的效果,另一方面,由於MnS+AlN複合夾雜物數量的減少,細小彌散AlN數量的增加,這既增強了二次再結晶的抑制力水平,也有利於初次晶粒細小均勻、初次再結晶程度高,有利於二次再結晶的完善,因此成品鋼板的磁感明顯提高。
相應地,《一種高磁感取向矽鋼及其製造方法》還提供了上述高磁感取向矽鋼的製造方法,其包括如下步驟:
(1)冶煉和澆鑄後獲得板坯;
(2)熱軋;
(3)常化退火;
(4)冷軋;
(5)脫碳退火:脫碳溫度滿足T(x1,x2)=ax1+bx2+c,其中x1為Sb+Bi+Nb+Mo的重量百分比含量,單位為ppm,x2為(Sb+Bi+Nb+Mo)/(V+Ti)的摩爾分數比,單位為1,a取值範圍為0.1~1.0,b取值範圍為0.1~1.0,c取值範圍為800~900℃,其表示不添加微量元素時的脫碳溫度;脫碳時間為80~160秒;
(6)滲氮處理;
(7)在鋼板上進行MgO塗層後進行高溫退火;
(8)塗敷絕緣塗層以及熱拉伸平整退火後得到高磁感取向矽鋼。
進一步地,《一種高磁感取向矽鋼及其製造方法》所述的高磁感取向矽鋼的製造方法將脫碳退火溫度控制為以使初次晶粒尺寸Φ≤30微米且初次再結晶度P≥90%。
進一步地,《一種高磁感取向矽鋼及其製造方法》所述的高磁感取向矽鋼的製造方法還包括步驟(9)細化磁疇,以獲得鐵損要求更低的產品。細化磁疇可以採用雷射刻痕的方法,經雷射刻痕後,高磁感取向矽鋼的磁性能更為優異。
進一步地,《一種高磁感取向矽鋼及其製造方法》所述的高磁感取向矽鋼的製造方法的步驟(2)中,加熱溫度≤1250℃。
進一步地,《一種高磁感取向矽鋼及其製造方法》所述的高磁感取向矽鋼的製造方法的步驟(4)中冷軋壓下率≥75%。
更進一步地,《一種高磁感取向矽鋼及其製造方法》所述的高磁感取向矽鋼的製造方法的步驟(6)中滲入氮含量50~260ppm。
《一種高磁感取向矽鋼及其製造方法》所述的高磁感取向矽鋼的製造方法,關鍵在於控制脫碳溫度,適宜的脫碳溫度的設定需要實現兩個目的:一是使初次晶粒尺寸Φ≤30微米,二是使初次再結晶的再結晶度P≥90%,其中初次再結晶度P的定義為脫碳退火後帶鋼發生初次再結晶的比例。當初次晶粒尺寸Φ≤30微米且再結晶度P≥90%時,帶鋼的磁性能更加優異。為了使初次晶粒尺寸與再結晶度都能滿足上述要求範圍,脫碳溫度需要根據板坯中微量元素含量及其比例進行設定,並滿足函式關係式T(x1,x2)=ax1+bx2+c。在本技術方案中,初次晶粒尺寸Φ和初次再結晶度P是可以採用本領域內的常規測量手段測得的,例如初次再結晶度P可以採用電子背散射衍射(EBSD)測得。
另外,由上述脫碳溫度的函式關係式可以看出,添加微量元素Sb、Bi、Nb或Mo後的脫碳溫度較不添加這些元素成分體系的脫碳溫度高。這是因為在鋼板中的MnS+AlN複合夾雜物數量的減少,而細小彌散AlN數量的增加,增強了初次再結晶的抑制效果,因此需要適當增加脫碳溫度。
《一種高磁感取向矽鋼及其製造方法》所述的高磁感取向矽鋼,相比普通的高磁感取向矽鋼,其初次再結晶度高,初次晶粒尺寸更為細小、均勻,二次再結晶晶粒更為粗大,在鐵損不降低或略有降低的情況下,其磁感顯著提高,產品磁性能穩定。
《一種高磁感取向矽鋼及其製造方法》所述的高磁感取向矽鋼的製造方法,通過在煉鋼過程中添加微量元素並控制相應雜質元素的含量,並配合後續脫碳退火工藝的調整,使初次晶粒尺寸≤30微米且初次再結晶的再結晶度≥90%,既可使微量元素及其形成的碳、氮化合物作為輔助抑制劑,又可使板坯中MnS+AlN複合夾雜物數量減少,細小彌散AlN數量增加,有利於初次晶粒細小均勻且初次再結晶度高,有利於成品磁感提高,從而獲得一種具有優異磁性能的取向矽鋼。
附圖說明
圖1顯示了高磁感取向矽鋼的初次晶粒尺寸、再結晶度與磁感的關係。

技術領域
《一種高磁感取向矽鋼及其製造方法》涉及一種鋼板及其製造方法,尤其涉及一種矽鋼及其製造方法。
權利要求
1.一種高磁感取向矽鋼,其特徵在於,其化學元素重量百分含量為:C:0.035~0.120%,Si:2.9~4.5%,Mn:0.05~0.20%,P:0.005~0.050%,S:0.005~0.012%,Als:0.015~0.035%,N:0.001~0.010%,Cr:0.05~0.30%,Sn:0.005~0.090%,V:≤0.0100%,Ti:≤0.0100%,微量元素Sb、Bi、Nb和Mo的至少其中之一,且滿足Sb+Bi+Nb+Mo:0.0015~0.0250%,餘量為Fe和其它不可避免的雜質;且(Sb/121.8+Bi/209.0+Nb/92.9+Mo/95.9)/(Ti/47.9+V/50.9)的值處於0.1~15範圍內。
2.如權利要求1所述的高磁感取向矽鋼,其初次晶粒尺寸Φ≤30微米,初次再結晶度P≥90%。
3.如權利要求1所述的高磁感取向矽鋼的製造方法,其特徵在於,包括下列步驟:(1)冶煉和澆鑄後獲得板坯;(2)熱軋;(3)常化退火;(4)冷軋;(5)脫碳退火:脫碳溫度滿足T(x1,x2)=ax1+bx2+c,其中x1為Sb+Bi+Nb+Mo的重量百分比含量,單位為ppm,x2為(Sb+Bi+Nb+Mo)/(V+Ti)的摩爾分數比,a取值範圍為0.1~1.0,b取值範圍為0.1~1.0,c取值範圍為800~900℃;脫碳時間為80~160s;(6)滲氮處理;(7)在鋼板上進行MgO塗層後進行高溫退火;(8)塗敷絕緣塗層以及熱拉伸平整退火後得到高磁感取向矽鋼。
4.如權利要求3所述的高磁感取向矽鋼的製造方法,其特徵在於,控制脫碳溫度,以使初次晶粒尺寸Φ≤30微米且初次再結晶度P≥90%。
5.如權利要求3或4所述的高磁感取向矽鋼的製造方法,其特徵在於,還包括步驟(9)細化磁疇。
6.如權利要求3或4所述的高磁感取向矽鋼的製造方法,其特徵在於,所述步驟(2)中,加熱溫度≤1250℃。
7.如權利要求3或4所述的高磁感取向矽鋼的製造方法,其特徵在於,所述步驟(4)中冷軋壓下率≥75%。
8.如權利要求3或4所述的高磁感取向矽鋼的製造方法,其特徵在於,所述步驟(6)中滲入氮含量50~260ppm。
實施方式
圖1顯示了本技術方案中高磁感取向矽鋼的初次晶粒尺寸、再結晶度與磁感的關係,從圖1可以看出,對於本技術方案來說,當初次晶粒尺寸Φ≤30微米且初次再結晶度P≥90%時,帶鋼的磁感B8>1.93T。
下面結合具體實施例和比較例對於《一種高磁感取向矽鋼及其製造方法》所述的技術方案做進一步的說明和解釋。
按照下列步驟製造《一種高磁感取向矽鋼及其製造方法》所述的高磁感取向矽鋼:
(1)按照如表1所示的成分配比進行冶煉,澆鑄後得到板坯;
(2)將板坯於1150℃加熱後熱軋至厚度為2.3毫米的熱軋板;
(3)常化退火;
(4)冷軋到成品厚度0.30毫米;
(5)脫碳溫度滿足函式關係式:T=0.21x1+0.16x2+831,脫碳時間為80~160s,使鋼板中
含量降到30ppm以下;
(6)滲氮處理:滲入[N]含量100~160ppm;
(7)在鋼板上進行MgO塗層後在氣氛為100%H2、溫度為1200℃的條件下進行20小時的高溫退火;
(8)開卷後塗敷絕緣塗層以及熱拉伸平整退火後得到高磁感取向矽鋼。
上述脫碳溫度函式關係式是通過選取冷軋到成品厚度且經過25h高溫退火的鋼材進行不同成分、不同脫碳溫度的試驗組合,測定脫碳鋼板的初次晶粒尺寸Φ與初次再結晶度P,選擇符合初次晶粒尺寸Φ≤30微米且初次再結晶度P≥90%的鋼卷進行統計分析(x1、x2值相同時,優選P/Φ值較大的鋼卷進行統計分析),採用線性擬合法得到脫碳溫度與x1、x2間的函式關係式的a、b與c。參與擬合的數據如表2所示。
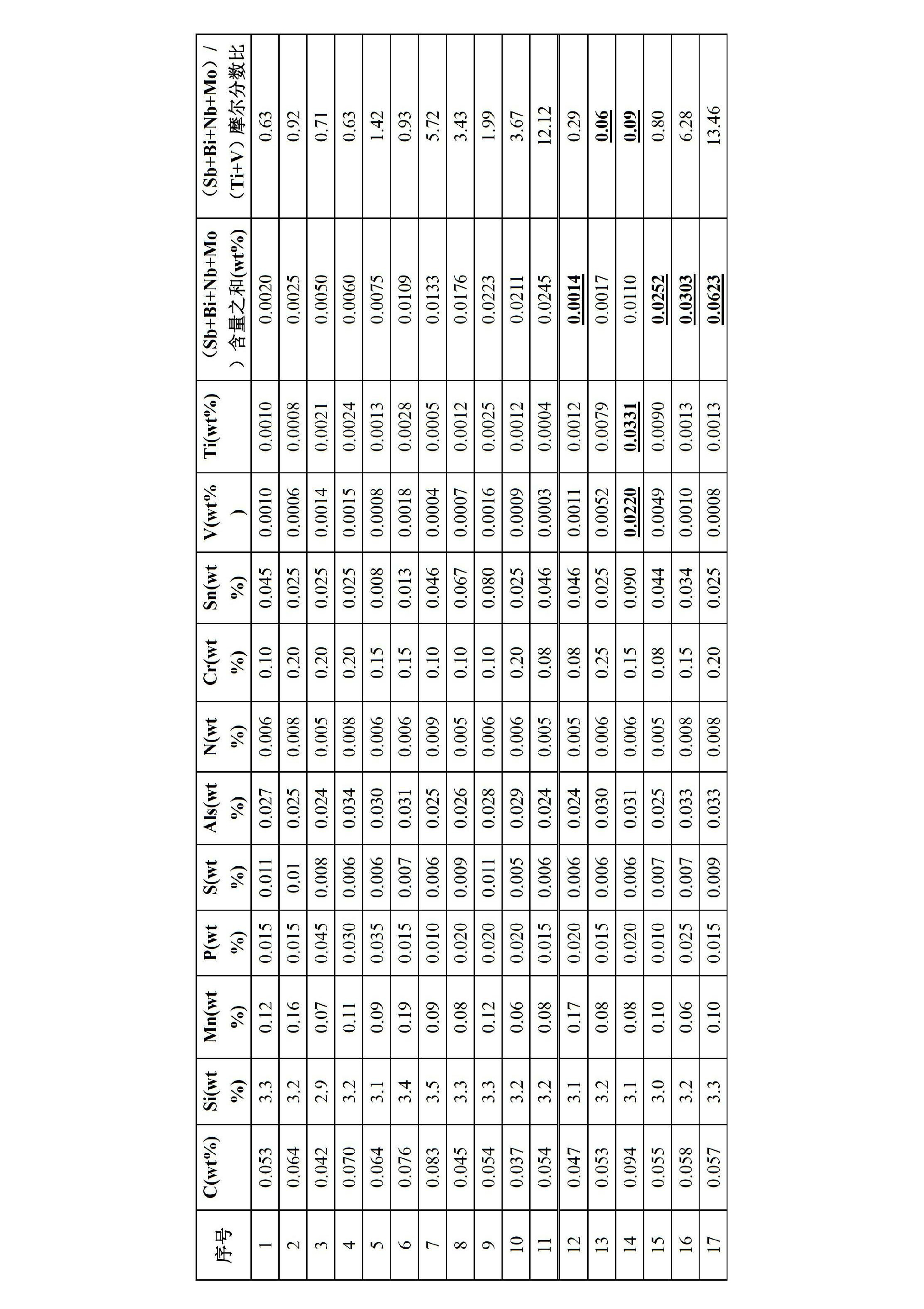
表1.
(序號1-11為實施例,序號12-17為比較例)
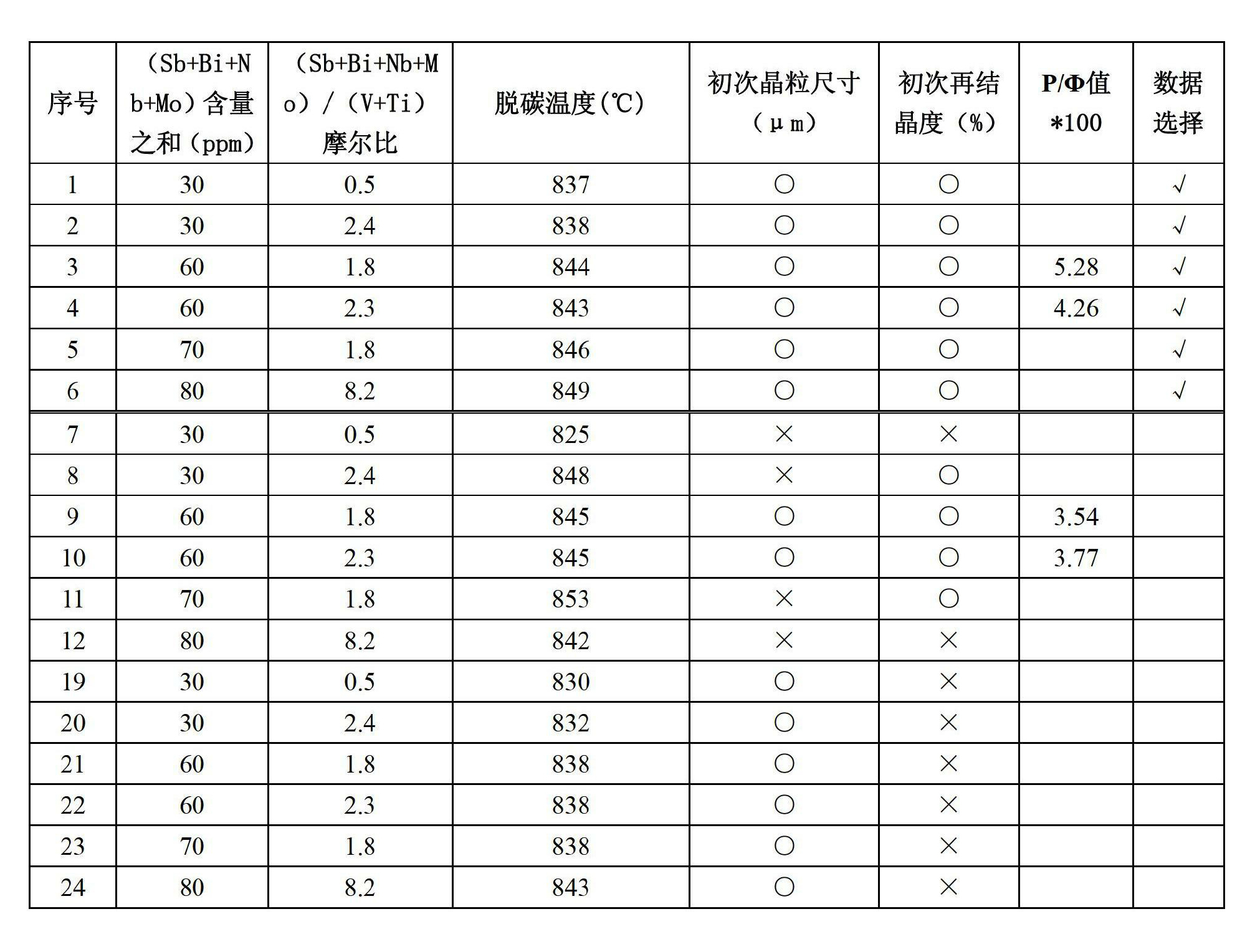
表2.
註:○表示滿足要求;×表示不滿足要求。
表3顯示了實施例1-12和比較例14-17的脫碳溫度、再結晶度、初次晶粒尺寸、磁感B8與鐵損P17/50。
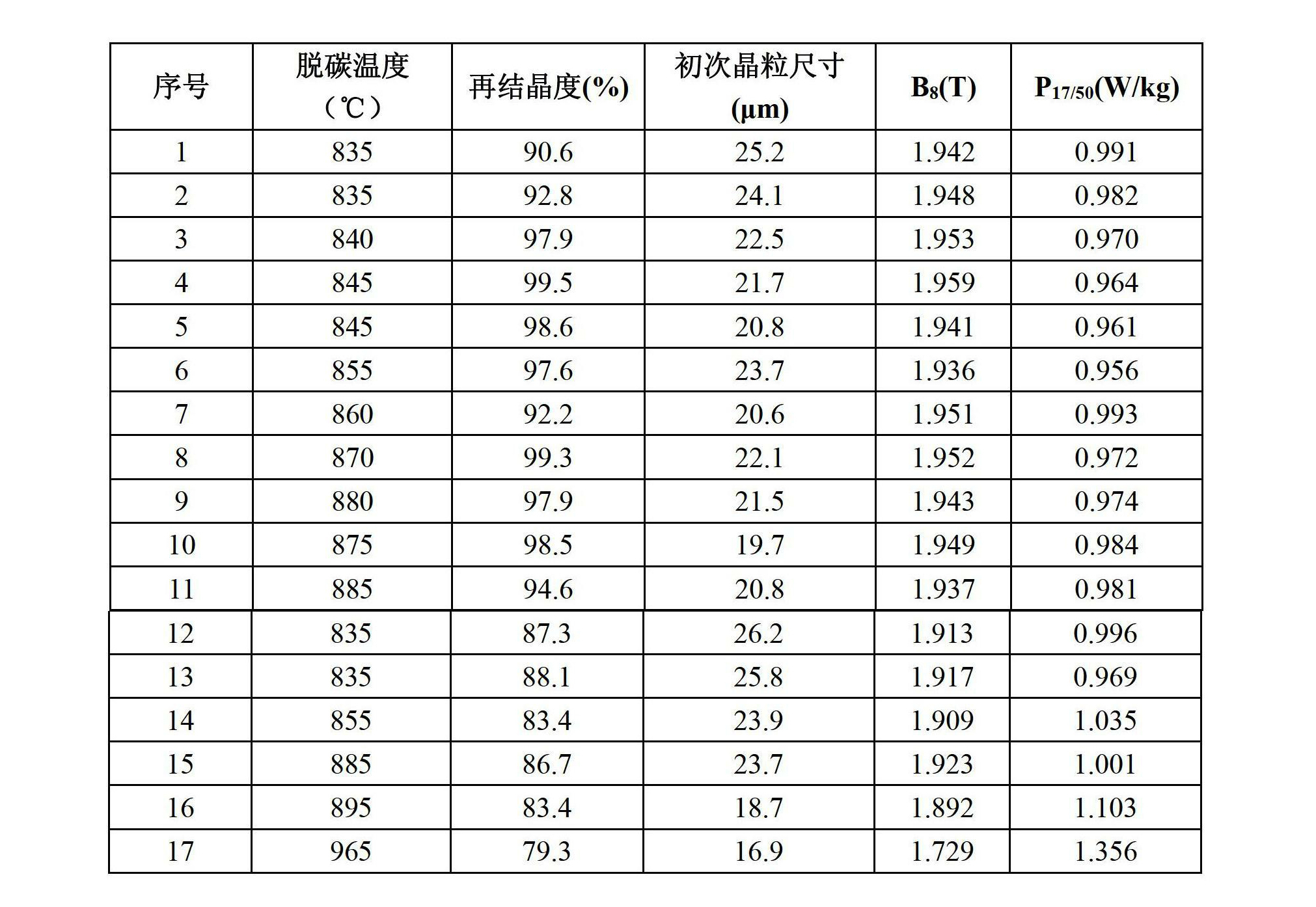
表3.
由表1和表3可見,採用《一種高磁感取向矽鋼及其製造方法》所述的技術方案的,尤其是微量元素含量及其比例滿足《一種高磁感取向矽鋼及其製造方法》的成分設計要求,脫碳溫度、初次晶粒尺寸和再結晶度滿足要求的鋼卷,其磁性能普遍很好,磁感B8都大於1.93T。
為了進一步說明細化磁疇步驟對取向矽鋼鐵損性能的影響,發明人還按常規低溫取向矽鋼成分,添加Sb、Bi、Nb或Mo元素,並控制V、Ti含量<0.0020%,通過採用合適的脫碳溫度獲得0.23毫米厚度取向矽鋼產品,經雷射刻痕處理後得到若干產品,其磁性能見表4。
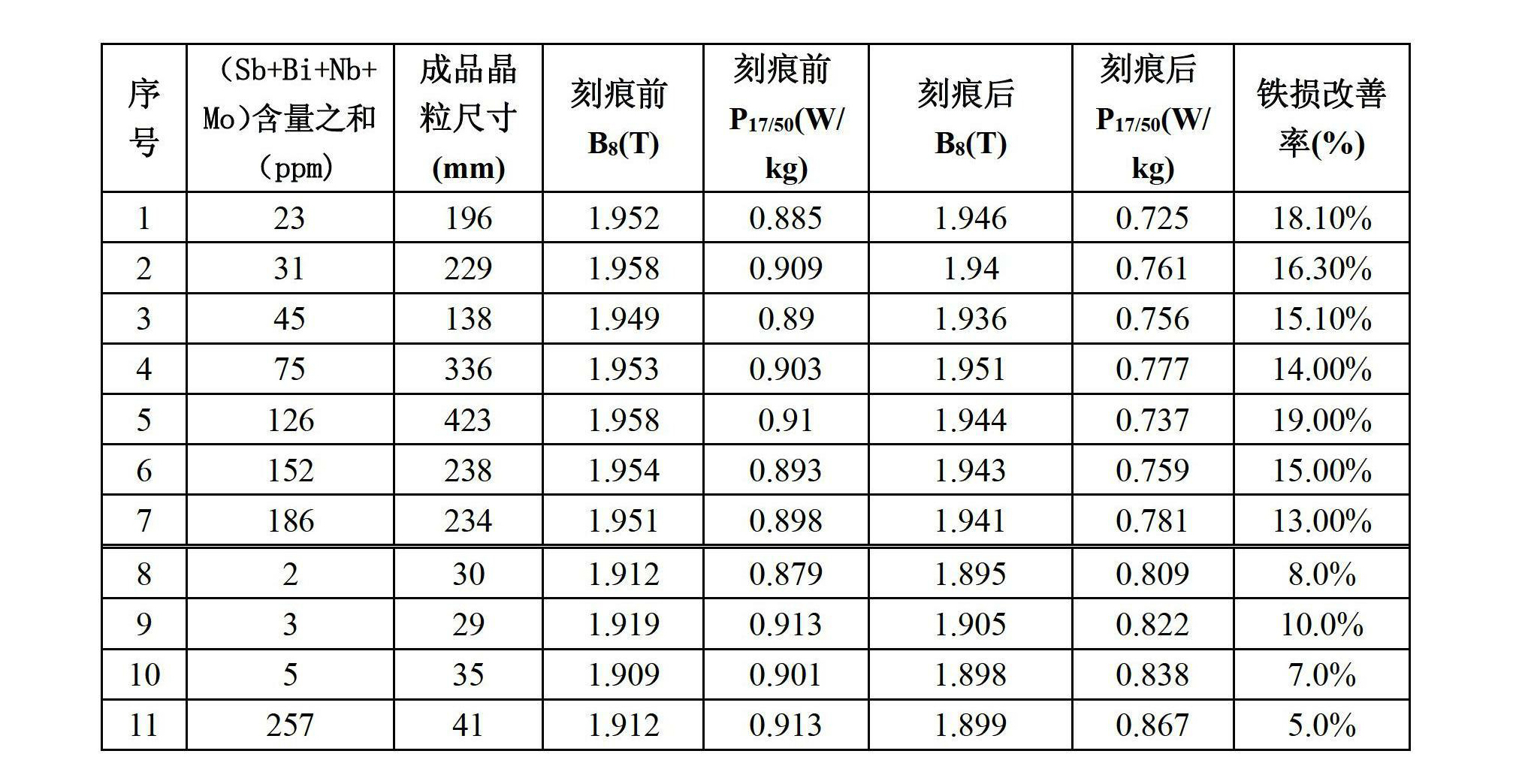
表4.
由表4可知,由於最終產品晶粒粗大,序號1~7的產品經雷射刻痕後,鐵損改善效果非常明顯,刻痕後產品綜合磁性能較序號8~11的產品明顯優異。
榮譽表彰
2018年12月20日,《一種高磁感取向矽鋼及其製造方法》獲得第二十屆中國專利優秀獎。