專利背景
混凝土超塑化劑(高效減水劑)尤其是高性能外加劑是減少水泥用量、提高工業廢渣利用率、提高混凝土強度等級和改善混凝土耐久性最有效、簡便和經濟的辦法,已成為配製高性能高耐久混凝土必不可少的第五組份,也是混凝土行業實現可持續發展戰略最重要的基礎材料。但傳統的萘系、三聚氰胺系等縮聚型外加劑存在減水率低、坍落度損失大、增大收縮等問題且生產工藝污染環境,不利於可持續發展,而且這類縮聚物外加劑由於受到分子結構和作用機理的制約性能不可能有大的改進。新一代聚羧酸系混凝土外加劑由於存在摻量低、保坍性能好、混凝土收縮率低、分子結構上高性能化的潛力大、生產過程中不使用甲醛和不排放廢液等突出優點成為了世界性的研究熱點和發展重點。日本是研究和套用聚羧酸系混凝土外加劑最多也是最成功的國家,截至2007年8月聚羧酸外加劑已占所有高性能外加劑產品總數的80%以上,北美和歐洲聚羧酸外加劑也占了50%以上的市場。中國聚羧酸系混凝土外加劑的研究始於20世紀90年代中後期,其工業化生產與套用始於21世紀初期。
常規聚羧酸系混凝土外加劑的合成方法是:首先合成單烷基聚醚,然後利用不飽和酸或酸酐對單烷基聚醚進行酯化製備不飽和大分子,最後採用自由基共聚合的方法將其它不飽和功能單體與酯化後的不飽和大分子一起共聚而製得梳形高分子聚羧酸系混凝土外加劑。
單烷基聚醚則是生產聚羧酸系混凝土外加劑的最主要原材料,占聚羧酸外加劑總重量的60~90%,使用該原料合成的聚羧酸高效系外加劑有較強的水泥顆粒分散性保持能力,使產品具有摻量低、減水率高、增強效果好、耐久性、不鏽蝕鋼筋及對環境友好等優點。可套用在現場攪拌及遠距離輸送的高性能、高強度(C60以上)的商品混凝土中。國內由於生產聚醚原材料的廠家不了解用於生產聚羧酸系減水劑聚醚的質量標準,部分廠家甚至採用雙氧水對聚醚進行脫色處理,但是在外加劑行業,單烷基聚醚要首先和不飽和酸酯化,原料中殘留的雙氧水起到了引發劑的作用,導致不飽和酸在酯化工程中發生聚合,這在極大程度上影響了酯化反應的順利進行,同時在酯化會產生羧酸均聚物副產物,降低了合成聚羧酸系混凝土外加劑原料的品質,從而也導致了後續生產出來的聚羧酸系混凝土外加劑質量不佳。
專利ZL200510037870.7中指出,對於聚羧酸系混凝土外加劑而言,具有短接枝側鏈的梳形共聚物由於空間位阻效應較弱,其分散性較低,但分散保持性很好;具有較長接枝側鏈的梳形共聚物由於空間位阻效應較強,對混凝土早期流動性能有利,但流動性的保持能力較差。只有準確調整合成聚羧酸系混凝土外加劑合成過程中聚醚的分子鏈長度以及各種聚醚的含量,才能靈活準確控制聚羧酸系混凝土外加劑的使用性能。
專利US5689012公開了一種在管式反應器或連續攪拌釜式反應器中套用DMC催化劑製備聚氧化烯聚醚的連續方法,但是向管式反應器中加入反應物時,反應物的高濃度可能會造成DMC催化劑的失活;而套用連續攪拌釜式反應器得到的產品含有大量未反應的氧化烯,這使得反應過程的危險性和污染性極高,不適宜於可持續性發展戰略目標的要求。
專利US2586767中描述了一種製備烷氧基化產品的工藝,在迴路反應器內,將包含至少6個碳原子和至少1個活性氫原子的化合物噴射到環氧乙烷靜止氣相中,液相通過外部循環冷卻並重新被噴射到反應區,直到反應產物達到預想的分子量為止。該工藝所製備的聚醚分子量分布也比較窄,產品質量較好,但由於反應器上端的環氧乙烷氣相為靜止相,氣相中環氧乙烷因局部濃度過大而長期得不到更新,一旦發生爆炸不能採取緊急停車措施,所以其安全性方面也存在缺陷,且其產品在後處理階段依然有少量污染物。同時該工藝所製備出的聚醚需要經過酯化過程,這不但增長了聚羧酸系混凝土外加劑的合成工藝路線,同時會由於一方面酯化程度不能達到100%進行而造成合成聚羧酸系混凝土外加劑原料品質的降低,另一方面,聚醚中雜質聚乙二醇經過酯化過程會生成對後續合成聚羧酸系混凝土外加劑過程有嚴重危害性的物質。
專利US5478535中公開了一種氣-液接觸反應裝置,該裝置具有極其優越的傳質傳熱效果,完善的安全性和極受關注和親睞的無環境污染性,聚醚分子量可控性好且分布窄。但是其並未指出採用端頭帶雙鍵的不飽和單體作為起始劑通過一步法製備具有聚合活性的聚羧酸系混凝土外加劑專用聚醚,而製備出的產品是烷氧基聚醚,因此要合成聚羧酸系混凝土外加劑同樣需要進行酯化過程,這對合成高性能聚羧酸系混凝土外加劑不利。
專利CN1310735A中公布了通過在有效量雙金屬氰化物配合物催化劑存在下,且在自由基聚合阻聚劑存在下,使用端頭含有雙鍵的不飽和單體作為起始劑引發氧化烯開環聚合反應,一步法直接合成了具有聚合活性的大分子聚醚單體,避免了聚醚進行酯化的工藝過程,但是該反應是在連續攪拌式反應釜中進行的,除同樣會帶來極大的危險性和污染性外,所製備的聚醚分子量分布較寬,依然不利於精確控制後期製備的聚羧酸系混凝土外加劑的使用性能。
發明內容
專利目的
《一種製備聚羧酸系混凝土外加劑專用聚醚的方法》要解決的技術問題是2007年8月之前聚羧酸系混凝土外加劑聚醚原料或其生產裝置所存在的下述不足:①聚醚分子鏈相對過短,且分子量分布過寬;②多數生產裝置除引起產品中殘餘原料氧化烯(主要指環氧乙烷、環氧丙烷、或環氧乙烷與環氧丙烷的混合物)含量高外,還易於發生爆炸、中毒或污染環境;③製備的單烷基聚醚需要進行酯化過程製備成具有聚合活性的功能單體,才能用於合成聚羧酸系混凝土外加劑,這不但增長了聚羧酸系混凝土外加劑的合成工藝路線,同時會由於一方面酯化程度不能達到100%進行而造成合成聚羧酸系混凝土外加劑原料品質的降低,另一方面,聚醚中雜質聚乙二醇經過酯化過程後會生成對後續合成聚羧酸系混凝土外加劑過程有嚴重危害性的物質;④雖然已有報導採用不飽和單體(如烯丙基醇、丙烯酸羥乙酯、丙烯酸羥丙酯等)作為烷氧基化起始劑一步製備具有可聚合活性聚醚的方法,卻局限於採用連續攪拌釜式反應器中進行。
技術方案
一種製備聚羧酸系混凝土外加劑專用聚醚的方法,所述聚醚由以下化學式(1)所表示:
①採用X-O-H作為氧化烯開環聚合反應的起始劑來製備具有可聚合活性聚醚,其中X所表示的基團與式(1)中X相同;②在BUSS烷氧基化裝置上利用氧化烯開環聚合製備具有可聚合活性聚醚。
《一種製備聚羧酸系混凝土外加劑專用聚醚的方法》的具體製備過程如下:
1)用氮氣置換整套BUSS烷氧基化裝置,向迴路反應器預反應釜中加入起始劑、催化劑和阻聚劑後抽真空,升溫至80~120℃後脫水,再充氮氣使預反應釜壓力達0.25~0.45兆帕;
2)開動小循環泵,同時根據目標產品的分子量壓入相應量的氧化烯,反應1~3小時,氧化烯的加入量按以下方式確定:氧化烯的質量=(每批原料總質量÷目標產品分子量)×氧化烯分子量=目標產品分子鏈摩爾數×氧化烯分子量=催化劑摩爾數×氧化烯分子量=(催化劑總質量÷催化劑分子量)×氧化烯分子量;
前述氧化烯的加入量是基於這樣的考慮來確定的:一個催化劑分子最後引發生成一條高分子鏈,在所加入的催化劑全部參與反應前提下,催化劑的摩爾數所反映的就是目標產品分子鏈的摩爾數。
3)開啟大循環泵,加入餘量的的氧化烯,在110~170℃和0.25~0.45兆帕的壓力下進行聚合,加料和反應維持4-8小時後停止加氧化烯,繼續循環熟化至反應器內壓力不再減小進,反應結束;
4)開啟真空脫除反應器內游離的廢氣,反應器內粗產品冷卻至80~95℃,停止循環,粗產品排入中和釜,加中和劑中和到pH=6.5+0.3後進行真空脫水,即得最終產品。上述合成聚醚體系中起始劑和氧化烯的摩爾數之比為1:1~65,阻聚劑的用量為起始劑質量的0.05~1.5wt%,催化劑用量為氧化烯質量的0.05~0.2wt%。
步驟1)中所述起始劑為羥酯或端烯醇,前述羥酯或端烯醇選自丙烯酸羥乙酯,甲基丙烯酸羥乙酯,丙烯酸羥丙酯或甲基丙烯酸羥丙酯,烯丙醇;所述催化劑選自K
2O、Na
2O、NaOH、KOH、
蒙脫土、累脫石、雙金屬氰化物、多金屬氰化物絡合物或前述物任意兩種或兩種以上的混合物;所述阻聚劑為1,4-苯醌或1,4-萘醌。
步驟1)抽真空至-750毫米汞柱,脫水時間40~60分鐘。
步驟2)加入的氧化烯的摩爾量與催化劑相同。
步驟3)中氧化烯的加入速率為:(每批原料總質量-起始劑質量-通過小循環泵加入的氧化烯質量)/加料時間,加入量為:每批原料總質量-起始劑質量-步驟2)氧化烯加入量。繼續循環熟化時間為3~10分鐘。
步驟2)和3)所述氧化烯為環氧乙烷、環氧丙烷或它們任意比例的混合物。
合成聚醚體系中起始劑和氧化烯的摩爾數之比為1:1~65,阻聚劑的用量為起始劑質量的0.05~1.5wt%,催化劑用量為氧化烯質量的0.05~0.2wt%。
步驟4)開啟真空所脫除的反應器內游離的廢氣通入聚醚尾氣處理塔水洗處理後,尾氣通過20米排氣筒排入大氣;中和釜使用水環式真空泵進行真空脫水。
《一種製備聚羧酸系混凝土外加劑專用聚醚的方法》所採用的迴路反應器為瑞士BUSSChemTechAG公司所研發設計的文丘里管氣-液接觸迴路反應器。
改善效果
《一種製備聚羧酸系混凝土外加劑專用聚醚的方法》可生產出專門針對於聚羧酸系混凝土外加劑用高性能聚羧酸系混凝土外加劑專用聚醚,具有如下優點:①聚醚分子量可控,能生產分子量為190~4,000的任意指定分子量聚醚,聚醚分子量分布極窄,操作靈活性大,性能控制精準性好,合成聚醚產品品質優越;②由於所生產的聚醚是端烯基聚醚,具有聚合活性,因而減少了聚羧酸系混凝土外加劑生產工藝中的酯化過程,同時也由於不需要酯化而提高了聚羧酸系混凝土外加劑合成原材料的品質;③生產過程安全,不使用溶劑,產品不需要後處理,反應系統密閉,沒有尾氣排放,對環境不會造成影響④裝置單批生產量大,極大程度上確保了聚醚的品質。
附圖說明
圖1《一種製備聚羧酸系混凝土外加劑專用聚醚的方法》採用的BUSS氣液接觸迴路反應裝置工藝流程圖。
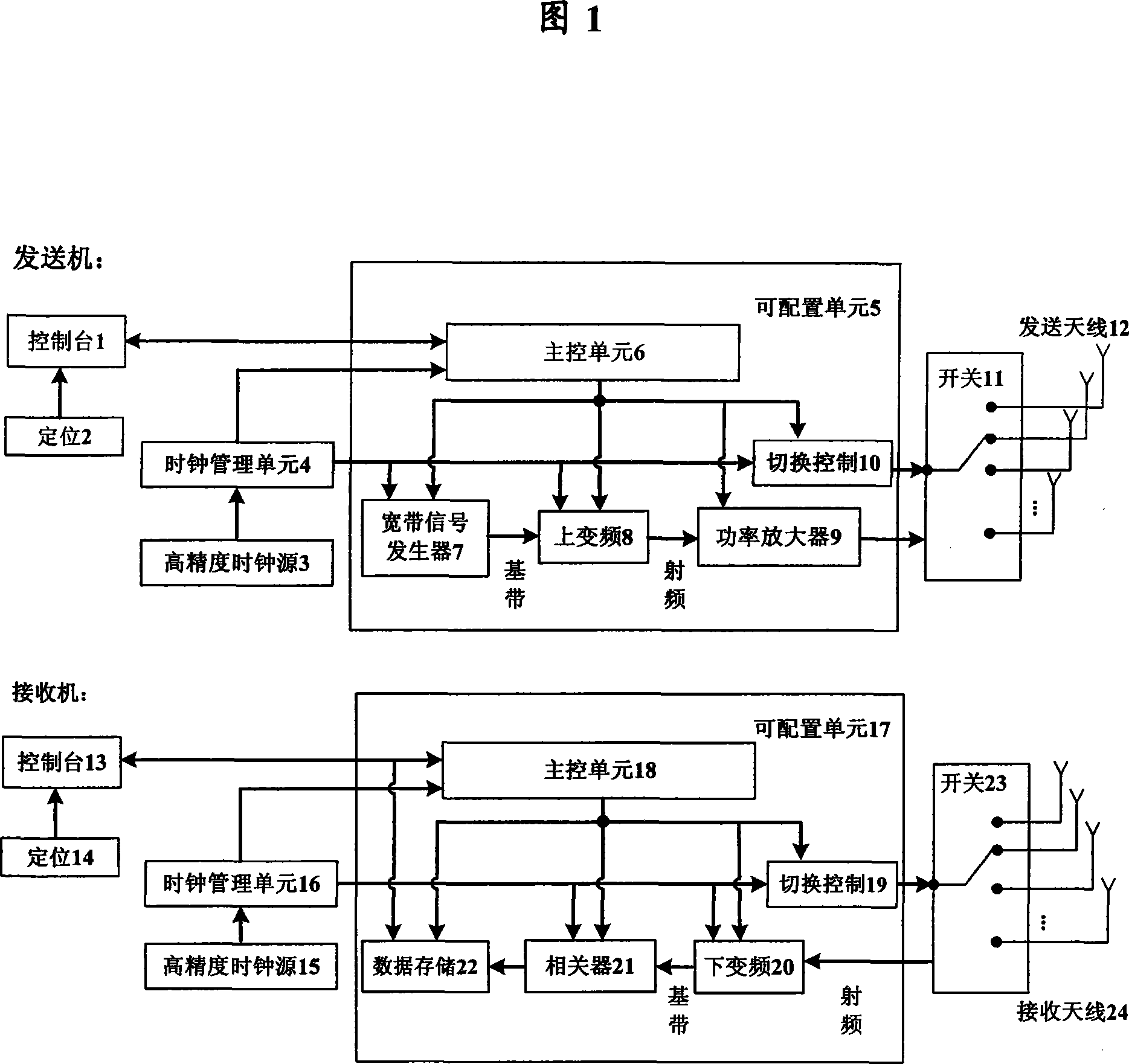
技術領域
《一種製備聚羧酸系混凝土外加劑專用聚醚的方法》涉及一種混凝土外加劑專用聚醚的製備方法,特別涉及一種聚羧酸系混凝土外加劑專用聚醚的製備方法。
權利要求
1.一種製備聚羧酸系混凝土外加劑專用聚醚的方法,所述聚醚由以下化學式(1)所表示:
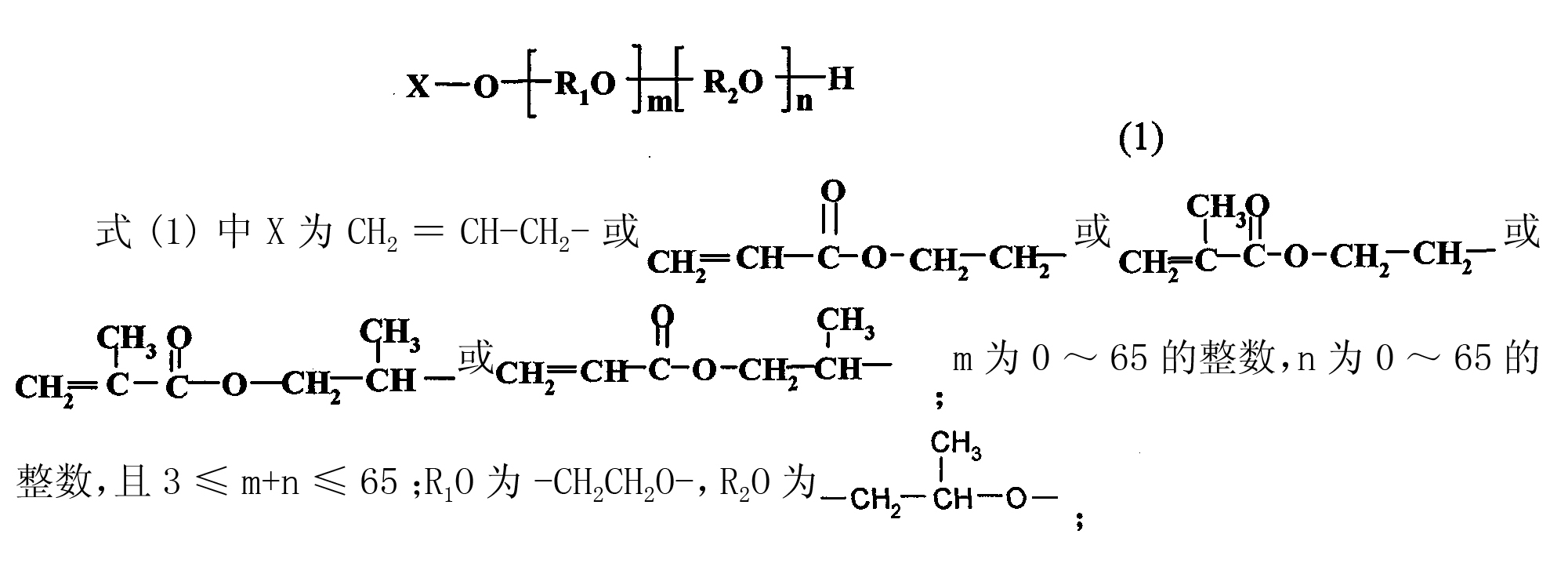
其特徵在於:①採用X-O-H作為氧化烯開環聚合反應的起始劑來製備具有可聚合活性聚醚,其中X所表示的基團與式(1)中X相同;②在BUSS烷氧基化裝置上利用氧化烯開環聚合製備具有可聚合活性聚醚。
2.如權利要求1所述製備聚羧酸系混凝土外加劑專用聚醚的方法,其特徵在於其具體反應過程如下:
1)用氮氣置換整套BUSS烷氧基化裝置,向迴路反應器預反應釜中加入起始劑、催化劑和阻聚劑後抽真空,升溫至80~120℃後脫水,再充氮氣使預反應釜壓力達0.25~0.45兆帕;
2)開動小循環泵,同時根據目標產品的分子量壓入相應量的氧化烯,反應1~3小時,氧化烯的加入量按以下方式確定:氧化烯的質量=(每批原料總質量÷目標產品分子量)×氧化烯分子量=目標產品分子鏈摩爾數×氧化烯分子量=催化劑摩爾數×氧化烯分子量=(催化劑總質量÷催化劑分子量)×氧化烯分子量;
3)開啟大循環泵,加入餘量的的氧化烯,在110~170℃和0.25~0.45兆帕的壓力下進行聚合,加料和反應維持4-8小時後停止加氧化烯,繼續循環熟化至反應器內壓力不再減小進,反應結束;
4)開啟真空脫除反應器內游離的廢氣,反應器內粗產品冷卻至80~95℃,停止循環,粗產品排入中和釜,加中和劑中和到pH=6.5+0.3後進行真空脫水,即得最終產品。
3.如權利要求2所述所述製備聚羧酸系混凝土外加劑專用聚醚的方法,其特徵在於所述聚醚分子量為190~4,000。
4.如權利要求2或3所述製備聚羧酸系混凝土外加劑專用聚醚的方法,其特徵在於步驟1)抽真空至-750毫米汞柱,脫水時間40~60分鐘。
5.如權利要求2或3所述製備聚羧酸系混凝土外加劑專用聚醚的方法,其特徵在於步驟2)加入的氧化烯的摩爾量與催化劑相同。
6.如權利要求2或3所述製備聚羧酸系混凝土外加劑專用聚醚的方法,其特徵在於步驟3)中氧化烯的加入速率為:(每批原料總質量-起始劑質量-通過小循環泵加入的氧化烯質量)/加料時間,加入量為:每批每批原料總質量-起始劑質量-步驟2)氧化烯加入量。
7.如權利要求2或3所述製備聚羧酸系混凝土外加劑專用聚醚的方法,其特徵在於步驟3)的繼續循環熟化時間為3~10分鐘。
8.如權利要求2或3所述製備聚羧酸系混凝土外加劑專用聚醚的方法,其特徵在於合成聚醚體系中起始劑和氧化烯的摩爾數之比為1:1~65,阻聚劑的用量為起始劑質量的0.05~1.5wt%,催化劑用量為氧化烯質量的0.05~0.2wt%。
9.如權利要求2或3所述所述製備聚羧酸系混凝土外加劑專用聚醚的方法,其特徵在於所述氧化烯為環氧乙烷、環氧丙烷或它們任意比例的混合物。
10.如權利要求2或3所述所述製備聚羧酸系混凝土外加劑專用聚醚的方法,其特徵在於所述阻聚劑為1,4-苯醌或1,4-萘醌。
11.如權利要求2或3所述所述製備聚羧酸系混凝土外加劑專用聚醚的方法,其特徵在於所述起始劑為羥酯或端烯醇。
12.如權利要求11所述所述製備聚羧酸系混凝土外加劑專用聚醚的方法,其特徵在於羥酯或端烯醇選自丙烯酸羥乙酯,甲基丙烯酸羥乙酯,丙烯酸羥丙酯或甲基丙烯酸羥丙酯,烯丙醇。
13.如權利要求2或3所述所述製備聚羧酸系混凝土外加劑專用聚醚的方法,其特徵在於所述催化劑選自K2O、Na2O、NaOH、KOH、蒙脫土、累脫石、雙金屬氰化物、多金屬氰化物絡合物或前述物任意兩種或兩種以上的混合物。
14.如權利要求2或3所述所述製備聚羧酸系混凝土外加劑專用聚醚的方法,其特徵在於所述酸性中和劑選自乙酸,稀硫酸,磷酸,
己二酸,丙二酸或丁二酸或酒石酸。
實施方式
註:以下各具體實施方案所製備的聚醚性能測試結果列於表1中。
實施例1
用氮氣(N2)置換整套裝置,向迴路反應器預反應釜中(R-2202)加入3193.30千克丙烯酸羥乙酯,18.83千克NaOH和31.93千克1,4-萘醌,抽真空(-750毫米汞柱)升溫至100℃脫水50分鐘,充N2使預反應釜壓力達0.3兆帕,開動小循環泵(P-2214),同時壓入20.71千克環氧乙烷開始反應2小時;然後開啟大循環泵(P-2204),按3762.70千克/時的速度向反應器內加入環氧乙烷,在160℃和0.3兆帕的壓力下進行聚合,加料及反應維持5小時,停止加環氧乙烷,繼續循環熟化5分鐘;當反應器內壓力不再減小時,反應結束,開啟真空脫除反應器內游離的環氧乙烷並通入聚醚尾氣處理塔水洗處理,尾氣通過20米排氣筒排入大氣;反應器內粗產品冷卻至85℃,停止循環,粗產品排入中和釜,加中和劑中和到pH=6.5±0.3;最後,中和釜使用水環式真空泵進行真空脫水,即得端烯基聚醚。最後用GPC法來測定聚醚的分子量及分子量分布,測定結果見表1。
實施例2
用氮氣(N2)置換整套裝置,向迴路反應器預反應釜中(R-2202)加入2863.08千克甲基丙烯酸羥乙酯,14.37千克NaOH和13.32千克1,4-苯醌,抽真空(-750毫米汞柱)升溫至100℃脫水50分鐘,充N2使預反應釜壓力達0.3兆帕,開動小循環泵(P-2214),同時壓入15.81千克環氧乙烷開始反應2小時;然後開啟大循環泵(P-2204),按3190.52千克/時的速度向反應器內加入環氧乙烷,在160℃和0.3兆帕的壓力下進行聚合,加料及反應維持6小時,停止加環氧乙烷,繼續循環熟化7分鐘;當反應器內壓力不再減小時,反應結束,開啟真空脫除反應器內游離的環氧乙烷並通入聚醚尾氣處理塔水洗處理,尾氣通過20米排氣筒排入大氣;反應器內粗產品冷卻至90℃,停止循環,粗產品排入中和釜,加中和劑中和到pH=6.5+0.3;最後,中和釜使用水環式真空泵進行真空脫水,即得端烯基聚醚。最後用GPC法來測定聚醚的分子量及分子量分布,測定結果見表1。
實施例3
用氮氣(N2)置換整套裝置,向迴路反應器預反應釜中(R-2202)加入1431.54千克丙烯酸羥丙酯,10.29千克NaOH和3.58千克1,4-苯醌,抽真空(-750毫米汞柱)升溫至100℃脫水50分鐘,充N2使預反應釜壓力達0.3兆帕,開動小循環泵(P-2214),同時壓入11.32千克環氧乙烷開始反應2小時;然後開啟大循環泵(P-2204),按2938.30千克/時的速度向反應器內加入氧化烯,在160℃和0.3兆帕的壓力下進行聚合,加料及反應維持7小時,停止加環氧乙烷,繼續循環熟化8分鐘;當反應器內壓力不再減小時,反應結束,開啟真空脫除反應器內游離的環氧乙烷並通入聚醚尾氣處理塔水洗處理,尾氣通過20米排氣筒排入大氣;
反應器內粗產品冷卻至90℃,停止循環,粗產品排入中和釜,加中和劑中和到pH=6.5+0.3;最後,中和釜使用水環式真空泵進行真空脫水,即得端烯基聚醚。最後用GPC法來測定聚醚的分子量及分子量分布,測定結果見表1。
實施例4
用氮氣(N2)置換整套裝置,向迴路反應器預反應釜中(R-2202)加入3650.74千克丙烯酸羥乙酯,36.82千克KOH和46.63千克1,4-苯醌,抽真空(-750毫米汞柱)升溫至100℃脫水50分鐘,充N2使預反應釜壓力達0.3兆帕,開動小循環泵(P-2214),同時壓入28.93千克環氧乙烷開始反應2小時;然後開啟大循環泵(P-2204),按4595.80千克/時的速度向反應器內加入環氧乙烷,在160℃和0.25兆帕的壓力下進行聚合,加料及反應維持4小時,停止加環氧乙烷,繼續循環熟化3分鐘;當反應器內壓力不再減小時,反應結束,開啟真空脫除反應器內游離的環氧乙烷並通入聚醚尾氣處理塔水洗處理,尾氣通過20米排氣筒排入大氣;反應器內粗產品冷卻至80℃,停止循環,粗產品排入中和釜,加中和劑中和到pH=6.5±0.3;最後,中和釜使用水環式真空泵進行真空脫水,即得端烯基聚醚。最後用GPC法來測定聚醚的分子量及分子量分布,測定結果見表1。
實施例5
用氮氣(N2)置換整套裝置,向迴路反應器預反應釜中(R-2202)加入906.21千克甲基丙烯酸羥丙酯,15.83千克KOH和0.45千克1,4-苯醌,抽真空(-750毫米汞柱)升溫至100℃脫水50分鐘,充N2使預反應釜壓力達0.3兆帕,開動小循環泵(P-2214),同時壓入16.39環氧丙烷開始反應2小時;然後開啟大循環泵(P-2204),按2635.46千克/時的速度向反應器內加入環氧丙烷,在120℃和0.35兆帕的壓力下進行聚合,加料及反應維持8小時,停止加環氧丙烷,繼續循環熟化10分鐘;當反應器內壓力不再減小時,反應結束,開啟真空脫除反應器內游離的環氧丙烷並通入聚醚尾氣處理塔水洗處理,尾氣通過20米排氣筒排入大氣;反應器內粗產品冷卻至90℃,停止循環,粗產品排入中和釜,加中和劑中和到pH=6.5+0.3;最後,中和釜使用水環式真空泵進行真空脫水,即得端烯基聚醚。最後用GPC法來測定聚醚的分子量及分子量分布,測定結果見表2。
表2各實施例所製備聚醚的分子量及分子量分布
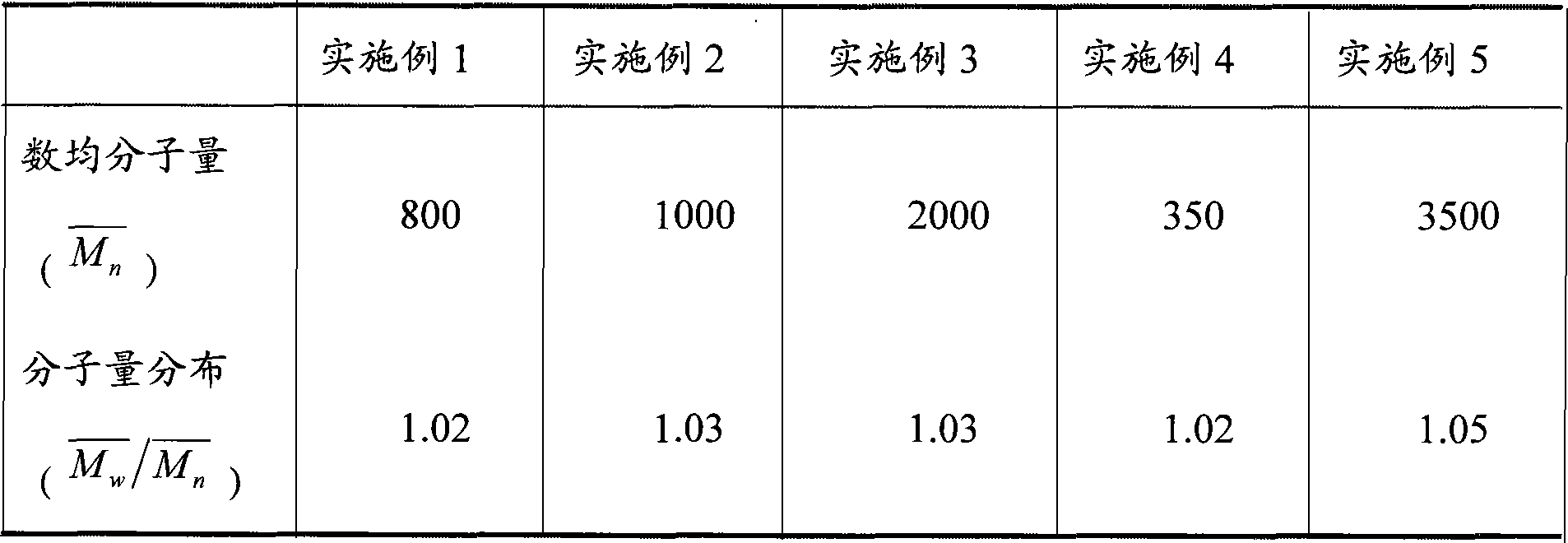
表2
榮譽表彰
2016年12月7日,《一種製備聚羧酸系混凝土外加劑專用聚醚的方法》獲得第十八屆中國專利優秀獎。